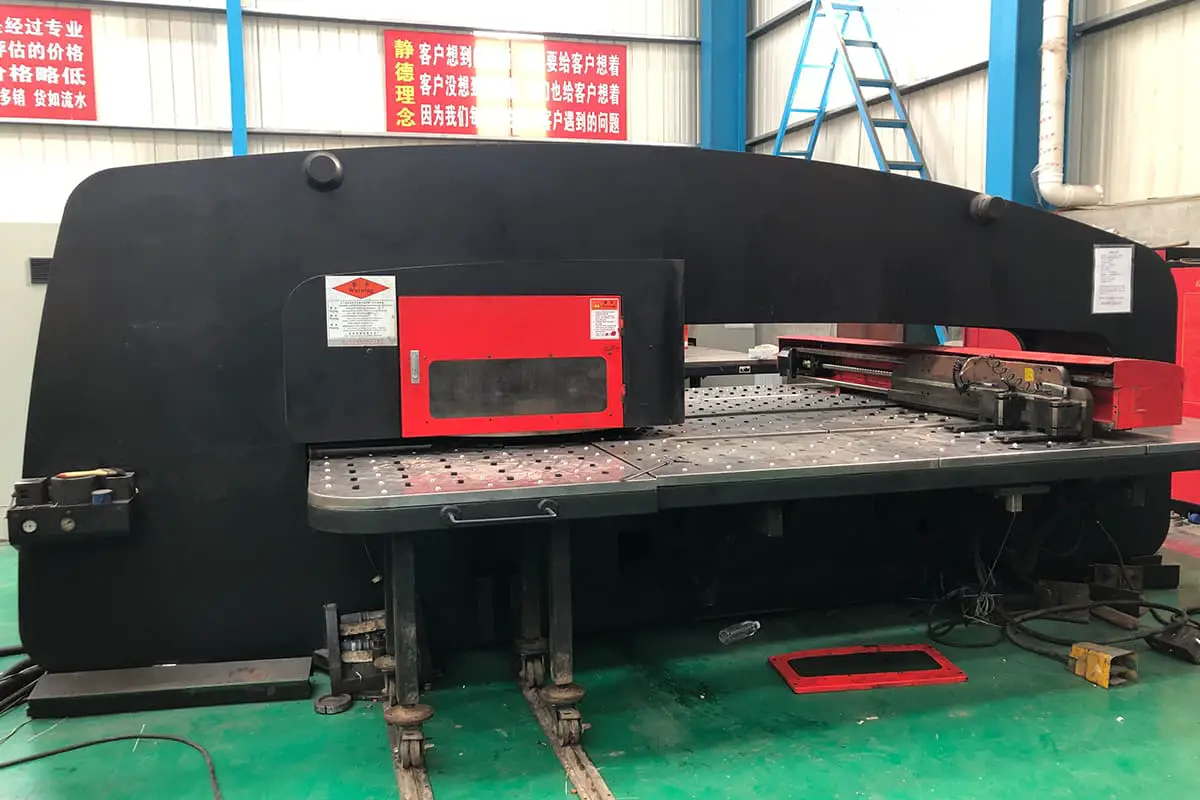
タレットパンチプレス開発の歴史
世界初のNCタレットパンチプレスは、アメリカのWIEDEMANN社(Wiedemann Machine Tools)が1955年のシカゴマシンショーで発表したのが始まりである。1964年にはWIEDEMATIC Sシリーズ、1972年にはMACH2シリーズを発表し、いずれも当時の業界では先駆的な設備であった。Wiedemannとの技術提携により、日本の村田製作所(MURATEC)は1970年の日本国際工作機械見本市(JIMTOF)にS2550タレットパンチプレスを出展し、1972年以降、村田製作所の日本工場で生産されたタレットパンチプレスの販売を開始した。1989年、村田機械はヴィーデマン社を買収。
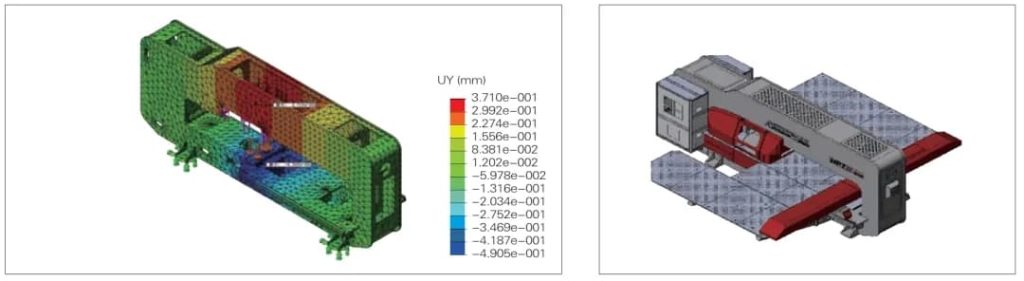
1970年代には、もうひとつのアメリカ企業、ストリッピット社(STRIPPIT)も大きな評判を得た。ストリッピットは、PCを使ってタレットパンチプレスのCNC制御を完成させた最初のメーカーであり、バネ式ダイツールの発明者としても知られている。社名のSTRIPPITは "STRIP IT "に由来する。1997年、ベルギーの有名企業LVD社がStrippit社を買収し、製品ラインナップを充実させ、北米でのビジネスを拡大した。
1980年代後半までに、中国市場に参入した最初の主要外国ブランドは日本のアマダ(AMADA)であった。1990年代初頭には、アマダ、村田製作所、アメリカのストリッピットの3社が中国市場で最も著名で活発なタレットパンチプレスサプライヤーであり、特に配電盤と通信盤の分野を独占していた。フィンランドのFinn-Power(FINNPOWER)とドイツのTrumpf(TRUMPF)(ノンタレットパンチプレス)が中国での販売活動を強化し始め、徐々に市場シェアを獲得したのは1990年代後半になってからである。
過去10年間で、レーザー切断機の急速な発展、レーザー切断コストの大幅な削減、レーザー切断技術の向上があった。 切断速度 と精度の高さから、レーザー切断機が広く採用されるようになった。これはCNCパンチプレス市場に直接影響を与えている。スタンピング工程を置き換えることができる特定の精密打抜き用途では、レーザー切断機には明確な利点がある。
しかし、特に電源キャビネット、通信キャビネット、制御キャビネット、空調キャビネット、エレベータ部品、厨房機器、カーテンウォールパネルなどの製造において、複合成形、パンチング、ブランキングを必要とする工程では、CNCパンチプレスは代替できない存在であり続けている。CNCパンチプレスは、これらの分野で不可欠な加工設備であり続けている。
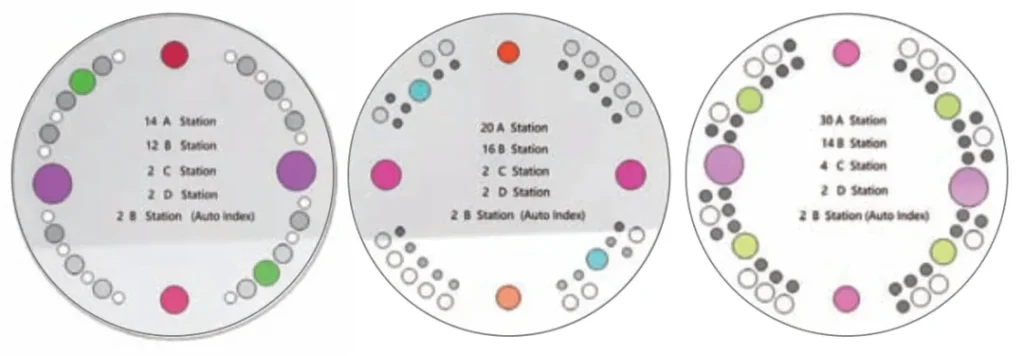
第一章 CNCタレットパンチの用途と産業
学習要件:
CNCタレットパンチの基本概念を理解する;
CNCタレットパンチの加工目的と主要メーカーを理解する。
1.1 CNCタレットパンチの定義
CNCタレットパンチプレスは、1955年にアメリカのウィードマン社によって正式に発表され、板金業界に新たな発展段階をもたらした。
初期の段階では、大きなサイズのシートの加工には、穴あけや振動のために手動マーキング穴あけ機が一般的に使用される。 剪断.
加工穴の寸法精度に対する要求が高い企業は、大トン数の複数セットを特別に注文する。 ディープスロートパンチ 様々な対応する位置決めとスタンピング加工を達成するために、スタンピング金型を一致させることは、加工範囲と加工精度を著しく制限する。
加工の形状や位置に応じて、CNCパンチは自動的に金型を変更し、自動的かつ正確に供給し、加工を完了することができます。
その加工効率と精度は、通常のディープスロートパンチとは明らかに違う。
現代の 板金加工CNCパンチは重要な加工設備である。
薄板(板厚0.5~6.35)の打ち抜き・浅延伸加工(延伸後のA・Bステーションの突き出し高さは6.35、C・Dステーションの突き出し高さは9.27以内)については、プログラムに従い、全サイズの板を1回で加工し、要求に対応することができる。
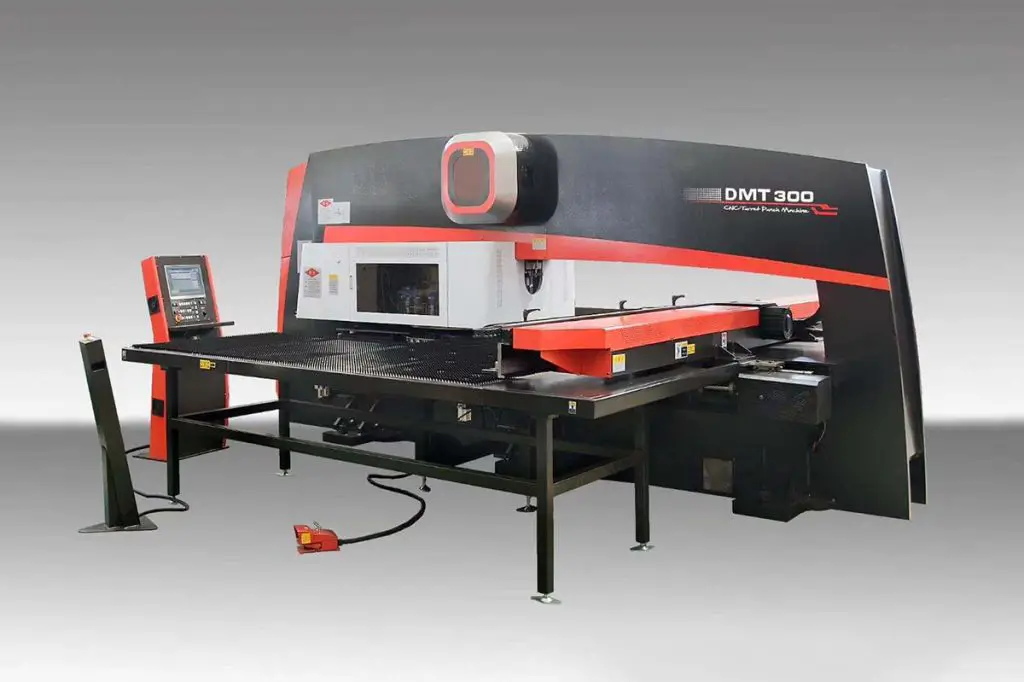
1.2 CNCタレットパンチのプロセスアプリケーション
CNCタレットパンチは、主にパンチング、浅絞り、スタンピングに使用されます。
シャローストレッチ機能は、丸ボス抜き、穴周りフランジング、パンチルーバー、ブリッジ穴、ノックダウン穴、ステップパンチルーバー、ステップパンチリブ、ロールリブ、ローリングシャー、ローリングステップ、パンチングヒンジ(2ダイアセンブリ、パンチング3回)に使用されます。
インプリント機能: マーキング、スタンプ、文字、彫刻。
1.3 数値制御パンチの応用産業
CNCパンチは、主に電気キャビネット(高・低電圧スイッチ、電気、電力、電子機器業界)、工作機械カバー板金業界、エレベーター、鉄道機関車、自動車ボックス、繊維機械、厨房機器、洗濯機器、コンテナ、金属構造物、金属製品、熱供給、照明、空調、冷凍庫などの家電業界、太陽熱温水器業界、貯蔵設備、軽工業アクセサリー、ハードウェア生産、壁カーテン生産、装飾業界などで使用されています。
1.4 CNCタレットパンチプレス産業の発展状況
1.4.1 市場の需要
現在、CNCタレットパンチの利用価値は市場で広く認知されている。
市場の需要は、特に国内市場において緩やかな成長傾向を示している。
近年、国内の年間需要は2000セット以上に達し、市場の需要は明らかに急成長期に入っている。
1.4.2 国内外のタレットパンチメーカー
現在、他の国内CNCタレットパンチメーカーは主に以下の通りである:JFY、Yangli、Jinan Jiemai、Guangdong LFK、台湾のTailift、Huangshiの合弁会社LVD;
また、徐州鍛造、無錫鍛造、中龍精密機械、済南恵利、広東大同、丹陽五徳精密機械などの生産量の少ないメーカーもある。
海外の先進的なタレットパンチ企業には、主に日本のアマダや村田製作所、フィンランドのプライムパワー社、ドイツのトランプフ社などがある。
外国企業の早期参入と急速な発展により、従来の油圧システムは廃止され、より省エネで環境に優しい機械式サーボスタンピングシステムが採用された。
1.5 CNCタレットパンチ産業の今後の発展
時代の発展と技術水準の向上により、板金加工の手段はパンチだけにとどまらない。
近年、CNC レーザー切断機 が徐々に姿を現し始めた。
業界はまた、レーザーの高速開発がパンチの将来の発展を制限することを懸念している。
以下、2つの製品の特徴を分析してみよう:
CNCタレットパンチの主な特徴は、複雑な成形加工を行うことができることであり、電子機器産業、工作機械シールド板金産業、ドア産業など、板金成形に対する要求が高い企業に適している。
レーザーと比較すると、同様の加工効率を持つCNCパンチは機械全体の約3分の1のコストしかかからず、その後のメンテナンスコストも低く、費用対効果が高い。
NCパンチダイスタンピングの使用コストは、NCパンチダイスタンピングの使用コストよりもはるかに低い。 レーザー切断 窒素や酸素を消費するマシン。
レーザーの主な利点は、金型のサイズに制限されない、不規則な形状のあらゆる種類の小さな間隔の部品を加工することができ、頻繁に金型を変更する必要がないことです。スピードも速い。
数値制御パンチと比べ、厚板の加工が可能。
振り返りの質問
1.CNCタレットパンチの加工用途は?
2.CNCタレットパンチの応用範囲
3.CNCタレットパンチの主なメーカーは?
4.CNCタレットパンチとCNCレーザー切断機の利点と欠点?
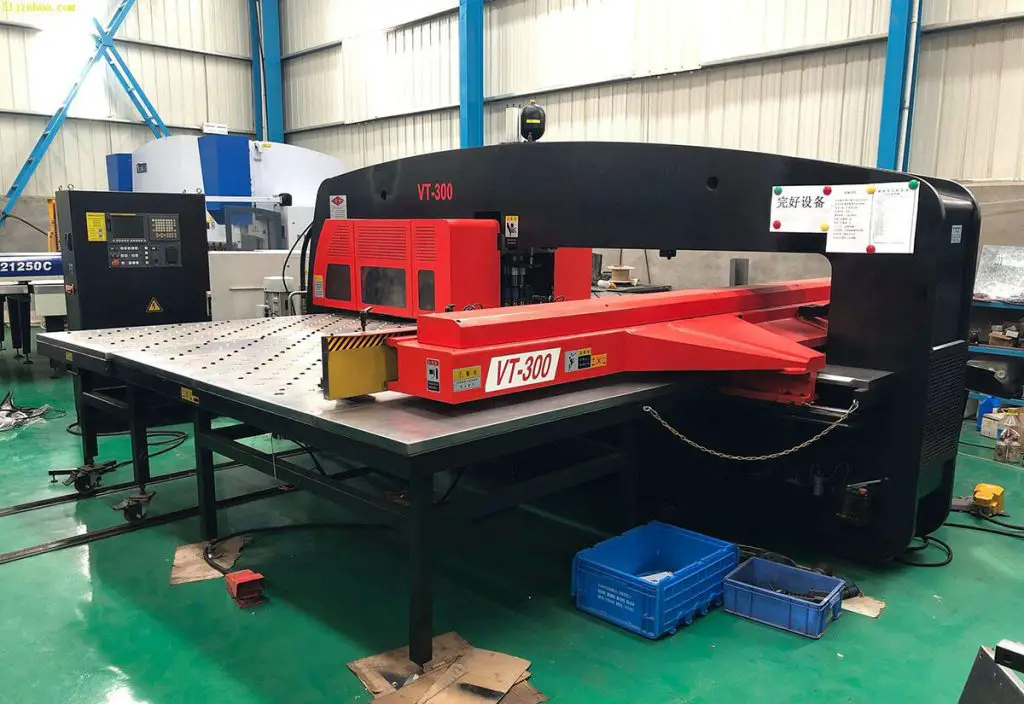
第2章 CNCタレットパンチの主なスタンピング構造と切断原理
学習要件:
CNCタレットパンチのいくつかのスタンピングタイプを理解する;
CNCタレットパンチの打ち抜き工程を理解する;
CNCタレットパンチの主な技術パラメータを理解する。
2.1 CNCタレットパンチの3つの主なスタンピング構造
フライホイール、クランクシャフト、コネクティングロッドの伝統的な機械式スタンピングメインドライブは、構造が簡単で、メンテナンスと修理が便利で、耐用年数が長く、コストが低いという利点がある。
欠点は、効率が低いこと、スタンピングの動きが調整可能なこと、アプリケーションの機能が少ないことである。 プレス加工スタンピング時の騒音とエネルギー消費が大きい。
高速油圧メインドライブの利点は、異なるスタンピングプロセスに応じて異なるスタンピングモーションモードを選択することができ、省エネ、高効率、フルストローク全負荷高速スタンピングです。
欠点は、制御構造が複雑で、同じ寿命でも使用とメンテナンスのコストが高いことだ。
スタンピング用メカニカルサーボメインドライブの利点は、高効率、省エネ、環境保護、低騒音です。
異なるスタンピング動作モードを選択することができます。 プレス加工メンテナンスが簡単で、維持費が安い。
2.2 パンチング原理と精度分析
打ち抜き工程には主に、押し出し、変形、分割、分離が含まれる。
上下のダイスの同心度は、エッジクリアランスとダイス寿命に影響する。
現在、同社は高精度の金型校正ツールにより、上下金型の同芯度誤差を0.02mm以内に管理している。
必要な処理圧力:
- (kN)=金型外周寸法(mm)×板厚(mm)×引張強さ(kN/mm2)
- (tonf)=金型外周寸法(mm)×板厚(mm)×引張強さ(kgf/mm)2)/1000
引張強度の値は以下の通りである(30%の安全係数が含まれており、以下は引張強度に従って計算されており、実際のせん断強度を使用すること):
- ソフトアルミニウム:0.196kN/mm2(20kgf/mm2)
- ジュラルミン:0.490kN/mm2(50kgf/mm2)
- 炭素鋼:0.490kN/mm2(50kgf/mm2)
- ステンレススチール:0.735kN/mm2(75kgf/mm2)
2.3 CNCタレットパンチの主要技術パラメータの構成
プレス公称トン数
HPH、HPI、HPQ、HPC、HIQの標準インパルス圧は30tで、HPHは50tモデルを装備できる。
パンチ速度周波数
HPHインパルス周波数は600回/分、HPIインパルス周波数は1000回/分、HPQインパルス周波数は1750回/分、HPCインパルス周波数は3800回/分、HIQインパルス周波数は1500回/分である。
1mmステップ、6mmストロークの作業速度周波数
HPHインパルス周波数320回/分、HPIインパルス周波数530回/分、HPQインパルス周波数690回/分、HPCインパルス周波数700回/分、HIQインパルス周波数750回/分。
25.4mmステップ距離、6mmストローク動作速度周波数
HPHインパルス周波数は230回/分、HPIインパルス周波数は295回/分、HPQインパルス周波数は330回/分、HPCインパルス周波数は350回/分、HIQインパルス周波数は350回/分である。
X軸とY軸の1回の送りストローク
X軸の一回の最大送りストロークは2500mm、Y軸の一回の最大送りストロークは1250mm;
最大送り速度は102m/min;
タレットモジュールの数、回転モジュールの仕様と数量
各モデルには26、30、36、40、56ステーションが標準装備されている。
このうち、26と36はBステーション回転ステーション2台を標準装備、30はDステーション回転ステーション6台を標準装備、40はDステーション回転ステーション2台を標準装備、56はB/Dステーション回転ステーション2台を標準装備している。
パンチングの精度: ブラシ作業台は±0.15、スチールボール作業台は±0.1。
最大加工直径: φ 88.9mm
回転テーブルの最高回転速度: 30r/min。
振り返りの質問
1 CNCタレットパンチにはどのようなスタンピング構造がありますか?
2.CNCタレットパンチの技術パラメータは何ですか?
3.計算 パンチ力 CNCタレットパンチの?
第三章 CNCタレットパンチの主な構造
学習要件:
CNCタレットパンチの主要構造を理解する;
CNCタレットパンチの各構造細分化タイプを理解する。
3.1 ラック
フレームは工作機械の様々な部品のキャリアであり、主にクローズドタイプとオープンタイプの2種類に分けられ、どちらも鋼板溶接構造である。
クローズドフレームはコンパクトな構造で、安定性があり、高い強度と剛性を備えている;
オープンフレームは操作の開放性がよく、加工も便利だが、溶接構造と溶接応力の校正に高い要求がある;
CNCタレットパンチのフレームが溶接された後、内部応力を除去するために高温焼戻しが行われる。
輸入したスペインのDANOBAT社製大型4軸マシニングセンタでは、重要な面の高精度加工を一度に完了し、工作機械本体の性能の安定性を確保している。
3.2 クロスビーム
クロスビームは、トランスミッション・コンポーネントの中で最も重要な部分であり、給送精度制御のためのマトリックスである。
X軸リードスクリュー、モーター、リニアガイドレール、板金保持用クランプ、クランプ固定用X軸スライドプレートなどをビームに取り付ける。
ビームは十分な剛性を持ち、Y軸の駆動負荷が過大にならないよう、また速度が低下しないよう、可能な限り慣性モーメントを小さくしなければならない。
その構造が合理的かどうかは、工作機械の送り精度や速度、安定性に直接影響し、高い技術的要求がある。
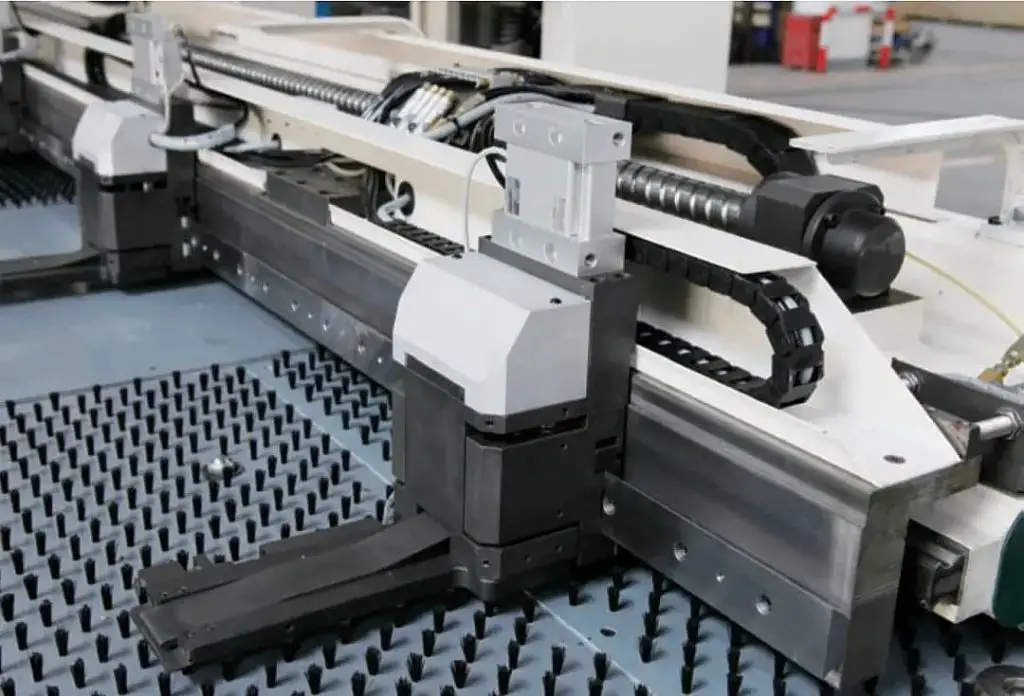
3.3 回転テーブル
タレットは工作機械の中核部品の一つでもある。その精度は金型の位置決め精度に直接影響し、工作機械の加工精度と金型の寿命に影響を与えます。
主に細い砲塔と太い砲塔に分けられる。
薄型ターレットは、コストが安く、剛性が低く、ガイド性能に劣り、通常の炭素鋼の加工変形が大きい。
厚いタレットは剛性が高く、誘導性能がよく、作業振動を吸収することができ、高級合金鋳鉄の高精度と安定性があり、高速ステップパンチと金型の偏心荷重処理の耐用年数が長く、使用中の変形が小さい。
現在は、上段ターンテーブル100mm、下段ターンテーブル90mmという分厚いターレット構造を採用している。
3.4 モジュールの回転位置
顧客の製品は複雑で変化しやすく、要求はますます高くなっている。
CNCタレットパンチの回転テーブルには、顧客のニーズを満たす回転ダイポジションが装備されていなければならない。
回転金型位置の金型は、必要に応じて必要な角度に回転させることができ、スタンピングに必要なトリミング角度も可能です。
加工にローラーダイスを使用する場合は、供給システムと連携して転造方向角度をリアルタイムで調整し、システムによって設定された転造経路に従って操作する。
回転工具の種類は次のように分けられる:
コンスタント・メッシュ構造で、精度が高く、ステーションがずれにくいという利点があるが、拡張性に乏しい。
分割された回転構造は、実際に使用されるときに駆動装置によって係合される。
この構造は高い組み立て精度と加工精度を必要とするが、拡張性に優れている。
例えば、プリマパワーのタレットには10個の回転ステーションがある。
3.5 クランプ
クランプは板金をクランプし、自動で正確な送り加工を行うための重要な部品です。
供給精度と速度を確保するため、クランプは十分な強度と全体的な取り付け剛性を持ち、自重はできるだけ軽くなければならない。
現在、クランプはその構造と機能によって以下の項目に分けられる:
クランプのフローティング機能は、主にプレートの適切な変形によって引き起こされるクランプ口の高さ変化に対処するために使用されます。
種類は以下の通り:
スイングクランプは軽量、長寿命、フレキシブルなフローティングという利点がある。
並進型クランプのY方向の爪の大きさは、理論上、上下に浮いた状態でも変わらないものとする。
クランプ機能は主にプレートのクランプに使用されます。
種類は以下の通り:
油圧クランプ、不便なメンテナンス、大きなクランプ力、ストリップするのは簡単ではありません。
空気圧クランプ、省エネ、環境保護、簡単なインストール。
クランプ位置の調整機能は、主にクランプを所定の位置に移動させるために使用します。
種類は以下の通り:
異なるワークピースのプレートには、CNCタレットパンチの前でクランプの位置と間隔を移動して調整する必要があります。
手動クランプの場合は、ハンドルを引いてロック装置を解除し、クランプを必要な位置まで押し、ハンドルを引いて調整を完了します。
自動クランプ: 調整中、加工プログラムで各クランプの位置を設定すると、工作機械は各クランプをクランププレートの前の必要な位置に自動的に調整します。
3.6 CNCタレットパンチの安全保護システム
CNCタレットパンチは近代的な 板金加工設備 高速、高精度、高自動化。
自動化された効率的な処理の信頼性を確保し、装置運転中のオペレーターと装置の安全を確保する。
CNCタレットパンチは、安全保護システムを構成する一連の安全保護装置を持っています。
脱型検知装置、クランプ剥離検知装置、シールド連動安全装置、可動式作業台連動安全装置、クランプ死角保護装置、クランプ衝撃検知装置、プレート過大変形検知装置など。
3.6.1 脱型検知装置
高速連続スタンピングの過程で、上型が金型に突き刺さった。 板金 そして、時折スムーズかつタイムリーにリセットすることができなかった。
工作機械が次のステップで動き続けると、材料の衝突、材料の持ち運び、クランプの金型への衝突などの安全事故が発生する可能性がある。
脱型検知装置は、上型のタイムリーなリセットを効果的に監視することができる。
スタンピング後、上型が時間内にリセットされないことを検出すると、装置はシステム停止アラームを作動させる。
こうして、その後の安全事故を回避することができる。
3.6.2 クランプ剥離検出装置
連続プレスの工程では、廃材のはね返りによって板が動かなくなることがある。
クランプがプレートを引き戻し続けると、クランプの1つまたはすべてが引き抜かれる。
クランプが外れた後、工作機械が次の工程で作業を続けると、材料の衝突や誤った位置でのスタンピングなどの事故が発生する。
クランプ剥離検出装置はクランプ剥離現象を効果的に監視することができます。一旦剥離が発生すると、この装置はシステムのシャットダウンアラームを作動させます。
こうして、その後の安全事故を回避することができる。
3.6.3 シールドと可動式作業台のインターロック安全装置
工作機械の自動加工中に、操作のためにシールドや可動作業台を開けると、人身事故が発生する恐れがあります。
そのため、工作機械の可動シールドと可動作業台には、インターロック式の安全装置が装備されている。
工作機械の自動加工中にシールドが開かれたり、可動作業台が手動で開かれたりすると、インターロック装置がシステムのシャットダウンアラームを作動させる。
こうして、その後の安全事故を回避することができる。
3.6.4 クランプ不感帯保護装置
クランプがシートメタルをクランプする位置(クランプデッドゾーンと呼ばれる)またはその付近で、必要なスタンピング加工が行われる場合があります。
対応する保護措置がない場合、加工中に金型がクランプに打ち抜かれ、金型やクランプの一部が損傷する。
クランプデッドゾーン保護装置は、このような状況に対応する自動保護装置である。
一組の誘導スイッチ(異なるサイズの金型は異なる誘導スイッチに対応)を通して、クランプがデッドゾーンに入り、工作機械の自動処理中に押し付け命令があると、保護装置はシステムシャットダウンアラームを作動させます。
こうして、その後の安全事故を回避することができる。
3.6.5 シートメタルの過度の変形の検出装置
クランプで板金を押さえながら連続プレスする工程では、廃材のはね返りによって板金が動かなくなることがある。
次に、クランプが板金を押し続けると、板金はジャッキで押されて変形する;
ワークブランクに過大な変形がある場合(総反り高さが20mmに達した場合)、タレットに送り込む際にタレットに衝突する。
クランプ衝撃と過度の変形検出装置は、シートの過度の変形に対して適時にシステム停止アラームを作動させることができます。
こうして、その後の安全事故を回避することができる。
3.7 CNCタレットの駆動モード パンチ
現在、主流製品の砲塔には主に2つの駆動モードがある:
この種の構造は、モーター駆動の減速機を介してチェーン駆動のタレットを駆動する。
構造は比較的信頼できるが、音が大きく、緩みやすいので定期的な調整が必要という欠点がある。
同期ベルトドライブ
現在、同期ベルト伝動にこの構造を採用している企業は多くない。
作動音は小さく、同期ベルトにかかる力は大きく、長期間使用すると歯が変形しやすい。
3.8 CNCタレットパンチの供給システム
CNCタレットパンチの送り装置、特にロングストロークの安定性と精度を確保することは非常に重要である。
現在、主要メーカーが採用している給餌形態は以下の通り:
3.8.1 ボールねじ駆動特性
ボールねじ駆動は、最も一般的な供給構造である。ボールねじのペアのボールねじシャフトとスクリューナットの間に転がる多くのボールがあります。
走行抵抗が小さいので、高い運動効率を得ることができる。成熟した処理システムが高精度を保証する。
サイドクリアランスなし、高剛性、高速供給、低加熱。
その欠点は、加工コストが高いことと、ベアリング容量が小さいことである。
さらに、コスト削減のために精密転造ボールねじを使用する企業も出てきた。
しかし、精度が低いため、実用上、断面パラメータ補正が必要となり、製品品質の安定制御が難しい。
3.8.2 ギアラックの特性
近年、ギアラックはますます広く使われるようになっている。
その利点は、負荷が大きく、伝達速度が速く、価格が安く、加工が容易なことにある。
その欠点は、設置条件が高いことにある。
加工や取り付けの精度が悪いと、摩耗やノイズの原因になりやすい。
3.9 CNCタレットパンチテーブル
CNCパンチプレスの作業台は次のように分けられる:
固定作業台、セミサーボ作業台、フルサーボ作業台。
機能によって、ブラシ作業台と鋼球作業台に分けられる。
実際の打ち抜き精度は、ブラシテーブルの摩擦抵抗が大きいため0.15mm、スチールボールテーブルの場合は0.1mmである。
3.10 CNCタレットパンチCNCオペレーティングシステム
現在、CNCタレットパンチシステムは主に以下の通りである:
- 日本ファナックCNCシステム;
- ドイツ製SIEMENS CNCシステム;
- レックスロスMTX CNCシステム。
さらに、スペインのFAGOR CNCシステム、日清繊維パンチCNCシステムなど、パンチプレス業界ではあまり使用されないCNCシステムもある。
3.11 CNCタレットパンチ油圧システムのタイプ
CNC用油圧システム パンチングマシン は2つのカテゴリーに分けられる:
ひとつは、大流量可変ポンプとサーボバルブで主油回路を制御し、数値制御システムでパンチの動きをプログラム制御するダイレクト・サーボ油圧システムである;
ダイレクトサーボ油圧システムの特徴
メリット
CNCシステムは、柔軟で多様な制御方法で、パンチのパンチ動作モードを直接制御します。
最大パンチ力はユーザープログラムでも設定できる。
デメリット
高いエネルギー消費、高いコスト、高い作動油の品質要求、高いユーザーのメンテナンスと後期の使用コスト、定期的な油交換とメンテナンス時のわずかな油汚染に起因するサーボバルブの制御不能の重大な故障(サーボバルブの交換にかかるコストが高い)。
もう1つのタイプは、油の供給に高圧および低圧の複式ポンプを使用する間接サービス油圧システムである。
高圧と低圧のデュアル・オイル回路には、ラムの動きを調整・制御する高速反転バルブがある。
油圧システムには専用の高速サーボ制御回路ユニットがある。
CNCシステムはラムの動作モードを選択し、油圧システムに関連するパラメータを入力する。
間接サーボ油圧システムの特徴
メリット
高効率、省エネ、簡単な制御、経済性、信頼性、耐久性、便利なメンテナンス;
デメリット
運転中の最大インパルス圧はプログラムで設定・調整できません。
現在、同社が主に使用している油圧システムは、ドイツのハーレー社製の油圧パンチシステムであり、対応するモデルは以下の通りである:
- HPHシリーズ - ECO油圧システム、オイルタンク容量180L;
- HPIシリーズ - HKL油圧システム、オイルタンク容量200L;
- HPQシリーズ - HRE油圧システム、オイルタンク容量275L;
- HPCシリーズ - HPPC油圧システム、オイルタンク容量275L;
- HIQシリーズ - 日新油圧システム、オイルタンク容量350L。
中でもECOは、ドイツ・ハレー社の低級油圧システムを採用し、6mmストロークの動作回数は毎分600回;
HKLは、ドイツHalley社の中・高級サーボ油圧システムを採用し、高精度(最大±0.2mm)、高精度スローフォーミング機能、高精度ローリング機能、5mmストローク動作頻度毎分1000回を備えています;
HREはドイツHalleyのハイエンドのサーボ油圧システムを採用し、パンチの動きの複数の制御モードを持つ 高精度(± 0.1mmを圧延することができる)、制御モードで多くの制御可能なパラメータ(速度も制御することができる)、およびマーキング周波数は毎分1750回に達することができます。
HPPCは、ハレー社が発売した最もハイエンドの油圧サーボシステムで、他のシステムの長所をすべて兼ね備えており、毎分3800回のマーキング速度が大幅に向上している。
Haley油圧システムにはMobil ATF220摩耗防止油圧オイルが、HIQ洗浄システムにはMobil DTE25摩耗防止油圧オイルが使用されている。
HPH、HPI、HPQ、HPC、HIQシリーズ油圧パンチの打ち抜きトン数は30t、HBL油圧パンチの打ち抜き圧力は50tである。
3.12 CNCタレットパンチのモデルコードの意味
各工作機械コードには固有の意味がある。
例えば、現在の工作機械コードHPI-3048-40LA2は、30はパンチングトン数30トン(20は20トン)、4はY軸移動量1250mm(5は1500mm)、8はX軸ライン2500mm、40は40ステーションのタレット、Lはロングダイ、A2はマシンが2つのロータリーダイを装備していることを表しています。
振り返りの質問
1 CNCタレットパンチの主な構成部品は何ですか?
2.CNCタレットパンチに主に使用されるCNCシステムは?
3.Yawei CNCタレットパンチのいくつかのモデルに対応する油圧システム?
第四章 CNCタレットパンチの金型
4.1 CNCタレットパンチ金型は次のように分けられる:
ガイドによって、ロングガイドダイとショートガイドダイに分けられる;
リセットタイプ:スプリングリセット金型と強制リセット金型;
内部構造によって、一体型とモジュール型に分けられる;
サイズと仕様に応じて:A、B、C、D、E駅金型;
プロセス使用に従って: 打つこと、形作ること、圧延および他の型;
サービス性能によって、通常の金型、耐摩耗コーティング金型、アンチストリップ金型に分けることができます;
刃先の形状によって、平刃型と傾斜刃型に分けられる;
金型コアの数によって、シングルパンチ金型、マルチサブ金型、マルチホール金型に分けられる。
4.2 金型は構造によって分けられる:
標準構造(E85シリーズ);
クイックチェンジ構造(S90シリーズ);
重荷重構造(AおよびBステーションで2.5mm以上のステンレス鋼、3.5mm以上の冷延鋼板、4.5mm以上のアルミニウム鋼板)。
4.3 ダイパンチ構造の分割:
平らなエッジ;
傾斜したカッティングエッジ(ルーフ構造);
内側に凹んだ刃先;
内側に面取りされたエッジ。
4.4 金型材料の特性
ダイスは主に高速度工具鋼SKHとM2で作られており、冷間圧延板、アルミニウム板、ステンレス鋼板に適用され、合金鋼よりも硬い。
合金工具鋼SKDとD2は、主に材料コストの低い冷間圧延板とアルミニウム板に適用されます。
硬度: 変形防止能力を反映している;
タフネス: 耐衝撃性を反映している;
耐摩耗性: 耐摩耗性と耐食性を反映している。
4.5 ダイクリアランスの選択
最適の利点 ダイ・クリアランス 金型寿命の延長、良好なアンロード効果、バリやフランジングの低減、研削時間の短縮などである。
クリアランスが小さすぎる: パンチ圧力が上昇すると、パンチと下型との摩耗が促進され、金型の寿命が短くなる;
過剰なクリアランス: バリが大きく、パンチの質が悪い;
クリアランスが大きすぎたり小さすぎたりすると、パンチの刃先に粘りが出やすくなり、ストリップの原因となる。
代表的な板厚とクリアランスを下表に示す。
厚さ | 1.0 | 2.0 | 2.5 | 3.0 | 3.5 | 4.0 | 4.5 | 5.0 | 6.0 |
アルミニウム板 | 0.15 | 0.3 | 0.38 | 0.45 | 0.6 | 0.7 | 0.8 | 1.0 | 1.2 |
冷間圧延シート | 0.2 | 0.4 | 0.5 | 0.7 | 0.85 | 1.0 | 1.1 | 1.25 | 1.5 |
ステンレス鋼 | 0.25 | 0.55 | 0.65 | 0.9 | 1.05 | 1.2 | 1.35 |
4.6 金型オーダーの3要素
加工形状、板厚、加工材料。
4.7 金型研削の注意事項
ダイの刃先Rが0.1mmになったら、パンチと下型を研磨する。
切断量は0.013mm以下;
ダイエッジのRは0.25mmを超えないようにすべきであり、そうでなければ厳しい摩耗段階に入る;
パンチの焼きなましを防ぐための十分な冷却;
研削後は清掃、消磁、潤滑を行う;
シムは下型を研いだ後に追加する。
振り返りの質問
1.NCタレットパンチ金型はいくつの構造を持っていますか?
2.選択方法 ダイ・クリアランス CNCタレットパンチの?
3.CNCタレットパンチ金型研削の注意事項?