Le traitement de surface consiste à modifier l'état et les propriétés de la surface des pièces en utilisant des technologies de pointe à l'intersection de la physique, de la chimie, de la métallurgie et du traitement thermique, afin d'optimiser la combinaison avec le matériau de base et de répondre à des exigences de performance prédéterminées.
Le traitement de surface consiste à former artificiellement une couche à la surface du matériau de base qui présente des propriétés mécaniques, physiques et chimiques différentes de celles du matériau de base, dans le but de répondre aux exigences du produit en matière de résistance à la corrosion, de résistance à l'usure, de décoration ou d'autres fonctions spéciales.
En fonction de l'objectif du traitement de surface, les technologies de traitement de surface peuvent être divisées en traitement de renforcement de la surface, traitement décoratif de la surface, traitement anticorrosion de la surface et traitement de réparation de la surface. Les méthodes courantes de traitement de surface comprennent la pulvérisation thermique, le grenaillage de précontrainte, le sablage, le laminage de surface, le placage ionique, le renforcement de surface par laser, le polissage, la galvanoplastie générale, la galvanoplastie spéciale, l'oxydation de l'acier, la phosphatation de l'acier, l'oxydation anodique de l'aluminium et le traitement de coloration, la peinture et la pulvérisation de plastique, etc.
I. Grenaillage de précontrainte
Le grenaillage de précontrainte, également connu sous le nom de renforcement par grenaillage, est l'une des méthodes efficaces pour réduire la fatigue des pièces et améliorer leur durée de vie. Le grenaillage de précontrainte est un processus dans lequel d'innombrables petits médias sphériques appelés grenaille d'acier sont projetés en continu à grande vitesse et martelés sur la surface de la pièce, produisant ainsi une couche de contrainte de compression résiduelle sur la surface.
En effet, lorsque chaque grenaille d'acier frappe la pièce métallique, elle agit comme un mini maillet qui martèle la surface, créant ainsi de petites indentations ou dépressions. Pour former ces dépressions, la couche superficielle du métal doit subir un étirement.
Les grains comprimés sous la surface tentent de redonner à la surface sa forme initiale, générant ainsi un hémisphère sous une force de compression élevée. D'innombrables dépressions se chevauchent pour former une couche uniforme de contrainte de compression résiduelle. En fin de compte, la résistance à la fatigue de la pièce est grandement améliorée et sa durée de vie est prolongée sous la protection de la couche de contrainte de compression.
L'équipement utilisé pour le grenaillage de précontrainte est une grenailleuse, comme le montre la figure 1.
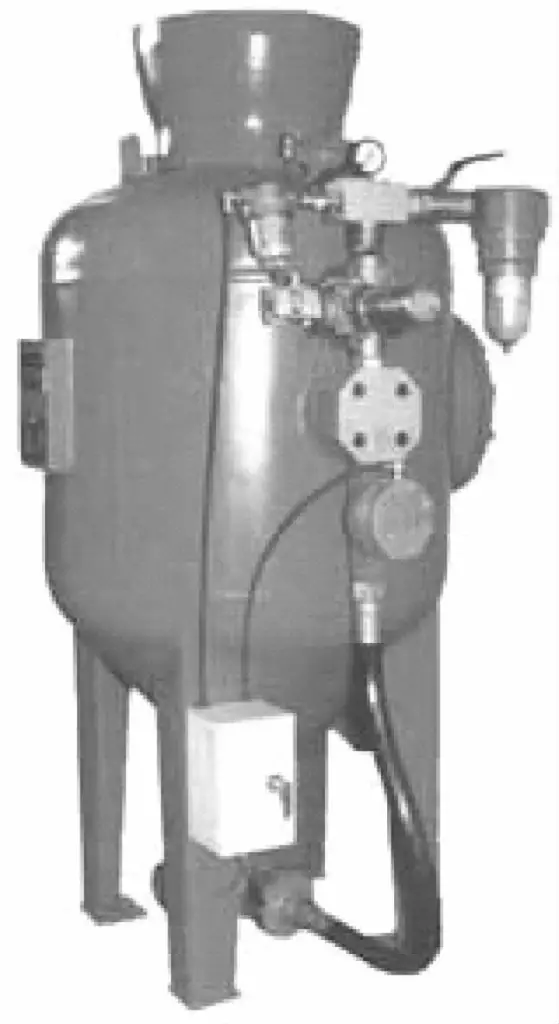
Les méthodes de grenaillage comprennent généralement le grenaillage manuel et le grenaillage mécanique, comme le montrent les figures 2 et 3.
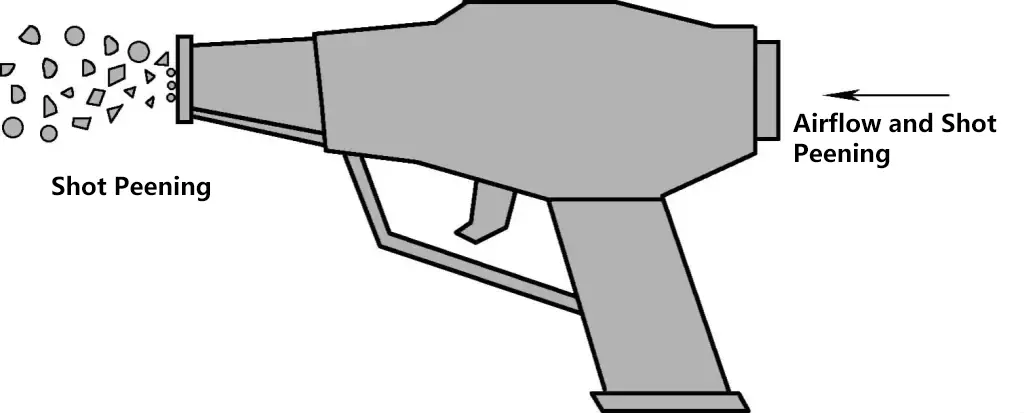
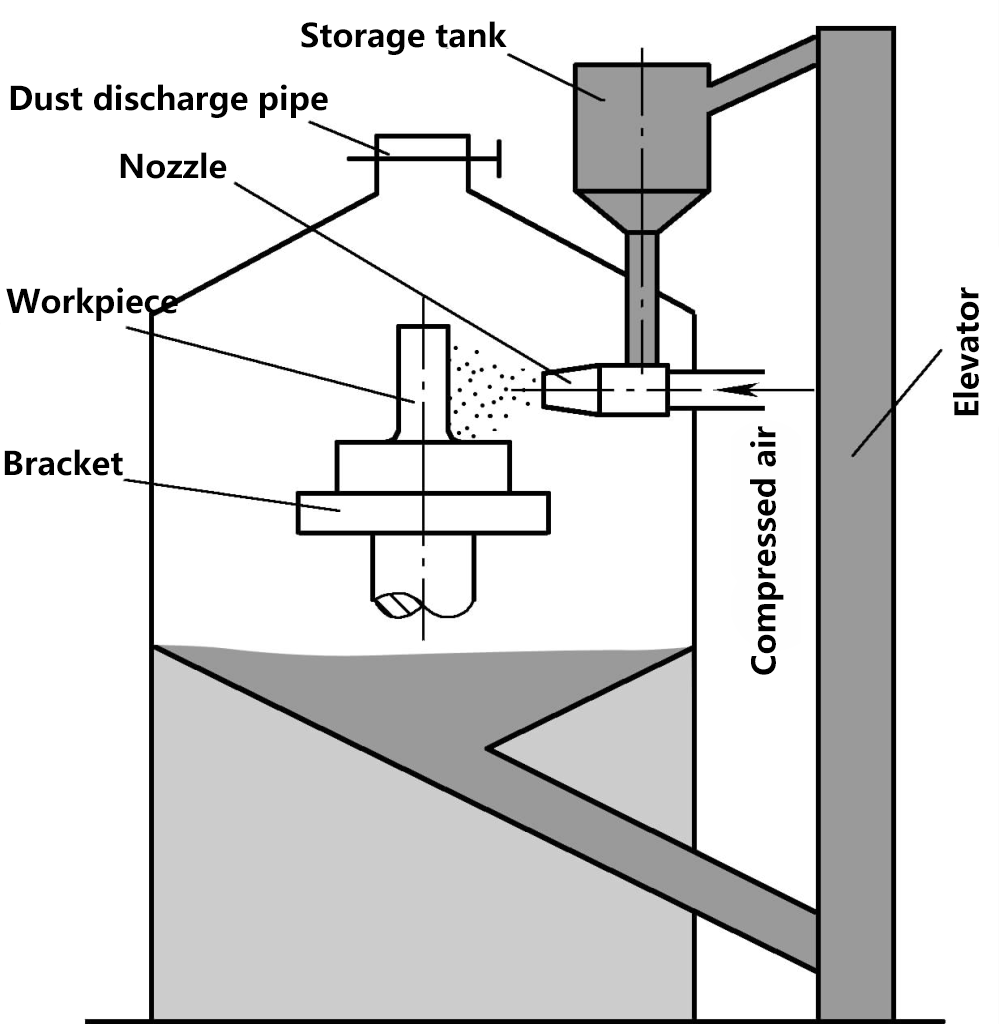
Les médias couramment utilisés pour le grenaillage de précontrainte sont des grains de sable ou des grenailles métalliques d'un diamètre de 0,5 à 2 mm, le sable étant souvent constitué d'Al₂O₃ ou de SiO₂. L'effet du traitement de surface est lié à la taille, à la vitesse et à la durée de la grenaille. Le grenaillage de précontrainte est utilisé pour améliorer la résistance des pièces, la résistance à l'usure, la résistance à la fatigue et la résistance à la corrosion, ainsi que pour la finition mate de la surface, la désoxydation et l'amélioration de la résistance à la corrosion. l'élimination des contraintes résiduelles dans les pièces moulées, forgées et soudées.
Le grenaillage de précontrainte est un procédé de renforcement de surface largement adopté dans les usines, avec un équipement simple, un faible coût, aucune restriction sur la forme et la position de la pièce, une opération pratique, mais un environnement de travail médiocre.
Le grenaillage de précontrainte et le sablage utilisent tous deux de l'air à haute pression ou de l'air comprimé pour souffler à grande vitesse sur la surface de la pièce afin d'obtenir un effet de nettoyage, mais le choix du fluide est différent, de même que les effets, comme le montre la figure 4.

II. Le sablage
Le sablage est un procédé qui consiste à utiliser de l'air comprimé mécanique ou purifié pour projeter un flux de sable sur la surface des produits métalliques, en utilisant l'impact puissant du flux de sable pour éliminer la saleté, à des fins de nettoyage ou de décoration.
Les principales utilisations du sablage sont les suivantes
- Élimination de la rouille, des scories de soudage, des dépôts de carbone, des vieilles couches de peinture et de la graisse à la surface des pièces.
- Élimination du sable de moulage et de la calamine de la surface des pièces moulées, forgées ou traitées thermiquement.
- Éliminer les bavures ou les rayures directionnelles de la surface des pièces.
- Réduire la rugosité de la surface de pièces, en améliorant l'adhérence entre le substrat et la couche de revêtement.
- Les pièces obtiennent ainsi un état de réflexion mat et diffus. Le sable utilisé pour le sablage doit être sec, propre, exempt d'impuretés et ne pas affecter les propriétés du matériau. L'équipement de sablage courant est illustré à la figure 5.
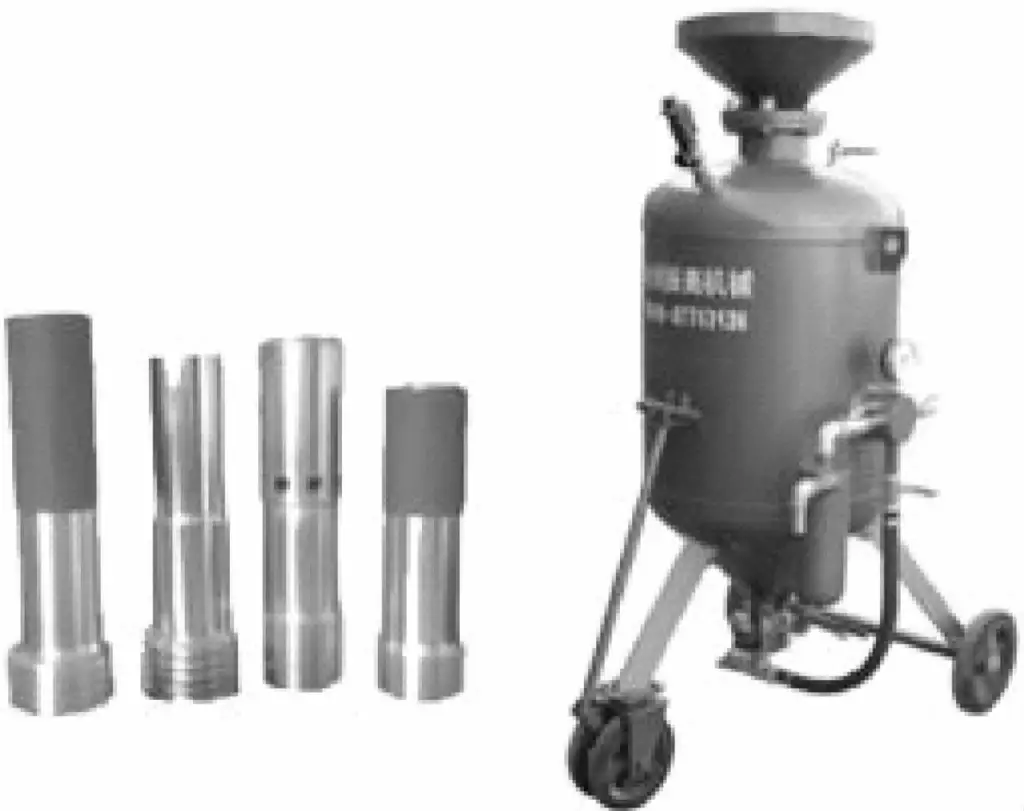
III. La galvanoplastie
La galvanoplastie permet de recouvrir des matériaux ou des pièces d'une couche de revêtement relativement uniforme et dense ayant une bonne adhérence, afin de modifier les caractéristiques et l'aspect de leur surface, dans le but de protéger ou de décorer les matériaux. En plus de rendre les produits beaux et durables, la galvanoplastie peut également remplir des fonctions spéciales, telles que l'amélioration de la résistance à la corrosion, de la résistance à l'usure, de la résistance à la chaleur, de la réflectivité, de la conductivité, de la lubrification et de la dureté de la surface des produits métalliques, ainsi que la réparation des dimensions des pièces usées et des défauts de surface.
Par exemple, le placage d'or sur les dispositifs semi-conducteurs permet d'obtenir une résistance de contact très faible ; le placage d'étain sur les composants électroniques permet d'obtenir une bonne soudabilité ; le placage de chrome sur les segments de piston et les arbres permet d'obtenir une résistance élevée à l'usure ; ainsi que le placage de cuivre pour empêcher la carburation locale, et le placage d'étain pour empêcher la nitruration locale. Le processus général de galvanoplastie est illustré à la figure 6.

Actuellement, les procédés de galvanoplastie les plus utilisés sont le cuivrage, le nickelage, le chromage, le zingage, l'argenture, l'orfèvrerie, etc. Prenons l'exemple du nickelage : le pièces métalliques sont immergés dans une solution de sel métallique (NiSO₄) comme cathode, avec une plaque de nickel comme anode, et après connexion à une source d'énergie à courant continu, une couche de nickel métallique sera déposée sur la pièce à usiner, le principe de fonctionnement est illustré à la figure 7.
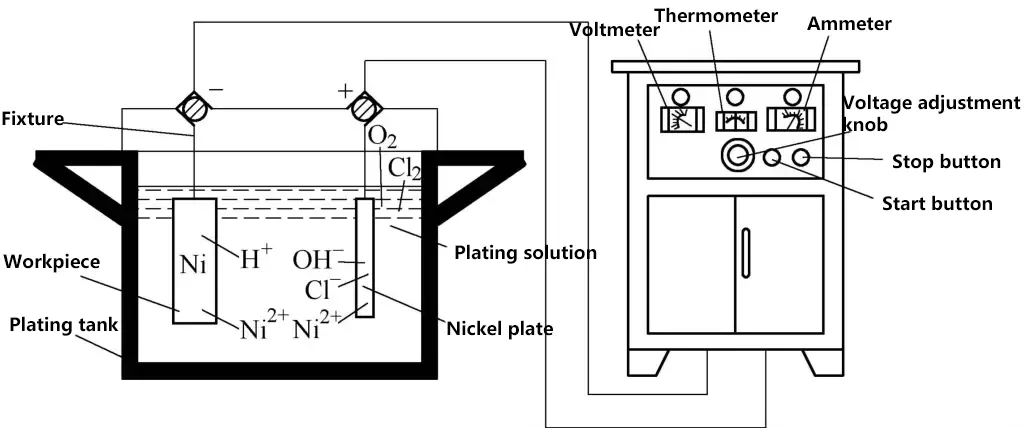
1. Placage électrolytique conventionnel
(1) Placage au zinc
Le zingage des pièces d'acier sert principalement de protection contre la corrosion et représente 1/3 à 1/2 de toutes les pièces galvanisées, ce qui en fait le volume de production le plus important parmi tous les types de zingage. Le zingage présente les avantages d'un faible coût, d'une bonne résistance à la corrosion et d'un aspect esthétique. Il est largement utilisé dans l'industrie légère, l'électromécanique, les machines agricoles et les industries de défense.
(2) Placage au cadmium
Le cadmiage des pièces en acier, dans les environnements marins et atmosphériques chauds et humides, offre une meilleure protection que le zingage. Les pièces des industries aéronautique, maritime et électronique utilisent principalement le cadmiage. Cependant, les sels de cadmium sont toxiques et provoquent une grave pollution de l'environnement, ce qui limite l'application du cadmiage.
(3) Étamage
Les produits de corrosion de l'étain sont inoffensifs pour l'homme et faciles à souder, ce qui fait que l'étamage est largement utilisé dans l'emballage des boîtes de conserve, les ustensiles de cuisine, la vaisselle et l'industrie électronique.
(4) Placage au cuivre
Le cuivrage est souvent utilisé comme couche intermédiaire pour d'autres revêtements afin d'améliorer l'adhérence entre le revêtement de surface et le métal de base. Dans l'industrie électrique, le fil de fer cuivré peut également être utilisé pour remplacer les conducteurs en cuivre pur afin de réduire la consommation de cuivre.
(5) Nickelage
Le nickelage a un large éventail d'applications, utilisées à la fois pour la décoration protectrice et la fonctionnalité. La première est principalement utilisée pour les revêtements décoratifs de protection sur les pièces de bicyclettes, de montres, d'appareils ménagers, de quincaillerie, d'automobiles, d'appareils photo, etc., tandis que la seconde est principalement utilisée pour la galvanoplastie de réparation des produits sujets à l'usure.
(6) Chromage
Le chrome peut conserver son éclat pendant longtemps dans l'atmosphère, ne réagit pas aux solutions alcalines, à l'acide nitrique, à l'acide sulfurique et à de nombreux acides organiques. Le chromage présente une dureté élevée, une excellente résistance à l'usure et un coefficient de frottement plus faible. Il est donc couramment utilisé comme revêtement décoratif protecteur pour empêcher le métal de base de rouiller, et est également souvent utilisé pour améliorer la résistance à l'usure des produits.
2. Placage électrolytique spécial
(1) Placage à la brosse
Le placage à la brosse n'utilise pas de bain de placage. La pièce en rotation est reliée à l'électrode négative d'une source de courant continu, le stylo de placage est relié à l'électrode positive et l'extrémité avant du stylo de placage est enveloppée de coton dégraissé. La solution de placage versée est trempée dans le manchon de coton dégraissé. Sous l'action du champ électrique, les cations métalliques de la solution de placage gagnent des électrons à la surface de la pièce (cathode) et se déposent sur la surface, formant une couche de placage électrolytique, comme le montre la figure 8.
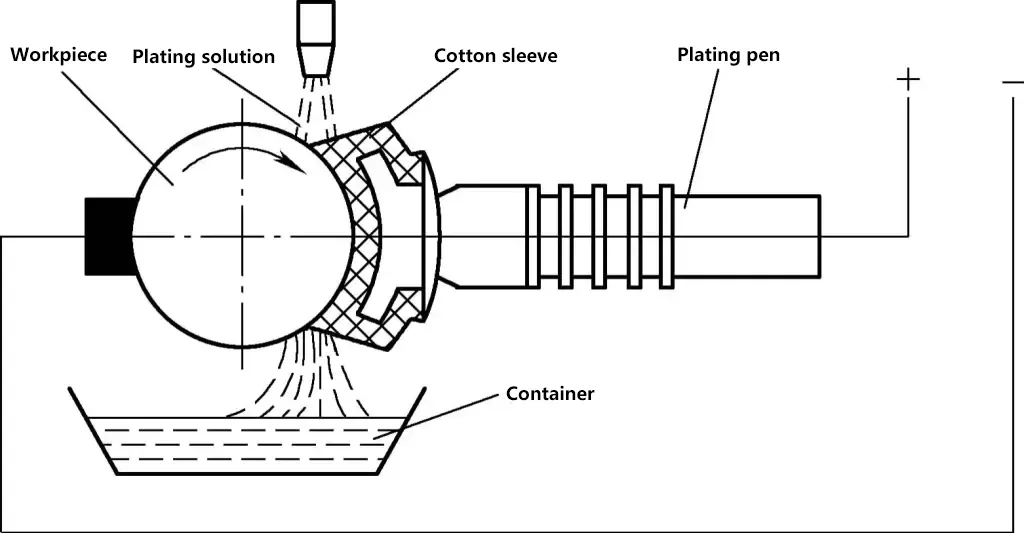
L'épaisseur de la couche de placage par brossage peut atteindre 0,01 à 0,5 mm, avec une bonne qualité, une grande force d'adhérence et une vitesse plus rapide que le placage en cuve. L'équipement de placage par brossage est simple, son fonctionnement est flexible et il peut être utilisé pour la galvanoplastie locale et les opérations sur le terrain.
(2) Placage électrolytique non métallique
La galvanoplastie non métallique fait référence à la galvanoplastie de produits non métalliques tels que les plastiques, le verre, les céramiques et les fibres. Le processus clé de la galvanoplastie non métallique est la métallisation de surface, qui génère une couche conductrice sur le substrat non métallique pour faciliter la galvanoplastie. Les méthodes de métallisation de surface comprennent le placage chimique, la pulvérisation et le brossage. La galvanoplastie non métallique est principalement utilisée pour certaines pièces décoratives des automobiles et des avions, ainsi que pour le blindage des instruments électroniques et des fibres de carbone.
IV. Placage chimique
La technologie du placage chimique est un processus de dépôt de métal qui se produit sous l'action catalytique de métauxLe dépôt chimique se fait par des réactions d'oxydoréduction contrôlables. Par rapport à la galvanoplastie, la technologie du placage chimique présente les caractéristiques suivantes : revêtement uniforme, petits trous d'épingle, pas besoin d'équipement d'alimentation en courant continu, possibilité de déposer sur des non-conducteurs, et certaines propriétés spéciales.
En outre, en raison du faible rejet de liquides résiduaires, de la pollution environnementale minimale et du coût réduit de la technologie de placage chimique, celle-ci a progressivement remplacé la galvanoplastie dans de nombreux domaines, devenant ainsi un processus de traitement de surface respectueux de l'environnement. Actuellement, la technologie de placage chimique est largement utilisée dans des industries telles que l'électronique, la fabrication de vannes, les machines, la pétrochimie, l'automobile et l'aérospatiale.
Caractéristiques du placage chimique :
- Permet d'obtenir une épaisseur uniforme de la couche de placage sur des pièces de forme complexe ;
- La couche de placage présente des grains fins et denses, avec moins de pores et de fissures ;
- Peut déposer des couches métalliques sur des matériaux non métalliques.
V. Oxydation et phosphatation de l'acier
1. L'oxydation
L'oxydation est une protection des matériaux technique qui consiste à chauffer l'acier à l'air ou en les immergeant directement dans une solution oxydante concentrée pour produire un film de Fe₃O₄ extrêmement fin sur leur surface, également connu sous le nom de bleuissement ou de noircissement.
Le processus d'oxydation de l'acier est le suivant : dégraissage chimique → lavage à l'eau chaude → lavage à l'eau froide → première oxydation → deuxième oxydation → lavage à l'eau froide → lavage à l'eau chaude → traitement supplémentaire → lavage à l'eau froide → lavage à l'eau chaude → séchage par soufflage ou séchage → inspection → immersion dans l'huile → stockage.
2. Phosphatation
L'immersion de pièces d'acier dans une solution composée principalement de phosphates, provoquant le dépôt à la surface d'un film de conversion de phosphate cristallin insoluble dans l'eau, est connue sous le nom de traitement de phosphatation. Les solutions de traitement par phosphatation les plus courantes sont les solutions de phosphate de manganèse et de fer et les solutions de phosphate de zinc. L'épaisseur du film de phosphatation après traitement est généralement de 1~5μm, et sa résistance à la corrosion est 2~10 fois supérieure à celle du traitement par oxydation.
Le film de phosphatation a une forte adhérence au substrat, une bonne résistance à la corrosion et des performances d'isolation élevées. Il présente une bonne résistance à la corrosion dans l'atmosphère, les huiles, le benzène et le toluène, ainsi qu'une excellente absorption de l'huile, de la cire, des pigments et de la peinture, ce qui en fait un apprêt approprié pour la peinture.
Toutefois, la résistance et la dureté du film de phosphatation lui-même sont relativement faibles, avec une certaine fragilité. Lorsque le matériau en acier est déformé de manière significative, de fines fissures peuvent apparaître, et il n'est pas résistant aux chocs, avec une mauvaise résistance à la corrosion dans l'acide, l'alcali, l'eau de mer et la vapeur. Après le traitement de phosphatation, la peinture de surface ou l'immersion dans l'huile peuvent améliorer considérablement la résistance à la corrosion.
L'équipement nécessaire au traitement de phosphatation est simple, facile à utiliser, peu coûteux et très productif. Il peut être utilisé comme couche de protection pour les pièces en acier des équipements mécaniques généraux, ainsi que comme couche de lubrification et de protection pour diverses armes.
VI. Revêtement
Le revêtement consiste à recouvrir des surfaces métalliques et non métalliques d'une couche protectrice ou décorative. Les procédés de revêtement les plus courants sont présentés dans le tableau 1.
Tableau 1 Procédés de revêtement courants
Numéro de série | Méthodes de peinture | Contenu | Caractéristiques | Domaine d'application |
1 | Brossage | Brossage manuel avec différentes brosses | Économie de matériel et de main-d'œuvre, mais physiquement exigeant | Toute forme de pièce, presque toute peinture |
2 | Revêtement par immersion automatique | La pièce est automatiquement plongée dans le réservoir de peinture par le mouvement de la chaîne sur le convoyeur aérien. | Économie de main-d'œuvre et de matériel, productivité élevée, mais évaporation d'une grande quantité de solvant du réservoir de peinture, exigences strictes en matière de protection contre l'incendie. | Production en chaîne à grande échelle |
3 | Pulvérisation manuelle (y compris la pulvérisation sans air à haute pression) A l'aide d'air comprimé, le pistolet pulvérise la peinture et la projette sur la surface de la pièce pour former un film. | Film de peinture uniforme, bonne qualité, mais gros gaspillage de peinture | Convient pour les pièces de formes diverses, en particulier pour les pièces de grande surface | Flow Coating |
4 | La pièce est placée sur un établi et le liquide de peinture est pulvérisé sur la pièce à l'aide d'une pompe de circulation. | Efficacité de travail élevée, faible perte de peinture liquide, convient aux opérations de la chaîne d'assemblage | Convient pour les grandes séries de revêtements d'apprêt de pièces uniques | Revêtement des rideaux |
5 | La pièce passe sous un rideau de peinture liquide qui s'écoule en continu pour le revêtement. | Rendement élevé, faible perte de liquide de peinture, convient aux opérations de la chaîne de montage, mais ne peut pas recouvrir la surface verticale de la pièce. | Convient à la production par lots et au revêtement d'une seule face de pièces de grande taille | Revêtement en lit fluidisé |
6 | Revêtement en lit fluidisé | En utilisant le revêtement en poudre dans une certaine pression d'air pour présenter un état "bouillant", il fusionne et refroidit sur la surface de la pièce préchauffée légèrement au-dessus de son point de fusion pour former un film. | L'épaisseur du revêtement est importante et la vitesse de revêtement est rapide. | Convient pour les pièces de grande taille et de forme différente |
7 | Revêtement au rouleau | Utilisation de machines de revêtement de rouleaux pour le revêtement de rouleaux | Peut utiliser des revêtements à viscosité plus élevée, l'épaisseur du film est uniforme, ce qui favorise la mécanisation et la production automatisée. | Convient pour le revêtement de panneaux plats |
Dans les applications de production, les procédés de revêtement les plus couramment utilisés sont la pulvérisation sans air à haute pression et la pulvérisation électrostatique.
1. Pulvérisation sans air à haute pression
La pulvérisation sans air à haute pression utilise de l'air comprimé à basse pression (0,4~0,6N/mm²) pour actionner une pompe à haute pression, pressurisant le revêtement à 10~20N/mm², puis le pulvérisant à travers une buse spéciale d'un pistolet de pulvérisation à haute pression pour former un revêtement, comme le montre la figure 9.
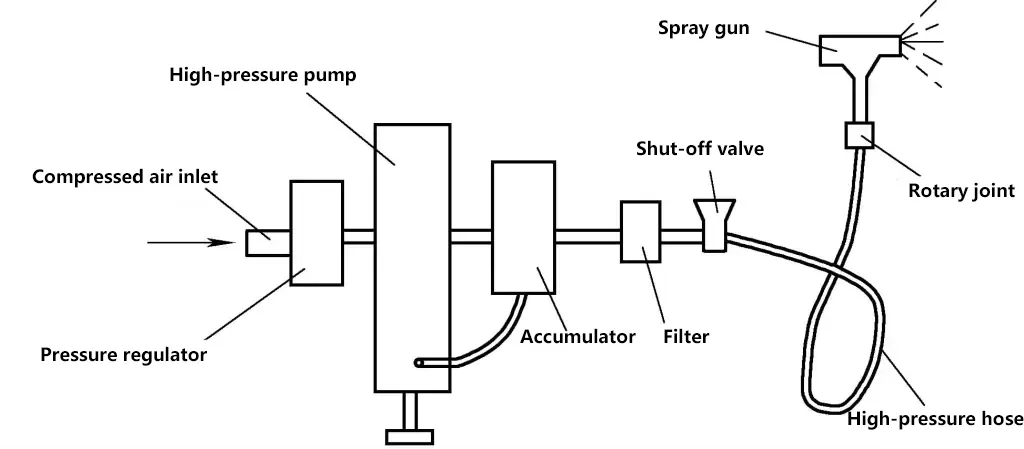
Les caractéristiques de la pulvérisation sans air à haute pression sont les suivantes :
- Pas de phénomène de rebond des particules de peinture et d'envol du brouillard de peinture, comme c'est le cas avec la pulvérisation générale d'air comprimé ;
- Productivité élevée, plusieurs fois à des dizaines de fois supérieure à celle de la pulvérisation d'air comprimé ;
- Adapté à la pulvérisation de revêtements à haute viscosité, une seule application permet d'obtenir une épaisseur de revêtement de 100~300μm.
2. Pulvérisation électrostatique
La pulvérisation électrostatique est une méthode de pulvérisation qui utilise un champ électrostatique à haute tension pour que les particules de peinture chargées négativement se déplacent dans la direction opposée au champ électrique et adsorbent les particules de peinture sur la surface de la pièce, comme le montre la figure 10. L'équipement de pulvérisation électrostatique se compose d'un pistolet de pulvérisation, d'un godet de pulvérisation et d'une alimentation électrique haute tension pour la pulvérisation électrostatique, etc.
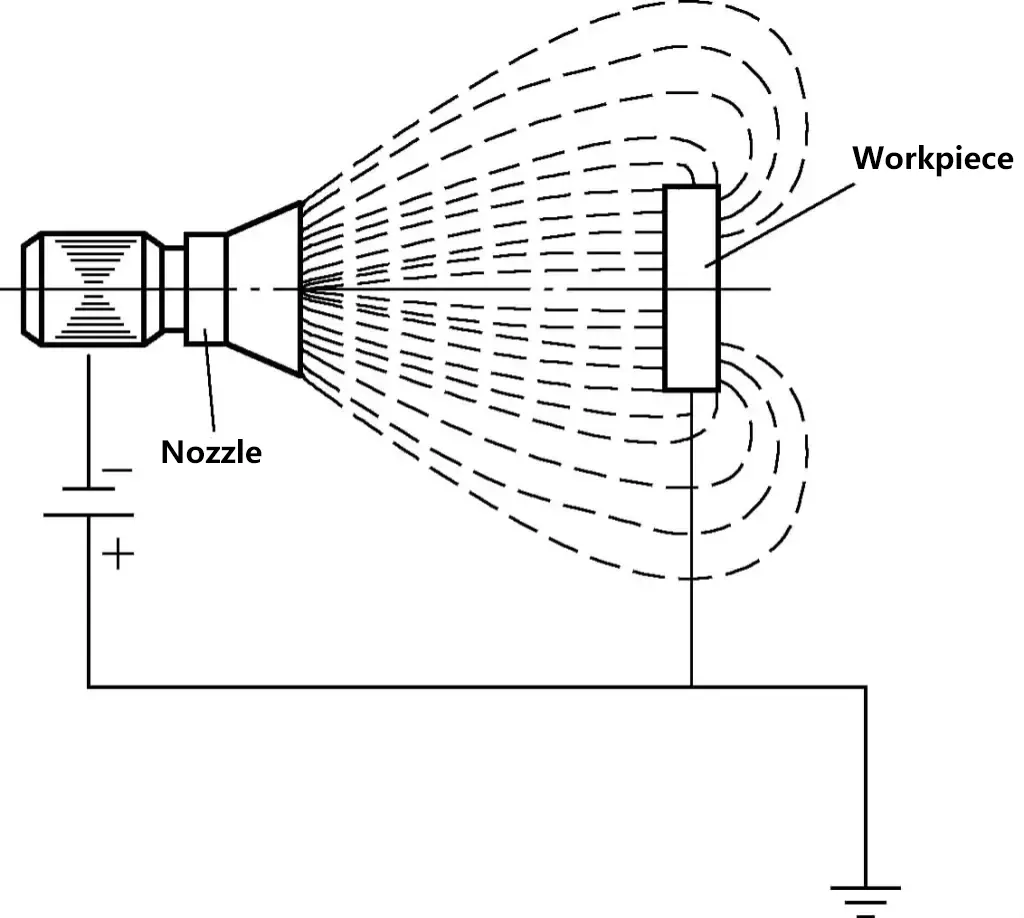
La pulvérisation électrostatique a une productivité plus élevée et une meilleure qualité de film que la pulvérisation ordinaire. Elle est couramment utilisée dans les lignes de production automatique d'automobiles, de bicyclettes et d'équipements électromécaniques produits en série. La figure 11 présente un schéma de la pulvérisation électrostatique d'une carrosserie de voiture.
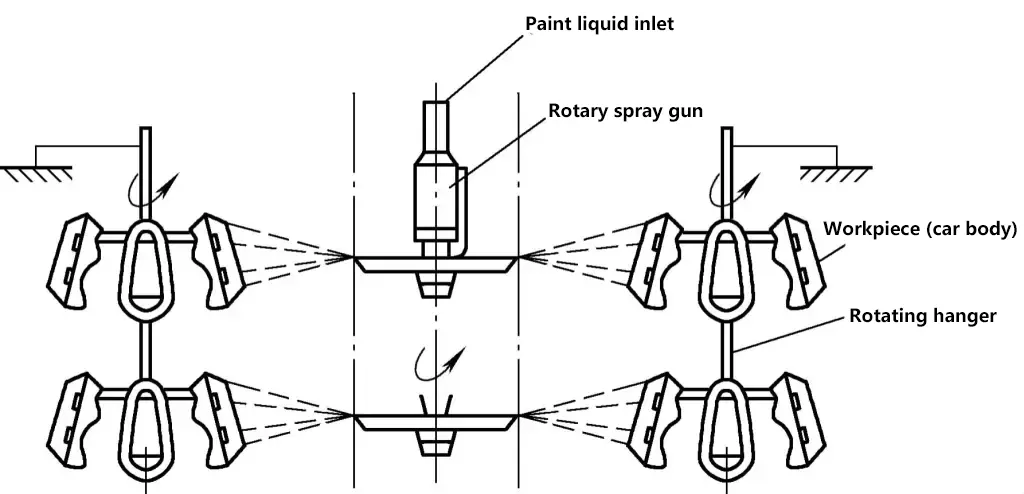
VII. Le polissage
Le polissage est une méthode de traitement pour la finition de la surface des pièces, qui ne permet généralement d'obtenir qu'une surface lisse, et ne peut pas améliorer ou même maintenir la précision de traitement d'origine. En fonction des conditions de prétraitement, la valeur de rugosité de surface Ra après polissage peut atteindre 0,008~1,6μm.
Le polissage peut être divisé en polissage mécanique, polissage chimique et polissage électrochimique.
1. Polissage mécanique
(1) Polissage des roues
Utilisation d'une roue de polissage flexible tournant à grande vitesse et d'abrasifs extrêmement fins pour rouler et micro-couper la surface de la pièce afin de la polir. Le disque de polissage est constitué de plusieurs couches de toile, de feutre ou de cuir et est utilisé pour le polissage de pièces plus grandes. Le processus d'opération de polissage à la meule est illustré à la figure 12.
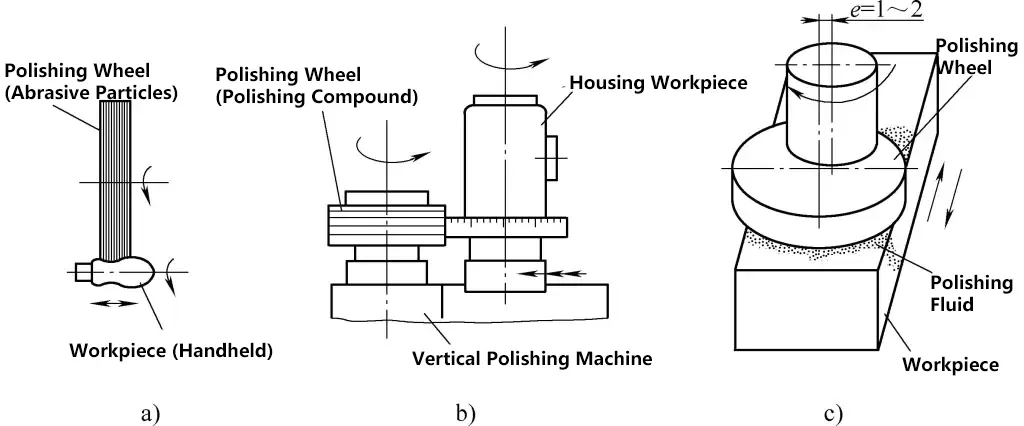
a) Polissage manuel
b) Polissage vertical
c) Polissage horizontal
(2) Polissage vibratoire
Les pièces à usiner, les abrasifs et le liquide de polissage sont chargés dans une boîte vibrante. Sous l'effet des vibrations de la caisse, les pièces se frottent les unes aux autres et aux abrasifs. Combiné à l'action chimique du liquide de polissage, l'huile et la rouille présentes à la surface des pièces sont éliminées et les pics sont broyés, ce qui permet d'obtenir une surface lisse.
Les caractéristiques du polissage vibratoire sont les suivantes :
- Élimine rapidement les bavures autour de la pièce, y compris les petits trous intérieurs, les trous de tube et les angles morts dans les crevasses.
- La pièce polie n'affecte pas la précision d'origine ; il n'y a pas de changement de forme et de taille, et la valeur de rugosité de surface Ra peut atteindre 0,01~0,1μm, présentant un éclat métallique brillant.
- Le temps de traitement est court, de l'ordre de 5~20min.
- Fonctionnement pratique, faible coût, pas de pollution.
2. Polissage chimique
Le polissage chimique consiste à immerger des pièces métalliques dans une solution chimique spéciale et à utiliser le phénomène selon lequel les parties en relief de la surface métallique se dissolvent plus rapidement que les parties en creux pour obtenir un polissage de la surface des pièces. L'avantage du polissage chimique est que l'équipement est simple et qu'il permet de traiter des pièces de formes relativement complexes.
Inconvénients du polissage chimique :
- La qualité du polissage n'est pas aussi bonne que celle du polissage électrolytique ;
- L'ajustement et la régénération de la solution utilisée sont relativement difficiles, ce qui limite son application ;
- Au cours du processus d'exploitation, l'utilisation d'acide nitrique émet parfois une grande quantité de gaz nocifs de couleur jaune-brun, ce qui entraîne une grave pollution de l'environnement.
3. Polissage électrochimique
Le polissage électrochimique, également connu sous le nom de polissage électrolytique, est un processus dans lequel la pièce à polir sert d'anode, un métal insoluble sert de cathode, les deux électrodes sont simultanément immergées dans une cellule électrolytique et un courant continu est appliqué pour produire une dissolution anodique sélective, ce qui permet de polir la surface de la pièce.
Le polissage électrochimique est similaire au polissage chimique, à la différence que le courant continu est également appliqué, que la pièce est connectée à l'anode, que la dissolution anodique se produit et que le polissage est également réalisé en utilisant le phénomène selon lequel les parties surélevées de la surface métallique se dissolvent plus rapidement que les parties en retrait.
Avantages du polissage électrolytique :
- La couleur interne et externe est homogène, le lustre durable et même les recoins que le polissage mécanique ne peut atteindre peuvent être nivelés ;
- Productivité élevée, faible coût ;
- Peut améliorer la résistance à la corrosion de la surface de la pièce.
VIII. Le brunissage
Le brunissage est un procédé de finition sous pression qui utilise les caractéristiques de plasticité à froid des métaux à température ambiante. Une certaine pression est appliquée à la surface de la pièce à l'aide d'un outil de brunissage, ce qui provoque un écoulement plastique du métal de surface qui remplit les creux résiduels d'origine, réduisant ainsi la rugosité de la surface de la pièce.
En raison de la déformation plastique du métal de surface bruni, la structure de la surface est durcie à froid et les grains sont affinés, formant une structure fibreuse dense et créant une couche de contrainte résiduelle, améliorant la résistance et la dureté de la surface de la pièce, améliorant ainsi la résistance à l'usure, la résistance à la corrosion et la qualité d'accouplement de la pièce. Le brunissage est une méthode de traitement des matières plastiques sans enlèvement de copeaux.
Les avantages du brunissage sont les suivants :
- Améliore la rugosité de la surface, la valeur de la rugosité de la surface peut fondamentalement atteindre Ra≤0,08μm.
- Corrige l'arrondi, l'erreur d'arrondi n'est pas supérieure à 0,01 mm.
- Augmente la dureté de la surface.
- La pièce traitée présente une couche de contrainte résiduelle qui améliore la résistance à la fatigue d'environ 30%.
- Améliore la qualité de l'accouplement, réduit l'usure et prolonge la durée de vie des pièces.
IX. Gonflement de la surface Éclaircissement
Le brunissage consiste à presser une bille d'acier ou un autre outil de brunissage façonné, dont le diamètre est légèrement supérieur à celui de l'ouverture, à travers le trou intérieur usiné de la pièce à température ambiante afin d'obtenir une surface précise, lisse et renforcée, comme le montre la figure 13.
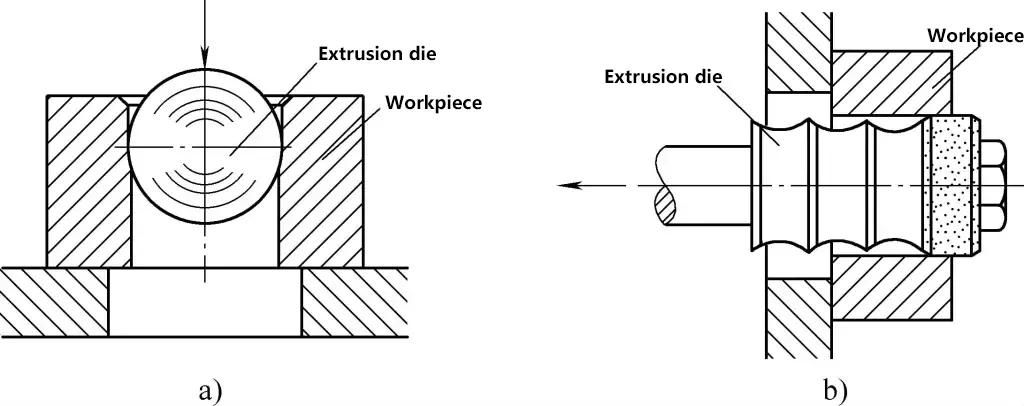
a) Polissage à la bille d'acier
b) Brûlage avec des outils d'autres formes
La surépaisseur de brunissage est généralement de 0,07~0,015 mm. Après le brunissage, le degré de tolérance dimensionnelle peut atteindre IT5~IT7, et la valeur de rugosité de surface Ra peut atteindre 0,025~0,8μm. Le brunissage est généralement effectué sur une presse ou un banc d'étirage.
X. Revêtement
1. Pulvérisation thermique
La projection thermique consiste à chauffer des matériaux métalliques ou non métalliques à l'état fondu et à les projeter en continu sur la surface de la pièce à l'aide de gaz comprimé afin de former un revêtement fermement lié au substrat, conférant ainsi à la couche superficielle de la pièce les propriétés physiques et chimiques requises.
La technologie de projection thermique crée une surface de travail spéciale sur la surface des matériaux ordinaires, remplissant une série de fonctions telles que la protection contre la corrosion, la résistance à l'usure, la réduction des frottements, la résistance aux températures élevées, la résistance à l'oxydation, l'isolation thermique, l'isolation électrique, la conductivité électrique et la protection contre les rayonnements micro-ondes, dans le but d'économiser des matériaux et de l'énergie. La surface de travail spéciale est appelée revêtement, et la méthode de fabrication du revêtement est appelée projection thermique, comme le montre la figure 14.
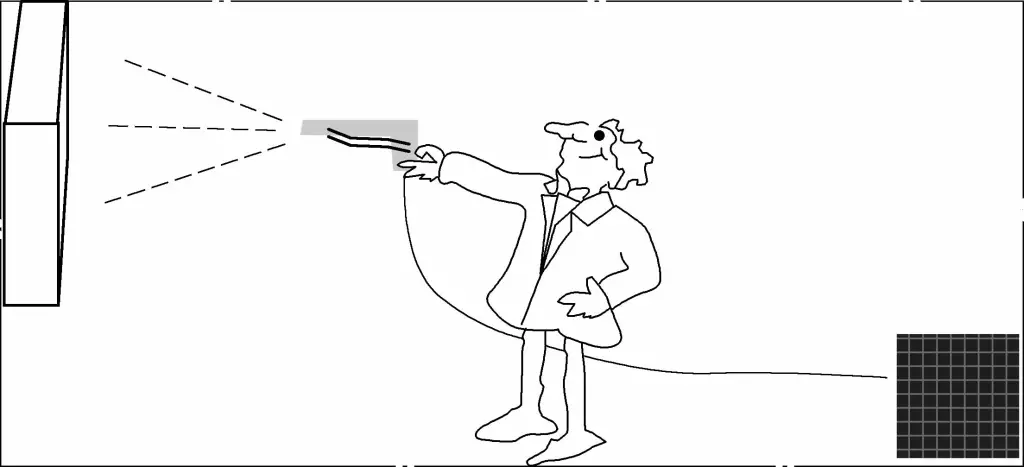
Les caractéristiques de la pulvérisation thermique sont les suivantes :
(1) Processus flexible
Les objets concernés par la projection thermique peuvent être de petite taille, comme des trous intérieurs de 10 mm, ou de grande taille, comme des ponts et des tours en fer. La projection peut être effectuée à l'intérieur ou sur le terrain ; elle peut être appliquée à toute la surface ou localement.
(2) Déformation minimale de la pièce sous contrainte
Pendant la pulvérisation, le substrat peut être maintenu à une faible température, ce qui entraîne une très faible déformation de la pièce.
(3) Productivité élevée
Le poids du matériau pulvérisé par heure varie de quelques kilogrammes à plusieurs dizaines de kilogrammes, ce qui se traduit par une productivité élevée.
Les applications de la projection thermique sont les suivantes :
(1) Protection contre la corrosion
Principalement utilisé pour la pulvérisation anticorrosion des grandes portes d'eau en acier, des cylindres de séchage des machines à papier, des structures métalliques souterraines dans les mines de charbon, des tours de transmission à haute tension, des antennes de stations de télévision, des grands ponts en acier, des grands réservoirs et des pipelines dans les usines chimiques.
(2) Résistance à l'usure
En pulvérisant des pièces usées en vue de leur réparation, ou en pulvérisant au préalable des matériaux résistants à l'usure sur des pièces sujettes à l'usure, telles que les arbres principaux de ventilateurs, les tuyères de hauts fourneaux, les vilebrequins d'automobiles, les broches de machines-outils, les rails de guidage de machines-outils, les chemises de cylindres de moteurs diesel, les tiges de forage dans les champs pétrolifères et les lames de machines agricoles.
(3) Couches fonctionnelles spéciales
La pulvérisation permet d'obtenir certaines propriétés spéciales de la couche de surface, telles que la résistance aux températures élevées, l'isolation thermique, la conductivité électrique, l'isolation, la protection contre les radiations, etc., qui sont largement utilisées dans l'aérospatiale, l'énergie atomique et d'autres secteurs.
Les techniques courantes de pulvérisation thermique comprennent la pulvérisation à la flamme, la pulvérisation à l'arc, la pulvérisation au plasma, etc.
2. Pulvérisation de flammes
En utilisant une flamme comme source de chaleur, les matériaux métalliques et non métalliques sont chauffés jusqu'à l'état fondu et propulsés par un flux d'air à grande vitesse pour former un brouillard qui est pulvérisé sur le substrat. Les minuscules particules fondues qui frappent le substrat subissent une déformation plastique et forment un revêtement déposé en couches. Ce processus est connu sous le nom de pulvérisation à la flamme, comme le montre la figure 15. Le pistolet de pulvérisation à flamme est illustré à la figure 16.
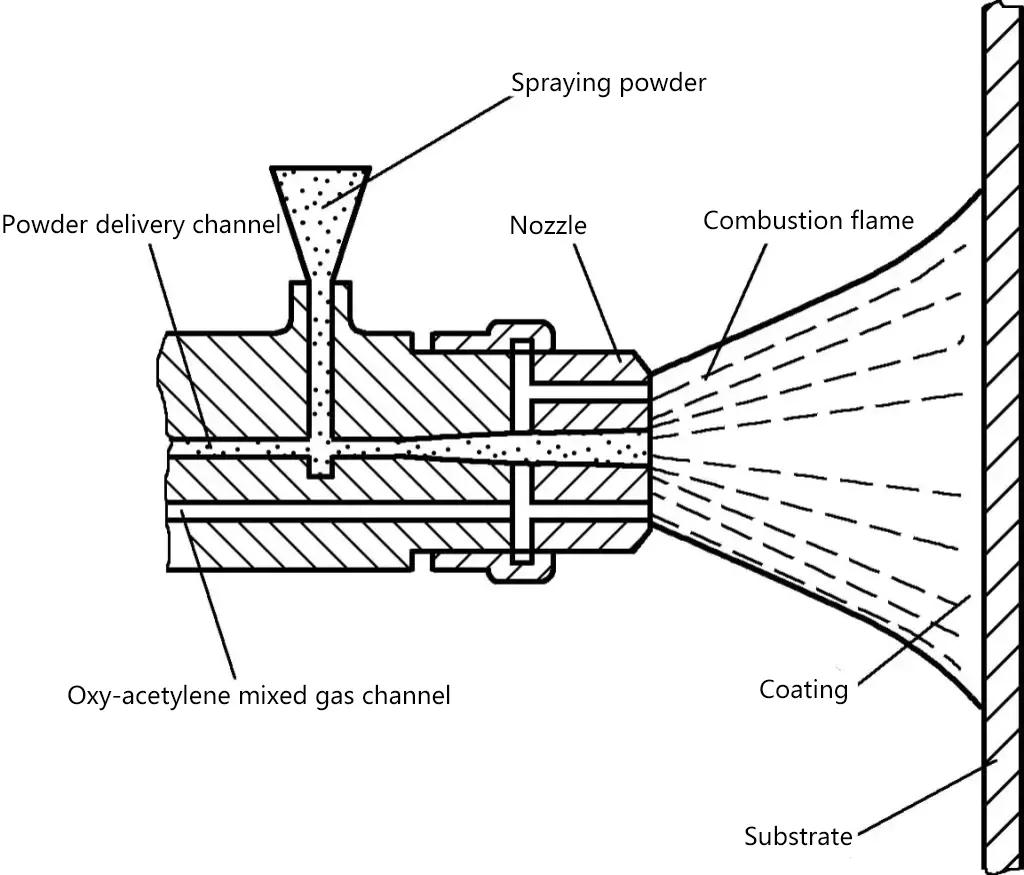
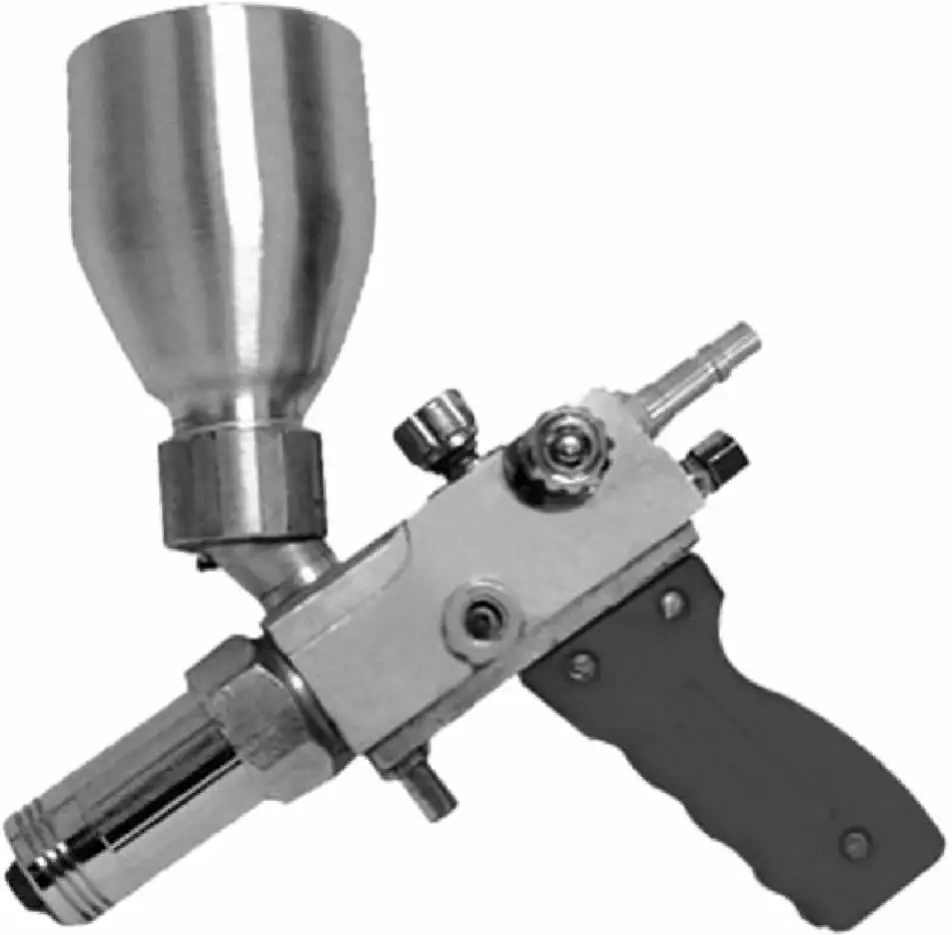
Les méthodes courantes de pulvérisation à la flamme comprennent la pulvérisation de poudre à la flamme oxyacétylénique et la pulvérisation de fil à la flamme oxyacétylénique. La pulvérisation de poudre par flamme oxyacétylénique utilise un équipement simple et peut être réalisée sur site, ce qui convient à la maintenance des équipements.
(1) Avantages de la technologie de pulvérisation à la flamme
- Il peut être pulvérisé sur des substrats métalliques et non métalliques, et la forme et la taille du substrat ne sont généralement pas limitées, mais les petits trous ne peuvent pas encore être pulvérisés.
- Un large éventail de matériaux de revêtement, notamment des métaux, des alliages, des céramiques et des matériaux composites, peuvent être utilisés comme matériaux de revêtement, ce qui permet à la surface d'avoir diverses propriétés telles que la résistance à la corrosion, la résistance à l'usure, la résistance aux hautes températures et l'isolation thermique.
- La structure poreuse du revêtement a des performances de lubrification par stockage d'huile et de réduction du frottement. La macro-dureté du revêtement pulvérisé contenant des phases dures peut atteindre 450HBW, et la couche de soudure pulvérisée peut atteindre 65HRC.
- La projection de flamme a peu d'impact sur le substrat, la température de surface du substrat est de 200~250℃, la température globale est de 70~80℃, donc la déformation du substrat est faible, et la structure du matériau ne change pas.
(2) Inconvénients de la technologie de pulvérisation à la flamme
- La force d'adhérence entre le revêtement pulvérisé et le substrat est relativement faible et ne peut pas résister à des charges alternées et à des charges d'impact.
- Exigences élevées en matière de préparation de la surface du substrat.
- Le processus de pulvérisation à la flamme est affecté par diverses conditions, et il n'existe toujours pas de méthode efficace pour détecter la qualité du revêtement.
3. Pulvérisation d'arc
La projection d'arc est une technique qui utilise un arc électrique brûlant entre deux fils métalliques alimentés en continu pour faire fondre le métal, atomiser le métal fondu avec un flux d'air à grande vitesse et accélérer les particules de métal atomisées pour les pulvériser sur la pièce afin de former un revêtement, comme le montre la figure 17. La projection d'arc est la méthode de projection thermique la plus couramment utilisée dans les applications pratiques d'ingénierie telles que la protection contre la corrosion, la résistance à l'usure et la réparation des structures en acier et des pièces mécaniques.
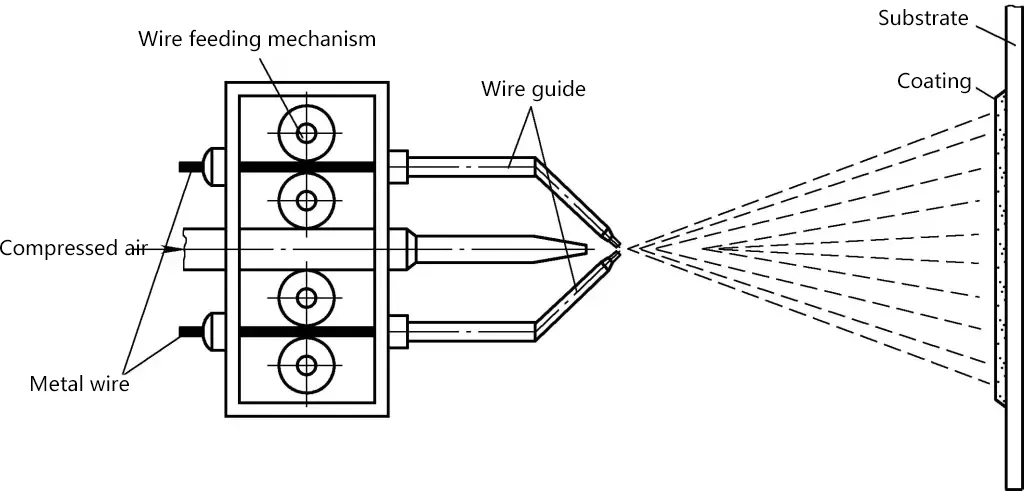
Les caractéristiques de la pulvérisation à l'arc sont les suivantes :
(1) Longue durée de protection contre la corrosion
En fonction des différents environnements de corrosion et des caractéristiques de fonctionnement spécifiques, grâce à une conception raisonnable du revêtement, la durée de résistance à la corrosion du système actuel de revêtement de protection anticorrosion durable par pulvérisation à l'arc a atteint plus de 50 ans, soit 2 à 3 fois celle de la galvanisation à chaud et 2 à 3 fois celle du revêtement FRP.
(2) Grande force d'adhérence avec le substrat métallique
La couche de pulvérisation à l'arc et le substrat sont combinés par encastrement et collage micro-métallurgique, ce qui permet d'obtenir une force d'adhérence plus élevée, trois fois supérieure à celle de la pulvérisation à la flamme et la plus élevée de tous les revêtements anticorrosion.
(3) Productivité élevée
Par rapport à la pulvérisation à la flamme oxyacétylénique, la pulvérisation à l'arc introduit des fils doubles, ce qui augmente de 3 à 4 fois la productivité d'une seule machine.
(4) Bonne qualité du revêtement
La pulvérisation à l'arc électrique chauffe le fil métallique à une température de fusion élevée et uniforme, ce qui permet une pulvérisation dense et une qualité de revêtement stable sans affecter la contrainte thermique de la pièce à usiner ; tandis que la pulvérisation à la flamme oxyacétylénique utilise le chauffage à la flamme, qui a une faible température de fusion du fil métallique, et présente des dangers cachés tels que l'oxydation et la carbonisation, ce qui affecte la qualité du revêtement.
(5) Forte réparabilité
Au cours du traitement, du levage, du transport et de l'installation des structures en acier, le revêtement est susceptible d'être endommagé et rayé. La technologie de pulvérisation d'arc peut être utilisée pour les réparations, garantissant l'intégrité et l'efficacité du système de protection contre la corrosion.
(6) Bonne universalité
La technologie de pulvérisation d'arc permet de sélectionner des matériaux résistants à la corrosion en fonction des différents environnements de corrosion, et le système de traitement est universellement adaptable.
4. Pulvérisation de plasma
La pulvérisation de plasma est une méthode qui utilise un jet de plasma pour chauffer le matériau à pulvériser jusqu'à ce qu'il atteigne un état fondu ou presque fondu et le dépose sur la surface du produit pour former une couche protectrice. L'équipement est illustré à la figure 18 et le principe de fonctionnement à la figure 19.
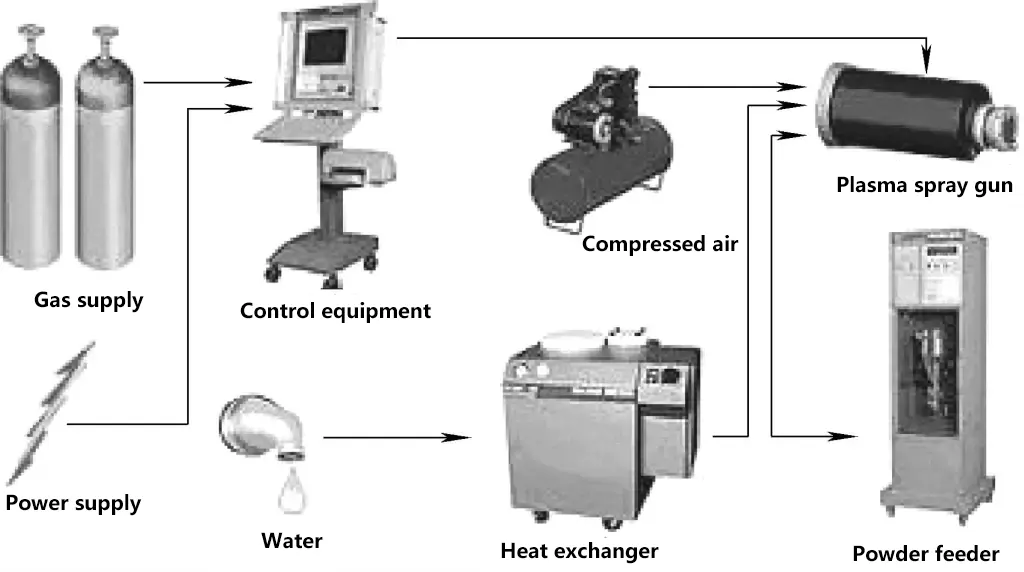
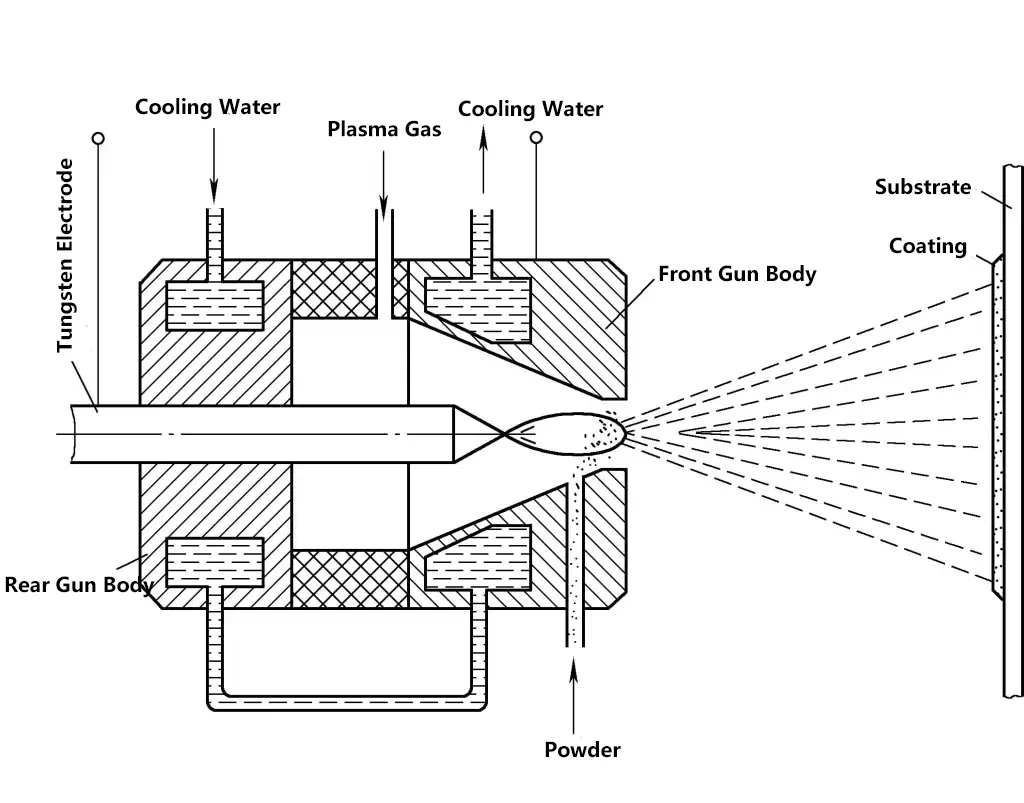
La technologie de pulvérisation par plasma est un nouveau type de méthode de pulvérisation de précision polyvalente qui a été vigoureusement développée après la pulvérisation par flamme. Elle présente les caractéristiques suivantes :
(1) Caractéristiques de la structure du revêtement
Les revêtements projetés au plasma ont une structure dense, avec une faible teneur en oxyde et une faible porosité. La liaison entre le revêtement et le substrat est principalement mécanique, mais une liaison par micro-zones et une liaison physique peuvent également se produire, ce qui se traduit par une plus grande force d'adhérence du revêtement.
(2) Caractéristiques de la technologie des procédés
Les matériaux pulvérisés sont largement applicables, allant des alliages d'aluminium à point de fusion bas à la zircone à point de fusion élevé. Les revêtements ont une grande force d'adhérence, une faible porosité, peu d'inclusions d'oxyde, une grande précision de contrôle de l'équipement et peuvent être utilisés pour préparer des revêtements fins.