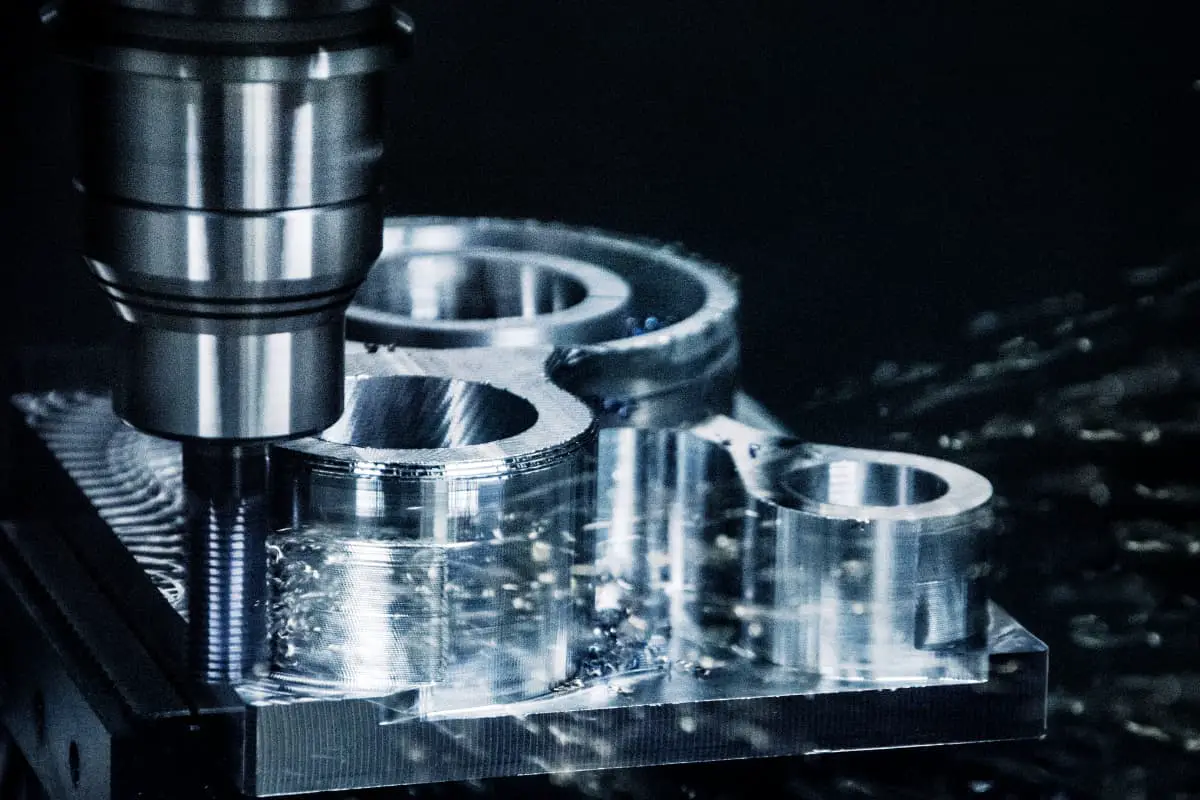
Analizden, soğuk ekstrüzyon kalıplarının çalışma koşullarının son derece sert olduğu ve kısa hizmet ömürlerine yol açtığı açıktır. Bu durum özellikle çelik malzemelerin soğuk ekstrüzyonunda kullanılan kalıplar için geçerlidir. Bu nedenle, soğuk ekstrüzyon teknolojisinin gelişimini teşvik etmek için, soğuk ekstrüzyon kalıplarının kullanım ömrüne ilişkin derinlemesine araştırma yapılması kilit bir konudur.
Soğuk ekstrüzyon kalıplarının ömrünü uzatmanın başlıca iki yönü vardır:
Birim ekstrüzyon kuvvetinin azaltılması
a) Uygun deformasyon yönteminin seçilmesi
Bir parça farklı ekstrüzyon yöntemleri kullanılarak oluşturulabildiğinde, alt üniteye sahip yöntem ekstrüzyon kuvveti seçilmelidir. Örneğin, basit doğrudan veya dolaylı ekstrüzyonu bileşik ekstrüzyona dönüştürmek için bir proses mili kullanmak, birim ekstrüzyon kuvvetini azaltmak ve kalıp ömrünü uzatmak için etkili bir önlemdir.
Ekstrüzyon kalıplama sırasında sürtünme direncinin yönü her zaman metal akış yönünün tersidir. Bu nedenle, birim ekstrüzyon kuvvetini azaltmak için Şekil 9-15'te gösterilen ekstrüzyon yöntemleri kullanılabilir.
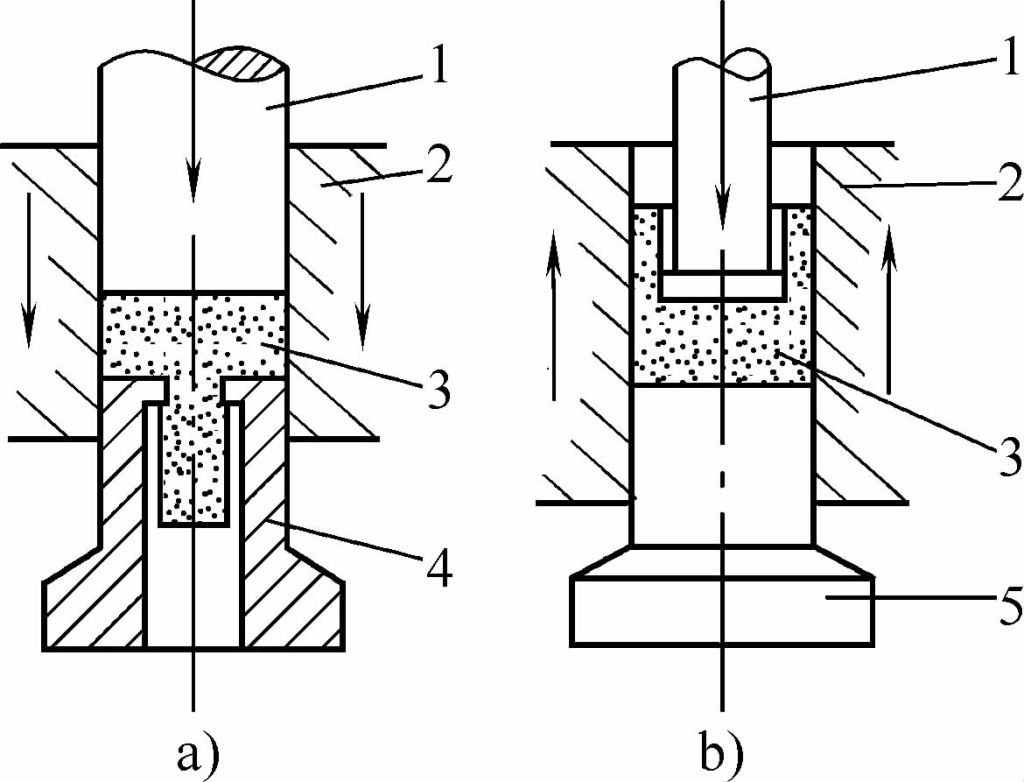
a) doğrudan ekstrüzyon ve b) dolaylı ekstrüzyon.
Bileşenler aşağıdaki gibi numaralandırılmıştır:
1 - Yumruk
2 - Ekstrüzyon silindiri
3 - Ekstrüde parça
4 - Ölmek
5 - İtici çubuk
b) Doğru deformasyon derecesinin seçilmesi
Gerçek üretimde, verimliliği artırmak ve deformasyon işlemlerinin sayısını azaltmak için, genellikle uygun olmayan deformasyon derecesini artırma yöntemi benimsenir. Bu da kaçınılmaz olarak birim ekstrüzyon kuvvetini artırarak erken kalıp arızasına yol açar. Bu nedenle, proses tasarımı sırasında, izin verilen deformasyon derecesi sıkı bir şekilde kontrol edilmelidir.
c) Optimum kalıp şeklinin kullanılması
İster doğrudan ekstrüzyon kalıbı ister dolaylı kalıp olsun, birim ekstrüzyon kuvvetini en aza indiren optimum bir şekil olmalıdır. Bu nedenle, gerçek üretimde, birim ekstrüzyon kuvvetini azaltmak ve kalıp ömrünü uzatmak için optimum kalıp şeklini bulmak üzere metal akışının sayısal simülasyonu kullanılmalıdır.
d) Doğru boşluk şeklinin seçilmesi
Mevcut veriler, makul bir işlenmemiş parça şekli kullanmanın birim ekstrüzyon kuvvetini azaltabileceğini göstermektedir. Bu nedenle, soğuk ekstrüzyon için kullanılan boşluklar doğrudan kesilmiş hammaddeden alınmaz, ancak bir preform işlemi ile işlenir.
e) Boşluğa sıkı ön işlem uygulanması
Soğuk ekstrüzyondan önce işlenmemiş parçanın makul bir şekilde tavlanması ve yüzey yağlama işlemi, birim ekstrüzyon kuvvetini önemli ölçüde azaltabilir. Örneğin, içinde çelik malzemelerin soğuk ekstrüzyonuekstrüzyon kuvveti, ekstrüzyondan önce fosfatlama işleminin kullanılıp kullanılmadığına bağlı olarak yaklaşık yarı yarıya farklılık gösterecektir.
Küfün Hasara Karşı Direncinin Artırılması
(1) Kalıp Malzemelerinin Kalitesinin İyileştirilmesi ve Yeni Malzemelerin Geliştirilmesi
Mevcut kalıp malzemelerinin kalitesini artırmak ve yenilerini geliştirmek, kalıbın ömrünü uzatmak için temel yöntemlerdir.
1) Kalıp malzemelerinin kalitesini artırmanın birincil yolu, metalürji tesislerinden metalürjik kalitelerini artırmalarını talep etmektir. Bu sadece çeliğin kimyasal bileşiminin değil aynı zamanda kalıp çeliğinin saflığının ve homojenliğinin de güvence altına alınmasını gerektirir. Üreticiler için, hammaddelerin denetimini güçlendirmek ve kalıp malzemelerinin kalitesini artırmak için bazı etkili süreç önlemlerini zamanında benimsemek çok önemlidir.
2) Son yıllarda, hem yurt içinde hem de yurt dışında yeni kalıp malzemelerinin geliştirilmesinde önemli ilerlemeler kaydedilmiştir. Yeni yüksek hız çeliği, çeliğe bağlı sert alaşımlar, baz çelikler ve seramik malzemeler gibi çok sayıda yenilikçi kalıp malzemesi geliştirilerek kalıp mukavemetinin artırılması ve kalıp ömrünün uzatılması için uygun ön koşullar sağlanmıştır.
Bununla birlikte, bu yeni malzemelerin özelliklerini tam olarak anlamak ve ciddi israfa ve potansiyel olarak tatmin edici olmayan kullanım etkilerine neden olabilecek yanlış kullanımdan kaçınmak için belirli çalışma koşullarına göre doğru şekilde seçmek çok önemlidir.
(2) Kalıp Malzemelerinin Doğru Seçimi
Soğuk ekstrüzyon kalıbının çalışma koşullarına göre uygun kalıp malzemesinin doğru seçilmesi, kalıbın ömrünü uzatmak ve maliyetleri düşürmek için önemli bir önlemdir. Bu nedenle kalıp malzemeleri seçilirken aşağıdaki iki husus göz önünde bulundurulmalıdır.
1) Kalıp malzemelerinin seçimi, kalıbın çalışma koşullarına göre yapılmalıdır. Soğuk ekstrüzyon kalıplarının gerçek çalışma koşulları genellikle değişir ve arıza modları tamamen aynı değildir. Kalıp esas olarak aşınma nedeniyle arızalanırsa, yüksek mukavemetli kalıp malzemeleri seçmek gereksizdir; bunun yerine, yüksek aşınma direncine sahip kalıp malzemeleri seçilmelidir.
Kalıp büyük eksantrik kuvvetlere maruz kalıyorsa ve çoğunlukla kırılarak arızalanıyorsa (zımba kalıpları gibi), yüksek tokluğa sahip kalıp malzemeleri seçilmelidir. Deneyimler, seçilen kalıp malzemesinin bazı yönlerden kullanım gereksinimlerini karşılayamaması durumunda kalıbın ömrünü kısaltabileceğini ve erken arızalara neden olabileceğini göstermektedir.
2) Kalıp malzemelerinin seçiminde ekonomik faydalar da tam olarak göz önünde bulundurulmalıdır. Bilindiği gibi, kalıp malzemelerinin fiyatları, özellikle bazı gelişmiş kalıp malzemeleri için genellikle oldukça yüksektir. Bu nedenle kalıp malzemelerini seçerken, kullanım gereksinimlerini karşılarken mümkün olduğunca daha uygun fiyatlı kalıp malzemelerini seçmek ve gelişmiş kalıp malzemelerinin keyfi olarak yanlış kullanımından kesinlikle kaçınmak gerekir.
(3) Makul Bir Kalıp Yapısının Tasarlanması
Makul bir kalıp yapısı, kalıbın yük taşıma kapasitesini artırmak ve ömrünü uzatmak için önemli bir önlemdir. Özetle, aşağıdaki noktalar dikkate alınmalıdır.
1) Kalıbın yeterli mukavemet, sağlamlık, güvenilirlik ve iyi yönlendirme performansına sahip olduğundan emin olun.
2) Mümkün olduğunca büyük stres konsantrasyonlarına sahip bir kalıp yapısı oluşturmaktan kaçının. Örneğin, geçiş parçaları yeterince büyük bir iç köşe yarıçapı ile tasarlanmalıdır; çatlamaya eğilimli kalıp boşluğu parçaları için bölünmüş yapılar benimsenmelidir, vb.
3) Kullanılan kalıp malzemesinin türüne göre farklı optimizasyon tasarım yöntemleri seçilmelidir. Örneğin, kalıp için sert alaşımlar veya çelik bağlı sert alaşımlar kullanıldığında, optimizasyon tasarımı kalıbın iç duvarında sıfır çekme gerilmesini hedeflemelidir.
Kalıp için takım çeliği kullanıldığında, optimizasyon tasarımı için hedef fonksiyon olarak hem kalıp hem de ön gerilmeli halka malzemesi aynı anda verim vermelidir. Bu şekilde kalıp malzemesinin potansiyelinden tam olarak yararlanılabilir.
4) Kanıtlanmış yeni kalıp yapılarını benimseyin. Örneğin, bir çelik şerit sarma kalıbı veya bir tel sarma kalıbı kullanmak, kalıbın boyutunu ve ağırlığını azaltırken kalıbın yüksek mukavemete sahip olmasını sağlayabilir; kademeli bir kombine kalıp kullanmak, aynı boyuttaki düz ağızlı bir kombine kalıptan daha büyük radyal iç basıncı taşıyabilir.
(4) Makul Bir Dövme Sürecinin Benimsenmesi
Kalıp çeliğindeki karbürlerin dağılımı ve biçimi, mekanik özellikleri üzerinde belirleyici bir etkiye sahiptir ve dövme deformasyonu, çelikteki bloklu ve bant şeklindeki karbürleri kırmak, malzeme anizotropisini ortadan kaldırmak ve iç kaliteyi iyileştirmek için küçük parçacıklar halinde eşit olarak dağıtmak için ana yöntemdir.
Çelik fabrikaları tarafından tedarik edilen kalıp malzemeleri belirli bir derecede basınç işleminden geçmiş olsalar da kullanım gereksinimlerini karşılayamazlar ve yeniden dövme işleminden geçmeleri gerekir. Kalıp çeliği yeniden dövülürken aşağıdaki hususlara dikkat edilmelidir.
1) Kalıp malzemelerinin yeniden dövülmesinin temel amacının mekanik özellikleri iyileştirmek ve sadece ikinci olarak şekli değiştirmek olduğunu tam olarak anlayın.
2) Dövme kalıp malzemeleri ile dövme genel malzemeleri arasındaki farklara özellikle dikkat edin ve kalıp malzemelerinin dövme işlemi özelliklerine kesinlikle uyun.
3) Karbürleri tamamen parçalamak ve eşit şekilde dağılmalarını sağlamak için, dövme için yüksek bir dövme oranı ve çok yönlü ekstrüzyon yöntemi benimsenmelidir.
(5) Makul Bir Isıl İşlem Sürecinin Benimsenmesi
Erken kalıp arızalarına ilişkin yerel ve uluslararası istatistiklere göre, erken kalıp arızalarının en büyük oranı makul olmayan ısıl işlem süreçlerinden kaynaklanmaktadır. Deneyimler, kalıbın ısıl işlem sürecinin kalıp malzemelerinin mekanik özelliklerini iyileştirmek için önemli araçlardan biri olduğunu göstermektedir.
Kalıbın yüksek mukavemet, sertlik, aşınma direnci ve ısıl sertliğe sahip olmasını sağlamak için, su verme ve temperleme ısıl işlem yöntemlerine ek olarak yüzey güçlendirme ısıl işlem süreçleri eklenmelidir. Bu, kalıp çalışma yüzeyinin sertliğini, aşınma direncini ve yorulma direncini önemli ölçüde artırabilir. Şu anda, soğuk ekstrüzyon kalıp çeliği için aşağıdaki yüzey güçlendirme ısıl işlem prosesleri kullanılmaktadır.
1) Karbonitrürleme
Karbon ve nitrojenin çeliğin yüzeyine aynı anda infiltrasyonuna karbonitrürleme denir. Çok elementli birlikte infiltrasyon kimyasal ısıl işleminin bir türüne aittir.
Karbonitrürleme, karbürlemeye kıyasla çeşitli avantajlara sahiptir.
① Sızdırılmış tabaka yüzeyi, karbürlenmiş çelikten daha yüksek sertlik ve aşınma direncinin yanı sıra belirli ısı sertliği ve korozyon direncine sahiptir.
② Östenit içinde çözünen azot, aşırı soğutulmuş östenitin stabilitesini artırır ve böylece sızan tabakanın sertleşebilirliğini geliştirir.
③ Azot ilavesi östenitin oluştuğu sıcaklığı düşürerek tane irileşmesini önleyebilir.
④ Karbonitrürlemenin deformasyonu karbürlemeden daha küçüktür.
Yukarıda belirtilen bir dizi avantaj nedeniyle, karbonitrürleme şu anda kalıpların yüzey güçlendirme ısıl işleminde karbürlemenin yerini alma eğilimindedir.
Karbonitrürleme işlemleri, kullanılan malzemelerin durumuna göre katı, sıvı ve gaz karbonitrürleme olarak ayrılabilir. Siyanür karbonitrürleme, yüksek toksisitesi nedeniyle son yıllarda aşamalı olarak kaldırılmıştır. Gazlı karbonitrürleme ise toksik değildir, iyi çalışma koşulları sağlar, kullanımı ve kontrolü kolaydır. Bu nedenle, gazlı karbonitrürleme şu anda yaygın olarak kullanılmaktadır.
2) Gaz Nitrokarbürleme
Bu, esas olarak Fe-C-N üçlü sisteminin ötektik sıcaklığının altındaki sıcaklıklarda gerçekleştirilen azot infiltrasyonunu içeren bir tür gaz karbonitrürleme anlamına gelir. Gaz nitrokarbürleme işleminden sonra kalıp yüzeyi daha yüksek mukavemet, aşınma direnci ve yorulma mukavemetine sahiptir. Şu anda, bu yüzey güçlendirme ısıl işlemi soğuk ekstrüzyon kalıplarında kullanılmaya başlanmış ve iyi sonuçlar elde edilmiştir.
Örneğin, belirli bir fabrika tarafından 15 çelik alet yuvasının soğuk ekstrüzyonu için kullanılan zımba kalıbı, gaz nitrokarbürleme işlemi olmadan CG-2 baz çelikten yapıldığında 14.500 adet kalıp ömrüne sahipti, ancak nitrokarbürleme işleminden sonra ortalama ömür 27.500 parçaya ulaştı ve en yüksek 45.600 parçaya ulaştı.
Gaz nitrokarbürleme için proses spesifikasyonu şöyledir: ısıtma sıcaklığı 530 ~ 570 ℃ ve bekletme süresi genellikle 1 ~ 16 saattir.
Ayrıca, soğuk ekstrüzyon kalıp çeliğinin yüzey güçlendirme ısıl işleminde iyon nitrürleme, sert krom kaplama, TiC buhar biriktirme, tuz banyosu vanadyum infiltrasyonu, bor infiltrasyonunun yanı sıra nadir toprak yüzey mühendisliği ve nano yüzey mühendisliği teknolojileri de uygulanmaktadır. Bunların hepsi kalıp yüzeyinin mukavemetini farklı ölçülerde artırabilir ve kalıbın ömrünü uzatabilir.
(6) İşleme Kalitesinin Sağlanması ve Yeni İşleme Yöntemlerinin Benimsenmesi
1) İşleme kalitesinin kesinlikle sağlanması.
Daha yüksek işleme kalitesi kalıbın hizmet ömrünü uzatabilir. Bu nedenle, belirtilen teknik gerekliliklerin yerine getirilmesini sağlamak için etkili süreç önlemleri alınmalıdır. Deneyimler, soğuk ekstrüzyon kalıplarının mekanik işlemesinde daha yüksek işleme kalitesi elde etmek için aşağıdaki noktaların vurgulanması gerektiğini göstermektedir:
i) Zımba kalıbının son işleminden sonra, tüm geçiş parçaları pürüzsüz ve dikişsiz olmalıdır. Çalışma parçası sıkıştırma parçası ile eş eksenli olmalı ve şekli kesinlikle simetrik olmalıdır. Aksi takdirde, sadece ekstrüde parçanın eşit olmayan kalınlığına neden olmakla kalmaz, aynı zamanda zımba kalıbının kendisi de tek taraflı stres nedeniyle bükülebilir.
ii) Zımba kalıbının yüksek mukavemetini sağlamak ve gerilim yoğunlaşması nedeniyle çatlamayı önlemek için, zımba kalıbının her iki ucunda da artık merkez delikleri olmamalıdır. Bu nedenle, zımba kalıbı işlenirken, merkez deliğin delinmesi için üst yüzeyde bir "tümsek" ayrılmalıdır.
iii) Zımba kalıbının yüzey pürüzlülüğü genellikle ekstrüde edilen parçanın hammaddesinin türüne bağlı olarak belirli gerekliliklere uygun olmalıdır. Çelik ters ekstrüzyon zımba kalıpları için, yüzey pürüzlülüğü Ra <0,2μm olmalıdır; demir dışı için metaller Saf alüminyum gibi, 0,8μm'lik bir yüzey pürüzlülüğü Ra yeterlidir.
Bununla birlikte, çalışma bandı parçası için, ekstrüde edilen malzemenin çelik veya demir dışı metal olmasına bakılmaksızın, <0,2μm'lik bir yüzey pürüzlülüğü Ra korunmalıdır.
iv) İleri veya geri ekstrüzyon kalıp boşluğunun yüzey pürüzlülüğü ne kadar düşük olursa o kadar iyidir, genellikle Ra<0,2μm olmalıdır. Taşlanmış ve ardından cilalanmış kalıp boşluğu, birim ekstrüzyon kuvvetini azaltarak kalıbın hizmet ömrünü önemli ölçüde uzatabilir.
v) Kalıbın çalışan kısmının taşlanması veya parlatılması son ısıl işlemden sonra yapılmalıdır. Taşlamadan önce bırakılan işleme payı 0,1 mm'yi geçmemeli ve yüzey pürüzlülüğü Ra <1,6μm olmalıdır. Taşlamadan sonra kalan gerilimi gidermek için, taşlama tamamlandıktan sonra gerilim giderici bir tavlama işlemi uygulamak en iyisidir.
2) Yeni işleme yöntemlerinin benimsenmesi.
Genel mekanik işleme yöntemlerine ek olarak, soğuk ekstrüzyon kalıplarının işlenmesi, elektrik deşarjlı işleme, elektrolitik işleme ve kalıp boşluklarının soğuk ekstrüzyonu gibi yöntemlerin yanı sıra ultra hassas işleme ve yüksek hızlı frezeleme gibi yeni işleme yöntemlerini de içerir. Burada, kalıp boşluklarının soğuk ekstrüzyon yöntemini kısaca tanıtacağız.
Kalıp boşluklarının soğuk ekstrüzyonunun özü, metallerin plastik şekillendirme prensibine dayanan soğuk ekstrüzyon işlemini kullanarak kalıp boşluğunu doğrudan işlemektir. Genellikle ilk olarak kalıp boşluğunun şekline göre takım çeliğinden yüksek sertlikte bir zımba kalıbının işlenmesini içerir.
Daha sonra, bir boşluklu ekstrüzyon makinesinin (veya büyük tonajlı bir hidrolik pres), zımba kalıbı işlenmemiş parçaya bastırılır ve böylece içbükey-dışbükey ters çevrilmiş bir şekilde zımba kalıbı çalışma parçasının şekli, çevresi ve boyutuyla eşleşen bir kalıp boşluğu oluşturulur.
Kalıp boşluklarının soğuk ekstrüzyonu için birçok yöntem vardır ve bunlar arasında en yaygın olanı Şekil 9-16'da gösterildiği gibi kalıp çerçevesi içindeki boşluk ekstrüzyonudur. Çalışma süreci şu şekildedir: tavlanmış ve yumuşatılmış işlenmemiş parça kalıp çerçevesine önceden yerleştirilir ve zımba kalıbı hidrolik presin etkisi altında işlenmemiş parçaya bastırılır.
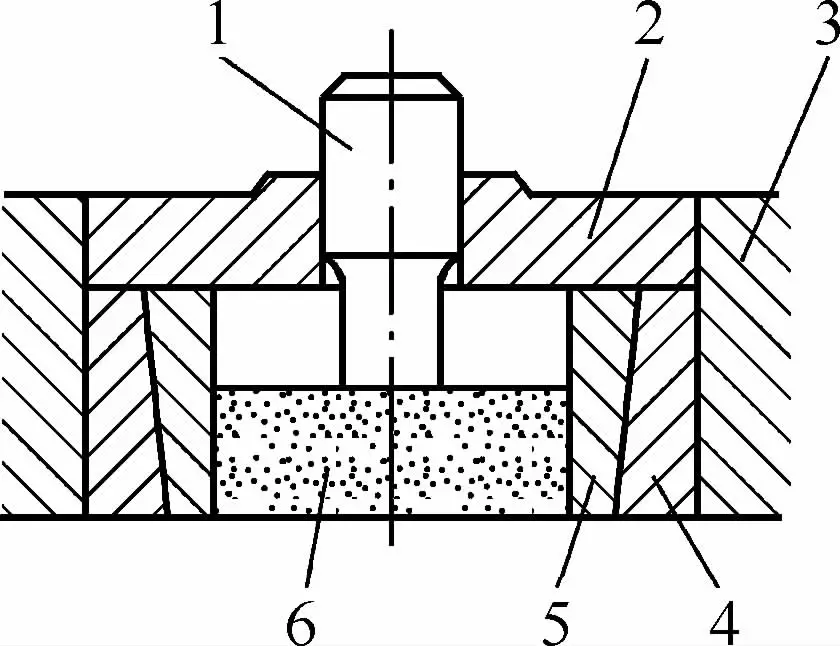
1. Yumruk
2. Kılavuz plaka
3. Dış halka
4. İç halka
5. Konik geçme blok
6. Boş
Bu sırada, işlenmemiş metal yalnızca yukarı doğru akabilir ve işlenmemiş metal ile zımba kalıbı arasında yakın temas sağlar. Sonuç olarak, kalıp boşluğunun hassasiyeti IT6-IT7'ye ulaşabilir, geometrik şekil doğrudur ve yüzey pürüzlülüğü Ra 0.1 ~ 0.2μm'dir.
Kalıp boşluğunun soğuk ekstrüzyonu için zımba kalıbı, şekillendirmenin başarısı veya başarısızlığı ile ilgili kritik bir bileşendir. Bu zımba kalıbının imalatına dikkat edilmelidir. Genel olarak aşağıdaki hususlar dikkate alınmalıdır:
i) Gerilim yoğunlaşmasını azaltmak için, zımba kalıbının geçiş kısmında ani değişiklikler olmamalı ve minimum 0,2 mm'lik bir eğrilik yarıçapına sahip olmalıdır.
ii) Zımba kalıbının yüksek mukavemet ve sertliğe sahip olmasını sağlamak için, zımba kalıbının hammaddesi olarak ultra yüksek mukavemetli çelik seçilmeli ve sıkı dövme deformasyonu ve ısıl işlem süreçleri uygulanmalıdır.
iii) Isıl işlemden sonra, zımba kalıbının çalışma kısmı Ra≤0.1μm yüzey pürüzlülüğü ile tekrar taşlanmalıdır.
iv) Zımba kalıbının kılavuzluk hassasiyetini sağlamak için, zımba kalıbı kılavuz parçasının uzunluğu genellikle kalıp boşluğunun maksimum radyal boyutunun 1,2 katından az olmamalıdır.
Soğuk ekstrüzyonla kalıp boşlukları üretme oranının kesme işleminden çok daha yüksek olduğu unutulmamalıdır. Daha da önemlisi, kalıp boşluğu soğuk ekstrüzyonla oluşturulduktan sonra, kalıbın iç yapısı daha yoğundur ve mukavemeti ve aşınma direnci daha yüksektir, böylece kalıbın hizmet ömrü uzar.
Bununla birlikte, ekstrüzyonla oluşturulan kalıp malzemesinin mukavemeti daha yüksek ve plastisitesi daha zayıf olduğundan, bu işleme yöntemi yalnızca basit şekiller ve sığ kalıp boşluğu işleme için kullanılır.
(7) Kalıpların Akılcı Kullanımı ve Bakımı
Soğuk ekstrüzyon şekillendirmenin özelliklerini anlamak ve kalıpların rasyonel kullanımı ve dikkatli bakımı da kalıpların hizmet ömrünü uzatmak için önemli önlemlerdir.
Kışın düşük sıcaklıklarda, çatlamayı önlemek için kullanmadan önce kalıbı önceden ısıtmak en iyisidir. Soğuk ekstrüzyon üretimi sırasında, ısının etkisi nedeniyle kalıbın sıcaklık artışı hızlıdır, bu nedenle kalıp düzenli olarak soğutulmalıdır.
Büyük kuvvetlere maruz kalan kalıplar için, birkaç bin ekstrüzyondan sonra, 2 saat boyunca 160~180°C'de gerilim giderici bir tavlama işlemi yapılmalıdır.
Tekrar tekrar kullanılan dış ve orta öngerilmeli halkalar için, birden fazla ekstrüzyondan sonra, 2 saat boyunca 180°C'de gerilim giderici bir tavlama işlemi yapılmalıdır; aksi takdirde, orta ve dış öngerilmeli halkalar aniden çatlayabilir ve sadece kalıba zarar vermekle kalmaz, aynı zamanda kişisel kazalara da neden olabilir.
Kalıbın hizmet ömrünü uzatmak için eksiksiz bir bakım ve onarım sistemi oluşturulmalıdır. Presi derhal ayarlamak ve kalıp onarımı, ayarı ve depolama işlerini gerçekleştirmek için atanmış personel görevlendirilmelidir. Kalıbın depolanması ve taşınması sırasında paslanmayı önleyici tedbirler alınmalı ve hasarı önlemek için üst ve alt kalıp tabanları arasında koruma sağlayan sınır blokları bulunmalıdır.