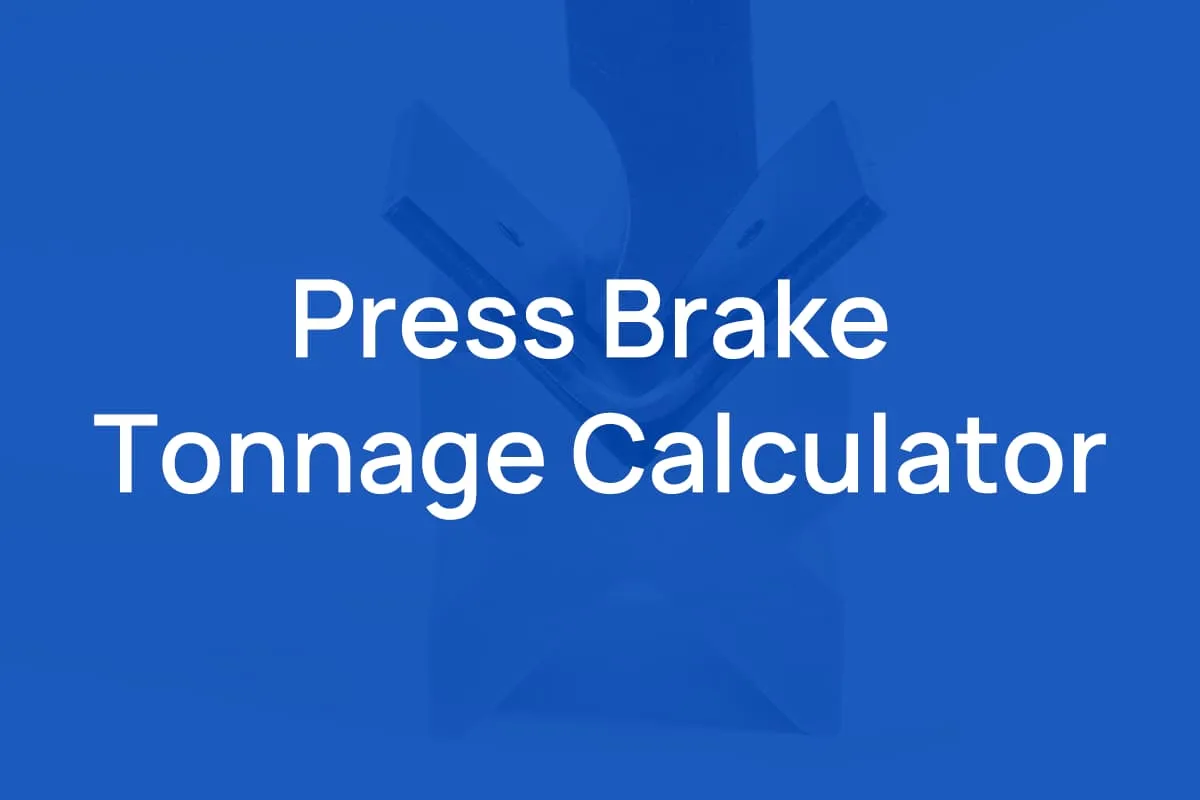
プレスブレーキ機の調整
- ラム上限の調整:
コリジョンブロックIIの位置を調整することにより、上昇するラムを希望の上死点位置で停止させることができます。この最適化により、ラムのストローク距離を短縮し、サイクルタイムを最小化し、全体的な生産性を向上させます。
- ラムのスローモーションの調整:
ラムの下降中、衝突ブロック「I」がストロークスイッチを作動させ、スローモーションを開始します。このスローモーションの継続時間は、可変抵抗器を使用して微調整することができ、曲げプロセスを正確に制御することができます。
- 上下の調整 ダイ・クリアランス:
a.ラムが上死点にある状態で、操作テーブルの右下にある操作ボタンを使用して、初期クリアランスを設定する。このクリアランスは板厚を超えるようにし、必要な曲げ角度に基づいてさらに調整する。微調整は、デジタル表示器に0.1mm単位で表示されるハンドホイールを使用して行うことができます。
b.ワークピース端の角度が一定しない場合は、サポートピンを緩め、コネクティングロッドを動かすことで、左右の回転コネクションを外します。ハンドホイールを使用してメカニカルリミットの一端を調整し、ワークピース端の正確な角度補正を可能にする。
注:調整後は、機械的な故障を防ぐため、スリーブ18が元の位置に戻され、サポートピンがしっかりと締め付けられていることを確認してください。
c.両端の角度は一定だが、中央部の角度がずれている場合は、上型の微調整を行う。上型を下型スロットに近づけ、調整ブロックと上型コンタクトプレートのねじを少しゆるめ、中間部の調整ブロックを軽くたたく。中間の角度が足りないところは、上型が少しはみ出すようにする。サポートピンを締め、ワーク全体の角度が規定の公差を満たすまでテスト曲げを行う。
- 曲げ力の調整:
提供された表または特定の板金用の曲げ力の公式を使用して、必要な曲げ力をキロニュートンで計算する。これを表1を用いて指示圧力値Pに変換する。リリーフバルブのハンドホイールを調整し、計算された曲げ力をわずかに超える力を発生させ、最適な性能を確保する。
- バックゲージの距離の調整:
曲げ加工時の長手方向の位置決めに重要なバックゲージは、前面のボタンボックスを使用してモーター制御で調整します。デジタル表示カウンターは0.1mm単位で調整値を表示し、より正確な位置決めにはハンドホイールを使用します。
- フットペダル操作:
フットペダルスイッチは、ラムの上下運動を人間工学的に制御し、曲げ加工中の作業効率と快適性を高めます。
プレスブレーキ機械のテストと操作
テストの前に、潤滑ラベルに従ってすべての指定潤滑ポイントにカルシウムベースの潤滑グリースを塗布します。油圧システムのオイルタンクに46#作動油を充填する。運転開始後1ヶ月が経過したら油を交換し、その後は使用状況に応じて毎年交換する。最低油温が15℃以上に保たれていることを確認してください。
最初のテスト手順:
- オイルポンプモーターユニットを始動させ、アイドリングさせる。
- ジョグ」モードを使ってマシンの機能をテストする。
- 単一」および「連続」アクションのパフォーマンスを検証する。
- ストロークとバックゲージの制御精度をチェックする。
マシンが正常に機能することを確認してから、操作のセットアップに進んでください:
- 板厚と曲げ長さに基づいて、必要な曲げ力とVダイ開口部寸法を計算または参照する。(Vダイス開口部は通常、板厚の8倍以上とする。)
- 上パンチと下ダイの中心を正確に合わせる。
- 上パンチと下ダイのクリアランスを設定し、調整する。
- バックゲージの位置を正確に決める。
- モードセレクタースイッチで適切なアクションモード("ジョグ"、"シングル"、"連続")を選択する。
- ワークピースを機械のワークテーブルの中央に置き、テストベンドを行う。
- 必要に応じて上型の調整ブロックを調整し、ダイクリアランスを微調整する。
運営上の配慮:
- すべてのシールに漏れがないか監視し、検出された場合は速やかに交換する。
- ワークの精度と機械の完全性を維持するため、曲げ加工は必ず機械の中心線で行ってください。不均等または中心から外れた荷重を避ける。
- やむを得ない片側操作の場合は、荷重を<100kNに制限する。可能な限り、荷重を均等に分散させるために両側曲げを使用する。
- 長さ 600 mm 未満の板を曲げる場合は、長さ 100 mm あたり 100 kN を超えないようにしてください。このような短い板材では、決して全能力(1000 kN)で運転しないでください。
- 試験中、モータの回転方向(反時計回り)が正しいことを確認してください。
マシンのメンテナンス、ケア、トラブルシューティング
本機を操作または整備する人は、本書をよく読み、本機の主な構造、性能、使用方法を理解し、定期的なメンテナンスと手入れを行わなければなりません。日々の使用状況を記録し、後で参照できるようにしてください。
- 機械の操作には専任の担当者が責任を持ち、オペレーターは操作手順を熟知し、それに従って正しく操作し、ワークピースの曲げ力を計算する必要があります。
- オイルポンプが空気を吸い込み、パイプラインの振動や破裂を引き起こしたり、関連する油圧部品がロックしたりこすれたりするのを防ぐため、オイルをきれいで妨げのない状態に保つ。
- 本機は分散給油を採用している。潤滑は、機械の潤滑ポイントの表示図に従って、作業条件に基づいて追加する必要があります(機械の左の壁パネルには、潤滑ラベルが装備されています)。
- ワークピースの曲げ力は、公称力を超えてはならない。
- 片荷重や一点荷重の作業は行わないこと。
- 電気および油圧コンポーネントは、柔軟な動作と正しい位置を確保しなければならない。
- 上型と下型のクリアランスは、曲げ材の板厚によって調整しますが、一般的には板厚より1mm程度大きくします。具体的な値は板厚によって調整してもよいが、クリアランスによる金型の破損を避けるため、板厚より大きくする必要がある。
- 使用者は、定期的にマシンに付属のスペアパーツを入手しなければならない。
- 異常現象や異常音が発生した場合は、直ちに停止し、原因を究明して点検・修理を行ってください。
一般的な油圧システムの故障 プレスブレーキ バルブの故障や切り替えの遅さ、漏れ、ソレノイドバルブの故障など。
(1)バルブの誤作動や切り替えの遅れは、潤滑不足、スプリング機構の損傷、バルブの摺動部品に残留油やゴミが混入していることが原因であることが多い。
この問題に対処するには、まずオイルミストセパレーターの機能を点検し、潤滑油の粘度を確認することから始めます。必要であれば、潤滑油を交換し、バルブの摺動部品を徹底的に清掃し、あるいは新しいスプリングとバルブを取り付ける。振動分析やオイル分析を用いた定期的な予知保全は、このような問題の予防に役立つ。
(2) 長時間の運転は、バルブコアシールリング、バルブステム、バルブシートを含む重要なバルブ部品の摩耗や損傷につながる可能性があります。この劣化は、内部漏れ、バルブ反応の鈍化、不適切なスイッチングを引き起こす可能性があります。
そのような場合、影響を受ける部品(シーリングリング、バルブ軸、バルブシート)を交換するか、大きな損傷がある場合は、バルブの全交換を選択する。状態に応じたメンテナンスプログラムを実施することで、システムの故障につながる前に、これらの問題を特定することができる。
(3) ソレノイドバルブの不具合は、吸気ポートや排気ポートの詰まり(オイルスラッジやゴミの堆積による)、シール不良、可動鉄芯の固着、電気回路の異常など、いくつかの要因で発生する可能性があります。
機械的な問題については、ソレノイドバルブの構成部品を徹底的に清掃し、特に可動鉄芯とその周辺に注意してください。制御回路またはソレノイドコイルの問題として典型的に現れる潜在的な回路の故障については、系統的なトラブルシューティングのアプローチに従ってください:
まず、定格圧力下で切替バルブのノブを手動で数回操作し、適切な動作を確認します。バルブが正しく切り替わったら、回路診断に集中します。マルチメータを使用してソレノイドコイルの電圧を測定し、それが定格仕様に適合していることを確認します。電圧が不十分な場合は、制御システム内の電源および関連するストロークスイッチ回路を調査してください。
スイッチングバルブが定格電圧下で正しく動作しない場合は、ソレノイドコイルの接続部に緩みがないか、接触不良がないか点検してください。プラグを外し、コイルの抵抗値を測定してください。メーカー指定の範囲外の抵抗値は、交換が必要な損傷したコイルを示しています。
システムの信頼性を高めるには、電気的な問題を早期に発見するためのサーマルイメージングや、内部リークを特定するための超音波検査など、高度な診断ツールの導入を検討してください。さらに、コンピュータ化された保守管理システム(CMMS)を統合することで、部品のライフサイクルを追跡し、予防保守作業のスケジュールを効果的に立てることができます。