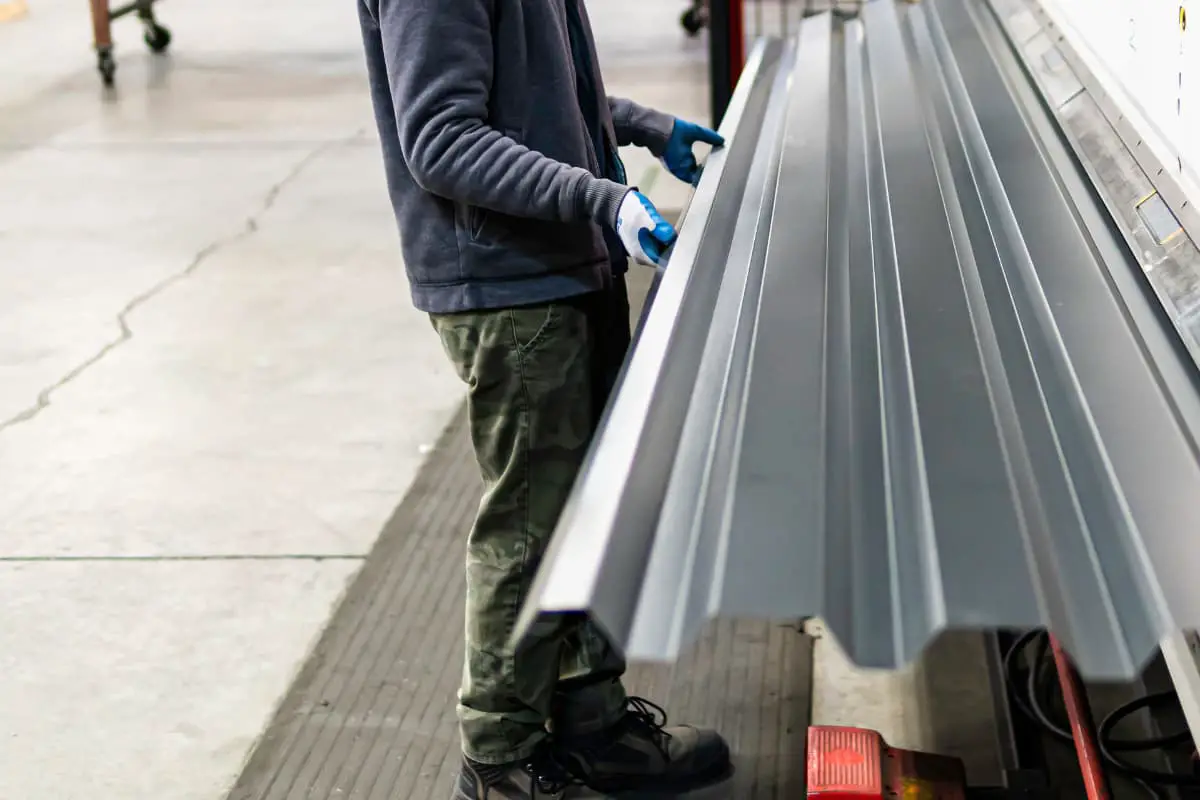
板金部品は、薄い金属板をプレス、曲げ、絞りなどの技術で加工して形成される構造部品である。キャビネット、ケーシング、プラグイン、コンソール、パネル、ブラケットなどの製造によく使用され、電子・電気モジュールの設置、支持、保護のためのキャリアとして機能します。
最適化された構造設計により、軽量でコスト効率に優れながら、高い強度と剛性を実現することができます。板金部品のコンパクトな構造、美しい外観、堅牢な信頼性は、金型加工に適しています。生産性の向上、生産サイクルの短縮、生産コストの削減といった利点があるため、その用途は驚くほど広がっています。
1.板金加工の概要
1.1 板金加工
の多くの手順がある。 板金加工 は、材料の塑性変形を伴う。板金部品の種類によって、使用する金型やブランクが異なり、変形方法も様々である。板金加工では、材料の変形特性に応じて、分離手順と変形手順に分けられる。
板金分離手順とは、手順後に材料の変形部分の応力が強度限界に達し、材料が変形して分離する手順を指す。これには、パンチング、ブランキングなどの作業が含まれる、 剪断ノッチング、トリミングなど
板金の変形加工とは、加工後に材料の変形部分の応力が降伏強度を超え(ただし強度限界以下)、塑性変形を生じ、それによって材料の元の形状や寸法が変化する加工を指す。これには、絞り加工、フランジ加工、バルジング加工、曲げ加工、ねじり加工、ウェーブフォーミング加工などが含まれる。
これら2つの異なる手順は、パンチとブランク、ブランクとドロー、ドローとトリムなどの複雑な手順を完了するために、しばしば組み合わされる。さらに、製品の組み立て作業では、プレス加工など、部品やコンポーネントの組み立てにスタンピング方法が使用されることが多い。 フィッティングリベッティング、パンチ・リベッティング、トルクス・リベッティングなど。
1.2 板金加工における一般的な用語
(1) シャーリング
材料の一部を鋏や金型によって周囲に沿って切断し、元の材料から加工品を完全に切り離す工程。
(2) ブランキング
一般的なプレス機などの金型を使って、被加工物の全周を切断し、元の材料から完全に切り離す工程。切断された部分がワークとなる。
(3) パンチング
一般的なプレス機などの金型を使って全周を切断し、スラグを元の素材から完全に分離する工程。取り除かれた部分がスラグ。
(4) レベリング
平らでない被加工物を取り出し、滑らかなまたはテクスチャ加工された上型と下型の間に置き、圧力を加えて平らな板にする、または他の装置や工具を使用して被加工物を平らにする工程。
(5) スロット加工
シートを完全に切り離さずに、一部をカットする(外周の一部を切り落とす)工程。
(6) セクション
曲げられたり引き抜かれたりした部品を2つ以上に切断すること。
(7) トリミング
部品から余分なエッジや不規則なエッジを切り取る工程。
(8) 仕上げ
平らな部品の縁や穴を正確な寸法と滑らかな断面に仕上げる工程。
(9) 型抜き
金型を使って非金属シート材の全周を切断する工程。
(10)曲げ
平らな材料や形材を一定の角度や形状に曲げる工程。板材や形材をプレス機で曲げ型を使って曲げる工程は、プレスブレーキングと呼ばれる。 折り畳み機折りたたみとも呼ばれる。この方法は、キャビネットやエンクロージャーなどの製造によく使われる。
(11) フランジング
ワークの直線エッジをオス型とメス型で挟み、圧力をかけながらオス型またはメス型の内側で直線エッジを転がし、曲げエッジを形成する工程。
(12)ツイスト
平らなシートの一部を他の部分に対してねじらせ、空間的な曲面形状を形成するプロセス。
(13) 成形
一般的な金型を用いてワークを変形させるプロセス。 プレスまたは油圧機械一般にフォーミングプロセスと呼ばれる。
(14) ディープ・ドローイング
ストレッチング」または「ドローイング」とも呼ばれ、平らな素材を中空部品にしたり、中空部品をより深くする(シートの平均厚さは変形の前後で変わらない)プロセスを指す。
(15) 薄肉深絞り加工
直径や壁の摩擦を減らすことによって、固体または中空の部品の寸法を変更するプロセス。
(16) ビーディング
コルゲーティング(corrugating)」とも呼ばれ、シート材を局所的に薄くすることで凹凸形状を形成する工程。
(17) フレアリング
パンチング・ホール」とも呼ばれ、一般的なプレス機などを使って、既存の穴の有無にかかわらず、シート材や中空部品に、エッジを曲げた大径の穴を形成する工程である。
(18) ねじ切り
ワークピースに内ねじを加工する工程。
(19)シェーピング
曲げ加工や絞り加工の後、被加工物に最終的な形状や正確な寸法を与える工程を指す。
(20) 拡大する
中空ワークの内部を加圧し、断面寸法を拡大するプロセスを指す。
(21) 削減
中空ワークに外圧を加え、その断面寸法を減少させるプロセスを指す。
(22) センター・パンチング
被加工物の表面に(貫通させずに)センターマークを付け、その後の穴あけ加工を行う工程。
(23) エンボス加工
金型を使って被加工物の材料を変位させ、板金の厚みを変えることによって文字や記号などの印象を作り出す工程。
(24) コールド・エクストルージョン
インパクト・エクストルージョン」とも呼ばれ、中実または中空のブランクをダイに入れ、パンチで押し出す工程を指す。
(25) エンボス加工
プレスの金型を使って、平らな被加工物に局所的に浅く盛り上がった形状を作る工程。
(26) コーナーカット
プレス機の金型を使ってワークの角を切り落とす工程。
(27) パンチング通気孔
従来型またはCNCプレスの金型を使って、平らな被加工物に網目状の穴を開ける工程。
(28) パンチングとブランキング
1つの複合金型内で打ち抜きと型抜きの両方の作業を完了させる工程。
(29) ブランキングと曲げ加工
ブランキングと曲げ加工の両方を1つの複合金型内で完了させる工程。
(30) ブランキングとドローイング
ブランキングとドローイングの両方の作業を1つの複合ダイス内で完了させる工程。
(31) 絞りと成形とフランジング
1つの複合ダイス内で絞り、成形、フランジ加工を完了させる工程。
(32) 穴の拡大
ドリル・ビットやフライス・カッターを使って、被加工物の小さな穴を拡大すること。
(33) カウンターシンク
円錐形の穴(深さは板の厚さより小さい)を工作物の表面に加工し、皿ネジ、リベットナット、その他のコネクターに対応させる工程。
(34) リベッティング
リベットを使用して、2つ以上の工作物を対面で接続する工程。皿リベットを使用する場合は、ワークピースを最初に皿加工する必要がある。
(35) プレス・リベット
リベット・ナット、リベット・スクリュー、またはプレス・リベットを、プレス機または油圧機を用いて被加工物にしっかりと押し付ける工程。
(36) スウェル・リベット
ワークピースをまず皿穴加工し、次にリベットナットをワークピースに確実に圧入する工程。
(37) リベットナット引き
リベット・ナットやリベット・スタッドのようなコネクターを、リベット・ガンを使って被加工物に確実に取り付ける工程で、リベット打ちに似ている。
(38) プルリベット
リベット・ガンとプル・リベット(ブラインド・リベット)を使って、2つ以上の被加工物を強固に結合する工程。
(39) 平坦化
ある形状の加工物を平らな面に滑らかに移行させる工程。
(40) 掘削
ドリルプレスやフライス盤で、ドリルビットを使って被加工物に穴をあける工程。
(41) バリ取り
グラインダー、ヤスリ、その他の工具を使用して、せん断、パンチング、ブランキングなどで生じたバリをワークピースから除去し、加工部分を滑らかで平坦にする工程。
(42) 面取り
金型、カッター、グラインダーなどを使って、工作物の鋭利な角を加工する工程。
(43) リタッピング
塗装や粉体塗装などの表面処理後に、ねじ切り前のワークピースに再びねじ切りを行う工程。
(44) 保護フィルムの貼り付け
保護フィルムを用いて加工物の表面を保護する工程。
(45) 保護フィルムの取り外し
ワークの表面から保護膜を取り除く工程。
(46) 熱収縮
加熱装置(ヒートガン、オーブン)を使って、被加工物の周囲にプラスチックを収縮させる工程。
(47) ラベリング
ワークピースの指定された位置にラベルを貼り付ける作業を指す。
(48) 線引き
これは、伸線機とサンドベルトで被加工物の表面を処理する工程を指す。
(49) 研磨
研磨装置を使ってワークの表面に光沢を出す工程を指す。
(50) 熱処理
これは、金属材料を適切な方法で加熱、断熱、冷却し、必要な構造と特性を実現するプロセスを指す。
(51) 水素アーク溶接
水素アーク溶接機によって、ワークの端部または継ぎ目でワーク間の接続部を溶接するプロセスを指す。特定の溶接要件に基づいて、断続溶接と全溶接にさらに分けられる。
(52) CO2ガスシールド溶接
CO2ガスシールドウェルディングマシンにより、ワークの端部や継ぎ目を溶接する工程を指す。一般的に次のような用途に使用される。 厚鋼板の溶接 2mm以上である。さらに、特定の溶接要件に基づいて、断続溶接と完全溶接に分けることができます。
(53) スポット溶接
スポット溶接機を使ってワークピースを対面溶接するプロセスを指す。スポット溶接では、溶接強度を高めるため、ワークの接触面の一方に溶接点を形成するのが一般的である。溶接点の大きさはφ1.5~φ2.5mm、高さは0.3mm程度である。
(54) スタッド溶接
スタッド溶接ガンを使用して、スタッドボルトをワークピースの表面にしっかりと溶接するプロセスを指す。
(55) シーム溶接補修
これは主に、グラインダー、ヤスリ、その他の工具を使用して、被加工物の溶接痕を平滑にし、水平にする工程を指す。
(56) 前処理
板金加工終了後、塗装や粉末溶射の前に、電解液で被加工物の表面皮膜(リン化物皮膜など)を脱脂・脱脂・強化し、洗浄する工程を指す。
(57) パテ埋め
これは、原子灰を使用してワークピース表面の欠陥(溶接ギャップやピットなど)を補正するプロセスを指します。
(58) パテ埋めと研磨
これは主に、パテ埋め後にサーフェスグラインダーやサンドクロスを使ってワークの表面を研磨する工程を指す。
(59) 絵画
専用のスプレーガンを使って、ワークの表面に塗料を均一に吹き付ける作業を指す。
(60) 粉体噴霧
粉体塗装とも呼ばれる粉末溶射は、プラスチック粉末を原料として、ここ数十年で急速に発展した新しいタイプの塗装プロセスである。粉末溶射とは、スプレーガンを使ってワークの表面に粉末を均一に吹き付けるプロセスを指します。
(61) スクリーン印刷
スクリーン印刷とは、シルクスクリーン印刷の略で、スキージを使ってインクやその他の印刷材料をスクリーンの露出部分から転写し、被印刷物の表面に刷り込んで文字や模様を形成する工程を指す。スクリーン印刷はバッチ印刷に適している。
(62) 電気めっき
保護や装飾のために、ワークピースの表面に金属の層を塗布するプロセスを指す。
(63) ブラックニング
保護や装飾のために、ワークピースの表面に酸化皮膜を形成するプロセスを指す。
(64) サンド・ブラスト
サンドブラスト機を使用してワークピースの表面を処理するプロセスを指す。
(65) 組み立て
これは、2つ以上のワークを組み立てる工程を指す。
(66) パッケージング
紙などで被加工物を保護する工程を指す。
(67) その他
平坦化、オフセット(Z型)、エッジ・ターニング、スレッディング、ホール・リベットなど。