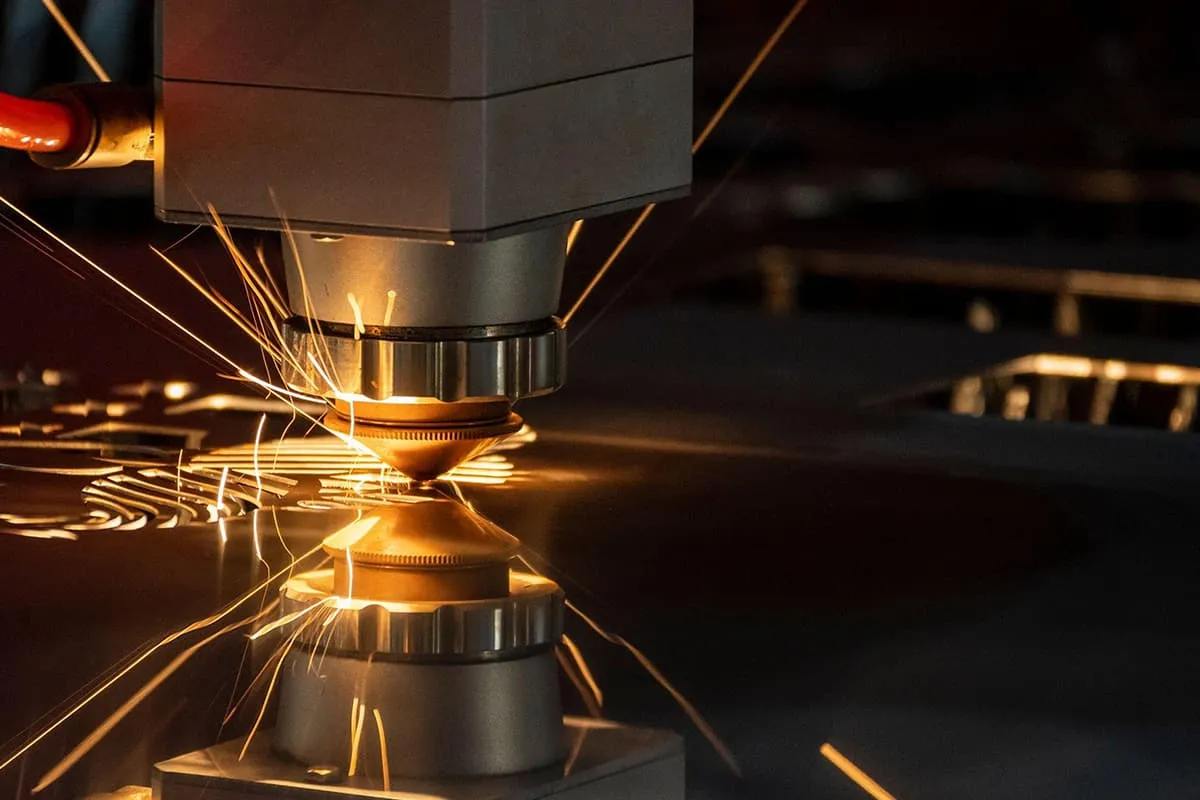
مقدمة في القطع بالليزر CO2
A. أساسيات تقنية ليزر ثاني أكسيد الكربون CO2
تشكل تقنية ليزر ثاني أكسيد الكربون CO2 العمود الفقري للعديد من أنظمة القطع والنقش الحديثة. ويعمل ليزر ثاني أكسيد الكربون في جوهره عن طريق التحفيز الكهربائي لخليط غازي يتكون أساساً من ثاني أكسيد الكربون والنيتروجين والهيليوم. ويؤدي هذا التحفيز إلى انبعاث ضوء الأشعة تحت الحمراء من جزيئات ثاني أكسيد الكربون بطول موجي يبلغ 10.6 ميكرومتر.
تشمل المكونات الرئيسية لنظام ليزر ثاني أكسيد الكربون ما يلي:
- أنبوب الغاز: يحتوي على خليط غاز ثاني أكسيد الكربون
- مزود الطاقة: يوفر الطاقة الكهربائية لإثارة الغاز
- المرايا: توجيه شعاع الليزر
- عدسة تركيز: تركز الشعاع للقطع
إن الطول الموجي الذي يبلغ 10.6 ميكرومتر فعال بشكل خاص لقطع ونقش مجموعة واسعة من المواد، وخاصة المواد العضوية والعديد من المواد البلاستيكية. يتم امتصاص هذا الطول الموجي بسهولة بواسطة هذه المواد، مما يسمح بالقطع الفعال والحد الأدنى من المناطق المتأثرة بالحرارة.
B. مزايا القطع بالليزر CO2 بالليزر
ثاني أكسيد الكربون القطع بالليزر العديد من المزايا مقارنة بطرق القطع التقليدية، مما يجعلها الخيار المفضل في العديد من الصناعات:
- دقة عالية: يمكن أن يحقق ليزر ثاني أكسيد الكربون دقة قطع تصل إلى ± 0.1 مم، مما يتيح إنشاء تصميمات معقدة وتفاوتات دقيقة.
- تعدد الاستخدامات: يمكن لأجهزة الليزر هذه أن تقطع وتنقش وتضع علامات على مجموعة كبيرة من المواد، بما في ذلك المعادن والخشب والأكريليك والنسيج وحتى المنتجات الغذائية.
- السرعة: بفضل سرعات القطع التي تصل إلى 20 مترًا في الدقيقة للمواد الرقيقة، يتفوق ليزر ثاني أكسيد الكربون على العديد من طرق القطع التقليدية.
- عملية عدم التلامس: لا يلامس شعاع الليزر المادة فعليًا، مما يقلل من تآكل أدوات القطع ويقلل من الحاجة إلى الاستبدال المتكرر.
- الحد الأدنى من نفايات المواد: يؤدي عرض الشق الضيق لليزر ثاني أكسيد الكربون (صغير يصل إلى 0.1 مم) إلى تقليل هدر المواد مقارنةً بطرق القطع الميكانيكية.
- ملائمة للأتمتة: يمكن دمج أنظمة ليزر ثاني أكسيد الكربون بسهولة مع وحدات التحكم الرقمي باستخدام الحاسوب والأنظمة الروبوتية، مما يتيح عمليات الإنتاج الآلي.
وقد أدت هذه المزايا إلى انتشار استخدام القطع بالليزر باستخدام ثاني أكسيد الكربون على نطاق واسع في مختلف الصناعات، مما أحدث ثورة في عمليات التصنيع وأتاح إمكانيات تصميم جديدة.
C. التطبيقات في مختلف الصناعات
إن تعدد استخدامات ودقة القطع بليزر ثاني أكسيد الكربون جعلته لا غنى عنه في العديد من الصناعات:
- اللحام والقطع الصناعي: في قطاعي السيارات والفضاء، تُستخدم ليزر ثاني أكسيد الكربون في قطع ولحام المكونات المعدنية بدقة عالية. على سبيل المثال، يتم استخدامها في قطع ألواح لوحة العدادات المعقدة ولحام السبائك المتخصصة في بناء الطائرات.
- الإجراءات الطبية: وجدت ليزر ثاني أكسيد الكربون تطبيقات في مختلف المجالات الطبية. ففي طب الأمراض الجلدية، تُستخدم في إعادة تسطيح الجلد وإزالة الآفات. في الجراحة، يمكن لليزر ثاني أكسيد الكربون عمل شقوق دقيقة بأقل قدر من النزيف، مما يساعد في إجراءات مثل إزالة الأورام.
- التصنيع المضاف: في مجال الطباعة ثلاثية الأبعاد، يلعب ليزر ثاني أكسيد الكربون دورًا حاسمًا في عمليات التلبيد الانتقائي بالليزر (SLS). وهي تُستخدم لدمج المواد المسحوقة طبقة تلو الأخرى، مما يؤدي إلى إنشاء كائنات ثلاثية الأبعاد معقدة للنماذج الأولية والإنتاج على نطاق صغير.
- النقش الفني: يستخدم الفنانون والحرفيون ليزر ثاني أكسيد الكربون لإنشاء تصميمات معقدة على مواد مثل الخشب والزجاج والجلد. وقد أحدثت هذه التقنية ثورة في خدمات التخصيص، مما يسمح بالنقش المخصص السريع والمفصّل على مجموعة متنوعة من المنتجات.
- صناعة المنسوجات: يتم استخدام ليزر ثاني أكسيد الكربون بشكل متزايد لقطع الأقمشة بدقة، خاصة في إنتاج الملابس الراقية والمنسوجات التقنية. ويمكنها إنشاء حواف نظيفة ومحكمة الغلق تمنع الاهتراء، وهي ميزة كبيرة مقارنة بطرق القص التقليدية.
- صناعة الأغذية: من المثير للدهشة أن ليزر ثاني أكسيد الكربون وجد تطبيقات في معالجة الأغذية. فهي تُستخدم في التقطيع الدقيق للأطعمة المجمدة وتقسيمها إلى أجزاء، وكذلك في إنشاء أنماط زخرفية على المخبوزات.
مخطط تفصيلي لسُمك القطع بالليزر CO2 والسرعة والطاقة
يُعد مخطط سُمك وسرعة ليزر ثاني أكسيد الكربون CO2 أداة مهمة لتصنيع المعادن الدقيقة، حيث يوفر للمشغلين معلمات محددة لتحسين أداء القطع عبر مختلف المواد والسماكات. وهو يربط بين إعدادات طاقة الليزر وسرعة القطع وسُمك المواد، مما يتيح تحسين العملية بكفاءة وجودة إنتاج متسقة.
إرشادات تفسير الرسم البياني
عند تفسير الرسم البياني للسمك والسرعة، من المهم أن تفهم أن هذه المخططات تعمل كنقطة مرجعية أساسية:
طاقة الليزر (القوة الكهربائية): تحدد القوة الكهربائية ناتج طاقة الليزر وقدرته على القطع. تتيح القوة الكهربائية الأعلى إمكانية القطع من خلال مواد أكثر سمكًا أو زيادة سرعات القطع. ومع ذلك، من الضروري النظر في جودة الشعاع (M²) وكثافة الطاقة (W / سم²) لفهم شامل لأداء القطع.
سُمك المادة: تقاس هذه المعلمة عادةً بالملليمتر (مم)، وتشير هذه المعلمة إلى السُمك الأقصى الذي يمكن قطعه بفعالية في إعدادات الطاقة المختلفة. من المهم ملاحظة أن العلاقة بين الطاقة والسُمك ليست دائمًا علاقة خطية، خاصة بالنسبة للمواد العاكسة مثل الألومنيوم أو النحاس.
معلمات القطع الخاصة بالمواد
- ملاحظات (طاقة الليزر 95% من الخرج المقدر)
1. مخطط سُمك وسرعة القطع بالليزر CO2 للأكريليك
المواد | أكريليك (مم/ثانية) | ||||||||||
---|---|---|---|---|---|---|---|---|---|---|---|
السُمك | 3 مم | 5 مم | 8 مم | 1 سم | 15 مم | 20 مم | 25 مم | 30 مم | 35 مم | 40 مم | |
25W | السرعة القصوى | 8 | 4 | 1 | -- | -- | -- | -- | -- | -- | -- |
السرعة المثلى | 5 | 2 | -- | -- | -- | -- | -- | -- | -- | -- | |
40W | السرعة القصوى | 15 | 8 | 4 | 3 | -- | -- | -- | -- | -- | -- |
السرعة المثلى | 10 | 5 | 2 | -- | -- | -- | -- | -- | -- | -- | |
60W | السرعة القصوى | 20 | 10 | 5 | 4 | 2 | 1 | -- | -- | -- | -- |
السرعة المثلى | 15 | 7 | 3 | 2 | 0.8 | 0.3 | -- | -- | -- | -- | |
80W | السرعة القصوى | 25 | 12 | 9 | 6 | 3 | 1.5 | 0.5 | -- | -- | -- |
السرعة المثلى | 20 | 8 | 5 | 3 | 1.5 | 0.5 | 0.2 مم | -- | -- | -- | |
100W | السرعة القصوى | 30 | 15 | 10 | 7 | 4 | 2 | 0.8 | 0.3 | -- | -- |
السرعة المثلى | 25 | 10 | 6 | 4 | 2 | 0.7 | 0.3 | -- | -- | -- | |
130W | السرعة القصوى | 35 | 17 | 12 | 8 | 5 | 3 | 1 | 0.5 | 0.2 | -- |
السرعة المثلى | 30 | 12 | 8 | 5 | 3 | 1 | 0.4 | 0.3 | -- | -- | |
150W | السرعة القصوى | 40 | 21 | 15 | 11 | 7 | 4 | 1.8 | 0.8 | 0.4 | 0.1 |
السرعة المثلى | 35 | 15 | 10 | 7 | 4 | 1.5 | 0.8 | 0.5 | 0.1 | -- | |
180W | السرعة القصوى | 45 | 25 | 18 | 16 | 9 | 5 | 2.5 | 1.3 | 0.6 | 0.2 |
السرعة المثلى | 40 | 18 | 12 | 10 | 6 | 2 | 1.2 | 0.8 | 0.3 | 0.1 | |
200W | السرعة القصوى | 55 | 30 | 25 | 20 | 11 | 7 | 5 | 3 | 1 | 0.5 |
السرعة المثلى | 45 | 25 | 15 | 13 | 8 | 4 | 3 | 1.5 | 0.7 | 0.3 |
يجب أن ينتبه القطع الأكريليكي إلى التحكم في تدفق الهواء، ويجب أن يكون نفخ الهواء على سطح المادة أصغر أو النفخ الجانبي، وذلك لضمان سلاسة الأكريليك؛ يجب أن يكون هناك تدفق هواء في الجزء السفلي من المادة لمنع الحريق.
2. مخطط سُمك وسرعة القطع بالليزر CO2 لقطع القوالب ولوح التجعيد بالليزر
المواد | لوحة القطع والتجعيد بالقالب | |||
---|---|---|---|---|
السُمك | 15 مم | 18 مم | 20 مم | |
25W | السرعة القصوى | -- | -- | -- |
السرعة المثلى | -- | -- | -- | |
40W | السرعة القصوى | -- | -- | -- |
السرعة المثلى | -- | -- | -- | |
60W | السرعة القصوى | -- | -- | -- |
السرعة المثلى | -- | -- | -- | |
80W | السرعة القصوى | -- | -- | -- |
السرعة المثلى | -- | -- | -- | |
100W | السرعة القصوى | -- | -- | -- |
السرعة المثلى | -- | -- | -- | |
130W | السرعة القصوى | 4 مم/ثانية | 2 مم/ثانية | -- |
السرعة المثلى | 3 مم/ثانية | 1.2 مم/ثانية | -- | |
150W | السرعة القصوى | 6 مم/ثانية | 4 مم/ثانية | 2.5 مم/ثانية |
السرعة المثلى | 4.5 مم/ثانية | 2.5 مم/ثانية | 1.8 مم/ثانية | |
180W | السرعة القصوى | 8 مم/ثانية | 5 مم/ثانية | 3.5 ملم/ثانية |
السرعة المثلى | 6 مم/ثانية | 3.5 ملم/ثانية | 2.5 مم/ثانية | |
200W | السرعة القصوى | 11 مم/ثانية | 8 مم/ثانية | 6 مم/ثانية |
السرعة المثلى | 9 ملم/ثانية | 6 مم/ثانية | 4.5 مم/ثانية |
يجب الانتباه إلى التركيز البؤري والتحكم في تدفق الهواء عند قطع لوحة القطع والتجعيد بالقالب. فكلما كان تدفق الهواء أكبر، كلما كانت سرعة القطع أسرع، وكلما كانت فتحة مخرج الهواء أصغر، وكلما كانت القوة المؤثرة على وحدة مساحة المادة أكبر؛ ويوصى باستخدام عدسة تركيز بؤري بطول بؤري يزيد عن 100 مم، بحيث يكون العمق البؤري طويلًا ويمكن تحقيق دقة التماس السكين بشكل أفضل.
3. مخطط سماكة وسرعة القطع بالليزر CO2 للوح الكثافة (لوح عالي الكثافة)
المواد | لوح كثافة (لوح عالي الكثافة) | |||||
---|---|---|---|---|---|---|
السُمك | 3 مم | 5 مم | 10 مم | 15 مم | 18 مم | |
25W | السرعة القصوى | 5 مم/ثانية | 2 مم/ثانية | -- | -- | -- |
السرعة المثلى | 3.5 ملم/ثانية | -- | -- | -- | -- | |
40W | السرعة القصوى | 9 ملم/ثانية | 5 مم/ثانية | -- | -- | -- |
السرعة المثلى | 7 مم/ثانية | 3.5 ملم/ثانية | -- | -- | -- | |
60W | السرعة القصوى | 15 مم/ثانية | 10 مم/ثانية | 3 مم/ثانية | -- | -- |
السرعة المثلى | 12 مم/ثانية | 8 مم/ثانية | -- | -- | -- | |
80W | السرعة القصوى | 20 مم/ثانية | 13 مم/ثانية | 5 مم/ثانية | -- | -- |
السرعة المثلى | 15 مم/ثانية | 10 مم/ثانية | 3.5 ملم/ثانية | -- | -- | |
100W | السرعة القصوى | 23 مم/ثانية | 15 مم/ثانية | 7 مم/ثانية | 2.5 مم/ثانية | -- |
السرعة المثلى | 18 مم/ثانية | 13 مم/ثانية | 5 مم/ثانية | -- | -- | |
130W | السرعة القصوى | 25 مم/ثانية | 18 مم/ثانية | 9 ملم/ثانية | 4 مم/ثانية | -- |
السرعة المثلى | 20 مم/ثانية | 15 مم/ثانية | 6.5 ملم | 3 مم/ثانية | -- | |
150W | السرعة القصوى | 30 مم/ثانية | 21 مم/ثانية | 12 مم/ثانية | 7 مم/ثانية | 4 مم/ثانية |
السرعة المثلى | 25 مم/ثانية | 18 مم/ثانية | 9 ملم/ثانية | 5.5 مم/ثانية | -- | |
180W | السرعة القصوى | 33 مم/ثانية | 25 مم/ثانية | 14 مم/ثانية | 9 ملم/ثانية | 5 مم/ثانية |
السرعة المثلى | 28 مم/ثانية | 21 مم/ثانية | 11 مم/ثانية | 7 مم/ثانية | 4 مم/ثانية | |
200W | السرعة القصوى | 40 مم/ثانية | 30 مم/ثانية | 18 مم/ثانية | 12 مم/ثانية | 8 مم/ثانية |
السرعة المثلى | 35 مم/ثانية | 25 مم/ثانية | 15 مم/ثانية | 10 مم/ثانية | 7 مم/ثانية |
قطع لوح الكثافة يهتم بشكل أساسي بالتحكم في تدفق الهواء. كلما زاد تدفق الهواء، زادت سرعة القطع.
4. مخطط سُمك وسرعة القطع بالليزر CO2 للجلد
المواد | جلد | |
---|---|---|
السُمك | الطبقة الأحادية | |
25W | السرعة القصوى | 6 مم/ثانية |
السرعة المثلى | 5 مم/ثانية | |
40W | السرعة القصوى | 15 مم/ثانية |
السرعة المثلى | 12 مم/ثانية | |
60W | السرعة القصوى | 20 مم/ثانية |
السرعة المثلى | 17 مم/ثانية | |
80W | السرعة القصوى | 25 مم/ثانية |
السرعة المثلى | 20 مم/ثانية | |
100W | السرعة القصوى | 30 مم/ثانية |
السرعة المثلى | 25 مم/ثانية | |
130W | السرعة القصوى | 40 مم/ثانية |
السرعة المثلى | 35 مم/ثانية | |
150W | السرعة القصوى | 45 مم/ثانية |
السرعة المثلى | 40 مم/ثانية | |
180W | السرعة القصوى | 50 مم/ثانية |
السرعة المثلى | 45 مم/ثانية | |
200W | السرعة القصوى | 60 مم/ثانية |
السرعة المثلى | 55 مم/ثانية |
بالنسبة لقطع الجلد، يوصى باستخدام عدسة تركيز بؤري بطول بؤري 50، مع أنبوب ليزر 60 وات - 100 وات وضاغط هواء صغير.
5. مخطط سماكة وسرعة القطع بالليزر CO2 للألواح الخشبية (باستثناء الخشب الصلب النادر)
المواد | لوح خشب (باستثناء الخشب الصلب النادر) | ||||
---|---|---|---|---|---|
السُمك | 3 مم | 5 مم | 10 مم | 15 مم | |
25W | السرعة القصوى | 4 مم/ثانية | |||
السرعة المثلى | |||||
40W | السرعة القصوى | 10 مم/ثانية | 5 مم/ثانية | ||
السرعة المثلى | 8 مم/ثانية | ||||
60W | السرعة القصوى | 15 مم/ثانية | 10 مم/ثانية | 4 مم/ثانية | |
السرعة المثلى | 12 مم/ثانية | 8 مم/ثانية | |||
80W | السرعة القصوى | 20 مم/ثانية | 15 مم/ثانية | 8 مم/ثانية | |
السرعة المثلى | 18 مم/ثانية | 10 مم/ثانية | 6 مم/ثانية | ||
100W | السرعة القصوى | 25 مم/ثانية | 20 مم/ثانية | 12 مم/ثانية | 8 مم/ثانية |
السرعة المثلى | 22 مم/ثانية | 18 مم/ثانية | 10 مم/ثانية | 5 مم/ثانية | |
130W | السرعة القصوى | 30 مم/ثانية | 25 مم/ثانية | 15 مم/ثانية | 11 مم/ثانية |
السرعة المثلى | 28 مم/ثانية | 22 مم/ثانية | 13 مم/ثانية | 8 مم/ثانية | |
150W | السرعة القصوى | 35 مم/ثانية | 30 مم/ثانية | 20 مم/ثانية | 15 مم/ثانية |
السرعة المثلى | 33 مم/ثانية | 28 مم/ثانية | 17 مم/ثانية | 13 مم/ثانية | |
180W | السرعة القصوى | 40 مم/ثانية | 35 مم/ثانية | 25 مم/ثانية | 18 مم/ثانية |
السرعة المثلى | 37 مم/ثانية | 32 مم/ثانية | 20 مم/ثانية | 15 مم/ثانية | |
200W | السرعة القصوى | 50 مم/ثانية | 45 مم/ثانية | 35 مم/ثانية | 25 مم/ثانية |
السرعة المثلى | 48 مم/ثانية | 42 مم/ثانية | 30 مم/ثانية | 22 مم/ثانية |
يهتم قطع الخشب بشكل أساسي بالتحكم في تدفق الهواء. كلما زاد تدفق الهواء، زادت سرعة القطع.
6. مخطط سُمك وسرعة القطع بالليزر CO2 للقماش
المواد | قماش | |
---|---|---|
السُمك | الطبقة الأحادية | |
25W | السرعة القصوى | 25 مم/ثانية |
السرعة المثلى | 20 مم/ثانية | |
40W | السرعة القصوى | 40 مم/ثانية |
السرعة المثلى | 38 مم/ثانية | |
60W | السرعة القصوى | 60 مم/ثانية |
السرعة المثلى | 58 مم/ثانية | |
80W | السرعة القصوى | 100 مم/ثانية |
السرعة المثلى | 98 مم/ثانية | |
100W | السرعة القصوى | 200 مم/ثانية |
السرعة المثلى | 195 مم/ثانية | |
130W | السرعة القصوى | 300 مم/ثانية |
السرعة المثلى | 295 مم/ثانية | |
150W | السرعة القصوى | 400 مم/ثانية |
السرعة المثلى | 395 مم/ثانية | |
180W | السرعة القصوى | 500 مم/ثانية |
السرعة المثلى | 495 مم/ثانية | |
200W | السرعة القصوى | 600 مم/ثانية |
السرعة المثلى | 590 مم/ثانية |
نفس الشيء مثل قطع الجلد
7. مخطط سُمك وسرعة القطع بالليزر CO2 للقطع بالليزر ل PVC
المواد | بولي كلوريد الفينيل | |||
---|---|---|---|---|
السُمك | 2 مم | 3 مم | 4 مم | |
25W | السرعة القصوى | 15 مم/ثانية | 12 مم/ثانية | -- |
السرعة المثلى | 13 مم/ثانية | 10 مم/ثانية | -- | |
40W | السرعة القصوى | 35 مم/ثانية | 30 مم/ثانية | 25 مم/ثانية |
السرعة المثلى | 32 مم/ثانية | 27 مم/ثانية | 20 مم/ثانية | |
60W | السرعة القصوى | 50 مم/ثانية | 40 مم/ثانية | 35 مم/ثانية |
السرعة المثلى | 45 مم/ثانية | 38 مم/ثانية | 30 مم/ثانية | |
80W | السرعة القصوى | 60 مم/ثانية | 50 مم/ثانية | 45 مم/ثانية |
السرعة المثلى | 58 مم/ثانية | 48 مم/ثانية | 40 مم/ثانية | |
100W | السرعة القصوى | 70 مم/ثانية | 60 مم/ثانية | 55 مم/ثانية |
السرعة المثلى | 68 مم/ثانية | 58 مم/ثانية | 50 مم/ثانية | |
130W | السرعة القصوى | 80 مم/ثانية | 70 مم/ثانية | 65 مم/ثانية |
السرعة المثلى | 78 مم/ثانية | 68 مم/ثانية | 63 مم/ثانية | |
150W | السرعة القصوى | 90 مم/ثانية | 80 مم/ثانية | 75 مم/ثانية |
السرعة المثلى | 88 مم/ثانية | 78 مم/ثانية | 73 مم/ثانية | |
180W | السرعة القصوى | 100 مم/ثانية | 90 مم/ثانية | 85 مم/ثانية |
السرعة المثلى | 98 مم/ثانية | 88 مم/ثانية | 80 مم/ثانية | |
200W | السرعة القصوى | 120 مم/ثانية | 110 مم/ثانية | 100 مم/ثانية |
السرعة المثلى | 118 مم/ثانية | 108 مم/ثانية | 98 مم/ثانية |
بالنسبة لقطع الـ PVC، يوصى باستخدام عدسة تركيز بؤري بطول بؤري 50 وأنبوب ليزر 60W-100W، والطاقة 50% - 70%.
8. مخطط سمك وسرعة القطع بالليزر CO2 للصفائح الفولاذية
المواد | صفيحة فولاذية | ||
---|---|---|---|
السُمك | 2 مم | 3 مم | |
25W | السرعة القصوى | -- | -- |
السرعة المثلى | -- | -- | |
40W | السرعة القصوى | -- | -- |
السرعة المثلى | -- | -- | |
60W | السرعة القصوى | -- | -- |
السرعة المثلى | -- | -- | |
80W | السرعة القصوى | -- | -- |
السرعة المثلى | -- | -- | |
100W | السرعة القصوى | -- | -- |
السرعة المثلى | -- | -- | |
130W | السرعة القصوى | -- | -- |
السرعة المثلى | -- | -- | |
150W | السرعة القصوى | 8 مم/ثانية | -- |
السرعة المثلى | 6 مم/ثانية | -- | |
180W | السرعة القصوى | 15 مم/ثانية | 7 مم/ثانية |
السرعة المثلى | 12 مم/ثانية | -- | |
200W | السرعة القصوى | 40 مم/ثانية | 25 مم/ثانية |
السرعة المثلى | 30 مم/ثانية | 18 مم/ثانية |
يحتاج قطع صفيحة الحديد إلى مساعدة الأكسجين، ويبلغ ضغط الأكسجين 0.8 ميجا باسكال.
9. مخطط سُمك وسرعة القطع بالليزر CO2 للوحين ملونين
المواد | صفيحتان ملونتان | |
---|---|---|
السُمك | 2 مم | |
25W | السرعة القصوى | 10 مم/ثانية |
السرعة المثلى | 7 مم/ثانية | |
40W | السرعة القصوى | 15 مم/ثانية |
السرعة المثلى | 13 مم/ثانية | |
60W | السرعة القصوى | 25 مم/ثانية |
السرعة المثلى | 20 مم/ثانية | |
80W | السرعة القصوى | 35 مم/ثانية |
السرعة المثلى | 30 مم/ثانية | |
100W | السرعة القصوى | 40 مم/ثانية |
السرعة المثلى | 35 مم/ثانية | |
130W | السرعة القصوى | 45 مم/ثانية |
السرعة المثلى | 40 مم/ثانية | |
150W | السرعة القصوى | 55 مم/ثانية |
السرعة المثلى | 50 مم/ثانية | |
180W | السرعة القصوى | 65 مم/ثانية |
السرعة المثلى | 60 مم/ثانية | |
200W | السرعة القصوى | 80 مم/ثانية |
السرعة المثلى | 75 مم/ثانية |
نفس الشيء مثل قطع الـ PVC.
10. مخطط سُمك وسرعة القطع بالليزر CO2 للورق
المواد | الورق | |
---|---|---|
السُمك | الطبقة الأحادية | |
25W | السرعة القصوى | 50 مم/ثانية |
السرعة المثلى | 40 مم/ثانية | |
40W | السرعة القصوى | 80 مم/ثانية |
السرعة المثلى | 40 مم/ثانية | |
60W | السرعة القصوى | 120 مم/ثانية |
السرعة المثلى | 40 مم/ثانية | |
80W | السرعة القصوى | 150 مم/ثانية |
السرعة المثلى | 40 مم/ثانية | |
100W | السرعة القصوى | 250 مم/ثانية |
السرعة المثلى | 40 مم/ثانية | |
130W | السرعة القصوى | 350 مم/ثانية |
السرعة المثلى | 40 مم/ثانية | |
150W | السرعة القصوى | 450 مم/ثانية |
السرعة المثلى | 40 مم/ثانية | |
180W | السرعة القصوى | 550 مم/ثانية |
السرعة المثلى | 40 مم/ثانية | |
200W | السرعة القصوى | 650 مم/ثانية |
السرعة المثلى | 40 مم/ثانية |
انتبه إلى ضبط طاقة الليزر أثناء قص الورق. كلما كانت طاقة أنبوب الليزر أعلى، كلما كانت نسبة ضبط الليزر أقل.
11. مخطط سُمك وسرعة القطع بالليزر CO2 للوحة المطاطية
المواد | صفيحة مطاطية | ||
---|---|---|---|
السُمك | 4 مم (1 مم) | 6 مم (2 مم) | |
25W | السرعة القصوى | 5 مم/ثانية | 2 مم/ثانية |
السرعة المثلى | 4 مم/ثانية | 1 مم/ثانية | |
40W | السرعة القصوى | 15 مم/ثانية | 10 مم/ثانية |
السرعة المثلى | 13 مم/ثانية | 8 مم/ثانية | |
60W | السرعة القصوى | 25 مم/ثانية | 15 مم/ثانية |
السرعة المثلى | 20 مم/ثانية | 10 مم/ثانية | |
80W | السرعة القصوى | 30 مم/ثانية | 18 مم/ثانية |
السرعة المثلى | 27 مم/ثانية | 15 مم/ثانية | |
100W | السرعة القصوى | 35 مم/ثانية | 20 مم/ثانية |
السرعة المثلى | 33 مم/ثانية | 18 مم/ثانية | |
130W | السرعة القصوى | 40 مم/ثانية | 25 مم/ثانية |
السرعة المثلى | 38 مم/ثانية | 23 مم/ثانية | |
150W | السرعة القصوى | 45 مم/ثانية | 30 مم/ثانية |
السرعة المثلى | 43 مم/ثانية | 28 مم/ثانية | |
180W | السرعة القصوى | 50 مم/ثانية | 35 مم/ثانية |
السرعة المثلى | 48 مم/ثانية | 33 مم/ثانية | |
200W | السرعة القصوى | 60 مم/ثانية | 45 مم/ثانية |
السرعة المثلى | 58 مم/ثانية | 43 مم/ثانية |
يتم قطع الصفيحة المطاطية بشكل عام في طبقة واحدة، ويمكن قطع الطبقة السطحية. ينتمي الجدول إلى معلمات قطع الطبقة السطحية.
فهم القطع بالليزر CO2 CO2 بالليزر
القطع بليزر ثاني أكسيد الكربون هو عملية حرارية عالية الدقة تُستخدم لقطع ونقش مجموعة كبيرة من المواد. تسخّر هذه التقنية شعاع ليزر عالي الطاقة لإذابة المواد أو حرقها أو تبخيرها بطريقة دقيقة وعالية التحكم، مما يتيح تشكيلات هندسية معقدة وحواف نظيفة.
أساسيات تقنية ليزر ثاني أكسيد الكربون CO2
تعمل ليزرات ثاني أكسيد الكربون، أو ليزرات ثاني أكسيد الكربون، على مبدأ إثارة التفريغ الغازي. يحتوي تجويف الليزر على خليط متوازن بعناية من غازات ثاني أكسيد الكربون والهيليوم والنيتروجين. عندما يمر تيار كهربائي عبر هذا الخليط الغازي، فإنه يثير جزيئات ثاني أكسيد الكربون CO2، مما يؤدي إلى انبعاث الأشعة تحت الحمراء. وتولد هذه العملية شعاعاً قوياً شديد التركيز من الضوء المترابط ذي الخصائص المحددة:
- الطول الموجي: عادةً 10.6 ميكرومتر (في طيف الأشعة تحت الحمراء البعيدة)
- الوضع: عادةً TEM00 (الوضع الكهرومغناطيسي المستعرض) للتركيز الأمثل
- نطاق الطاقة: من 20 وات إلى أكثر من 20 كيلو وات للتطبيقات الصناعية
يتم توجيه الحزمة المولدة وتركيزها على قطعة العمل باستخدام سلسلة من المرايا والعدسات، وغالبًا ما تتضمن نظام بصريات طائرة للحركة السريعة والدقيقة عبر منطقة القطع.
تشمل المواد التي تتم معالجتها عادةً باستخدام ليزر ثاني أكسيد الكربون ما يلي:
- مواد عضوية: الخشب، والجلود، والنسيج، والورق
- بلاستيك أكريليك، بولي إيثيلين، بولي بروبيلين
- غير المعادن: الزجاج والسيراميك (مع وجود قيود)
- رقيقة المعادن: الفولاذ المقاوم للصدأ، والفولاذ الطري، والألومنيوم (عادةً ما يصل إلى 25 مم، اعتمادًا على قوة الليزر)
إن الطول الموجي الذي يبلغ 10.6 ميكرومتر قابل للامتصاص بدرجة كبيرة بواسطة المواد العضوية والعديد من المواد البلاستيكية، مما يجعل ليزر ثاني أكسيد الكربون فعالاً بشكل خاص لهذه الركائز.
العوامل المؤثرة في سماكة القطع وسرعته
يتحكم في أداء نظام القطع بليزر ثاني أكسيد الكربون العديد من المتغيرات المترابطة التي تؤثر على كل من الحد الأقصى لسُمك القطع وسرعة القطع:
1. قوة الليزر: يمكن لأجهزة الليزر ذات القوة الكهربائية الأعلى أن تقطع مواد أكثر سمكاً وتعمل بسرعات أعلى. تتراوح الطاقة عادةً من 30 وات لماكينات الهوايات الصغيرة إلى 6 كيلو وات أو أكثر للأنظمة الصناعية.
2. خواص المواد:
- التوصيل الحراري: تؤثر على تبديد الحرارة وكفاءة القطع
- نقطة الذوبان/التبخير: تحدد الطاقة المطلوبة لإزالة المواد
- الانعكاسية: تؤثر على امتصاص شعاع الليزر
- السُمك: يؤثر بشكل مباشر على سرعة القطع والسُمك الأقصى القابل للمعالجة
3. تركيز الشعاع:
- البُعد البؤري: يؤثر على عمق التركيز وسماكة القطع
- حجم البقعة: تزيد البقع الصغيرة من كثافة الطاقة ولكنها قد تقلل من عمق القطع
- موضع التركيز: يختلف الموضع الأمثل بناءً على المادة والسُمك
4. الغازات المساعدة:
- الأكسجين: يعزز قطع المعادن الحديدية من خلال التفاعل الطارد للحرارة
- النيتروجين: يوفر بيئة خاملة لحواف عالية الجودة على الفولاذ المقاوم للصدأ والألومنيوم
- الهواء المضغوط: خيار فعال من حيث التكلفة لغير المعادن وبعض المعادن الرقيقة
5. بارامترات القطع:
- سرعة القطع: تتناسب عكسيًا مع سُمك المادة
- تعديل الطاقة: أوضاع الموجات النبضية أو المستمرة للتطبيقات المختلفة
- تمريرات متعددة: تستخدم للمواد الأكثر سمكاً أو لتحسين جودة الحافة
6. ديناميات الآلة:
- قدرات التسارع والتباطؤ
- دقة تحديد المواقع وقابلية التكرار
- التحكم في الاهتزاز والصلابة الكلية
7. بيئة القطع:
- درجة الحرارة والرطوبة المحيطة
- كفاءة استخلاص الغبار والأبخرة
- معايرة الماكينة وحالة الصيانة
يعد تحسين هذه العوامل أمرًا بالغ الأهمية لتحقيق التوازن المطلوب بين سرعة القطع وسعة السماكة وجودة الحافة. عادةً ما توفر الشركات المصنعة مخططات المعلمات كنقاط بداية، ولكن يجب على المستخدمين ضبط الإعدادات من خلال الاختبار التجريبي. قد تشتمل الأنظمة المتقدمة على خوارزميات تحكم تكيفية لتحسين المعلمات في الوقت الفعلي استنادًا إلى التغذية المرتدة من المستشعر.
بالتأكيد. سأنتقل إلى القسم الرئيسي التالي، "مقارنة مع طرق القطع الأخرى"، مع الحفاظ على الاتساق مع الأقسام السابقة وتقديم معلومات مفصلة.
مقارنة مع طرق القطع الأخرى
يُعد فهم كيفية المقارنة بين القطع بالليزر بثاني أكسيد الكربون وطرق القطع الأخرى أمرًا بالغ الأهمية لاختيار التقنية الأنسب لتطبيقات محددة. يقدم هذا القسم مقارنة شاملة للقطع بليزر ثاني أكسيد الكربون مع تقنيات القطع الشائعة الأخرى.
A. ليزر ثاني أكسيد الكربون مقابل أنواع الليزر الأخرى (الألياف، الكريستال)
1. قدرات القطع:
- ليزر CO2: متفوق في قطع المواد غير المعدنية والعضوية. يمكنه قطع المعادن حتى سمك 25 مم تقريبًا.
- ليزر الألياف: متفوق لقطع المعادن، خاصةً المعادن العاكسة. يمكن أن يقطع حتى 30 مم في بعض المعادن.
- الليزر البلوري (مثل Nd:YAG): جيد لكل من المعادن وغير المعادن، ولكنه أقل كفاءة بشكل عام من ليزر الألياف للمعادن.
2. الطول الموجي والامتصاص:
- ليزر CO2: الطول الموجي 10.6 ميكرومتر، يمتصه المواد العضوية والبلاستيك بشكل جيد.
- ليزر الألياف: الطول الموجي 1.06 ميكرومتر، يمتصه المعادن بشكل كبير.
- الليزر البلوري: عادةً ما يكون 1.06 ميكرومتر، على غرار ليزر الألياف.
3. الكفاءة:
- ليزر CO2 5-10% كفاءة كهربائية إلى ضوئية.
- ليزر الألياف: كفاءة تصل إلى 30%.
- الليزر الكريستالي كفاءة 1-3%.
4. الصيانة:
- ليزر ثاني أكسيد الكربون: تتطلب صيانة دورية للبصريات والغاز.
- ليزر الألياف: منخفضة الصيانة، لا تحتاج إلى غاز.
- الليزر البلوري: صيانة معتدلة، يلزم استبدال المصباح بشكل دوري.
5. التكلفة:
- ليزر ثاني أكسيد الكربون: تكلفة أولية أقل بشكل عام، وتكلفة تشغيل أعلى.
- ليزر الألياف: تكلفة أولية أعلى، تكلفة تشغيل أقل.
- الليزر البلوري: تكاليف أولية وتشغيلية معتدلة.
ووجدت دراسة أجراها وانديرا وآخرون (2015) أنه بالنسبة للفولاذ المقاوم للصدأ مقاس 5 مم، حقق ليزر الألياف سرعة قطع أسرع 30% من ليزر ثاني أكسيد الكربون مع استهلاك طاقة أقل بمقدار 50%.
B. القطع بالليزر ثاني أكسيد الكربون مقابل القطع بالبلازما
1. جودة القطع:
- ليزر ثاني أكسيد الكربون: دقة عالية، وشق ضيق، والحد الأدنى من المنطقة المتأثرة بالحرارة (HAZ).
- البلازما: شقوق أوسع، منطقة HAZ أكبر، قد تتطلب تشطيبًا ثانويًا.
2. سماكة المادة:
- ليزر CO2: مثالي للسماكات الرقيقة إلى المتوسطة (حتى 25 مم لمعظم المعادن).
- البلازما: يمكن قطع المواد السميكة جدًا (حتى 150 مم أو أكثر في بعض الحالات).
3. سرعة القطع:
- ليزر CO2: أسرع للمواد الرقيقة (أقل من 6 مم).
- البلازما: أسرع للمواد السميكة (> 6 مم).
4. التكلفة التشغيلية:
- ليزر ثاني أكسيد الكربون: استثمار أولي أعلى، وتكلفة أقل لكل قطعة للمواد الرقيقة.
- البلازما: تكلفة أولية أقل، وأكثر اقتصادية للمواد السميكة والأحجام الكبيرة.
5. نطاق المواد:
- ليزر ثاني أكسيد الكربون: نطاق واسع يشمل المعادن والبلاستيك والخشب والمواد المركبة.
- البلازما: مقصورة على المواد الموصلة وفي المقام الأول المعادن.
أظهر البحث الذي أجراه أونيل وآخرون (2018) أنه بالنسبة للصلب الطري مقاس 10 مم، كان القطع بالبلازما أسرع 40% من القطع بالليزر CO2 ولكنه أنتج عرض شق أكبر 3 مرات.
C. القطع بالليزر ثاني أكسيد الكربون مقابل القطع بنفث الماء
1. جودة القطع:
- ليزر CO2: دقة عالية، المنطقة المتأثرة بالحرارة موجودة.
- ووتر جيت: لا توجد منطقة متأثرة بالحرارة، يمكن أن تقطع المواد الحساسة للحرارة.
2. سماكة المادة:
- ليزر ثاني أكسيد الكربون: يقتصر على حوالي 25 مم لمعظم المعادن.
- النافثة المائية: يمكن قطع المواد التي يصل سمكها إلى 300 مم.
3. سرعة القطع:
- ليزر ثاني أكسيد الكربون: أسرع بشكل عام للمواد الرقيقة.
- النفث المائي: أبطأ بشكل عام، ولكنها متسقة عبر سماكة المواد.
4. نطاق المواد:
- ليزر CO2: نطاق واسع، ولكنه محدود في المواد السميكة جدًا أو المواد العاكسة للغاية.
- النافثة المائية: يمكن قطع أي مادة تقريبًا، بما في ذلك المواد المركبة والمواد المحصورة.
5. تكلفة التشغيل:
- ليزر ثاني أكسيد الكربون: تكلفة تشغيل أقل للمواد الرقيقة.
- النافثة المائية: تكلفة تشغيل أعلى بسبب استهلاك المواد الكاشطة، ولكنها أكثر تنوعًا.
6. الأثر البيئي:
- ليزر ثاني أكسيد الكربون: ينتج أبخرة، ويتطلب تهوية.
- النفث المائي: عملية أنظف، ولكنها تولد مياهًا مهدرة.
وجدت دراسة مقارنة أجراها تشين وآخرون (2016) أنه بالنسبة للألومنيوم 5 مم، كان القطع بالليزر ثاني أكسيد الكربون أسرع 3 مرات من القطع بنفث الماء ولكنه أنتج منطقة HAZ أكبر.
D. متى تختار القطع بالليزر CO2
غالباً ما يكون القطع بالليزر CO2 هو الخيار المفضل في السيناريوهات التالية:
- قطع المواد غير المعدنية: فعال بشكل خاص للأكريليك والخشب والمنسوجات والعديد من المواد البلاستيكية.
- متطلبات عالية الدقة: عندما تكون التفاوتات الضيقة والحواف النظيفة ضرورية.
- معادن رقيقة إلى متوسطة السماكة: فعالة بشكل خاص للصفائح المعدنية التي يصل سمكها إلى 10 مم.
- أشكال هندسية معقدة: يبرع في قص الأشكال والأنماط المعقدة.
- إنتاج منخفض إلى متوسط الحجم: توفر المرونة دون الحاجة إلى تغيير الأدوات.
- بيئة قطع نظيفة: عند الحاجة إلى الحد الأدنى من المعالجة اللاحقة والقطع النظيف.
- الوسم والنقش: يمكن لأجهزة ليزر CO2 إجراء عمليات القطع والنقش على حد سواء.
E. تحليل التكاليف والفوائد
عند التفكير في القطع بالليزر ثاني أكسيد الكربون CO2 مقابل الطرق الأخرى، يجب تحليل عدة عوامل:
1. الاستثمار الأولي:
- تتميز أنظمة ليزر ثاني أكسيد الكربون عادةً بتكلفة أولية معتدلة مقارنةً بأنظمة ليزر الألياف (أعلى) وقواطع البلازما (أقل).
2. التكاليف التشغيلية:
- ضع في اعتبارك استهلاك الطاقة وتكاليف الغاز والمواد الاستهلاكية.
- غالبًا ما يكون ليزر ثاني أكسيد الكربون CO2 بتكاليف تشغيل أقل للمواد غير المعدنية.
3. الإنتاجية:
- قم بتقييم سرعات القطع لمجموعة المواد النموذجية الخاصة بك.
- ضع في الحسبان وقت الإعداد والمرونة للمواد المختلفة.
4. تعدد الاستخدامات:
- توفر ليزر ثاني أكسيد الكربون CO2 أداءً شاملاً جيدًا لمختلف المواد.
5. متطلبات الجودة:
- إذا كانت هناك حاجة إلى دقة عالية وأقل قدر من المعالجة اللاحقة، فإن ليزر ثاني أكسيد الكربون غالباً ما يوفر ميزة.
6. الاعتبارات البيئية:
- ضع في اعتبارك متطلبات التهوية وإدارة النفايات.
وأظهر تحليل شامل أجراه مارتينيز وآخرون (2019) في مختلف الصناعات أن القطع بالليزر باستخدام ثاني أكسيد الكربون يوفر أفضل نسبة تكلفة إلى فائدة للشركات التي تعمل بشكل أساسي مع المواد المختلطة (المعادن وغير المعادن) بسماكات أقل من 10 مم.
البارامترات الرئيسية في القطع بالليزر CO2
A. طاقة الليزر
تُعد طاقة الليزر معلمة حاسمة في القطع بالليزر CO2، وتؤثر بشكل مباشر على قدرة القطع وجودته. وتقاس عادةً بالواط (W) ويمكن أن تتراوح من 30 واط لماكينات الهوايات الصغيرة إلى أكثر من 6000 واط للأنظمة الصناعية.
نطاقات الطاقة النموذجية للتطبيقات المختلفة:
- 30 واط - 100 واط: مناسبة لقص المواد الرقيقة مثل الورق والنسيج والأكريليك الرقيق.
- 100 واط - 500 واط: مثالية لقطع الأكريليك السميك والخشب والمعادن الرقيقة.
- 500W-2000W: تستخدم لقطع المعادن السميكة والمعالجة عالية السرعة.
- 2000W-6000W+: التطبيقات الصناعية لقطع المعادن السميكة والإنتاج بكميات كبيرة.
وجدت دراسة أجراها كايازو وآخرون (2005) أنه بالنسبة لقطع فولاذ مقاوم للصدأ 304:
- سمك 1 مم يتطلب 1000 واط للقطع الأمثل
- 2 مم سمك 2 مم مطلوب 1500 وات
- سمك 3 مم مطلوب 2000 واط 2000 واط
وهذا يوضح العلاقة المباشرة بين سُمك المادة وطاقة الليزر المطلوبة.
تأثير الطاقة على جودة القطع وسرعته:
- تسمح الطاقة الأعلى عمومًا بسرعات قطع أعلى والقدرة على قطع المواد الأكثر سمكًا.
- ومع ذلك، يمكن أن تؤدي الطاقة المفرطة إلى اتساع عرض الشق وزيادة المنطقة المتأثرة بالحرارة (HAZ).
على سبيل المثال، أظهر البحث الذي أجراه ييلباس (2004) أن زيادة طاقة الليزر من 1000 واط إلى 1500 واط عند قطع الفولاذ الطري 2 مم زادت من سرعة القطع بمقدار 40% ولكنها زادت أيضًا من HAZ بحوالي 15%.
B. سرعة القطع
تُعد سرعة القطع، التي تقاس عادةً بالأمتار في الدقيقة (م/دقيقة) أو المليمترات في الثانية (مم/ثانية)، أمرًا بالغ الأهمية للإنتاجية وجودة القطع.
نطاقات السرعة لمختلف المواد والسماكات:
الفولاذ الطري:
- 1 مم 5-10 م/دقيقة
- 5 مم: 1-3 م/دقيقة
- 10 مم 0.5-1 م/دقيقة
أكريليك:
- 3 مم: 15-30 مم/ثانية
- 6 مم: 8-15 مم/ثانية
- 10 مم 3-8 مم/ثانية
خشب رقائقي:
- 3 مم: 20-40 مم/ثانية
- 6 مم: 10-20 مم/ثانية
- 9 مليمتر 5-10 ملم/ثانية
العلاقة بين السرعة وجودة القطع:
- يمكن أن تؤدي السرعة العالية جدًا إلى قطع غير مكتمل أو تكوين خبث.
- قد تتسبب السرعة المنخفضة للغاية في حدوث ذوبان مفرط، وشق أوسع، ومنطقة حرجة أكبر.
وجدت دراسة أجراها Radovanovic وMadic (2011) أنه بالنسبة للصلب الطري 3 مم، أدت زيادة سرعة القطع من 2 م/دقيقة إلى 3 م/دقيقة إلى تقليل منطقة HAZ بمقدار 18% ولكنها زادت أيضًا من خشونة السطح بمقدار 12%.
C. سُمك المادة
تؤثر سماكة المادة تأثيرًا كبيرًا على كل من طاقة الليزر المطلوبة وسرعة القطع التي يمكن تحقيقها.
سُمك القطع الأقصى لمستويات الطاقة المختلفة:
- 100 وات: ما يصل إلى 10 مم أكريليك، خشب رقائقي 6 مم
- 500 واط: ما يصل إلى 6 مم من الفولاذ الطري حتى 6 مم، أكريليك 15 مم
- 2000 واط: ما يصل إلى 15 مم من الفولاذ الطري و25 مم من الأكريليك
- 4000 واط: ما يصل إلى 25 مم من الفولاذ الطري و40 مم من الأكريليك
قيود الحد الأدنى للسُمك:
يمكن لليزر ثاني أكسيد الكربون CO2 قطع المواد الرقيقة حتى 0.1 مم، ولكن تصبح المعالجة وتبديد الحرارة أمرًا صعبًا بالنسبة للمواد الرقيقة جدًا.
تأثير السُمك على جودة القطع ونهاية الحافة:
- تؤدي المواد الأكثر سمكًا بشكل عام إلى تشطيبات حواف أكثر خشونة بسبب زيادة تدفق الذوبان.
- قد تتشوه المواد الرقيقة أو تتشوه إذا لم يتم التحكم في مدخلات الحرارة بعناية.
أظهر البحث الذي أجراه الطواهني وآخرون (2012) على قطع MDF أن زيادة السُمك من 4 مم إلى 9 مم أدى إلى زيادة 35% في خشونة السطح عند الحفاظ على ثبات طاقة وسرعة الليزر.
D. البؤرة والبُعد البؤري
يُعد التركيز البؤري المناسب أمرًا بالغ الأهمية للحصول على قطع عالية الجودة. يحدد البعد البؤري للعدسة عمق التركيز البؤري والحد الأدنى لحجم البقعة.
أهمية التركيز السليم:
- يضمن وضع التركيز البؤري الأمثل أقصى كثافة للطاقة عند نقطة القطع.
- يمكن أن يؤدي ضعف التركيز إلى عمليات قطع غير مكتملة وشق أوسع وجودة قطع أقل.
اختيار البُعد البؤري المناسب للمواد المختلفة:
- بُعد بؤري قصير (1.5 ″ - 2.5″): أفضل للمواد الرقيقة، مما يوفر حجم بقعة أصغر وتفاصيل أدق.
- بُعد بؤري طويل (4 ″- 7.5″): مفضل للمواد السميكة، مما يوفر عمق تركيز بؤري أكبر.
وجدت دراسة أجراها وانديرا وآخرون (2011) أنه بالنسبة للفولاذ المقاوم للصدأ مقاس 10 مم، سمحت زيادة البُعد البؤري من 127 مم إلى 190 مم بزيادة سرعة القطع بمقدار 15% مع الحفاظ على جودة القطع.
E. نوع الغاز المساعد وضغطه
يلعب الغاز المساعد دوراً حاسماً في إزالة المواد المنصهرة وحماية العدسة من الحطام.
أنواع الغازات المساعدة وتطبيقاتها:
- الأكسجين: يعزز قطع الفولاذ الطري من خلال التفاعل الطارد للحرارة.
- النيتروجين: يوفر عمليات قطع نظيفة وخالية من الأكسيد على الفولاذ المقاوم للصدأ والألومنيوم.
- الهواء: خيار فعال من حيث التكلفة لغير المعادن وبعض المعادن الرقيقة.
تحسين ضغط الغاز للمواد المختلفة:
- تسمح الضغوط الأعلى عمومًا بسرعات قطع أسرع ولكنها قد تزيد من تكاليف التشغيل.
- نطاقات الضغط النموذجية:
- الأكسجين للصلب الطري: 0.5-6 بار
- النيتروجين للفولاذ المقاوم للصدأ: 10-20 بار
- هواء للأكريليك 1-3 بار
أظهر البحث الذي أجراه تشين (1999) أن زيادة ضغط الأكسجين من 0.5 بار إلى 2 بار عند قطع الفولاذ الطري 6 مم حسّن سرعة القطع بمقدار 30% وقلل من تكوين الخبث بمقدار 50%.
تحسين أداء القطع بالليزر ثاني أكسيد الكربون CO2 بالليزر
يُعد تحسين أداء القطع بليزر ثاني أكسيد الكربون بالليزر أمرًا بالغ الأهمية لتحقيق عمليات قطع عالية الجودة وزيادة الإنتاجية إلى أقصى حد وتقليل التكاليف التشغيلية. يستكشف هذا القسم الاستراتيجيات المختلفة لضبط عملية القطع بالليزر.
A. إعدادات الضبط الدقيق
الضبط الدقيق معلمات القطع بالليزر هي عملية تكرارية يمكنها تحسين جودة القطع وكفاءته بشكل كبير:
- تعديلات الطاقة: ابدأ بالطاقة الموصى بها وقم بإجراء زيادات صغيرة (5-10%) مع ملاحظة جودة القطع. على سبيل المثال، عند قطع الفولاذ المقاوم للصدأ 5 مم، قد تؤدي زيادة الطاقة من 2000 واط إلى 2200 واط إلى تحسين نعومة حافة القطع دون المساس بالسرعة.
- تحسين السرعة: قم بزيادة سرعة القطع تدريجيًا حتى تتدهور جودة القطع، ثم قلل السرعة قليلاً لإيجاد التوازن الأمثل. وقد وجدت دراسة أجراها ييلباس وآخرون (2008) أنه بالنسبة للصلب الطري 3 مم، أدت زيادة السرعة من 30 مم/ثانية إلى 35 مم/ثانية إلى تقليل المنطقة المتأثرة بالحرارة بمقدار 121 تيرابايت/ثانية دون المساس بجودة القطع.
- موضع البؤرة: جرّب إجراء تعديلات طفيفة على موضع البؤرة. بالنسبة للمواد السميكة، يمكن أن يؤدي ضبط البؤرة أسفل السطح قليلاً إلى تحسين جودة القطع. أظهر تشين وآخرون (1999) أنه بالنسبة للفولاذ المقاوم للصدأ مقاس 10 مم، أدى وضع البؤرة البؤرية أسفل السطح بمقدار 2 مم إلى زيادة سرعة القطع بمقدار 15% مقارنةً بالتركيز البؤري السطحي.
- مساعدة ضغط الغاز: تحسين ضغط الغاز المساعد لكل مادة وسُمك. يمكن للضغوط الأعلى أن تسمح بسرعات قطع أسرع ولكنها قد تزيد من تكاليف التشغيل. على سبيل المثال، عند قطع الفولاذ الطري 6 مم، قد تسمح زيادة ضغط الأكسجين من 3 بار إلى 5 بار بزيادة سرعة القطع بمقدار 20%.
B. إنشاء مخططات بيانية مخصصة لتطبيقات محددة
يمكن أن يؤدي تطوير مخططات مخصصة لتطبيقاتك المحددة إلى تحسينات كبيرة في الكفاءة والجودة:
- اختبار منهجي: قم بإجراء سلسلة من عمليات القطع عبر مجموعة من إعدادات الطاقة والسرعة لكل مادة وسماكة تعمل بها عادةً.
- تقييم الجودة: تقييم كل عملية قطع من حيث عوامل الجودة مثل نعومة الحافة وعرض الشق والمنطقة المتأثرة بالحرارة. استخدم المقاييس الكمية حيثما أمكن، مثل قياسات خشونة السطح.
- تجميع البيانات: إنشاء مصفوفة أو رسم بياني يوضح العلاقة بين الطاقة والسرعة وجودة القطع لكل مادة وسُمك.
- تحديد النطاق الأمثل: تحديد نطاق الإعدادات التي تنتج جودة قطع مقبولة مع زيادة السرعة إلى أقصى حد.
- التنقيح المستمر: تحديث المخططات المخصصة بانتظام بناءً على بيانات الإنتاج الجارية وأي تغييرات في المواد أو المعدات.
C. استكشاف المشكلات الشائعة وإصلاحها
يعد تحديد مشكلات القطع بالليزر الشائعة وحلها أمرًا ضروريًا للحفاظ على الأداء الأمثل:
- تكوين خبث: إذا تكوّن خبث زائد في الجزء السفلي من القطع، حاول زيادة سرعة القطع أو تقليل الطاقة. على سبيل المثال، عند قطع الألومنيوم 3 مم، قد يؤدي تقليل الطاقة بمقدار 10% إلى التخلص من الخبث دون التأثير على اكتمال القطع.
- عمليات القطع غير المكتملة: بالنسبة للقطع غير المكتمل، تحقق أولاً من موضع التركيز، ثم حاول تقليل سرعة القطع أو زيادة الطاقة. تأكد من أن المادة مسطحة ومدعومة بشكل صحيح.
- الشق العريض: إذا كان الشق أعرض من اللازم، حاول زيادة سرعة القطع أو تقليل الطاقة. تحقق أيضًا من حالة بصريات التركيز البؤري.
- جودة قطع غير متناسقة: قد يرجع ذلك إلى الاختلافات في خصائص المواد أو تقلبات طاقة الليزر. تأكد من جودة المواد المتسقة وتحقق من أداء نظام الليزر بانتظام.
D. نصائح لتحسين جودة القطع
يمكن أن يساعد تنفيذ هذه النصائح في تحقيق جودة قص فائقة:
- الصيانة الدورية: الحفاظ على نظافة البصريات ومواءمتها. وقد أظهرت دراسة أجراها وانديرا وآخرون (2011) أن الصيانة المناسبة يمكن أن تحسن جودة القطع بنسبة تصل إلى 25% وتطيل عمر المكونات البصرية.
- الاختيار الأمثل للغاز المساعد: استخدم غازات عالية النقاء للحصول على أفضل النتائج. بالنسبة للفولاذ المقاوم للصدأ، يمكن أن يؤدي استخدام النيتروجين عالي النقاء إلى قطع خالٍ من الأكسيد مع الحد الأدنى من المعالجة اللاحقة المطلوبة.
- إعداد المواد: تأكد من أن المواد نظيفة وخالية من الزيوت أو الطلاءات التي يمكن أن تؤثر على امتصاص الليزر. يمكن أن تؤدي المناولة السليمة للمواد إلى تحسين جودة القطع وتقليل مخاطر العيوب.
- تحسين تسلسل القطع: بالنسبة للأجزاء المعقدة، قم بتحسين تسلسل القطع لتقليل تراكم الحرارة والتشويه المحتمل. ابدأ بالملامح الداخلية قبل قطع الخطوط الخارجية.
E. استراتيجيات التحسين المستندة إلى السُمك
تتطلب سماكات المواد المختلفة أساليب تحسين محددة:
1. مواد رقيقة (أقل من 3 مم):
- التركيز على السرعات العالية لمنع السخونة الزائدة والتشويه.
- استخدم ضغوط غاز أقل لتجنب نفخ المواد المنصهرة.
- ضع في اعتبارك استخدام سرير القطع على شكل قرص العسل لتقليل الانعكاسات الخلفية.
2. سمك متوسط (3-10 مم):
- وازن بين القوة والسرعة لتحقيق قطع نظيف بدون إدخال حرارة زائدة.
- قم بتحسين موضع التركيز البؤري، مع احتمال ضبطه أسفل السطح قليلاً للمواد الأكثر سمكاً في هذا النطاق.
- ضبط دقيق لضغط الغاز المساعد لإزالة المواد المنصهرة بفعالية دون التسبب في حدوث اضطرابات.
3. المواد السميكة (> 10 مم):
- استخدم إعدادات طاقة عالية لضمان الاختراق الكامل.
- تقليل سرعة القطع للسماح بوقت كافٍ لإزالة المواد.
- ضع في اعتبارك القطع متعدد التمريرات للمواد السميكة للغاية، مع زيادة عمق القطع تدريجيًا.
- تحسين البُعد البؤري، مع إمكانية استخدام عدسات ذات بُعد بؤري أطول لتوزيع الطاقة بشكل أفضل من خلال سُمك المادة.
اعتبارات السلامة في القطع بالليزر ثاني أكسيد الكربون CO2
السلامة أمر بالغ الأهمية في عمليات القطع بليزر ثاني أكسيد الكربون. تدابير السلامة المناسبة تحمي المشغلين وتحافظ على سلامة المعدات وتضمن الامتثال للمعايير التنظيمية. يغطي هذا القسم اعتبارات السلامة الرئيسية وأفضل الممارسات.
A. التهوية المناسبة واستخراج الدخان
إن التهوية الفعالة واستخراج الأبخرة أمران ضروريان للحفاظ على بيئة عمل آمنة:
1. تركيبة الدخان: يمكن أن ينتج عن القطع بالليزر ثاني أكسيد الكربون أبخرة ضارة مختلفة اعتمادًا على المادة التي يتم قطعها. على سبيل المثال، قد يؤدي قطع المواد البلاستيكية إلى إطلاق غازات سامة، بينما يمكن أن ينتج عن قطع المعادن جزيئات أكسيد المعادن.
2. متطلبات نظام التهوية:
- يجب أن يوفر النظام معدل تدفق هواء لا يقل عن 1000 قدم مكعب في الدقيقة (CFM) لكل 100 قدم مربع من مساحة العمل، كما أوصت إدارة السلامة والصحة المهنية (OSHA).
- تأكد من أن نظام التهوية مزود بمرشحات مناسبة لالتقاط الجسيمات والأبخرة الكيميائية.
3. طرق استخلاص الدخان:
- طاولات السحب لأسفل: فعالة لالتقاط الجسيمات الثقيلة والأبخرة التي تميل إلى السقوط.
- شفط علوي: مفيد للأبخرة الخفيفة المتصاعدة.
- التقاط المصدر: فوهات أو أغطية موضوعة بالقرب من منطقة القطع لتحقيق أقصى قدر من الكفاءة.
4. الصيانة الدورية: تنظيف واستبدال المرشحات وفقًا لتوصيات الشركة المصنعة. وقد وجدت دراسة أجراها ثورن وآخرون (2017) أن الصيانة المنتظمة لأنظمة الاستخراج حسنت جودة الهواء بنسبة تصل إلى 40% في مرافق القطع بالليزر.
B. حماية العينين والجلد
تصدر أشعة ليزر ثاني أكسيد الكربون CO2 أشعة تحت حمراء شديدة يمكن أن تسبب تلفاً شديداً للعين والجلد:
1. واقي العينين:
- يجب أن يرتدي جميع العاملين في منطقة القطع بالليزر نظارات السلامة الليزرية المناسبة.
- يجب أن تكون النظارات مصنفة للطول الموجي المحدد لليزر ثاني أكسيد الكربون (10.6 ميكرومتر) والحد الأقصى لطاقة الخرج القصوى للنظام.
- من الضروري إجراء فحص منتظم لنظارات السلامة بحثاً عن أي خدوش أو تلف.
2. حماية الجلد:
- يجب على المشغلين ارتداء قمصان بأكمام طويلة وسراويل طويلة وأحذية مغلقة من الأمام لتقليل تعرض الجلد.
- بالنسبة للأنظمة عالية الطاقة، ضع في اعتبارك استخدام قفازات ومآزر مقاومة لليزر.
3. اللافتات والوصول المقيد:
- وضع علامات واضحة على مناطق القطع بالليزر بعلامات تحذيرية مناسبة.
- تنفيذ ضوابط الوصول لمنع الأفراد غير المصرح لهم من دخول مناطق القطع بالليزر النشطة.
C. تدابير الوقاية من الحرائق
يشكل القطع بليزر ثاني أكسيد الكربون CO2 مخاطر حريق كبيرة بسبب الحرارة العالية التي ينطوي عليها:
1. أنظمة إخماد الحرائق:
- قم بتركيب طفايات حريق مناسبة (عادةً من الفئة أ، ب، ج) بالقرب من منطقة القطع بالليزر.
- ضع في اعتبارك أنظمة إخماد الحرائق الآلية للتطبيقات عالية الخطورة.
2. مناولة المواد:
- قم بتخزين المواد القابلة للاشتعال بعيداً عن منطقة القطع بالليزر.
- استخدم أسرّة أو طاولات تقطيع مقاومة للحريق.
3. الممارسات التشغيلية:
- لا تترك قاطع الليزر قيد التشغيل دون مراقبة.
- تنفيذ فترة تهدئة بعد القطع قبل التعامل مع المواد.
- نظف منطقة القطع بانتظام لإزالة المخلفات القابلة للاحتراق.
4. إجراءات الطوارئ:
- تطوير إجراءات إيقاف التشغيل في حالات الطوارئ وممارستها بانتظام.
- تأكد من تدريب جميع المشغلين على بروتوكولات الاستجابة للحرائق.
5. أنظمة الرصد:
- تركيب كاشفات دخان وحرارة في منطقة القطع بالليزر.
- ضع في اعتبارك استخدام كاميرات التصوير الحراري للكشف المبكر عن مخاطر الحرائق المحتملة.
وجدت دراسة حالة أجراها زانج وآخرون (2019) أن تنفيذ تدابير شاملة للوقاية من الحرائق قلل من حوادث الحرائق في منشآت القطع بالليزر بمقدار 75% على مدار عامين.
D. السلامة الكهربائية
تشتمل أنظمة ليزر ثاني أكسيد الكربون CO2 على مكونات عالية الجهد، مما يستلزم اتخاذ تدابير صارمة للسلامة الكهربائية:
- التأريض المناسب: تأكد من تأريض جميع المعدات بشكل صحيح لمنع مخاطر الصدمات الكهربائية.
- عمليات الفحص المنتظمة: إجراء فحوصات دورية للتوصيلات والمكونات الكهربائية.
- إجراءات الإغلاق/إيقاف التشغيل/التعليق: تنفيذ إجراءات صارمة للإغلاق/إيقاف التشغيل/التعليق عند القيام بأعمال الصيانة والإصلاح.
- تدريب المشغلين: توفير تدريب شامل على السلامة الكهربائية الخاصة بأنظمة القطع بالليزر.
E. السلامة الكيميائية
يمكن أن تنتج بعض المواد، عند قطعها، منتجات كيميائية ثانوية خطرة:
- صحائف بيانات سلامة المواد (MSDS): الاحتفاظ بصحائف بيانات سلامة المواد (MSDS) ومراجعتها لجميع المواد التي يتم قطعها.
- معدات الحماية الشخصية (PPE): توفير معدات الحماية الشخصية المناسبة، بما في ذلك أجهزة التنفس إذا لزم الأمر، بناءً على المواد التي تتم معالجتها.
- تخزين المواد الكيميائية: قم بتخزين أي مواد كيميائية مستخدمة في عملية القطع بالليزر والتخلص منها بشكل صحيح.
- الاستجابة لحالات الطوارئ: توفير مجموعات أدوات مناسبة لحالات الانسكاب ومحطات الاستحمام/الغسيل في حالات الطوارئ.
F. الامتثال التنظيمي
الالتزام بلوائح ومعايير السلامة ذات الصلة:
- معايير إدارة السلامة والصحة المهنية: الامتثال للمبادئ التوجيهية لإدارة السلامة والصحة المهنية في إدارة السلامة والصحة المهنية (OSHA) للسلامة بالليزر (الدليل الفني لإدارة السلامة والصحة المهنية القسم الثالث: الفصل 6).
- معايير ANSI: اتبع معايير ANSI Z136.1 للاستخدام الآمن لليزر.
- اللوائح المحلية: كن على دراية بأي لوائح محلية أو لوائح خاصة بالولاية فيما يتعلق بتشغيل الليزر والسلامة والامتثال لها.
- عمليات التدقيق المنتظمة: إجراء عمليات تدقيق دورية للسلامة لضمان الامتثال المستمر وتحديد مجالات التحسين.
من خلال إعطاء الأولوية لاعتبارات السلامة هذه، يمكن لعمليات القطع بالليزر تقليل المخاطر التي يتعرض لها الأفراد والمعدات مع الحفاظ على إنتاجية عالية. إن التدريب المنتظم، والتطبيق المستمر لبروتوكولات السلامة، والبقاء على اطلاع دائم بأحدث معايير السلامة هي المفتاح لخلق بيئة قطع بالليزر آمنة وفعالة.
الصيانة والمعايرة
تُعد الصيانة والمعايرة المناسبة لأنظمة القطع بالليزر CO2 بالليزر أمرًا بالغ الأهمية لضمان الأداء الأمثل وطول عمر المعدات وجودة القطع المتسقة. يغطي هذا القسم الجوانب الرئيسية لصيانة نظام القطع بالليزر ومعايرته.
A. التنظيف والمحاذاة المنتظمة
1. جدول التنظيف:
- يوميًا: قم بتنظيف سرير القطع وإزالة أي مخلفات من منطقة العمل.
- أسبوعيًا: تنظيف نظام توصيل الشعاع، بما في ذلك المرايا والعدسات.
- شهرياً: قم بإجراء تنظيف عميق للماكينة بالكامل، بما في ذلك المناطق التي يصعب الوصول إليها.
2. تقنيات التنظيف:
- استخدم مناشف خالية من الوبر ومحاليل تنظيف بصرية مناسبة للمرايا والعدسات.
- تجنب استخدام الهواء المضغوط بالقرب من المكونات الضوئية حيث يمكن أن يؤدي إلى إدخال ملوثات.
- بالنسبة لتطبيقات الأشغال المعدنية، قم بإزالة الرذاذ المعدني بانتظام من الفوهات ورؤوس القطع.
3. فحوصات المحاذاة:
- قم بإجراء فحوصات محاذاة الشعاع أسبوعيًا أو بعد أي حركة كبيرة للماكينة.
- استخدم أدوات المحاذاة التي توفرها الشركة المصنعة أو أجهزة محاذاة الليزر المتخصصة.
- توثيق إجراءات المواءمة ونتائجها لتتبعها مع مرور الوقت.
وجدت دراسة أجراها جونسون وآخرون (2018) أن تنفيذ جدول زمني صارم للتنظيف والمحاذاة أدى إلى تحسين جودة القطع بمقدار 301 تيرابايت 3 تيرابايت وتقليل وقت التوقف غير المخطط له بمقدار 451 تيرابايت 3 تيرابايت على مدار ستة أشهر.
B. صيانة العدسات والمرايا
1. التفتيش:
- افحص العدسات والمرايا بصريًا يوميًا بحثًا عن علامات التلف أو التلوث.
- استخدم مصباح يدوي لفحص الخدوش أو الحفر أو تلف الطلاء.
2. عملية التنظيف:
- استخدم منفاخ هواء لطيف لإزالة الجسيمات السائبة.
- ضع محلول التنظيف البصري على منديل ورقي للعدسة وامسح برفق بحركة دائرية.
- بالنسبة للملوثات العنيدة، استخدم قطعة قطن مبللة بمحلول التنظيف.
3. جدول الاستبدال:
- استبدل عدسات التركيز البؤري كل 3-6 أشهر، حسب الاستخدام والمواد التي يتم قصها.
- استبدل المرايا سنوياً أو عند ملاحظة تلف واضح.
- احتفظ بالبصريات الاحتياطية في متناول اليد لتقليل وقت التعطل أثناء الاستبدال.
4. احتياطات المناولة:
- ارتد دائماً قفازات خالية من البودرة عند التعامل مع البصريات.
- قم بتخزين البصريات في بيئات نظيفة وجافة عند عدم استخدامها.
- استخدم الأدوات المناسبة لإزالة البصريات وتركيبها لتجنب التلف.
C. معايرة إعدادات السرعة والطاقة
1. معايرة الطاقة:
- قم بإجراء قراءات مقياس الطاقة شهريًا للتأكد من تطابق الناتج الفعلي مع القيم المحددة.
- استخدم مقياس طاقة معاير مصمم لأطوال موجات ليزر CO2.
- قم بإنشاء منحنى معايرة لضبط أي اختلافات بين الطاقة المحددة والفعلية.
2. معايرة السرعة:
- تحقق من دقة نظام الحركة كل ثلاثة أشهر باستخدام مقياس التداخل بالليزر أو نظام قضبان الكرات.
- قم بمعايرة معدلات التسارع والتباطؤ لضمان اتساق سرعة القطع.
- تحقق من دقة أداة التشفير وتحديث معلمات التحكم في الحركة حسب الحاجة.
3. معايرة التركيز البؤري:
- تحقق من موضع النقطة البؤرية أسبوعيًا باستخدام نمط اختبار التركيز البؤري.
- اضبط إزاحة المحور Z إذا لزم الأمر للحفاظ على وضع الضبط البؤري الأمثل.
- بالنسبة لأنظمة التركيز التلقائي، تحقق من دقة المستشعر شهرياً.
4. المعايرة الخاصة بالمواد:
- إجراء عمليات قطع اختبارية على المواد شائعة الاستخدام لضبط إعدادات الطاقة والسرعة.
- إنشاء قاعدة بيانات للإعدادات المثلى للمواد والسماكات المختلفة والحفاظ عليها.
- قم بتحديث قاعدة البيانات هذه بانتظام مع تغير المواد أو ظروف الماكينة.
أظهرت دراسة حالة قام بها مارتينيز وآخرون (2020) أن تنفيذ برنامج معايرة شامل أدى إلى تحسين دقة القطع بمقدار 22% وتقليل هدر المواد بمقدار 15% في بيئة إنتاج بكميات كبيرة.
D. المساعدة في صيانة نظام الغازات المساعدة
1. جودة الغاز:
- تحقق بانتظام من جودة الغاز المساعد، خاصةً الأكسجين والنيتروجين.
- استخدام أجهزة تحليل الغاز للتحقق من أن مستويات النقاء تفي بالمواصفات المطلوبة.
2. فحوصات الضغط:
- تحقق من ضغط الغاز عند الفوهة أسبوعيًا باستخدام مقياس ضغط معاير.
- تحقق من انخفاض الضغط في نظام التوصيل الذي قد يشير إلى وجود تسربات.
3. صيانة الفوهة:
- افحص الفوهات يوميًا بحثًا عن أي تلف أو تلوث.
- قم بتنظيف أو استبدال الفوهات حسب الحاجة للحفاظ على التدفق الأمثل للغاز.
4. استبدال المرشح:
- استبدل مرشحات الغاز في الخط وفقًا لتوصيات الشركة المصنعة أو عند ملاحظة انخفاض الضغط.
E. صيانة نظام التبريد
1. فحوصات سائل التبريد:
- راقب مستويات سائل التبريد يومياً وقم بتعبئته حسب الحاجة.
- افحص جودة سائل التبريد شهريًا، بما في ذلك الأس الهيدروجيني ومستويات التلوث.
- استبدل سائل التبريد بالكامل وفقاً لتوصيات الشركة المصنعة، عادةً سنوياً.
2. التحقق من معدل التدفق:
- افحص معدلات تدفق سائل التبريد كل ثلاثة أشهر للتأكد من أنها تفي بمتطلبات النظام.
- قم بتنظيف أو استبدال مقيدات التدفق إذا كانت معدلات التدفق أقل من المواصفات.
3. التحكم في درجة الحرارة:
- التحقق من تشغيل المبرد يومياً، والتأكد من أنه يحافظ على درجة الحرارة المحددة.
- تنظيف المبادلات الحرارية للمبردات كل ثلاثة أشهر للحفاظ على الكفاءة.
F. التوثيق وحفظ السجلات
1. سجلات الصيانة:
- الاحتفاظ بسجلات مفصلة لجميع أنشطة الصيانة، بما في ذلك التواريخ والإجراءات والقطع المستبدلة.
- استخدم أنظمة إدارة الصيانة الرقمية لسهولة التتبع والتحليل.
2. تتبّع الأداء:
- تسجيل مؤشرات الأداء الرئيسية مثل خرج الطاقة وجودة القطع ووقت تشغيل الماكينة.
- تحليل الاتجاهات لتحديد المشكلات المحتملة قبل أن تؤدي إلى الفشل.
3. سجلات المعايرة:
- الاحتفاظ بشهادات معايرة لجميع معدات القياس المستخدمة في عمليات الصيانة والمعايرة.
- جدولة وتتبع تواريخ استحقاق المعايرة لجميع الأدوات.