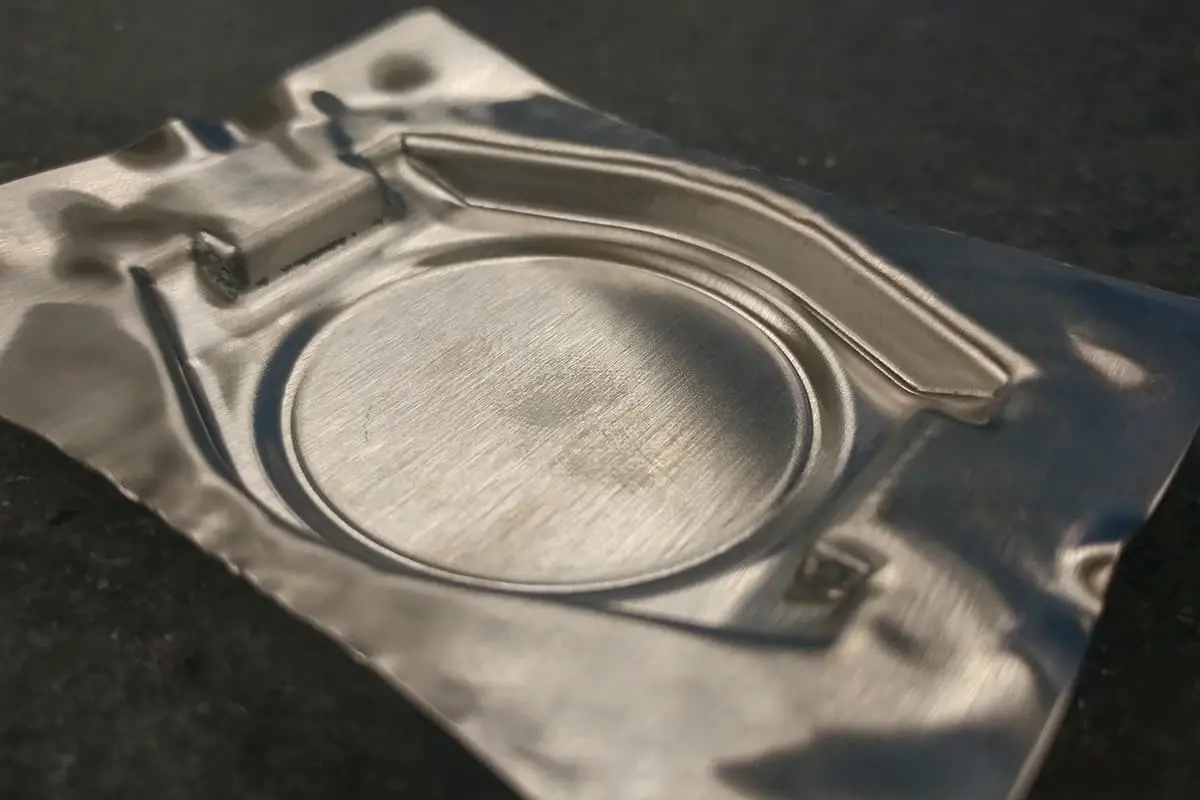
В процессе производства гибка листового металла часто сталкивается с различными проблемами качества, влияющими на повышение эффективности производства и стабильность качества продукции.
В данной статье рассматриваются распространенные проблемы качества гибки и резки, встречающиеся в производственной практике, анализируются причины этих проблем и предлагаются решения, позволяющие получить опыт и рекомендации для решения аналогичных проблем, которые могут возникнуть в последующей производственной практике.
Введение
Гибка листового металла предполагает использование Гибочный станок с ЧПУ оснащенные стандартными (или специализированными) штампами для гибки металлических листов в различные требуемые геометрические формы поперечного сечения.
Рациональность процесса гибки напрямую влияет на конечные размеры и внешний вид изделия. Выбор правильных гибочных штампов имеет решающее значение для конечной формы изделия.
В реальном производстве из-за неопределенности размеров изделий и разнообразия типов продукции мы часто сталкиваемся с такими проблемами, как нарушение размеров и несовпадение углов штампов при холодной обработке деталей, что создает значительные трудности.
На качество гибки влияют такие факторы, как размер, форма, материал, штампы, оборудование и вспомогательные средства, что приводит к возникновению различных проблем с качеством, влияющих на эффективность производства и стабильность качества продукции. Поэтому решение и предотвращение этих проблем качества особенно важно.
В данной статье обобщены и описаны распространенные проблемы качества гибки листового металла, встречающиеся в производственной практике, проанализированы причины их возникновения на основе производственного опыта и предложены пути их решения.
Общие проблемы с качеством гибки
2.1 Растрескивание при изгибе
Трещины при изгибе - это явление, при котором на краях материалов после резки часто появляются заусенцы или мелкие трещины, ножницыили штамповки, что приводит к концентрации напряжений и образованию трещин при изгибе. Примером могут служить трещины на углах U-образного усилительного паза (2A90100185G00) аксессуара локомотива HXD1C после сгибания, как показано на рис. 1.
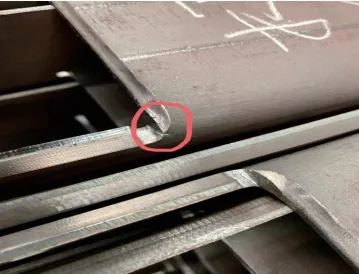
К основным причинам образования трещин при изгибе относятся:
- Не удаленные заусенцы на кромках деталей.
- Направление изгиба параллельно направлению прокатки листа.
- Чрезмерно маленькие радиус изгиба листового материала.
В процессе производства явление растрескивания при изгибе должно решаться в зависимости от конкретных обстоятельств. Для решения проблемы растрескивания при изгибе, показанной на рис. 1, можно использовать такие решения, как добавление технологических отверстий или канавок, как показано на рис. 2.
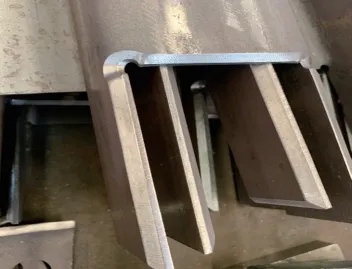
2.2 Помехи при изгибе
Помехи при гибке возникают в основном в изделиях, подвергающихся вторичной гибке или гибке более высокого порядка, когда кромка гиба сталкивается со штампом или оборудованием, препятствуя нормальному формированию. Помехи при гибке в основном зависят от формы, размера детали и штампа, а также от конструктивной структуры гнутой детали, выбранной последовательности гибки и выбранных гибочных штампов.
Решения включают в себя:
- Изготовление или замена штампов (например, штампов для гибки ножей).
- Модификация гибочных штампов (например, обработка отдельных участков).
- Настройка последовательности гибки (например, метод обратной деформации).
- Изменение размеров сгибаемой детали.
Например, монтажный кронштейн для кабельного лотка крепления шасси шанхайской линии 18 (ADC1027252G030) представляет собой U-образный стальной швеллер со средней шириной 100 мм, высотой борта 80 мм и радиусом изгиба 15 мм. Использование существующих цеховых штампов для моделирования изгиба привело к возникновению помех при изгибе.
Для устранения этой помехи часть гибочного верхнего штампа была механически изменена (как показано на рисунке 3). В средней линии существующего верхнего штампа с прямым лезвием R15 мм (L=800 мм) был вырезан паз размером 140 мм×48 мм (как показано на рис. 4).
Положение выемки было определено на основе смоделированного места возникновения помех при изгибе, без ущерба для ее первоначальной функции. Эта модификация гибочного штампа позволила успешно решить проблему помех при изгибе.
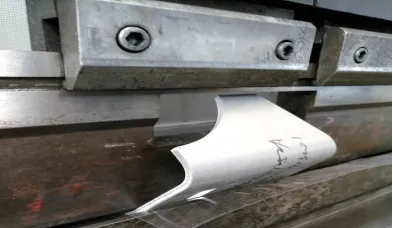

Рисунок 4: Помехи при изгибе, определение зоны обработки
2.3 Индентирование при изгибе
Вмятина при гибке возникает, когда металлический лист во время гибки постепенно прижимается к внутренней поверхности V-образного паза штампа, создавая трение, которое оставляет заметные следы на поверхности материала.
Для деталей с высокими требованиями к поверхности традиционная гибка не может удовлетворить требования к качеству, а вмятина от гибки (как показано на рис. 5) не удовлетворяет требованиям последующего процесса.

Вмятина при гибке в основном зависит от твердости листового материала и конструкции нижнего штампа. Чем тверже материал, тем выше его сопротивление пластической деформации, что затрудняет деформацию материала и облегчает образование вмятин.
Вероятность появления вмятин при изгибе в распространенных материалах располагается в следующем порядке: Алюминий > Углеродистая сталь > Нержавеющая сталь. Чем шире отверстие нижнего штампа, тем шире и мельче вмятина. Чем больше размер R буртика штампа, тем меньше глубина вмятины.
Для решения проблемы вдавливания при изгибе, помимо повышения твердости материала и изменения конструкции нижнего штампа, можно использовать такие методы, как применение резиновых прокладок против вдавливания и нижних штампов с шарикоподшипниками.
Резиновые прокладки против вмятин уменьшают образование вмятин за счет физической изоляции, как показано на рисунке 6. Нижние штампы с шарикоподшипниками преобразуют трение сжатия, необходимое для традиционной штамповки, в трение качения, уменьшая трение и сводя к минимуму повреждение изделия, как показано на рисунке 7.
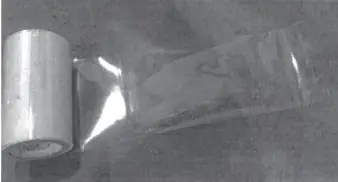

2.4 Пружинистость при изгибе
В процессе гибки материалы подвергаются как пластической, так и упругой деформации. После извлечения заготовки из гибочного штампа происходит ее упругое восстановление, в результате чего ее форма и размеры отличаются от тех, что были при загрузке. Это явление известно как пружинящий изгиб и является одной из основных причин недостаточного угла изгиба.
К факторам, влияющим на отскок, относятся механические свойства листового материала и условия деформации при изгибе. Величина отскока прямо пропорциональна пределу текучести листа и обратно пропорциональна его модулю упругости.
Чем меньше относительный радиус изгиба (отношение радиуса изгиба к толщине листа, R/t), тем меньше пружинящий изгиб. Форма гнутой детали также влияет на величину пружинящей отдачи; обычно U-образные детали имеют меньшую пружинящую отдачу, чем V-образные.
Основным методом преодоления пружинения при гибке является компенсация угла. Обычно это достигается путем создания гибочного штампа с наклоном, равным углу пружинения, что позволяет эффективно сбалансировать эффект пружинения. Как показано на рис. 8, использование гибочного штампа с углом наклона 80° позволяет успешно согнуть заготовку на угол 90°.
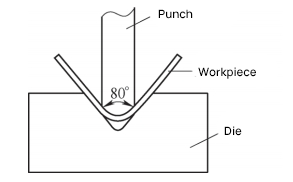
Учитывая множество факторов, влияющих на пружинение при гибке, точно рассчитать его величину крайне сложно. Путем пробных корректировок и накопления опыта освоение модели пружинящего отката и применение соответствующей компенсации, а также меры по изменению конструкции штампа являются эффективными методами обеспечения качества продукции.
2.5 Скольжение при изгибе
Проскальзывание при гибке - это явление, при котором заготовка, подлежащая гибке, не имеет полных и эффективных точек опоры на нижней канавке штампа, в результате чего заготовка легко соскальзывает и не может быть правильно позиционирована для гибки.
Основными причинами проскальзывания при изгибе являются следующие:
1) Ширина нижней гибочной матрицы слишком велика, что приводит к проскальзыванию, когда размер гиба составляет менее половины ширины нижней матрицы.
2) Форма и размер заготовки влияют на позиционирование, что приводит к проскальзыванию гибки, если у заготовки слишком короткая сторона для позиционирования штампа или отсутствует эффективная позиционирующая кромка.
Существует два основных метода решения проблемы проскальзывания при изгибе:
1) Метод 1. Выберите подходящий нижний гибочный штамп, обычно ширина штампа в 4-6 раз превышает толщину листа для гибки.
2) Метод 2. Устранение проблем соскальзывания при гибке, вызванных плохим позиционированием во время гибки, путем добавления шаблонов или технологических кромок.
Как правило, гибка осуществляется вдоль одной прямой кромки заготовки, что требует контакта с двумя торцевыми поверхностями гибочного штампа для позиционирования. Однако в реальном производстве бывают случаи, когда кромка изделия для позиционирования штампа слишком коротка или вообще отсутствует, что делает позиционирование гибки невозможным.
Решения включают:
a) При толщине листа t ≤ 6 мм добавьте технологические кромки для позиционирования. Технологическая кромка должна выходить заподлицо с торцевой кромкой детали, а стык может быть вырезано лазером прорезь для легкой шлифовки и удаления после сгибания.
b) При толщине листа t > 6 мм для позиционирования используйте вырезанные шаблоны. Толщина шаблона может быть равна или немного меньше толщины заготовки. Как показано на рис. 9, оба метода позиционирования позволяют решить проблему проскальзывания при гибке.
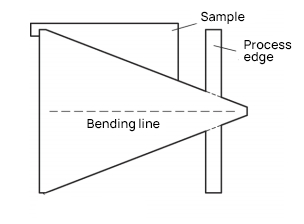
2.6 Изгиб по большому радиусу
В процессе производства часто встречаются заготовки, требующие большого радиуса изгиба, для которых в мастерской нет подходящих штампов большого радиуса. В таких случаях изготовление интегрального формовочного штампа или штампа большого радиуса может занять много времени и стоить дорого. Вместо этого более экономичным и универсальным является использование процесса многорадиусной формовки с малым радиусом изгиба.
Например, компонент проекта Superbus 2.0, вертикальная пластина 3 (ADC1043361G030), требует радиуса изгиба 125 мм и угла изгиба 90°, как показано на рис. 10. При отсутствии в мастерской соответствующего гибочного штампа можно применить процесс многократной гибки.
Сначала позиция R125 мм моделируется в 3D-программном обеспечении для гибки макета, затем программа автоматически разворачивает плоский двухмерный чертеж. Введя в программу радиус изгиба 45 мм и сравнив несколько наборов данных, было подтверждено, что формовка путем 8-кратного изгиба может обеспечить дугообразное сечение.
Затем генерируются данные по изгибу для каждого разреза (угол изгиба, длина линии сгиба), как показано на рис. 11. Наконец, данные о гибке используются для пробной гибки на месте, как показано на рис. 12.

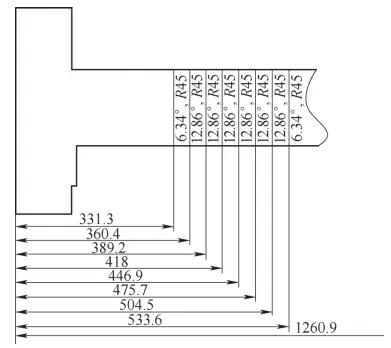

2.7 Выпуклость изгиба
Выпуклость при изгибе возникает, когда листовой металл после сгибания имеет выступы по обе стороны от изгиба из-за сжатия материала, что приводит к увеличению ширины по сравнению с первоначальным размером. Размер выпуклости при изгибе обычно зависит от толщины детали и радиуса изгиба; чем толще материал и меньше радиус, тем более выражена выпуклость.
Для предотвращения этой проблемы на стадии вытяжки гибочного расширения с обеих сторон линии гибки могут быть сделаны технологические надрезы, как показано на рис. 13. Эти надрезы обычно имеют форму дуги, диаметр которой обычно превышает толщину заготовки более чем в 1,5 раза, что позволяет эффективно противодействовать выпуклости при изгибе. Для заготовок, уже получивших выпуклость при изгибе, обычно применяется ручное шлифование для исправления.

Заключение
Следует отметить, что перечисленные выше общие проблемы качества гибки и резки не учитывают влияние человеческого фактора или оборудования (например, ошибки в Развернуть размеры, неправильный выбор параметров гибки и старение оборудования).
В производственной практике очень важно выбрать подходящие параметры процесса гибки в зависимости от производительности оборудования, размера изделия и характеристик материала, а также строго соблюдать нормы эксплуатации.
Необходимо не только всесторонне учитывать такие факторы, как ход проекта, стоимость и качество, и применять подходящие методы для решения проблем качества гибки, но и заранее выявлять и предотвращать потенциальные проблемы гибки путем накопления опыта и предвидения при анализе процесса.
В этой статье перечислены несколько распространенных проблем, связанных с качеством гибки, и их решения, в надежде предоставить коллегам по отрасли некоторые справочные материалы и рекомендации.