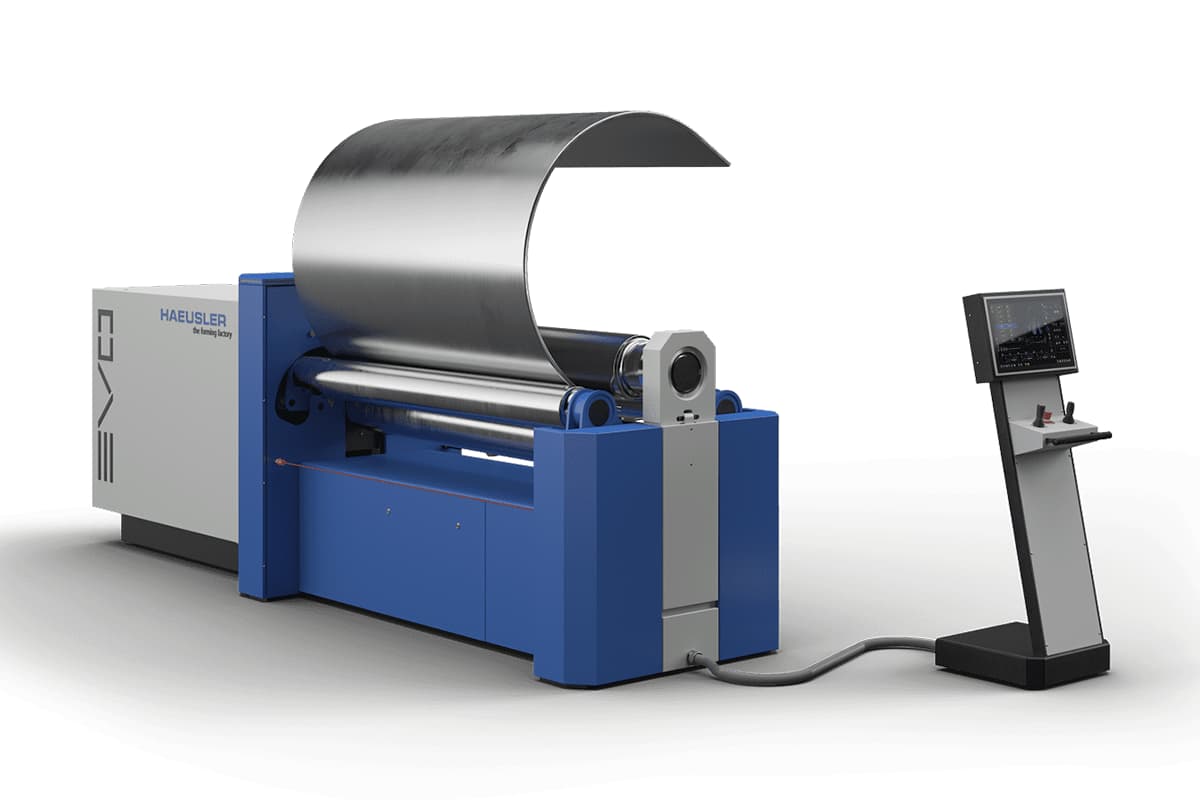
Soldadura
I. Princípios, características e âmbito de aplicação da soldadura por arco com metal blindado
1. Princípio da soldadura por arco com metal blindado
A soldadura por arco de metal blindado é um método básico de soldadura por fusão que utiliza a operação manual do elétrodo, utilizando o arco de soldadura gerado entre o elétrodo e a peça de trabalho para aquecer e fundir o metal de base ou o elétrodo no ponto de soldadura para formar um cordão de soldadura, como se mostra na Figura 7-1.
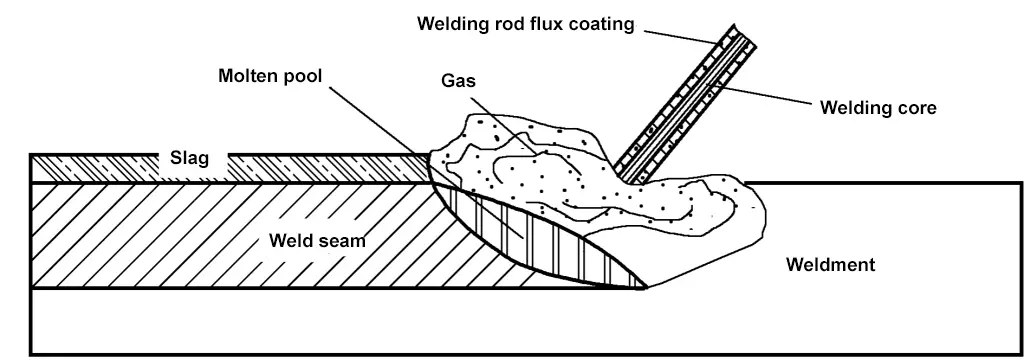
2. Características da soldadura por arco com metal blindado
1) O processo é flexível e altamente adaptável. Durante a soldadura, a operação manual pode controlar o comprimento do arco, o ângulo do elétrodo, a velocidade de soldadura, etc., adequado para vários materiais metálicos, espessuras, formas estruturais e posições.
2) É fácil dispersar a tensão de soldadura e controlar a deformação da soldadura alterando as operações do processo.
3) Em comparação com métodos como a soldadura com proteção gasosa e soldadura por arco submersoO equipamento é simples, a manutenção é cómoda e os custos de produção são mais baixos.
4) A baixa eficiência de produção, a elevada intensidade de trabalho e a qualidade da soldadura exigem um elevado nível de competência e experiência do operador.
3. Âmbito de aplicação da soldadura por arco com metal blindado
A soldadura por arco metálico blindado é amplamente utilizada em vários sectores da economia nacional. Pode ser utilizada para soldar aço-carbono, aço de baixa liga, aço resistente ao calor e aço inoxidável. Também é adequado para soldar aço de alta liga, ferro fundido, metais não ferrosos metaise para o revestimento de vários materiais metálicos.
II. Eléctrodos e princípios de seleção de eléctrodos
Um elétrodo é um material de soldadura revestido com fluxo para utilização na soldadura por arco metálico protegido. Durante a soldadura, o elétrodo desempenha duas funções: como elétrodo e como metal de adição, que se funde com o material de base para formar um cordão de soldadura.
Existem muitos tipos de eléctrodos, cada um com o seu âmbito de aplicação. A seleção adequada dos eléctrodos tem um impacto significativo na qualidade da soldadura, no custo do produto e na produtividade do trabalho. Os seguintes princípios devem ser seguidos ao selecionar os eléctrodos:
1) Selecionar com base nas propriedades mecânicas e na composição química do material de base. Ao soldar materiais de base como o aço de baixo carbono, o aço de médio carbono ou o aço de baixa liga comum, escolha um elétrodo com a resistência correspondente para garantir que o cordão de soldadura tem o mesmo desempenho que o material de base.
2) Para estruturas importantes que exijam elevada tenacidade e ductilidade no cordão de soldadura, ou para aço com elevada tendência para fissurar e elevada rigidez, escolher eléctrodos básicos, eléctrodos de elevada tenacidade, ou mesmo eléctrodos de hidrogénio ultra-baixo.
3) Ao selecionar eléctrodos para soldar aço inoxidável, molibdénio e aço resistente ao calor com crómio-molibdénio ou para revestimento, começar por garantir o desempenho especial da junta soldada, exigindo que a composição química e o tipo do metal de solda sejam iguais ou semelhantes ao material de base.
4) Para soldar juntas de metais dissimilares entre aço de baixo carbono e aço de baixa liga, escolher um elétrodo com um nível de resistência inferior.
4) Para soldar juntas de metais dissimilares entre aço de baixo carbono e aço de baixa liga, escolher um elétrodo com um nível de resistência inferior.
5) Selecionar os eléctrodos com base no equipamento existente e nas condições de construção. De preferência, utilizar eléctrodos adequados tanto para CA como para CC. Se a superfície biselada da peça de trabalho for difícil de limpar, utilizar eléctrodos ácidos que sejam fortemente oxidantes e insensíveis a manchas de ferrugem e óleo; em recipientes fechados ou em condições de fraca ventilação, utilizar eléctrodos ácidos que emitam menos gases nocivos durante a soldadura.
6) Considerar a resistência à fissuração do metal de solda. Quando a estrutura soldada tem elevada rigidez, grande espessura e forma complexa, utilizar eléctrodos básicos de baixo hidrogénio resistentes à fissuração.
7) Quando as peças soldadas estão sujeitas a cargas de vibração ou de impacto, além de garantir a resistência, utilizar eléctrodos de base com melhor plasticidade e tenacidade.
8) Ao selecionar com base em processos simplificados, produtividade e relação custo-eficácia, tente utilizar eléctrodos que produzam menos poeira e danos e que sejam baratos. Para peças soldadas com uma grande quantidade de trabalho de soldadura, utilize eléctrodos maiores e mais eficientes, tais como eléctrodos de aço inoxidável de alta eficiência e eléctrodos de gravidade, assegurando simultaneamente o desempenho da soldadura.
III. Classificação e medidas de prevenção da deformação residual da soldadura
O aquecimento desigual e a contração durante o processo de soldadura são as principais causas da tensão residual, e a tensão residual é a principal causa da deformação estrutural.
1. Classificação da deformação residual de soldadura
Na produção atual, a deformação das estruturas soldadas é bastante complexa. De acordo com o impacto da deformação residual da soldadura em toda a estrutura, esta pode ser dividida em duas categorias: uma é a deformação local, que ocorre em algumas partes da estrutura soldada, como mostra a Figura 7-2; a outra é a deformação global, que causa alterações na forma e no tamanho de toda a estrutura soldada, como mostra a Figura 7-3.
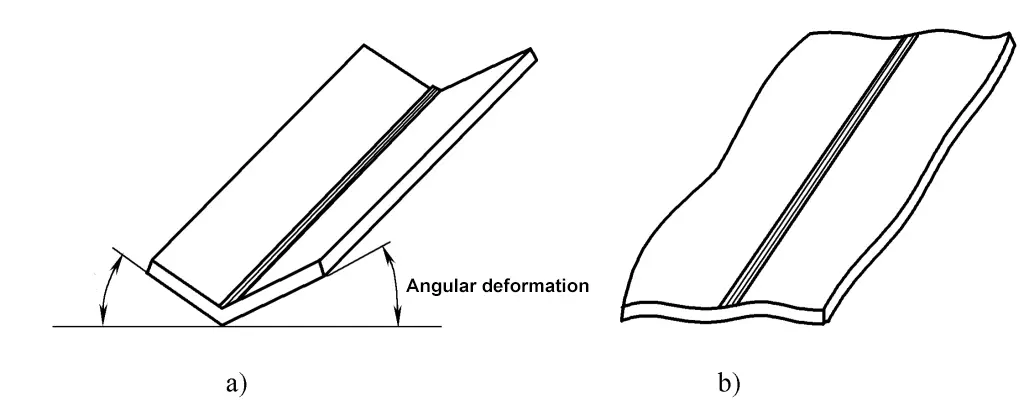
a) Deformação angular
b) Forma de bordo ondulado
De acordo com as características da deformação residual da soldadura, esta pode ser dividida em seis formas básicas de deformação: deformação por retração, deformação angular, deformação por flexão, deformação ondulada, deformação por torção e deformação por desalinhamento, como mostram as Figuras 7-2 e 7-3.
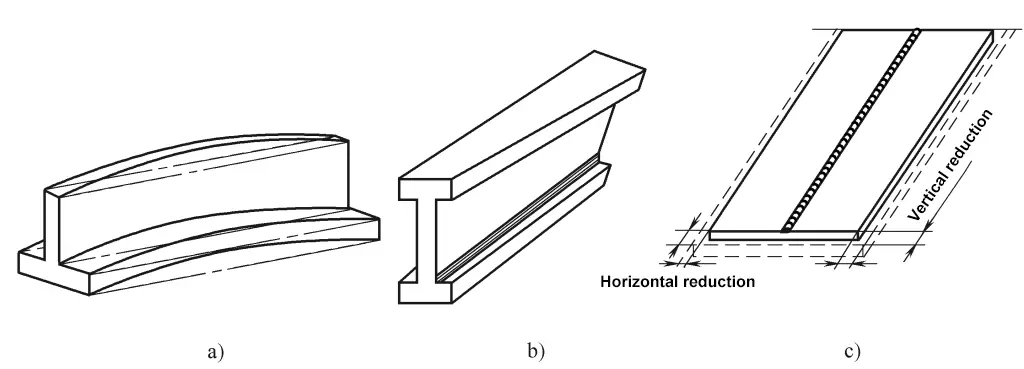
a) Deformação por flexão
b) Deformação por torção
c) Deformação por contração
2. Medidas para evitar a deformação residual da soldadura
Para controlar a deformação residual da soldadura, considere as seguintes medidas normalmente utilizadas numa perspetiva de processo:
(1) Utilizar uma sequência de soldadura de montagem razoável
1) Utilizar o método de soldadura simétrica para soldaduras simétricas
Uma vez que a soldadura tem sempre uma sequência, e à medida que o processo de soldadura avança, a rigidez da estrutura também aumenta. Por conseguinte, as soldaduras que são soldadas primeiro tendem a causar deformação da estrutura. Assim, mesmo que a estrutura das soldaduras seja simétrica, a deformação da soldadura ocorrerá após a soldadura. O objetivo da soldadura simétrica é superar ou reduzir a deformação causada pelo primeiro cordão de soldadura quando a rigidez da peça soldada é baixa.
2) Soldar primeiro o lado com menos costuras para soldaduras assimétricas
Para estruturas com soldaduras assimétricas, soldar primeiro o lado com menos cordões e depois o lado com mais cordões. Isto pode permitir que a deformação da última soldadura compense a deformação do lado soldado mais cedo, reduzindo a deformação global.
3) Utilizar diferentes sequências de soldadura para controlar a deformação da soldadura
Para soldaduras longas em estruturas, se for utilizada a soldadura contínua, esta causará uma deformação significativa. Isto não é apenas devido à direção da soldadura, mas também porque a soldadura é aquecida durante um longo período de tempo. Se possível, a mudança da soldadura contínua para a soldadura segmentada e a alteração adequada da direção de soldadura podem reduzir a deformação causada pelas soldaduras locais ou compensar-se mutuamente para atingir o objetivo de reduzir a deformação global. Como mostrado na Figura 7-4.
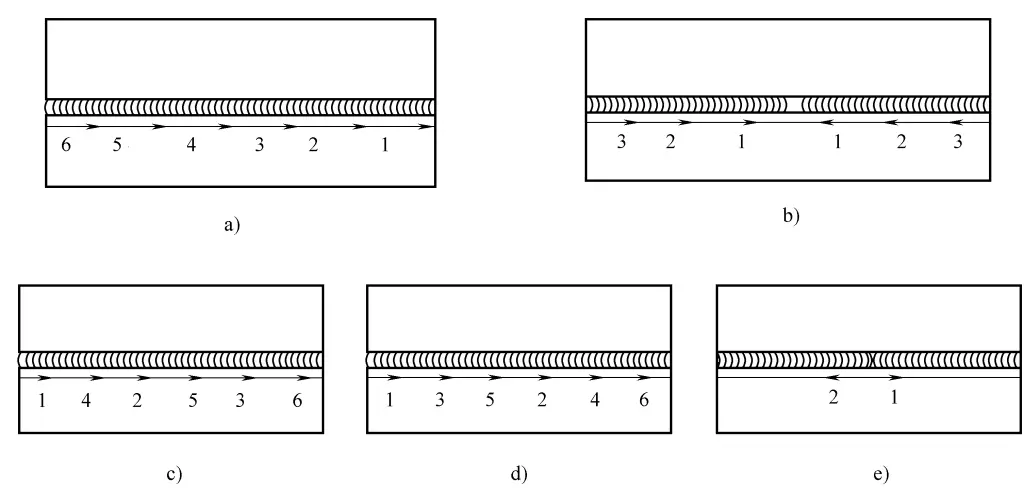
a) Método de soldadura por retrocesso
b) Método de soldadura por retrocesso central
c) Método de soldadura por saltos
d) Método de soldadura alternada
e) Método de soldadura topo a topo da secção intermédia
(2) Método de contra-deformação
De acordo com o padrão de deformação da soldadura, colocar artificialmente a soldadura numa deformação oposta à direção de deformação da soldadura com antecedência, a fim de alcançar o objetivo de contrariar a deformação da soldadura. Este método é chamado o método da contra-deformação (também conhecido como o método do subsídio reservado). A utilização deste método requer experiência na previsão da dimensão da contra-deformação, e o ângulo de flexão inversa deve ser controlado, nem demasiado pequeno nem demasiado grande. A soldadura topo a topo da ranhura em forma de Y mostrada na Figura 7-5 é um exemplo de controlo da deformação angular utilizando o método de contra-deformação.
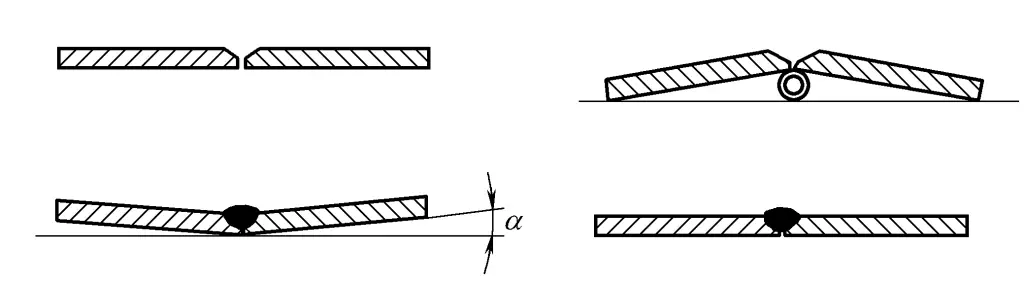
(3) Método de fixação rígida
A quantidade de deformação da soldadura depende da rigidez da estrutura; quanto maior for a rigidez, menor será a deformação causada após a soldadura, e a rigidez da estrutura depende principalmente da forma e do tamanho da estrutura. Em termos da capacidade da estrutura para resistir à tensão ou à compressão, a dimensão da rigidez está relacionada com a dimensão da área da secção transversal.
Quanto maior for a área da secção transversal, maior será a rigidez e maior será a capacidade de resistir à deformação. Por conseguinte, as chapas de aço grossas têm menos deformação após a soldadura do que as chapas de aço finas.
O método de fixação rígida consiste em utilizar medidas obrigatórias ou recorrer a dispositivos de fixação com grande rigidez para componentes que não têm rigidez suficiente, para limitar e reduzir o grau de deformação após a soldadura. Com este método, os dispositivos fixos só podem ser removidos depois de a soldadura ter arrefecido completamente. As Figuras 7-6 a 7-8 mostram exemplos de diferentes estruturas soldadas que utilizam o método de fixação rígida para reduzir a deformação da soldadura.
1) Utilizar objectos pesados para pressionar ou utilizar a soldadura por pontos para o posicionamento. Este método é adequado para a soldadura de placas finas, em que a soldadura por pontos é utilizada à volta da placa para a soldar firmemente à plataforma ou à estrutura, e são colocados objectos pesados em ambos os lados do cordão de soldadura. Após o cordão de soldadura ter arrefecido completamente, remover os objectos pesados, raspar os pontos de soldadura de aderência e atingir o objetivo de reduzir a deformação. Como se mostra na Figura 7-6.
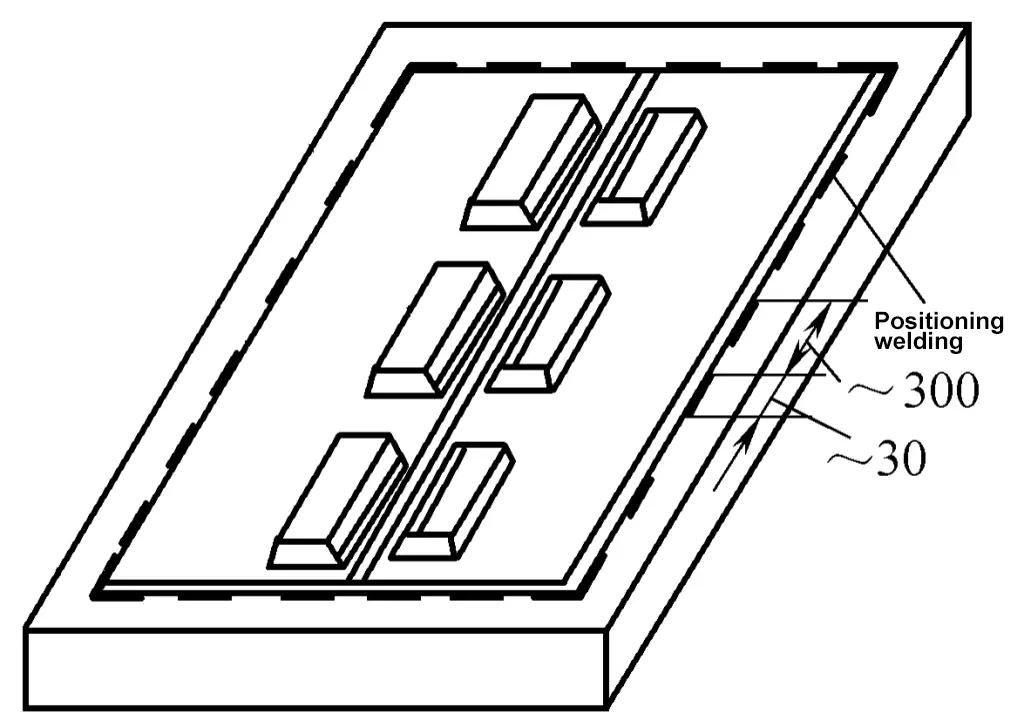
2) Utilizar dispositivos de fixação. Como mostra a Figura 7-7a, antes de soldar a viga em I, aparafusar firmemente as flanges na plataforma, utilizando a rigidez da plataforma para reduzir a deformação angular e a deformação por flexão após a soldadura.
Se as condições limitarem a utilização do método acima referido, pode também ser utilizado o método mostrado na Figura 7-7b, combinando duas vigas em I, utilizando grampos em cunha para apertar as duas flanges, aumentando a rigidez da estrutura em I para atingir o objetivo de reduzir a deformação após a soldadura. Este método também é normalmente utilizado na soldadura de montagem de bases, estruturas e outros componentes.
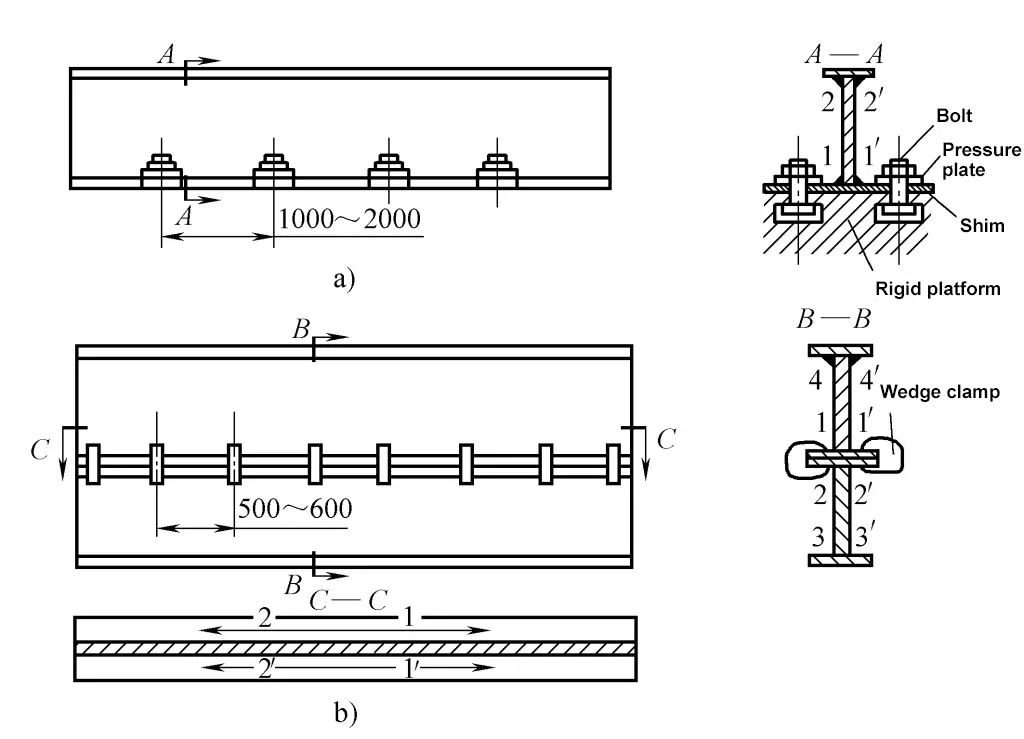
a) Uma viga em I
b) Combinação de duas vigas em I
3) Utilizar "cavalos de serra" ou suportes temporários para fixação. Na soldadura topo a topo de chapas de aço, o método de fixação com "cavalos de serra" também pode ser utilizado para controlar a deformação, que é um método simples e fiável amplamente utilizado na produção. Para pequenas soldaduras gerais, o método de fixação rígida com suportes temporários também pode ser utilizado, como mostra a Figura 7-8.
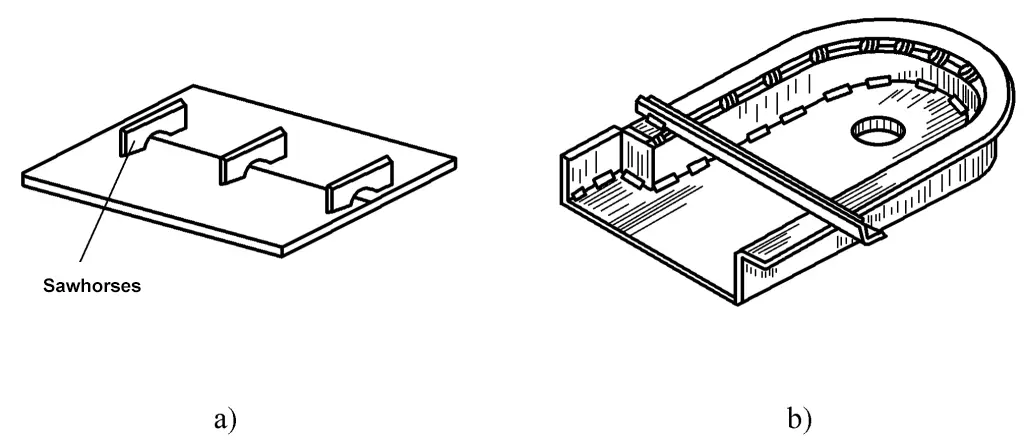
a) Método de fixação com "cavalinhos de serra"
b) Método de fixação com suportes temporários
É de notar que, embora a deformação da soldadura seja efetivamente controlada com a fixação rígida, devido às grandes restrições na estrutura, são geradas tensões internas significativas. Por conseguinte, a fixação rígida só é adequada para soldaduras com boa soldabilidade. Para aço de carbono médio e aço de liga com fraca soldabilidade, a fixação rígida não deve ser utilizada para soldar para evitar fissuras.
Além disso, a escolha de métodos de soldadura e os parâmetros também podem reduzir a deformação da soldadura. Por exemplo, a utilização de calor concentrado, zona afetada pelo calor estreita CO, soldadura com proteção gasosa, soldadura por arco de plasma em vez de soldadura a gás e soldadura por arco de metal protegido pode reduzir a deformação da soldadura; a utilização de parâmetros de soldadura mais pequenos para reduzir a entrada de calor também pode reduzir a deformação da soldadura.
Rebitagem
I. Princípios da rebitagem
A rebitagem é o método de ligação de duas ou mais peças do mesmo material ou de materiais diferentes, com orifícios para rebites, transformadas num todo através de ferramentas e equipamento de rebitagem, utilizando a deformação dos rebites à temperatura ambiente ou após aquecimento.
O fluxo de trabalho geral da rebitagem é o seguinte:
1) Utilizar a perfuração, o alargamento, a brocagem e o alargamento para processar os furos dos rebites nas peças de ligação.
2) De acordo com os requisitos de dimensão do desenho estrutural, selecionar a referência de montagem para o posicionamento das peças rebitadas.
3) Selecionar corretamente os rebites que satisfazem os requisitos técnicos.
4) Determinar o equipamento e as ferramentas de rebitagem.
5) Efetuar as operações de rebitagem de queima, de união, de roscagem e de remate.
6) Inspeção da qualidade da rebitagem.
A rebitagem apresenta um equipamento de processo simples, uma distribuição de tensões uniforme e fiável, uma deformação mínima após a montagem, uma elevada resistência, um controlo de qualidade fácil, uma inspeção conveniente, juntas que não são propensas a afrouxar, uma longa vida útil e facilidade de manutenção e inspeção. É uma ligação não destacável, normalmente utilizada em ligações que têm de suportar grandes cargas de impacto e cargas de vibração, fraca soldabilidade ou materiais não metálicos.
Com o desenvolvimento da tecnologia industrial, a rebitagem foi gradualmente substituída pela soldadura e pela colagem devido às suas desvantagens, tais como múltiplos processos, elevada intensidade de trabalho, elevado ruído e baixa eficiência de trabalho, mas continua a ser amplamente utilizada em sectores como o automóvel, a aviação, a instrumentação, as pontes e a construção.
II. Classificação e âmbito de aplicação da rebitagem
1. Tipos de rebitagem
Dependendo do desempenho de trabalho dos componentes e do âmbito de aplicação, a rebitagem pode ser dividida em:
(1) Rebitagem forte
Apenas requer que os rebites e os componentes tenham resistência suficiente para suportar grandes cargas, sem requisitos especiais para o aperto da junta. Por exemplo, pontes, vigas, veículos, torres e outros componentes de treliças.
(2) Rebitagem apertada
Requer não só uma resistência suficiente da ligação para suportar determinadas forças, mas também uma boa estanquicidade da junta para garantir que não haja fugas de líquidos ou gases sob determinadas pressões. Este tipo de rebitagem é normalmente utilizado em componentes de recipientes de alta pressão, tais como caldeiras, reservatórios de gás, etc.
(3) Rebitagem apertada
A junta não suporta uma força significativa, requer apenas uma elevada estanquidade para evitar fugas de água e ar, sendo sobretudo utilizada na ligação de componentes de contentores de paredes finas, como tanques de água, tanques de óleo, etc.
2. Formas de rebitagem
De acordo com as diferentes posições relativas das partes ligadas, divide-se em três formas: juntas sobrepostas, juntas de topo e juntas de canto.
(1) Volta
Uma folha é rebitada em cima de outra folha, como mostra a Figura 7-9.
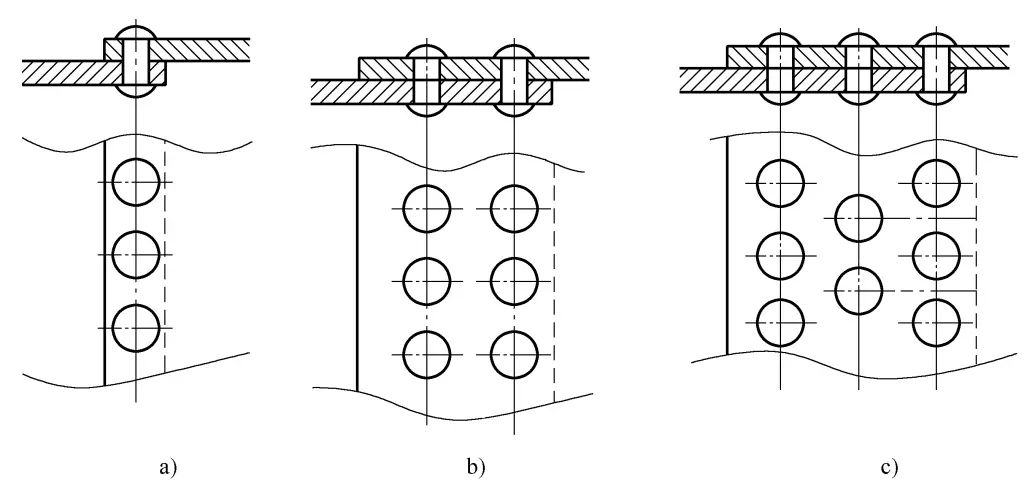
a) Linha única
b) Fileira dupla
c) Várias linhas
(2) Junta de topo
A rebitagem é efectuada colocando as juntas de duas placas no mesmo plano e utilizando uma placa de cobertura como conetor para unir as juntas. Existem dois tipos de chapas de cobertura: simples e dupla, cada uma dividida em fila simples, fila dupla e filas múltiplas, de acordo com o número de filas de rebites. A disposição dos rebites pode ser paralela ou escalonada, como se mostra na Figura 7-10.

a) Fila única, placa de cobertura única
b) Fileira dupla, placa de cobertura dupla
c) Junta de topo de ferro angular
(3) Junta de canto
Liga duas placas perpendiculares ou num determinado ângulo entre si, normalmente utilizando cantoneiras como conetor, disponíveis em formas de face simples e dupla face, como mostra a Figura 7-11.
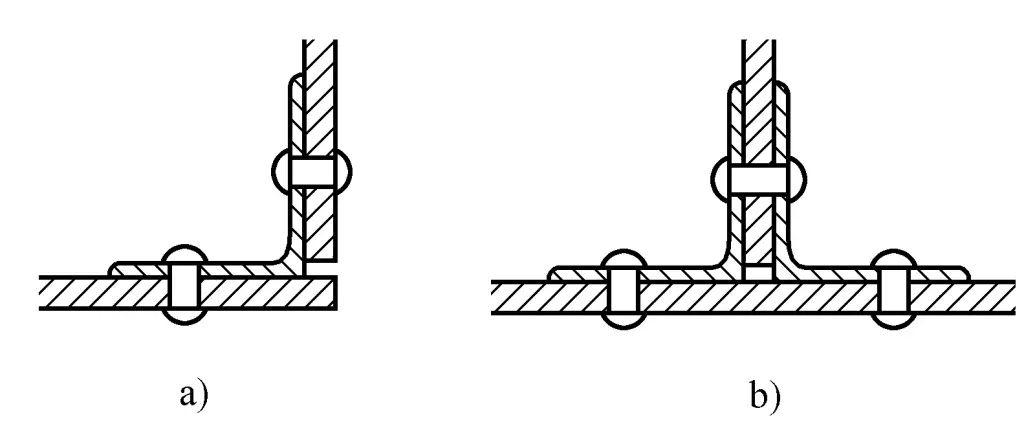
a) Junta de canto de uma face
b) Acoplamento em ângulo de dupla face
III. Parâmetros básicos da disposição dos rebites
Os parâmetros básicos referem-se ao espaçamento entre rebites, espaçamento entre fileiras e distância entre bordas, como mostrado na Figura 7-12.
1) Espaçamento do rebite t: A distância entre os centros de dois rebites adjacentes na mesma fila.
2) Espaçamento entre filas c: A distância entre os centros de duas filas de rebites adjacentes.
3) Distância do bordo e: A distância da fila de rebites mais exterior ao bordo da placa de trabalho.
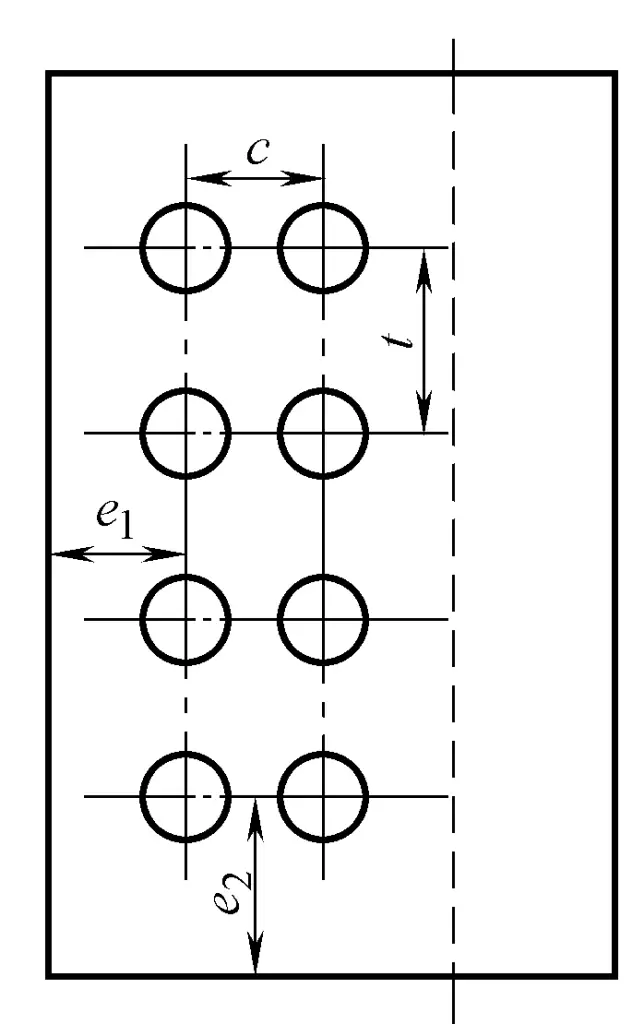
Determinação dos parâmetros de disposição dos rebites em chapas de aço, ver Quadro 7-1.
Tabela 7-1 Determinação dos parâmetros de disposição dos rebites em chapas de aço
Nome | Localização e orientação | Distância máxima admissível (tomar o mínimo dos dois) | Distância mínima admissível | |
Distância do rebite t ou passo c | Fileira exterior | 8d 0 ou 12δ | 3d0 | |
Linha do meio | Componente sob compressão | 12d 0 ou 18δ | ||
Componente sob compressão | 16d 0 ou 24δ | |||
Margem e | Paralelo à direção da carga e 1 | 4d 0 ou 8δ | 2d0 | |
Direção perpendicular à carga e 2 | Vanguarda | 1.5d0 | ||
Borda de rolamento | 1.2d0 |
Nota: d 0 é o diâmetro do furo do rebite; δ é a espessura da placa mais fina
IV. Determinação dos rebites e do seu diâmetro, comprimento e dimensão do furo
1. Rebites
Um rebite é constituído por uma cabeça de rebite e uma haste cilíndrica, sendo a cabeça de rebite frequentemente forjada a partir de matrizes, disponíveis nos tipos maciço e oco. Os rebites maciços dividem-se em várias formas, tais como cabeça redonda, escareada, semi-escareada, cabeça cónica plana e cabeça plana; os rebites ocos são leves e convenientes para a rebitagem, mas têm uma baixa resistência da cabeça, sendo adequados para estruturas sob menos tensão.
De acordo com a norma GB/T116-1986, os rebites de aço incluem Q215, Q235, ML2, ML3, 10, 15, os rebites de cobre incluem T3, H62 e os rebites de alumínio incluem L3, LY1, LY10, LF10 (utilizam os novos tipos de materiais, em conformidade com os regulamentos nacionais padrão para rebites).
Durante o processo de rebitagem, como o rebite precisa de suportar uma deformação plástica significativa, o material do rebite deve ter uma boa plasticidade. Por este motivo, os rebites fabricados por encabeçamento a frio têm de ser recozidos. De acordo com os requisitos, os rebites devem ser submetidos a testes de forjabilidade e testes de resistência mecânica, como tração e cisalhamento. A superfície do rebite não deve apresentar quaisquer defeitos que afectem a sua utilização.
2. Diâmetro do rebite
O diâmetro do rebite é determinado pela espessura da placa de ligação de acordo com os requisitos de resistência estrutural, e a relação entre a espessura da placa componente δ e o diâmetro do rebite d é geralmente a seguinte:
1) Para juntas sobrepostas de uma e duas fiadas, d≈2δ.
2) Para ligações de placas de cobertura de uma e duas filas, d≈(1,5~1,75)δ.
O diâmetro do rebite também pode ser determinado de acordo com a Tabela 7-2.
Tabela 7-2 Determinação do diâmetro do rebite (Unidade: mm)
Espessura da placa δ | 5~6 | 7~9 | 9.5 ~12.5 | 13 ~18 | 19 ~24 | >25 |
Diâmetro do rebite d | 10 ~12 | 14 ~25 | 20 ~22 | 24~27 | 27~30 | 30 ~36 |
Os seguintes princípios devem ser seguidos ao determinar o diâmetro do rebite com base na espessura da placa:
1) Ao brunir chapas com espessuras semelhantes, tomar a espessura da chapa mais grossa.
2) Ao brunir chapas com espessuras significativamente diferentes, tome a espessura da chapa mais fina.
Para a ligação de placas e perfis, é necessário considerar a espessura média de ambos.
A espessura total das peças ligadas não deve exceder 5 vezes o diâmetro do rebite.
3. Comprimento do rebite
A qualidade da rebitagem está diretamente relacionada com o comprimento selecionado da haste do rebite. Se a haste for demasiado comprida, a cabeça do rebite será demasiado grande e é provável que a haste se dobre; se a haste for demasiado curta, não haverá perturbação suficiente e a cabeça do rebite não será totalmente formada, afectando gravemente a resistência e o aperto da rebitagem.
O comprimento do rebite deve ser determinado com base em factores como a espessura total das peças a ligar, a folga entre o furo e o diâmetro da haste e o método do processo de rebitagem. O comprimento da haste do rebite com um diâmetro de furo padrão pode ser calculado usando a seguinte fórmula:
Rebite de cabeça redonda L = (1,65 ~ 1,75)d + 1,1∑δ
Rebite escareado L = 0,8d + 1,1∑δ
Rebite semicontrabaixo L = 1.1d + 1.1∑δ
- L - Comprimento da haste do rebite (mm);
- d - Diâmetro da haste do rebite (mm);
- Comprimento total das peças ligadas (∑δ) em mm.
Os comprimentos dos rebites calculados acima são valores aproximados; o comprimento real da haste do rebite para a rebitagem em massa deve ser determinado após a rebitagem experimental.
4. Determinação do diâmetro do furo do rebite
O ajuste entre o diâmetro do furo do rebite e o rebite deve ser determinado com base em diferentes métodos de rebitagem a frio e a quente.
Durante a rebitagem a frio, a haste não é fácil de perturbar e, para garantir a resistência da junta, o diâmetro do furo deve estar próximo do diâmetro da haste.
Durante a rebitagem a quente, o rebite expande-se e engrossa devido ao calor, mas permanece maleável; para facilitar a inserção, a diferença entre o diâmetro do furo e o diâmetro da haste deve ser ligeiramente maior. Ver Tabela 7-3 para diâmetros de furo padrão. Para a rebitagem estanque de placas multicamadas, o diâmetro de perfuração deve ser reduzido em 1~2mm de acordo com o tamanho do furo padrão, e para componentes cilíndricos, os furos devem ser perfurados antes da dobragem, e o diâmetro do furo deve ser reduzido em 1~2mm do padrão para permitir o alargamento durante a montagem.
Tabela 7-3 Diâmetros padrão dos furos dos rebites (unidade: mm)
Diâmetro da haste do rebite | Diâmetro do furo d0 | |
Montagem de precisão | Montagem em bruto | |
3.5 | 3.6 | 3.9 |
4 | 4.1 | 4.5 |
5 | 5.2 | 5.5 |
6 | 6.2 | 6.5 |
8 | 8.2 | 8.5 |
10 | 10.3 | 11 |
12 | 12.4 | 13 |
14 | 14.5 | 15 |
16 | 16.5 | 17 |
18 | 19 | |
20 | 21.5 | |
22 | 23.5 | |
24 | 25.5 | |
27 | 28.5 | |
30 | 32 | |
36 | 38 |
V. Equipamentos e ferramentas de rebitagem normalmente utilizados
1. Pistola de rebitar
A pistola de rebites é a principal ferramenta para soldar. Também conhecida como pistola de ar, como se mostra na Figura 7-13. É constituída principalmente por uma pega 2, corpo da pistola 4, interrutor 3 e conetor de tubo 1. Podem ser instaladas várias matrizes de rebites ou punções no orifício na extremidade frontal do corpo da pistola para operações de rebitagem ou punção. Quando em uso, a matriz é geralmente amarrada ao punho com fio de aço fino para evitar que o pistão deslize para fora quando a matriz se desprende do corpo da pistola quando a pistola é levantada.
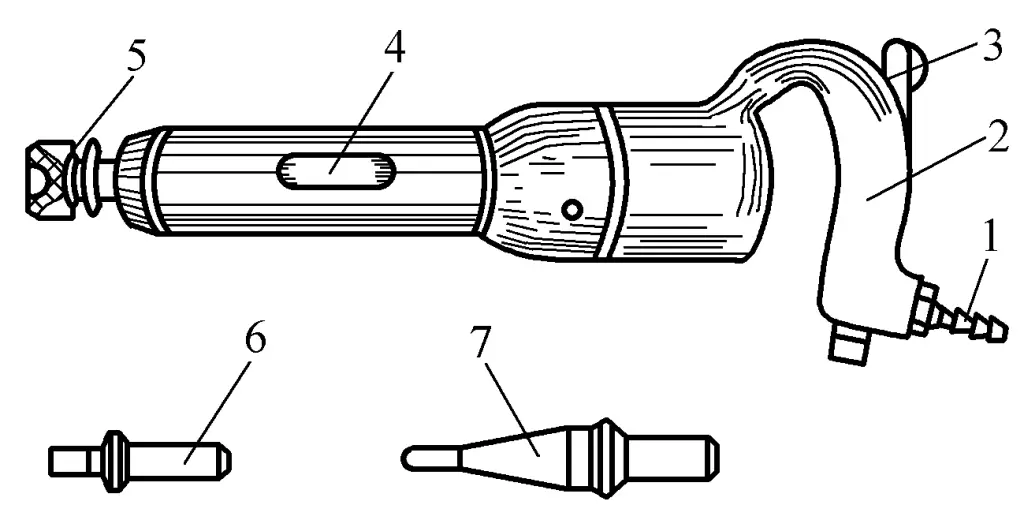
Conector de 1 tubo
2 pegas
3-Troca
Corpo com 4 pistolas
5-Morte
6-Rubo de cabeça chata
7-Soco
Antes de utilizar a pistola de rebites, injetar uma pequena quantidade de óleo de máquina na junta de entrada de ar para manter o corpo da pistola bem lubrificado durante o funcionamento, depois soprar a sujidade da mangueira de ar comprimido e ligá-la ao conetor da mangueira da pistola de rebites. O volume de entrada de ar é controlado pela válvula reguladora de pressão, e a pressão do ar comprimido é geralmente 0.4~0.6MPa. A pistola de rebites é compacta, fácil de operar e pode executar várias tarefas de rebitagem desconhecidas, mas é muito barulhenta durante a operação.
2. Máquina de rebitar
Diferente de uma pistola de rebites, uma rebitadora é um equipamento especializado que utiliza pressão hidráulica ou pneumática para deformar plasticamente a haste do prego e formar uma cabeça de rebite. Possui dois mecanismos: rebitagem e pino superior. Devido à pressão elevada e uniforme produzida pela rebitadora, tanto a qualidade como a resistência da rebitagem são elevadas, e funciona sem ruído.
Existem dois tipos de máquinas de rebitagem: estacionárias e móveis. As máquinas de rebitagem estacionárias têm uma elevada eficiência de produção, mas são mais caras, pelo que só são adequadas para a produção profissional; as máquinas de rebitagem móveis são flexíveis e amplamente utilizadas, disponíveis nos tipos hidráulico, pneumático e elétrico.
A máquina de rebitagem hidráulica utiliza princípios hidráulicos para rebitagem, como mostrado na Figura 7-14. É constituída por uma estrutura 1, pistão 5, cabeça côncava 3, cabeça côncava do pino superior 2 e mola amortecedora 9. Quando o óleo hidráulico entra no cilindro hidráulico através da junta do tubo 8, empurra o pistão para baixo. A extremidade inferior do pistão tem uma cabeça côncava 3, e o rebite é pressionado entre as cabeças côncavas superior e inferior para formar a cabeça do rebite.
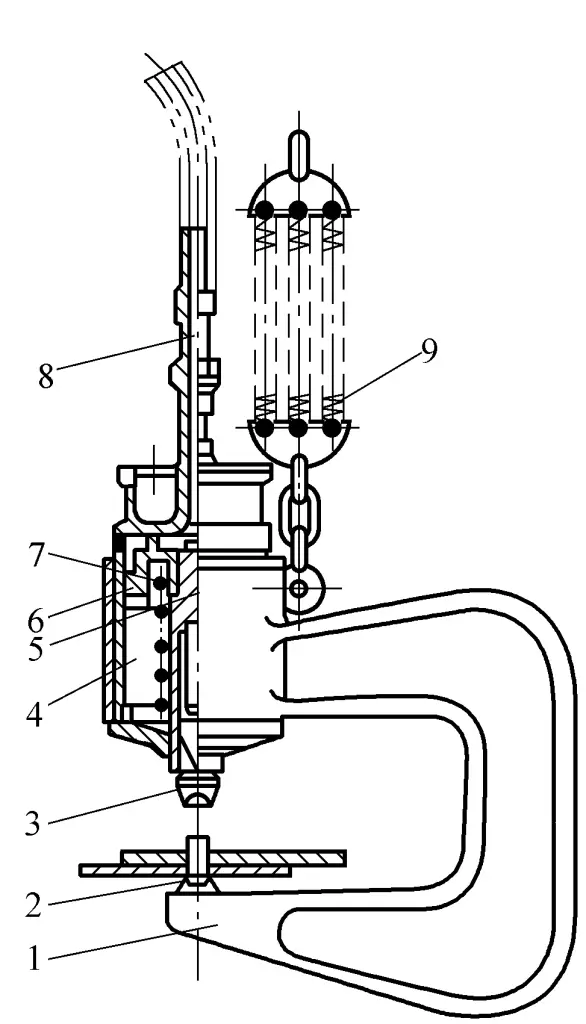
1-Armação
2-Cabeça côncava do pino superior
3-Cabeça côncava
4-Cilindro hidráulico
5 pistões
6-Almofada de vedação
7-primavera
Tubo 8 de encaixe
Mola de 9 tampões
Quando o pistão se move para baixo, a mola 7 é comprimida e deformada. Após a rebitagem estar concluída, o pistão é reposto pela elasticidade da mola. A função da almofada de vedação 6 é evitar a fuga de óleo do pistão. Toda a máquina de rebitagem pode ser movida por um guindaste e, para evitar vibrações durante a rebitagem, a mola no anel de elevação pode ser usada para amortecer.
VI. Processo de rebitagem
A rebitagem divide-se em rebitagem a frio e rebitagem a quente com base na temperatura; esta secção apresenta principalmente a rebitagem a quente.
1. Rebitagem a frio
A rebitagem à temperatura ambiente é chamada de rebitagem a frio. A rebitagem a frio requer que o rebite tenha uma boa plasticidade. Quando se utiliza uma máquina de rebitagem para a rebitagem a frio, o diâmetro máximo do rebite não deve exceder 25 mm. Quando se utiliza uma pistola de rebites para a rebitagem a frio, o diâmetro do rebite é geralmente inferior a 12 mm.
2. Rebitagem a quente
A rebitagem após o aquecimento do rebite é designada por rebitagem a quente. Após o aquecimento, a resistência da haste do rebite diminui, a plasticidade aumenta e a cabeça do rebite forma-se facilmente. A força externa necessária para a rebitagem é significativamente reduzida em comparação com a rebitagem a frio, pelo que a rebitagem a quente é normalmente utilizada para rebites de maior diâmetro ou rebitagem em massa.
Durante a rebitagem a quente, para além de se formar uma cabeça de rebite selada, uma extremidade da haste do rebite é também revirada para preencher o orifício do rebite. Após o arrefecimento, o rebite contrai-se em comprimento, exercendo uma pressão suficiente sobre as peças rebitadas, tornando a costura mais apertada e conseguindo assim uma resistência suficiente da junta.
O processo básico de rebitagem a quente é o seguinte:
(1) Fixação de peças rebitadas e alargamento de furos de rebites
Aquando da montagem de peças rebitadas, é necessário alinhar os orifícios nas placas e apertá-los com parafusos com as especificações correspondentes. A distribuição dos parafusos deve ser uniforme e o número não deve ser inferior a um quarto do número de furos de rebites. Depois de apertar os parafusos, as superfícies de junção das costuras devem ser apertadas.
Na montagem dos componentes, devido a erros de maquinagem, podem ocorrer alguns orifícios desalinhados, pelo que é necessário escarear os orifícios dos rebites com um punção de correção ou um escareador antes da rebitagem para garantir a concentricidade e uma rebitagem suave. Os orifícios de rebites que tenham ficado com folgas no pré-processamento devem ser escareados de uma só vez. A sequência de alargamento consiste em alargar primeiro os furos sem parafusos apertados, depois inserir os parafusos após o alargamento e, por fim, retirar os parafusos originais e alargar novamente os furos.
(2) Aquecimento do rebite
Ao rebitar com uma pistola de rebite, o rebite precisa ser aquecido a 1000 ~ 1100 ℃. Durante o aquecimento, o rebite é aquecido a uma cor amarelo-laranja (cerca de 900 ~ 1100 ℃), depois mudou para fogo lento para arder, permitindo que o rebite aqueça uniformemente em todo o seu comprimento e interior, e o rebite bem aquecido pode então ser retirado para rebitagem (rebites que são superaquecidos ou insuficientemente aquecidos durante o aquecimento não podem ser usados).
(3) Apanhar e inserir o rebite
Lançar o rebite com precisão, apanhar o rebite com firmeza e inserir rapidamente o rebite no orifício depois de o apanhar, esforçando-se por completar a rebitagem a alta temperatura.
(4) Rebitagem superior
A qualidade da rebitagem de topo afecta diretamente a qualidade da rebitagem. A forma da cabeça côncava e as especificações na pega superior devem corresponder à cabeça do rebite pré-fabricado. O "côncavo" deve ser mais raso e a rebitagem superior deve ser forte para fazer com que a cabeça do rebite formada se encaixe firmemente na superfície da placa.
(5) Rebitagem
Inicialmente, o fornecimento de ar intermitente é usado na rebitagem, e depois que a haste do prego é virada, o volume de ar é aumentado para forjar a haste do prego exposta em forma de cabeça de rebite. Depois da cabeça do rebite estar formada, a pistola de rebites é ligeiramente inclinada e rodada à volta da cabeça do rebite durante uma volta para forçar a cabeça do rebite a encaixar firmemente na superfície do componente, mas não é permitida uma inclinação excessiva para evitar danificar a superfície do componente com a cabeça côncava. Como mostrado na Figura 7-15.
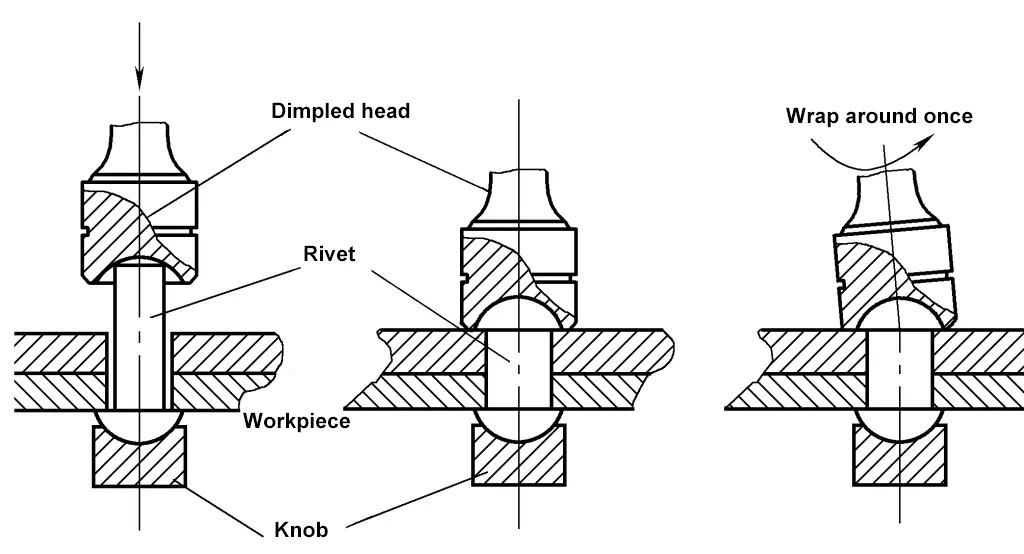
Para garantir a qualidade da rebitagem, a pressão do ar comprimido não deve ser inferior a 0,5MPa; a temperatura final de rebitagem do rebite deve estar entre 450 ~ 600 ℃. Se a temperatura final de rebitagem for muito alta, reduzirá a tensão inicial da haste do prego, impedindo que os componentes rebitados sejam totalmente apertados; se a temperatura final de rebitagem for muito baixa, o rebite ficará quebradiço.
Por conseguinte, o processo de rebitagem a quente deve ser concluído o mais rapidamente possível num curto espaço de tempo. No caso de estruturas com elevados requisitos de estanquidade das costuras, é ainda necessário proceder ao aperto das costuras após a rebitagem. Depois de concluída a rebitagem, cada rebite deve ser verificado individualmente quanto à sua qualidade e os que se encontrarem soltos e irreparáveis devem ser retirados e rebitados.
Articulação de mordida
I. Determinação da forma estrutural e da dimensão da articulação de mordida
1. Características da mordedura da costura
A união por costura é um método de ligação em que os bordos das peças a ligar são dobrados num determinado ângulo, interligados e depois pressionados um contra o outro. As ligações por costura são bastante robustas, têm uma boa densidade de costura, requerem menos exigências em termos de maquinaria e ferramentas e são fáceis de implementar. As uniões por costura são frequentemente utilizadas em estruturas de chapa metálica com uma espessura inferior a 2 mm, como em projectos de condutas muito utilizados, onde as uniões por costura são utilizadas em muitos locais para substituir a brasagem.
As ligações de costura são classificadas por forma de ligação em costura simples, costura dupla e costura composta; por forma de costura em costura plana, costura de canto e costura vertical; e por posição de costura em costura longitudinal e costura transversal.
As ligações de costura são geralmente efectuadas manualmente ou com equipamento mecânico. Para uma produção única ou em pequena escala, a união manual de costuras é amplamente utilizada para fabricar pequenos produtos de chapa metálica, caracterizados pelo baixo custo e comodidade.
Para a produção em massa, utiliza-se o corte mecânico de costuras, que, em comparação com o corte manual de costuras, apresenta vantagens como menor ruído, melhor qualidade das costuras, menor intensidade de trabalho para os operários e maior eficiência de produção (pode ser aumentada de 8 a 25 vezes), mas exige um grande investimento único em equipamento. O corte mecânico de costuras deve ser utilizado tanto quanto possível, se as condições o permitirem.
2. Formas de costura
Dependendo da estrutura e dos requisitos das peças de chapa metálica, são utilizadas diferentes formas de costuras. As formas de costura mais comuns são apresentadas no Quadro 7-4.
Quadro 7-4 Formas de costura
Nome da costura | Diagrama simplificado | Tamanho da margem de costura | Utilização | |
Costura plana | Costura normal plana | ![]() | A margem de costura é 3 vezes Largura da costura | Utilizado para ligações de tubos cilíndricos, cónicos e rectangulares. Utilizar uma costura lisa se a costura tiver de ser fixada a uma superfície plana ou tiver de ser hermética; utilizar uma costura dupla se for necessária uma maior resistência e hermeticidade. |
Costura lisa e plana | ![]() | |||
Costura plana de suspensão | ![]() | |||
Costura dupla plana | ![]() | A margem de costura é 5 vezes a largura da costura | ||
Costura de canto | Canto com costura simples | ![]() | A margem de costura é 3 vezes a largura da costura | Costura de canto utilizada no fabrico de curvas em cotovelo |
Canto com costura dupla | ![]() | |||
Costura composta de canto | ![]() | A margem de costura é 4 vezes a largura da costura | ||
Costura vertical | Costura simples vertical | ![]() | A margem de costura é três vezes a largura da costura | Utilizado para várias ligações de transição ao ligar tubos de derivação, cotovelos e transição de secções transversais redondas para outras secções transversais |
Costura dupla vertical | ![]() | A margem de costura é cinco vezes a largura da costura |
II. Ferramentas e utilização para a costura
1. Ferramenta de costura
Ferramenta de costura, como se mostra na Figura 7-16.
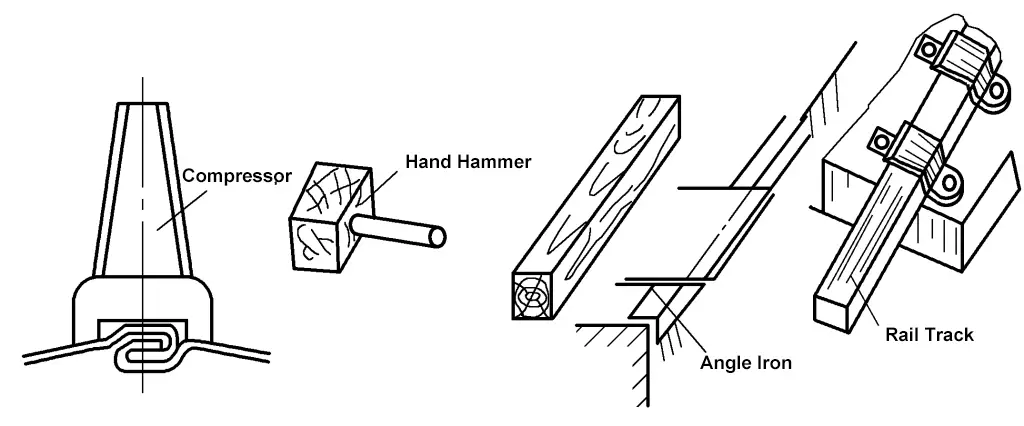
2. Etapas da operação de costura
A costura por mordedura é geralmente efectuada manualmente e os passos gerais são os seguintes
1) Calcular a margem de costura em função do tipo de costura.
2) Desenhar a linha de dobragem da costura no bordo da placa.
3) Dobrar o bordo da placa ao longo da linha de dobragem.
4) Aperte e pressione os dois lados juntos para completar a costura.
3. Ligação plana de costura simples
As costuras simples planas são geralmente utilizadas para ligar placas de 0,2 a 1,5 mm de espessura, com a largura da costura a depender da espessura da placa. Quando a espessura da placa é de 0,2~0,5mm, a largura da costura é de 3~5mm; quando a espessura da placa é de 0,75~1,5mm, a largura da costura é de 5~8mm. A margem para uma costura simples e plana é três vezes a largura da costura. O processo de costura é o seguinte:
1) Determinar a largura da costura com base na espessura da placa e prever uma margem de costura três vezes superior à largura da costura.
2) Desenhar a linha de dobragem da costura na borda da placa (uma borda na largura da costura; a outra borda no dobro da largura da costura).
3) Alinhar a linha de dobragem da aresta da placa com o canto ou a aresta da barra quadrada e bater com um martelo para a dobrar num ângulo reto, como se mostra na Figura 7-17a.
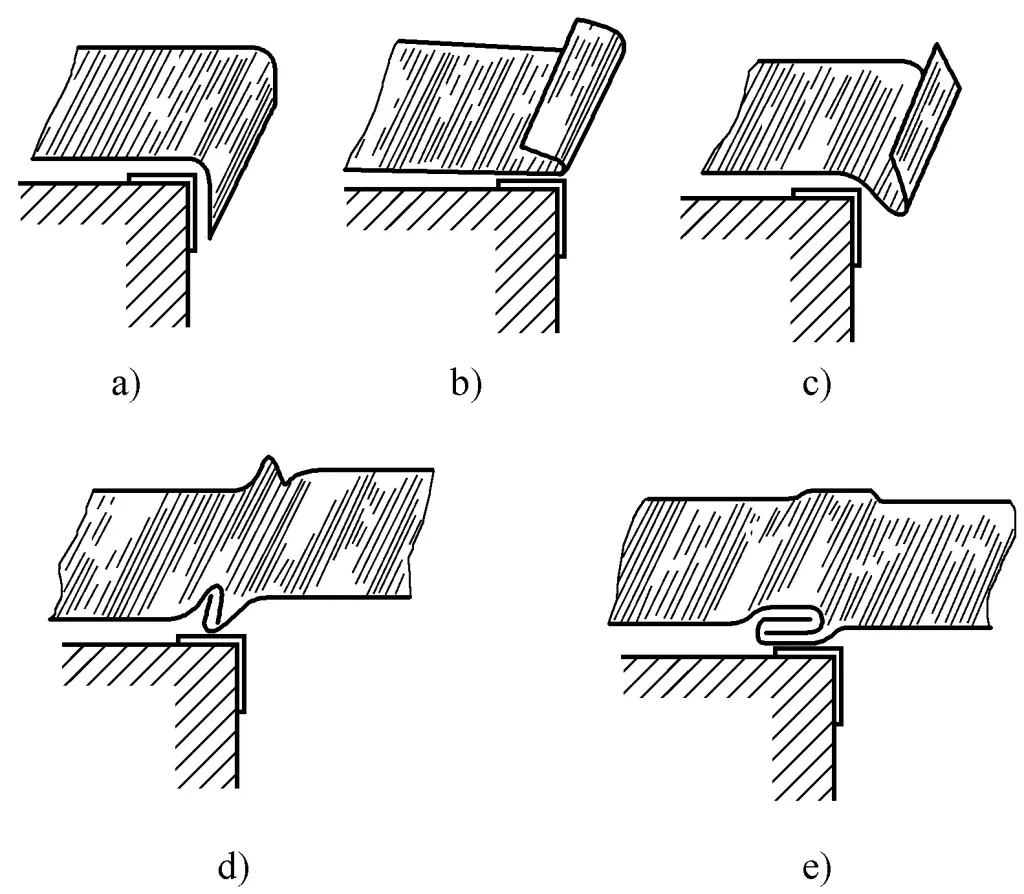
4) Virar a folha e utilizar um martelo para dobrar ainda mais o bordo da folha, como se mostra na Figura 7-17b. Note-se que deve ser deixado um espaço maior do que a espessura da folha durante a dobragem, caso contrário a outra extremidade não pode ser inserida e unida.
5) Mover a folha para a frente um pouco mais do que a largura da aresta dobrada, bater-lhe com um martelo para a dobrar cerca de 45°, como se mostra na Figura 7-17c. A outra extremidade também é feita da mesma forma.
6) Juntar os dois bordos e bater para comprimir, como indicado nas Figuras 7-17d e 7-17e. Se for necessária uma costura interior ou exterior plana, esta pode ser pressionada utilizando um calcador de costuras, como se mostra na Figura 7-18a, ou utilizando o bordo de uma plataforma ou barra quadrada, como se mostra na Figura 7-18b.
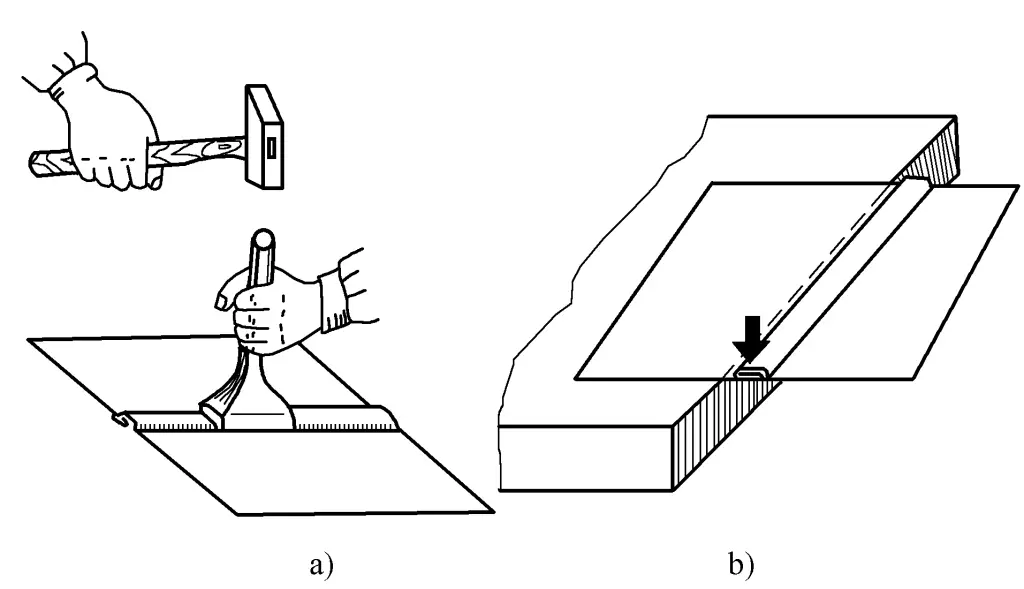
a) Passado a ferro com um calcador de costuras
b) Pressionado com a borda de uma plataforma, barra quadrada
4. Junta de costura de canto
A largura da junta de canto é determinada pela espessura da chapa, geralmente entre 3~8mm, sendo que as chapas mais finas têm o valor mais pequeno e as chapas mais grossas têm o valor maior. A margem para a junção da junta de canto é três vezes a largura da junta. O processo de fabrico é o seguinte:
1) Determinar a largura da costura com base na espessura da folha, libertar a margem de junção e desenhar a linha de dobragem no bordo da folha (um lado com a largura da costura; o outro lado com o dobro da largura da costura).
2) Alinhe a linha de dobragem com a plataforma ou com a extremidade da barra quadrada, dobre-a num ângulo reto com um martelo, depois vire a placa e dobre-a ainda mais batendo com um martelo (deixando um espaço maior do que a espessura da placa), como se mostra nas Figuras 7-19a e 7-19b.
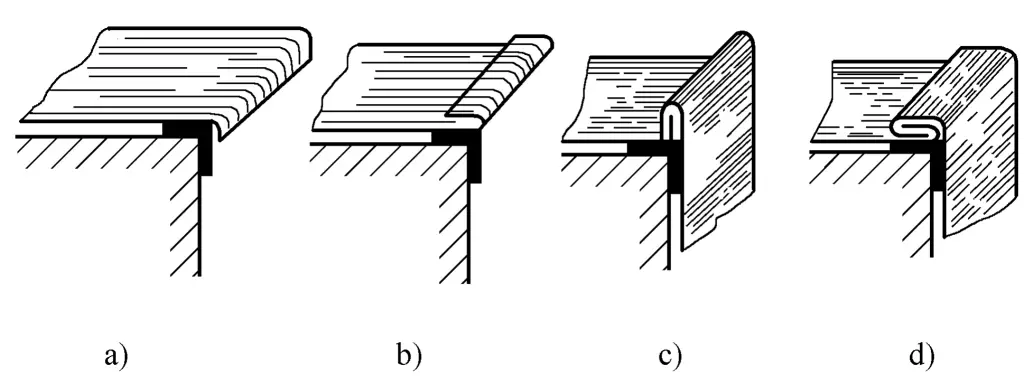
3) Dobrar outra placa num ângulo reto e, em seguida, virá-la de modo a que a placa já dobrada fique presa à aresta reta, como se mostra na Figura 7-19c.
4) Dobrar e pressionar a parte da borda reta em gancho, como se mostra na Figura 7-19d.
Ligação roscada
I. Estrutura e ferramentas comuns das ligações roscadas
Uma ligação fixa amovível formada por peças roscadas. As ligações roscadas comuns incluem a ligação por parafuso, a ligação por perno de cabeça dupla e a ligação por parafuso, que são amplamente utilizadas devido à sua estrutura simples, fixação fiável, montagem e desmontagem rápidas e convenientes, e custo-benefício. Existem muitos tipos e especificações de fixadores roscados, mas a sua estrutura, forma e tamanho foram normalizados e podem ser encontrados nas normas correspondentes.
As ferramentas comuns incluem chaves de fendas, chaves ajustáveis, chaves de caixa, chaves hexagonais, chaves de bocas e chaves de porcas.
II. Processo de ligação roscada
1. Ligação por parafusos
A ligação por parafusos é constituída por parafusos, porcas e anilhas, sendo principalmente utilizada para ligações em que as peças são finas e podem ser formadas através de orifícios.
Existem dois tipos de ligações aparafusadas: uma é a ligação que suporta a carga de tração axial, que permite uma certa folga entre a haste do parafuso de tensão e a parede do furo; a outra é a ligação do parafuso de corte que suporta a força radial, que requer um diâmetro de furo rigoroso, precisa de ser escareado e utiliza um ajuste de transição ou ajuste de interferência com o sistema básico de furos para a parte da haste não roscada do parafuso. Por conseguinte, pode fixar com precisão a posição relativa das peças ligadas e suportar a força radial. tosquia e a compressão causada por cargas laterais, como mostra a Figura 7-20.
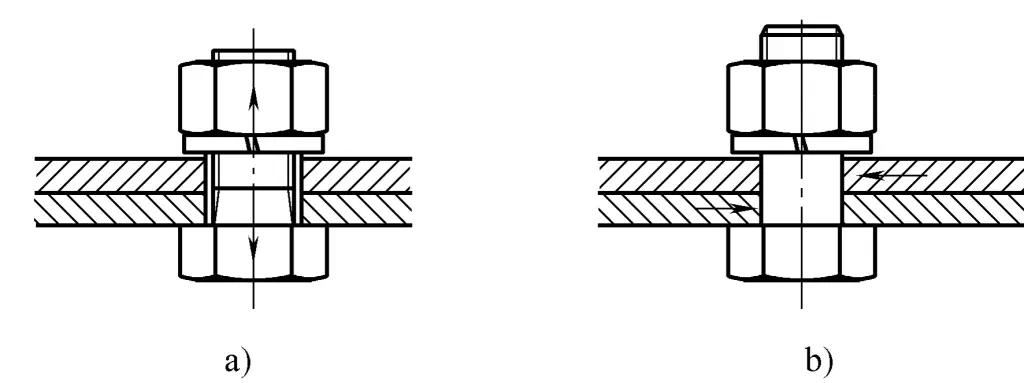
a) Ligação dos parafusos de tração
b) Ligação por parafusos de corte
(1) Método de montagem da ligação por parafusos
Ao efetuar uma ligação por parafuso, as especificações e a quantidade de parafusos, porcas e anilhas devem ser determinadas com base na espessura e no diâmetro do orifício das peças que estão a ser ligadas. Geralmente, o comprimento do parafuso é igual à espessura combinada das peças ligadas, da porca e da anilha, mais uma tolerância de 1~2t (t é o tamanho do passo).
Durante a ligação, o parafuso passa através do orifício de passagem na peça ligada e, depois de adicionar uma anilha, a porca é apertada. Para evitar que o parafuso rode com a porca durante o aperto, utilize chaves para segurar o parafuso e a porca separadamente e rode em direcções opostas até obter o aperto necessário.
Durante o aperto, o binário de aperto deve ser controlado; um binário demasiado elevado pode provocar o alongamento dos parafusos, a rutura e a deformação das peças ligadas; um binário demasiado reduzido não pode garantir os requisitos e a fiabilidade da ligação durante o funcionamento.
(2) Sequência de montagem dos parafusos agrupados
O aperto de parafusos agrupados deve ser efectuado numa determinada ordem e gradualmente apertado por fases (normalmente em três fases) para evitar inconsistências no aperto, tensão desigual nos parafusos, deformação dos fixadores ou mesmo a quebra de parafusos individuais sob tensão elevada. A Figura 7-21 mostra a sequência de aperto dos parafusos em várias posições de montagem.
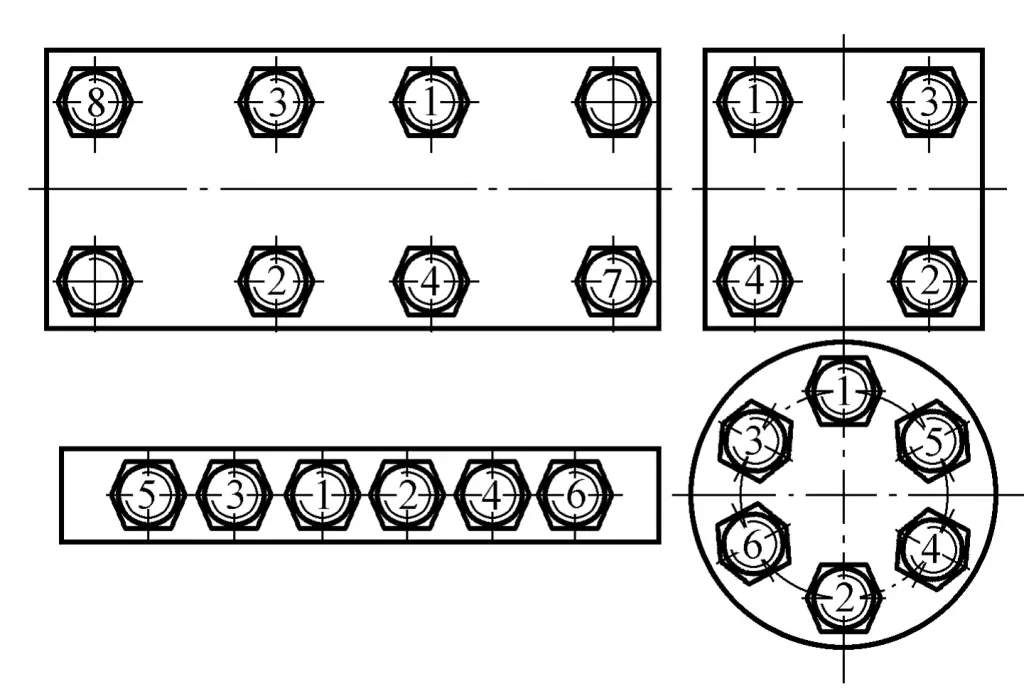
2. Ligação de pernos
Os pernos de extremidade dupla são utilizados principalmente em situações em que as peças são demasiado espessas para ligações com parafusos. Durante a ligação, uma extremidade do perno de extremidade dupla é aparafusada nas roscas do orifício cego e a outra extremidade passa através do orifício de passagem da peça de ligação, depois é colocada uma anilha e a porca é apertada. Para desmontar, desaparafusar a porca para separar as peças ligadas, como se mostra na Figura 7-22.
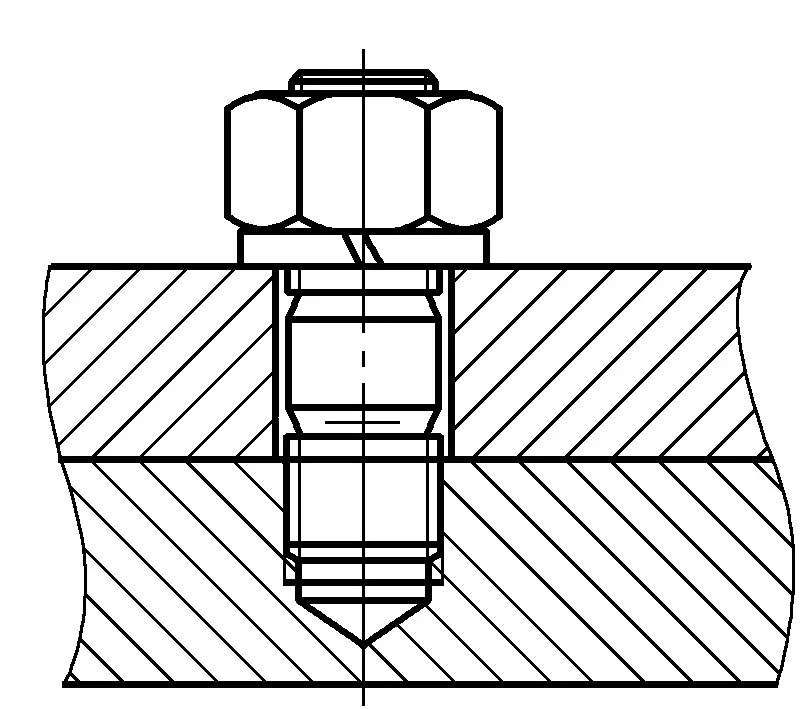
(1) Método de montagem de pernos de extremidade dupla Uma vez que os pernos de extremidade dupla não têm uma extremidade fixa, não podem ser diretamente apertados com a extremidade aparafusada. Normalmente, é utilizado o método de aperto com as porcas duplas viradas uma para a outra ou com um parafuso virado para o perno, conforme ilustrado na Figura 7-23.
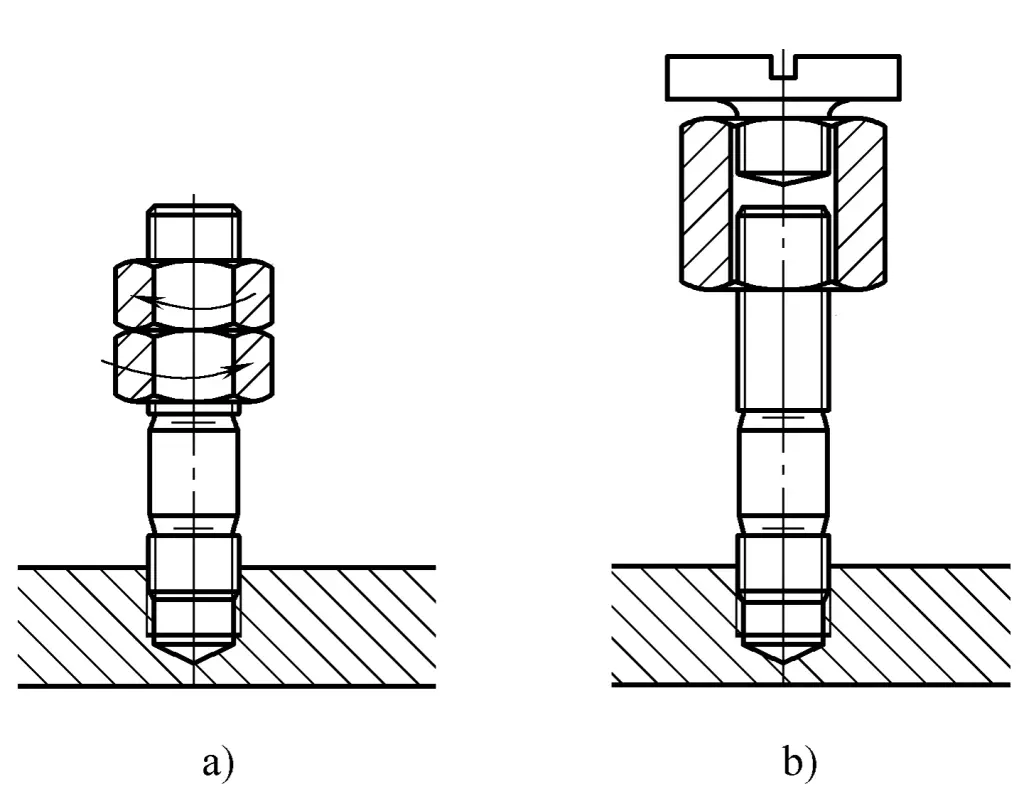
a) Porcas duplas viradas uma para a outra
b) Parafuso virado para a cavilha
(2) Precauções de montagem
1) As superfícies de contacto dos pernos e dos furos roscados devem estar limpas e secas. Apertar o parafuso à mão até ao fim da rosca. Se não puder ser aparafusado, não o aperte à força com uma chave para evitar danificar as roscas.
2) O ajuste entre o perno de extremidade dupla e o furo roscado deve ser suficientemente apertado para garantir que o perno não se solte quando a porca é removida ou instalada. A extremidade roscada do perno deve utilizar um ajuste transitório durante a maquinagem para assegurar uma certa quantidade de interferência no diâmetro médio das roscas após o encaixe.
3) A linha central da cavilha deve ser perpendicular à superfície do componente ligado.
3. Medidas para evitar o afrouxamento das ligações roscadas
As ligações roscadas têm um certo desempenho de autobloqueio e não se soltam sozinhas sob cargas estáticas e pequenas alterações na temperatura de trabalho. No entanto, em caso de cargas de impacto, cargas variáveis ou alterações significativas da temperatura de trabalho, pode ocorrer um afrouxamento. Para garantir a segurança e a fiabilidade da ligação e evitar acidentes causados pelo afrouxamento, devem ser tomadas certas medidas anti-afrouxamento.
As medidas comuns de anti-afrouxamento incluem o anti-afrouxamento mecânico e o aumento da resistência ao atrito.
(1) Anti-afrouxamento mecânico
1) Anti-afrouxamento do contrapino. Como se mostra na Figura 7-24, passar a chaveta pela ranhura da porca e pelo orifício do parafuso e, em seguida, dobrar a extremidade da cauda para impedir que o parafuso e a porca rodem um em relação ao outro, atingindo assim o objetivo de antiafrouxamento. O anti-afrouxamento da chaveta é normalmente utilizado em máquinas de alta velocidade sob cargas vibratórias.
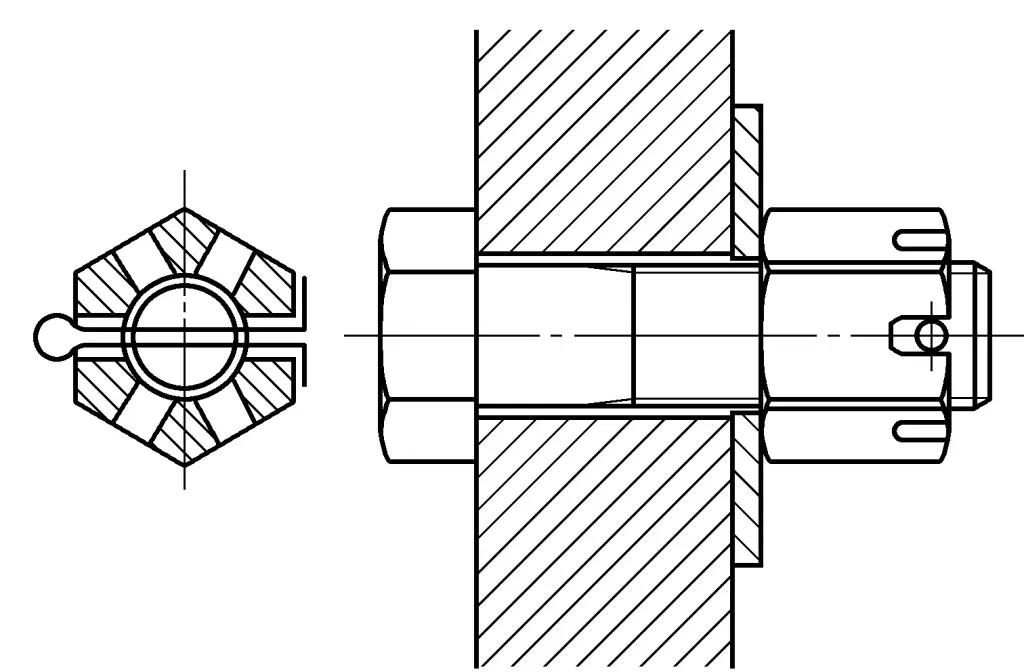
2) Parar o anti-afrouxamento da anilha. Conforme ilustrado na Figura 7-25. Introduzir as asas interiores da anilha de paragem na ranhura axial na extremidade da peça roscada exterior, apertar a porca e, em seguida, dobrar as asas exteriores da anilha na ranhura da porca, bloqueando assim a porca. Utilizada para anti-afrouxamento em ligações roscadas do tipo veio.

3) Arruela de bloqueio anti-afrouxamento. Conforme ilustrado na Figura 7-26. Depois de apertar a porca, dobrar as orelhas simples ou duplas da anilha de bloqueio para aderir firmemente aos bordos da peça e da porca, impedindo que a porca se solte. Só pode ser utilizada onde houver espaço para acomodar as orelhas dobradas.
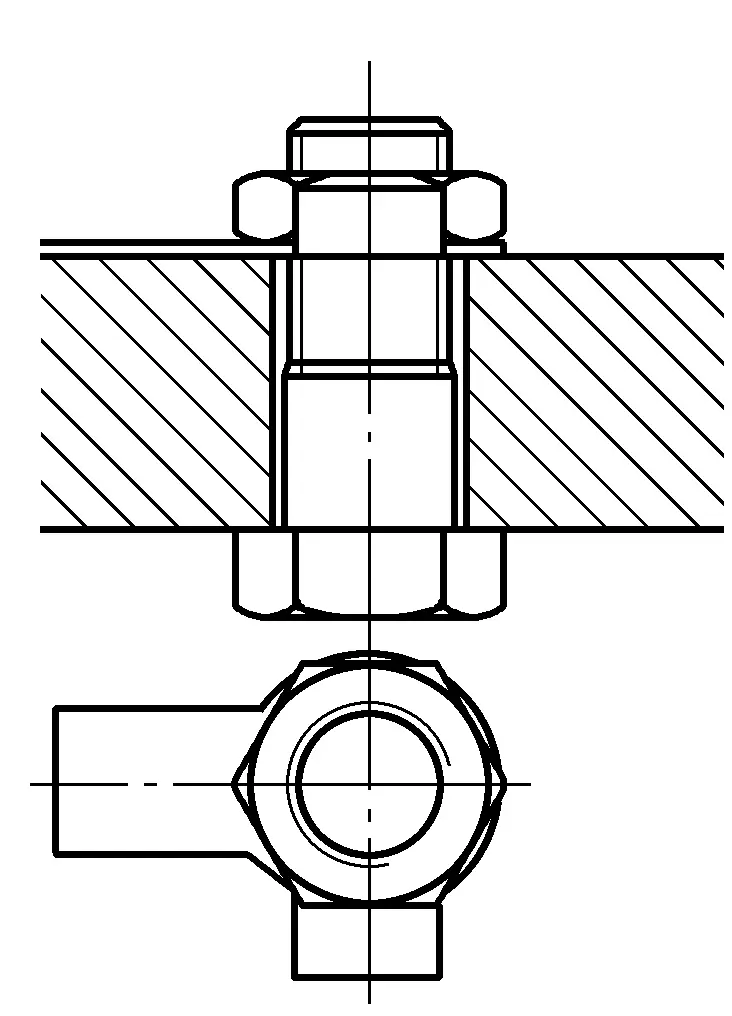
(2) Aumentar o atrito para evitar o afrouxamento
Como se mostra na Figura 7-27, aplica-se uma força axial adicional para aumentar a fricção entre as superfícies das roscas apertadas para atingir o objetivo de evitar o afrouxamento, incluindo principalmente os métodos das anilhas de mola e das porcas duplas. No entanto, o desempenho anti-afrouxamento não é fiável e só é adequado para situações com pouco impacto e vibração.

a) Arruela de pressão para evitar que se solte
b) Porca dupla para evitar que se solte
c) Aumento do atrito nas superfícies de contacto roscadas
Formação em competências de conexão
I. Diagrama da peça de trabalho para soldadura plana com junta biselada
O diagrama da peça de trabalho de soldadura plana com junta em bisel é mostrado na Figura 7-28.
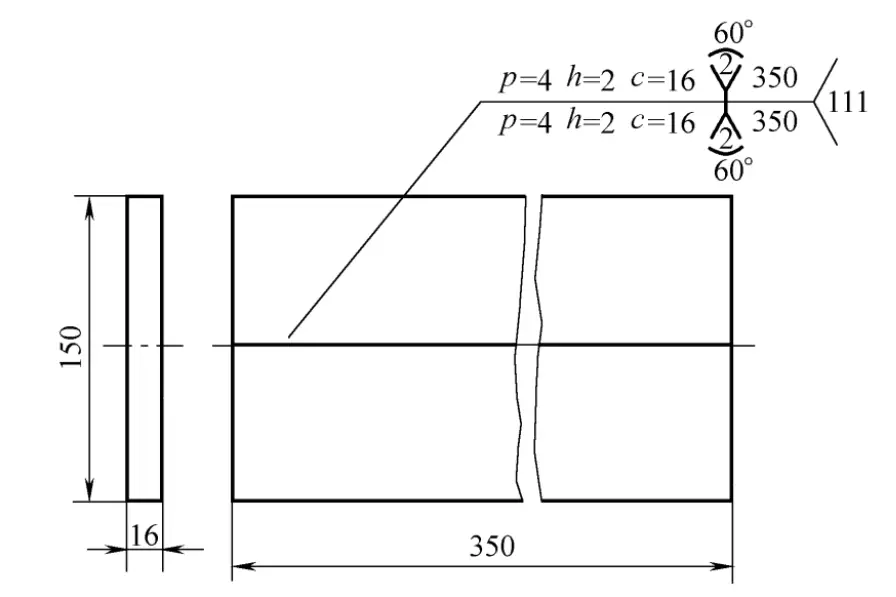
Requisitos técnicos
- A peça de trabalho deve utilizar a soldadura de dupla face e de dupla camada, com a sequência de soldadura a seguir um padrão simétrico de dentro para fora.
- Cada soldadura externa deve incluir pelo menos uma junta e a forma da junta deve ser coerente com a da soldadura.
- Todas as dimensões das soldaduras têm de cumprir os requisitos especificados e devem ser esteticamente agradáveis, rectas e isentas de defeitos, tais como cortes inferiores, inclusões de escória e porosidade.
- Após a soldadura, remover cuidadosamente todas as escórias e salpicos. Se a peça de trabalho estiver significativamente deformada, deve ser endireitada.
II. Seleção das especificações do processo para peças de trabalho de soldadura plana de junta de topo com bisel
1. Selecionar a forma do bisel da junta
Para juntas de placas mais espessas, o bisel deve permitir que o arco penetre profundamente na raiz da soldadura, assegurando a penetração da raiz e facilitando a remoção da escória, alcançando resistência suficiente e formando uma boa soldadura. O tipo de chanfro selecionado deve satisfazer as seguintes condições: garantir a penetração da soldadura; a forma do chanfro é fácil de processar; alta produtividade, poupar as varas de soldadura; menor deformação da peça soldada após a soldadura. Por conseguinte, a peça de trabalho mostrada na Figura 7-28 é mais vantajosa com um bisel em forma de X.
2. Escolher o diâmetro do elétrodo para o bisel em forma de X
A secção transversal é radial e a quantidade de metal de adição na soldadura exterior é muito maior do que na soldadura interior. Ao escolher os eléctrodos, o diâmetro do elétrodo exterior deve ser maior do que o da soldadura interior. Geralmente, um elétrodo de 4,0 mm de diâmetro pode ser selecionado para a soldadura interior, ou um elétrodo de 4,0 mm de diâmetro pode ser utilizado para ambas as camadas.
3. Seleção da corrente do elétrodo
Ao soldar com um elétrodo de 4,0 mm de diâmetro, a corrente de soldadura pode ser selecionada entre 160~210A, e a corrente de soldadura para a soldadura exterior deve ser ligeiramente superior à da camada interior. Quando a soldadura exterior utiliza um elétrodo de 5,0 mm de diâmetro