I. Composição e princípio de funcionamento dos centros de maquinagem
Um centro de maquinagem é um equipamento de processamento altamente automatizado desenvolvido a partir de máquinas de fresagem CNC. É uma máquina-ferramenta CNC com um depósito de ferramentas e um permutador automático de ferramentas (ATC), também conhecida como máquina-ferramenta CNC de troca automática de ferramentas ou máquina-ferramenta CNC multiprocesso.
Depois de a peça de trabalho ser fixada uma vez, o sistema CNC pode controlar a máquina para selecionar e mudar automaticamente as ferramentas de acordo com diferentes processos; alterar automaticamente a velocidade do fuso, a taxa de avanço e a trajetória de movimento da ferramenta em relação à peça de trabalho, bem como outras funções auxiliares; e completar a maquinação multi-processo em várias superfícies da peça de trabalho em sequência.
Isto reduz o tempo de fixação da peça de trabalho, de medição e de ajuste da máquina, encurta o tempo de armazenamento e manuseamento da peça de trabalho e melhora a eficiência da produção e a utilização da máquina. Os centros de maquinação são equipamentos indispensáveis no processamento automatizado e são também as principais máquinas em sistemas de fabrico flexíveis (FMS). Para melhorar a funcionalidade dos centros de maquinação, surgiram centros de maquinação com mudanças automáticas de armazém de ferramentas, mudanças automáticas de cabeça de spindle e mudanças automáticas de caixa de spindle.
Os centros de maquinação com mudanças automáticas de armazém de ferramentas têm maiores capacidades de armazém de ferramentas, facilitando a maquinação multi-processo de peças complexas tipo caixa. Os centros de maquinação com mudanças automáticas da cabeça do fuso podem realizar fresagem horizontal, fresagem vertical, retificação e fresagem indexável. Além do magazine de ferramentas, esse tipo de centro de usinagem também possui um magazine de cabeça de fuso, que é trocado por robôs industriais ou mãos mecânicas.
Os centros de maquinagem com mudanças automáticas de caixa de fuso têm geralmente caixas de fuso de maquinagem de desbaste e caixas de fuso de maquinagem fina para melhorar a precisão e o alcance da maquinagem. A principal diferença entre os centros de maquinagem e as máquinas-ferramentas CNC comuns é que podem concluir trabalhos numa única máquina que exigiriam várias máquinas.
Atualmente, os centros de maquinação têm capacidades crescentes de armazenamento de ferramentas, tempos de troca de ferramentas mais curtos, maior precisão de maquinação e funcionalidade melhorada. Para além dos centros de maquinação desenvolvidos a partir de fresadoras CNC (centros de maquinação de fresagem e perfuração), surgiram também centros de maquinação de torneamento desenvolvidos a partir de tornos CNC.
1. Composição dos centros de maquinagem
Desde que o primeiro centro de maquinação do mundo nasceu em 1958, surgiram vários tipos de centros de maquinação com diferentes estruturas externas, mas são geralmente compostos pelas seguintes partes principais.
(1) Corpo da máquina-ferramenta
O corpo de um centro de maquinagem refere-se à sua entidade de estrutura mecânica, composta pelo sistema de acionamento principal, sistema de acionamento de alimentação, cama, coluna e mesa de trabalho.
Estes componentes incluem peças de ferro fundido e estruturas de aço soldadas. São a estrutura básica do centro de maquinação e devem suportar a carga estática do centro de maquinação, bem como a carga de corte gerada durante a maquinação, pelo que devem ter rigidez suficiente.
(2) Sistema CNC
O sistema CNC é o centro de controlo do centro de maquinagem e da sua alma. É composto principalmente pelo sistema de controlo principal, controlador lógico programável (PLC), interface de entrada/saída, teclado e monitor. O sistema de controlo principal é composto principalmente por CPU, memória e controlador.
Os principais objectos de controlo do sistema CNC são grandezas mecânicas, como a posição, o ângulo e a velocidade, bem como grandezas físicas, como a temperatura, a pressão e o fluxo. Os seus métodos de controlo podem ser divididos em duas categorias: controlo do processamento de operações de dados e controlo lógico sequencial.
O módulo de interpolação no controlador principal lê o programa de peças, processa-o através de descodificação e compilação, executa os cálculos de interpolação do caminho da ferramenta correspondentes e controla o deslocamento de cada eixo de coordenadas da máquina-ferramenta, comparando com os sinais de feedback de posição e velocidade de cada sistema servo de coordenadas.
O controlo lógico sequencial é normalmente realizado pelo PLC, que coordena as acções necessárias no processo de maquinação da máquina-ferramenta, faz julgamentos lógicos com base em vários sinais de deteção e controla o funcionamento ordenado de várias partes da máquina-ferramenta.
(3) Sistema servo
O sistema servo é a ligação de acionamento elétrico entre o sistema CNC e o corpo da máquina-ferramenta. É constituído principalmente por servomotores, sistemas de controlo de acionamento e dispositivos de deteção e retorno de posição. O servomotor é o componente executante do sistema, enquanto o sistema de controlo de acionamento é a fonte de energia para o servomotor.
O sinal de comando emitido pelo sistema CNC é comparado com o sinal de feedback da posição e utilizado como um comando de deslocação. Após a amplificação da potência pelo sistema de acionamento, este faz rodar o motor, que por sua vez faz mover a mesa de trabalho ou o porta-ferramentas através de dispositivos de transmissão mecânica.
(4) Dispositivos auxiliares
Os dispositivos auxiliares incluem principalmente o permutador automático de ferramentas (ATC), o permutador automático de paletes (APC), o mecanismo de fixação e libertação de peças, a mesa de trabalho rotativa, os dispositivos de lubrificação e refrigeração, o sistema automático de remoção de aparas e o sistema hidráulico, sistema pneumáticosistema elétrico, dispositivos de sobrecarga e de proteção, etc. Eles desempenham um papel importante na garantia da eficiência de trabalho, precisão de maquinação e fiabilidade de segurança do centro de maquinação.
2. Princípio de funcionamento dos centros de maquinagem
Para maquinar peças num centro de maquinagem, em primeiro lugar, com base no desenho da peça concebida e após a análise e conceção do processo de maquinagem, são necessárias várias operações durante o processo de maquinagem, como o arranque/paragem do fuso, a alteração da velocidade do fuso, os parâmetros de corte, o percurso de avanço, fluido de corte e o deslocamento relativo entre a ferramenta e a peça de trabalho, são escritos num programa de maquinagem utilizando códigos CNC especificados num determinado formato.
De seguida, a informação é transmitida ao sistema CNC através de um teclado ou de outros dispositivos de entrada. O computador no sistema CNC processa e calcula as instruções de programa recebidas, envia comandos para o sistema servo e outros circuitos de controlo auxiliares, fazendo-os executar a maquinação automática de acordo com a sequência de ação especificada, a trajetória de movimento da ferramenta e os parâmetros do processo de corte no programa. Quando a maquinação da peça está concluída, a máquina pára.
Quando o centro de maquinação tiver concluído a introdução do programa, a depuração e o corte experimental da primeira peça e entrar na produção em lote, o operador geralmente só precisa de carregar e descarregar peças de trabalho e, em seguida, premir o botão de início do ciclo automático do programa, e o centro de maquinação pode concluir automaticamente todo o processo de maquinação.
II. Classificação e utilização dos centros de maquinagem
1. Classificação dos centros de maquinagem
Existem muitas variedades de centros de maquinagem com diferentes formas, e existem vários métodos de classificação.
De acordo com a precisão da maquinação, podem ser divididos em centros de maquinação normais e centros de maquinação de alta precisão; de acordo com o número de eixos de coordenadas controláveis e eixos de coordenadas ligados, podem ser divididos em centros de maquinação de três eixos com três ligações, quatro eixos com três ligações, cinco eixos com quatro ligações e seis eixos com cinco ligações; de acordo com o número e a função das mesas de trabalho, podem ser divididos em centros de maquinação de mesa de trabalho única, centros de maquinação de mesa de trabalho dupla e centros de maquinação de mesa de trabalho múltipla, etc.
O método de classificação comum baseia-se na estrutura da máquina, geralmente dividida em centros de maquinação vertical, centros de maquinação horizontal, centros de maquinação de pórtico e centros de maquinação de cinco faces.
(1) Centro de maquinação vertical
Um centro de maquinação vertical refere-se a um centro de maquinação com um fuso colocado verticalmente, geralmente com três eixos de coordenadas e com capacidade de ligação de três eixos. Alguns centros de maquinação podem mesmo efetuar o controlo de cinco ou seis eixos, permitindo a maquinação de peças mais complexas.
A figura 1 mostra a vista exterior de um centro de maquinação vertical. A sua estrutura é frequentemente do tipo coluna fixa, com uma mesa de trabalho retangular sem função de rotação de indexação, adequada para maquinação de peças do tipo disco, manga e placa. Uma mesa rotativa CNC de eixo horizontal pode ser instalada na mesa de trabalho de um centro de maquinação vertical para maquinação de peças do tipo espiral.
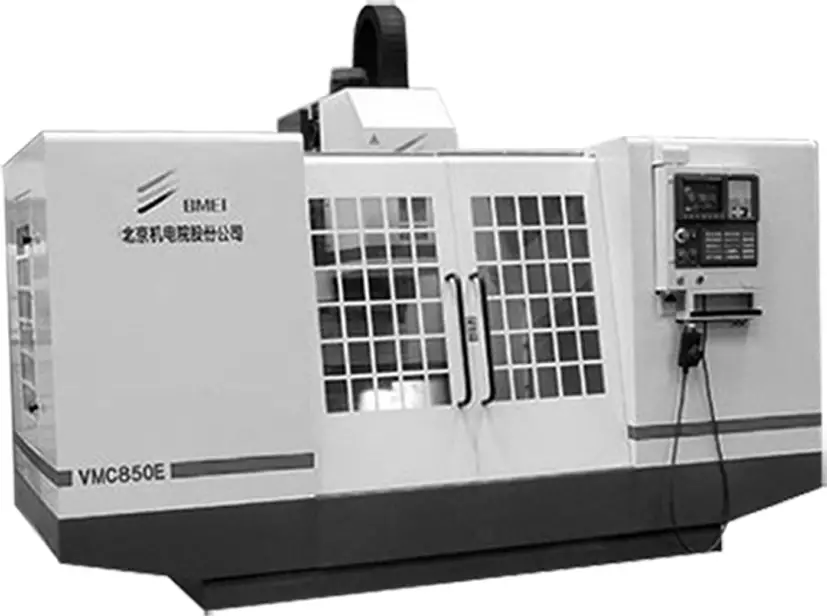
Os centros de maquinação vertical são convenientes para a fixação de peças, fáceis de observar, operar e depurar programas. Além disso, os centros de maquinagem verticais têm uma estrutura simples e compacta, uma pegada pequena e um preço relativamente baixo, pelo que têm sido amplamente utilizados.
No entanto, devido às limitações da altura da coluna e do dispositivo de troca de ferramentas, os centros de maquinação vertical não podem maquinar peças muito altas. Na maquinação de cavidades ou superfícies côncavas, a remoção de aparas é difícil, o que pode danificar seriamente as ferramentas e as superfícies maquinadas, afectando o bom andamento da maquinação.
(2) Centro de maquinagem horizontal
Um centro de maquinação horizontal refere-se a um centro de maquinação com um fuso colocado horizontalmente. A figura 2 mostra a vista exterior de um centro de maquinação horizontal.
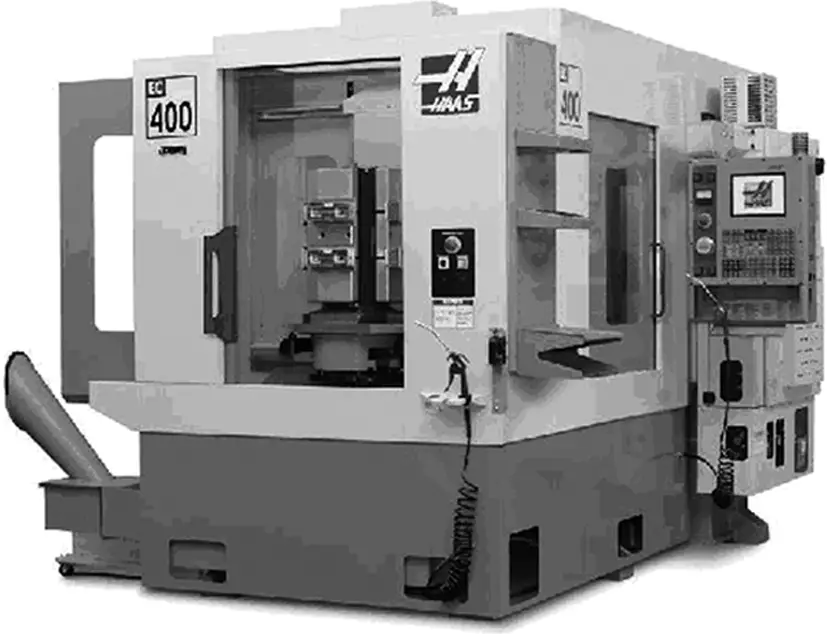
Os centros de maquinação horizontais têm geralmente 3 a 5 eixos de coordenadas, normalmente três eixos de coordenadas de movimento linear mais um eixo de coordenadas de movimento rotativo, permitindo que a peça de trabalho complete a maquinação em quatro lados, exceto a superfície de montagem e a superfície superior após uma única fixação. Em comparação com os centros de maquinação verticais, são mais adequados para a maquinação de peças tipo caixa, especialmente peças tipo caixa com requisitos de precisão de posição relativa entre furos e superfícies de referência de localização ou entre furos, facilitando a garantia da precisão da maquinação.
Os centros de maquinação horizontais são inconvenientes para a observação durante a depuração do programa e o corte experimental, e para a monitorização durante a maquinação. A fixação e a medição da peça de trabalho também não são convenientes, mas a remoção de aparas é fácil durante a maquinação, o que é benéfico para o processamento.
Em comparação com os centros de maquinagem verticais, os centros de maquinagem horizontais têm características como maior capacidade de armazenamento de ferramentas, estrutura geral mais complexa, maior volume e espaço no chão e preço mais elevado. Os centros de maquinação horizontais são o tipo de centro de maquinação mais utilizado.
(3) Centro de maquinação tipo pórtico
A forma de um centro de maquinação do tipo pórtico é semelhante a uma fresadora de pórtico, com o fuso normalmente colocado na vertical. Para além do dispositivo de troca automática de ferramentas, possui também acessórios de cabeça de fuso intercambiáveis, funções CNC abrangentes e pode ser utilizado para múltiplos fins. É especialmente adequada para o processamento de peças de trabalho de grandes dimensões ou de formas complexas, como se mostra na Figura 3.
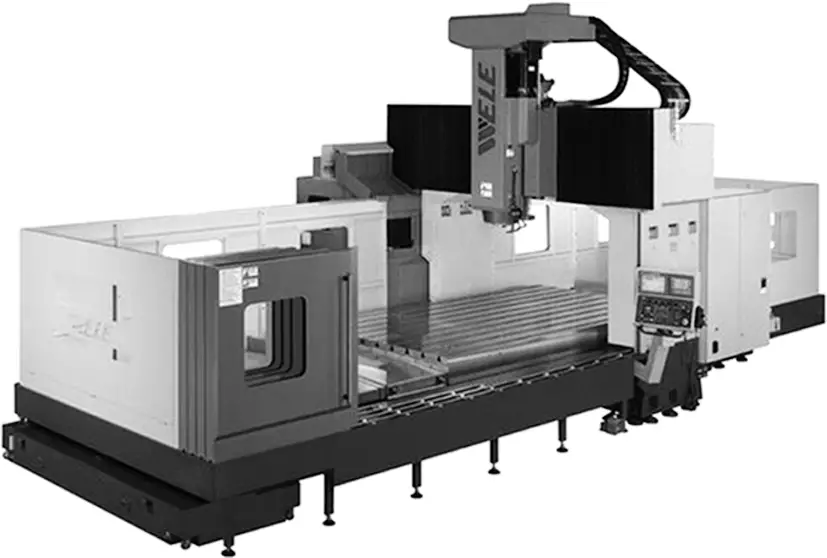
(4) Centro de maquinagem de cinco faces
O centro de maquinação de cinco faces é um centro de maquinação que combina as funções de centros de maquinação verticais e horizontais, ou seja, um centro de maquinação composto para utilização vertical e horizontal, como mostra a Figura 4.
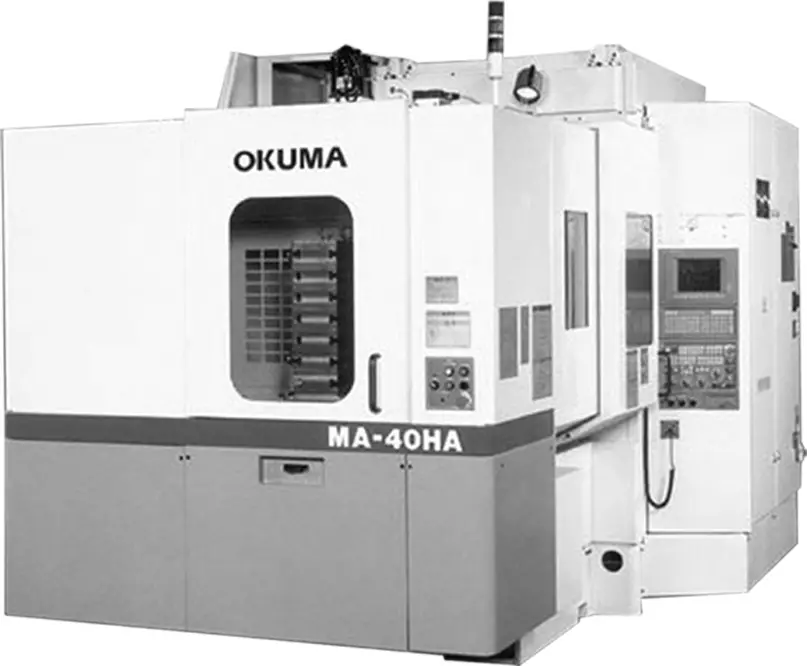
O centro de maquinação de cinco faces pode completar a maquinação de todos os cinco lados, exceto a superfície de montagem, após uma única instalação da peça de trabalho, melhorando consideravelmente a precisão da maquinação e a eficiência da produção, com benefícios económicos significativos.
Existem dois tipos comuns de centros de maquinação de cinco faces: um em que o fuso pode rodar 90° para obter uma maquinação vertical e horizontal; o outro em que o fuso não muda de direção, mas a mesa de trabalho rotativa CNC roda 90° ao longo do eixo X, rodando assim a peça de trabalho 90° para completar a maquinação de cinco superfícies da peça de trabalho.
2. Aplicações dos centros de maquinagem
Os centros de maquinação são caros, requerem um grande investimento inicial, têm custos de processamento de peças elevados e exigem operadores de alta qualidade. Por conseguinte, é necessário considerar exaustivamente quais as peças adequadas para serem processadas em centros de maquinagem, tendo em conta vários aspectos, como a forma e os requisitos de precisão.
De um modo geral, os centros de maquinagem são adequados para peças com formas complexas, requisitos de elevada precisão, processos múltiplos e peças que requerem vários tipos de máquinas-ferramentas convencionais e numerosas ferramentas e acessórios, e que só podem ser concluídas após várias configurações e ajustes.
(1) Peças do tipo caixa
As peças do tipo caixa referem-se geralmente a peças com mais do que um sistema de orifícios, uma certa cavidade interna e uma certa proporção em termos de comprimento, largura e altura. Estas peças são comuns em indústrias como a maquinaria, automóvel e aeroespacial, tais como blocos de motores de automóveis, caixas de caixas de velocidades, cabeçotes de máquinas-ferramenta, caixas de fusos, blocos de motores a diesel, caixas de bombas de engrenagens, etc.
As peças do tipo caixa requerem geralmente um sistema de furos em várias posições e maquinação plana, o que as torna um dos principais objectos de maquinação para centros de maquinação.
Os requisitos de tolerância, especialmente os requisitos de tolerância geométrica, são relativamente rigorosos, exigindo normalmente processos de fresagem, perfuração, alargamento, chanfragem, rosqueamento e outros. Uma única configuração pode completar 60% a 95% do conteúdo do processo das máquinas-ferramentas convencionais, resultando numa precisão consistente da peça, qualidade estável, ciclos de produção muito mais curtos e custos reduzidos.
Para peças com várias posições de maquinação que requerem várias rotações da mesa de trabalho para serem concluídas, os centros de maquinação horizontais são geralmente escolhidos; quando há menos posições de maquinação e o vão não é grande, os centros de maquinação verticais podem ser escolhidos para maquinação a partir de uma extremidade.
(2) Peças do tipo disco, manga e placa
Peças como discos, mangas ou veios com ranhuras ou furos radiais, ou com sistemas de furos distribuídos ou superfícies curvas na face final, por exemplo, mangas de veio flangeadas, veios com ranhuras ou cabeças quadradas, etc. Além disso, existem peças do tipo placa com maquinação de múltiplos furos, tais como várias coberturas de motores.
Para peças do tipo disco, manga e placa com sistemas de orifícios distribuídos ou superfícies curvas na face final, os centros de maquinação verticais são adequados, enquanto os centros de maquinação horizontais podem ser escolhidos para aqueles com orifícios radiais.
(3) Peças com formas estruturais complexas e requisitos de elevada precisão
As peças com formas estruturais complexas têm frequentemente múltiplas superfícies de maquinagem compostas por superfícies curvas complexas, exigindo normalmente uma maquinagem de ligação multi-coordenada, que é geralmente difícil ou impossível de realizar em máquinas-ferramentas convencionais.
Superfícies curvas complexas, tais como superfícies de perfil de aeronaves e automóveis, impulsores, hélices e vários moldes de formação de superfícies curvas ocupam uma posição importante na indústria de fabrico mecânico, especialmente nas indústrias aeroespacial, automóvel, de construção naval e de defesa. Os centros de maquinação são geralmente escolhidos para processar este tipo de peças, que são também os principais objectos de maquinação das máquinas-ferramentas CNC normais.
As peças típicas incluem peças do tipo came, peças do tipo impulsor integral e peças do tipo molde. A escolha de centros de maquinação para o processamento de peças de lotes médios e pequenos com requisitos de alta precisão pode alcançar uma boa precisão dimensional e de posição de forma, com boa consistência dimensional e qualidade estável.
Na maquinação de superfícies curvas complexas, se não existirem zonas de interferência de maquinação ou pontos cegos, as fresas esféricas podem ser utilizadas para maquinação com três coordenadas. Isto resulta numa elevada precisão de maquinação mas numa eficiência relativamente baixa. Se existirem zonas de interferência de maquinação ou pontos cegos na peça, é necessário considerar a utilização de máquinas-ferramentas de ligação de quatro ou cinco coordenadas.
A vantagem da troca automática de ferramentas nos centros de maquinação não pode ser totalmente utilizada na maquinação de superfícies curvas complexas, uma vez que a maquinação de superfícies curvas complexas passa geralmente por etapas desde a fresagem em desbaste até à fresagem de acabamento (semi), utilizando menos ferramentas, especialmente na maquinação de uma peça única, como moldes.
(4) Peças com formas irregulares
As peças de formato irregular são componentes com formas externas irregulares e a maioria requer maquinação mista em várias posições com pontos, linhas e superfícies, tais como suportes, bases, modelos e gabaritos. As peças com formas irregulares têm geralmente pouca rigidez, fixação complexa, são propensas a deformação durante o corte e é difícil garantir a precisão da maquinação.
Se forem utilizadas máquinas-ferramentas convencionais para a maquinação, existem muitos processos, várias instalações, longos tempos de processamento e é difícil garantir a qualidade da maquinação. Neste caso, a caraterística de concentração de processos dos centros de maquinação pode ser totalmente utilizada, adoptando medidas de processo adequadas para completar a maior parte ou todo o conteúdo da maquinação numa ou duas configurações num tempo relativamente curto.
Na maquinação de peças com formas irregulares, quanto mais complexa for a forma e quanto maiores forem os requisitos de precisão, mais as vantagens dos centros de maquinação podem ser apresentadas e utilizadas. Ao utilizar centros de maquinação para maquinar peças, o tempo gasto na preparação do processo e na edição do programa representa uma grande parte do tempo total de trabalho. Portanto, para a produção cíclica de peças em lote, o mesmo programa pode ser usado repetidamente muitas vezes, encurtando muito o ciclo de produção.
III. Características de maquinagem e gama de aplicações dos centros de maquinagem
1. Características de maquinagem dos centros de maquinagem
Em comparação com as máquinas-ferramentas CNC convencionais, os centros de maquinagem têm as seguintes características notáveis.
(1) Concentração de processos
Os centros de maquinagem têm armazéns de ferramentas e dispositivos de troca automática de ferramentas. Após a configuração de uma única peça, o sistema CNC pode controlar a máquina para selecionar e mudar automaticamente as ferramentas de acordo com diferentes processos, alterar automaticamente a velocidade do fuso da máquina, a taxa de avanço, a trajetória do movimento da ferramenta em relação à peça e outras funções auxiliares. Pode executar continuamente vários processos, tais como fresagem, perfuração, alargamento, mandrilagem e rosqueamento em várias superfícies de usinagem da peça de trabalho automaticamente, adequado para usinagem de peças de superfície complexas, como cames, caixas, suportes, placas de cobertura e moldes.
(2) Elevada precisão de maquinagem
Tal como outras máquinas-ferramentas CNC, os centros de maquinação têm a caraterística de elevada precisão de maquinação. Além disso, devido à concentração dos processos de maquinação, os centros de maquinação evitam longos fluxos de processo e reduzem a interferência humana, resultando numa precisão de maquinação ainda maior e numa qualidade de maquinação mais estável.
(3) Forte adaptabilidade na maquinagem
Os centros de maquinação têm uma forte adaptabilidade aos objectos a maquinar, ou seja, uma elevada flexibilidade. A flexibilidade de produção dos centros de maquinação reflecte-se não só na resposta rápida a requisitos especiais, mas também na capacidade de atingir rapidamente a produção em lote, melhorando assim a competitividade do mercado.
(4) Redução da intensidade do trabalho e melhoria das condições de trabalho
Os centros de maquinação processam peças automaticamente de acordo com rotinas pré-programadas, completando a maquinação de peças. Os operadores só precisam de operar o painel de controlo, carregar e descarregar peças de trabalho, definir ferramentas, realizar inspecções intermédias para processos-chave e observar o funcionamento da máquina, sem a necessidade de operações manuais repetitivas pesadas. Isto reduz significativamente a intensidade e a tensão do trabalho e também melhora as condições de trabalho.
(5) Elevada eficiência de produção
Os centros de maquinagem estão equipados com armazéns de ferramentas e dispositivos de troca automática de ferramentas. Alguns centros de maquinagem também têm capacidades de troca automática de estações de trabalho. Vários processos podem ser concentrados numa única máquina, reduzindo o tempo de preparação da peça, de medição e de ajuste da máquina, bem como reduzindo o tempo de transferência, manuseamento e armazenamento de produtos semi-acabados, diminuindo consideravelmente o tempo auxiliar e melhorando a eficiência da produção.
(6) Boas vantagens económicas
Ao utilizar centros de maquinação para processar peças, o custo do equipamento atribuído a cada peça é dispendioso. No entanto, a sua elevada eficiência de produção, elevada precisão de maquinação e maquinação estável reduzem a taxa de refugo, e os baixos custos do equipamento de processamento resultam em custos de produção muito reduzidos, obtendo assim bons benefícios económicos.
(7) Facilita a modernização da gestão da produção
A utilização de centros de maquinação para processar peças permite o cálculo exato do tempo de processamento das peças e simplifica eficazmente a inspeção, a gestão de ferramentas e acessórios e a gestão de produtos semi-acabados, o que conduz à modernização da gestão da produção.
Embora os centros de maquinação tenham as vantagens acima referidas, são caros, tecnicamente complexos, difíceis de manter, têm custos de processamento elevados e requerem pessoal de gestão e operação de alta qualidade. Por conseguinte, vários factores devem ser considerados de forma abrangente para obter os melhores benefícios económicos para a empresa.
2. Gama de aplicações dos centros de maquinagem
Os centros de maquinação são máquinas-ferramentas de alta eficiência, alta precisão e altamente automatizadas com muitas vantagens que as máquinas-ferramentas comuns não conseguem igualar. Atualmente, a gama de aplicações dos centros de maquinação está em constante expansão. Para explorar plenamente os melhores benefícios dos centros de maquinagem, estes são mais adequados para o processamento de peças com as seguintes características.
(1) Peças de produção de lotes pequenos e multi-variedades
A flexibilidade de produção dos centros de maquinação reflecte-se não só na resposta rápida ao processamento de peças especiais, mas também na capacidade de atingir rapidamente a produção em lotes e conquistar rapidamente a quota de mercado.
(2) Peças com formas e estruturas complexas
Algumas peças têm formas e estruturas complexas que requerem equipamento de processamento dispendioso quando maquinadas em máquinas-ferramentas convencionais. Mesmo a utilização de máquinas de fresagem CNC requer várias mudanças de ferramentas e dispositivos, enquanto que a utilização de um centro de maquinação pode realizar vários processos, tais como fresagem, perfuração, mandrilagem e roscagem numa única configuração.
(3) Peças caras e de alta precisão
Algumas peças têm pouca procura mas são caras e são componentes críticos que não podem ser eliminados. Exigem uma elevada precisão e um tempo de produção curto. Se forem utilizadas máquinas-ferramentas tradicionais para o processamento, é necessário que várias máquinas coordenem o trabalho e é fácil produzir produtos defeituosos devido a factores humanos.
Ao utilizar centros de maquinação para o processamento, o processo de produção é inteiramente controlado por programas, evitando factores de interferência no fluxo do processo, resultando numa elevada eficiência de produção e numa qualidade estável.
(4) Peças de produção repetidas ciclicamente
Alguns produtos têm uma procura cíclica e sazonal no mercado. A utilização de linhas de produção especializadas não seria rentável. A utilização de equipamento normal resulta numa baixa eficiência de processamento e numa qualidade instável. No entanto, ao utilizar um centro de maquinação, depois de a primeira peça ser cortada com sucesso, o programa e a informação relacionada podem ser guardados. Da próxima vez que o produto for produzido, a produção pode começar com um tempo mínimo de preparação.
(5) Peças que requerem modificações frequentes
Quando o objeto de processamento muda, apenas o programa de processamento tem de ser modificado e os parâmetros da ferramenta ajustados para processar novas peças. Isto reduz significativamente o ciclo de preparação da produção e proporciona um atalho para o desenvolvimento de novos produtos, melhoramento de produtos e modificações.
(6) Peças difíceis de medir
Para algumas peças difíceis de medir, as características de alta precisão do próprio centro de maquinação podem ser totalmente utilizadas para garantir a precisão do processamento das peças.
IV. Estrutura principal e parâmetros técnicos dos centros de maquinagem
1. Componentes do fuso
O componente do fuso é uma das partes mais importantes de um centro de maquinação. A sua rigidez e precisão de rotação afectam diretamente a qualidade de processamento da peça de trabalho. O componente do fuso consiste principalmente na caixa do fuso, no motor do fuso, no fuso e nos rolamentos do fuso.
O motor do fuso de um centro de maquinagem utiliza principalmente motores de fuso CC e motores de fuso CA para obter uma variação de velocidade contínua do movimento principal. As acções de arranque, paragem e mudança de velocidade do fuso são todas controladas pelo sistema CNC, e o corte é efectuado através de ferramentas montadas no fuso, que é o componente de saída de potência para operações de corte.
2. Sistema de apoio
(1) Cama
A cama é a base da máquina-ferramenta, exigindo uma rigidez estática e dinâmica suficientemente elevada e uma retenção de precisão. Ao mesmo tempo que se cumprem os requisitos gerais de conceção, devem ser feitos esforços para obter uma estrutura razoável, uma disposição adequada das nervuras e garantir uma boa tecnologia de processamento a frio e a quente.
Para centros de maquinagem de torneamento, é geralmente utilizada uma base inclinada para melhorar a rigidez. A base inclinada pode melhorar a condição de força durante o corte, e a secção transversal pode formar uma estrutura de cavidade fechada. O seu interior pode ser preenchido com núcleos de lama e betão como materiais de amortecimento, que dissipam a energia de vibração através do desgaste relativo durante a vibração.
(2) Coluna
A coluna de um centro de maquinagem suporta principalmente a caixa do fuso e acomoda o movimento do eixo Z do fuso. A coluna deve ter uma boa rigidez e estabilidade térmica. Os centros de maquinação utilizam uma estrutura de caixa fechada, com placas internas inclinadas para melhorar a resistência da coluna à flexão e à torção. Toda a estrutura é obtida através de fundição.
(3) Guias
A maioria dos centros de maquinação utiliza guias lineares de rolamento. As guias de rolamento têm coeficientes de atrito muito baixos e pequenas diferenças entre os coeficientes de atrito estático e dinâmico. Proporcionam um movimento suave a baixa velocidade sem rastejar, alcançando assim uma elevada precisão de posicionamento.
No entanto, a obtenção desta precisão deve basear-se no estado correto da base. Caso contrário, os erros de altura do suporte vertical causarão distorção lateral estrutural, levando a alterações na resistência de fricção ao longo da gama de deslocação, resultando em erros de precisão de posicionamento.
No passado, quando eram utilizadas guias deslizantes, as superfícies de contacto das guias necessitavam de ser raspadas e afinadas. Durante a montagem, a distorção da guia podia ser detectada e corrigida através de ajustes. Com as guias de rolamento, não há processo de correção, o que torna difícil evitar a distorção do leito ou a distorção da via causada pela instalação. Por conseguinte, deve ser utilizada uma base de apoio de três pontos.
3. Sistema servo
(1) Sistema servo do fuso
Com o desenvolvimento da tecnologia CNC, as máquinas-ferramentas CNC modernas têm requisitos cada vez mais elevados para a transmissão do fuso. Por exemplo, requerem uma velocidade continuamente ajustável numa vasta gama, uma vasta gama de potência constante e capacidade de acionamento em quatro quadrantes. Para satisfazer as necessidades de troca automática de ferramentas e certas tecnologias de processamento em centros de maquinação, é necessário um controlo de orientação de alta precisão do fuso.
Atualmente, a variação da velocidade de acionamento do fuso adopta principalmente duas formas: uma é o motor do fuso com variação de velocidade contínua segmentada por engrenagem; a outra é o motor do fuso que acciona o fuso através de uma correia dentada síncrona ou correia de transmissão. Este último tipo de motor de fuso é também designado por motor de gama larga ou motor de corte pesado, caracterizado por uma vasta gama de potência constante.
O controlo da orientação do fuso divide-se em orientação mecânica e orientação eléctrica. Atualmente, todos os sistemas CNC nacionais e estrangeiros de média e alta gama adoptam o controlo da orientação eléctrica.
1) Sistema de acionamento do fuso DC.
Os accionamentos de fuso CC utilizam frequentemente métodos de controlo de velocidade por tiristores. O sistema servo de alimentação CC é um sistema de controlo de circuito duplo composto por um circuito de velocidade e um circuito de corrente para controlar a tensão da armadura do motor do fuso CC. O motor do fuso utiliza um motor excitado separadamente, com o enrolamento de excitação e o enrolamento da armadura independentes um do outro.
Desde o valor mínimo até ao valor nominal da velocidade do motor, a corrente de excitação permanece constante, obtendo-se um controlo de velocidade regulado por tensão, que pertence ao controlo de binário constante. Desde o valor nominal até ao valor máximo, a corrente de excitação diminui, obtendo-se um controlo de velocidade regulado por fluxo magnético, que pertence ao controlo de potência constante.
2) Sistema de acionamento do fuso AC.
Com o desenvolvimento da tecnologia de controlo da velocidade AC, o acionamento do fuso das máquinas-ferramentas CNC adopta agora, na sua maioria, o método de controlo do motor do fuso com conversor de frequência. O inversor do lado da rede eléctrica é constituído por um circuito retificador trifásico totalmente controlado por ponte, composto por seis tiristores. Este circuito pode funcionar em estado de retificação, fornecendo diretamente energia ao circuito intermédio, e pode também funcionar em estado de inversor, completando a tarefa de retorno de energia à rede eléctrica.
O inversor do lado da carga é composto por seis transístores de potência com díodos de roda livre antiparalelos. Através do controlo do computador do campo magnético, o inversor do lado da carga produz uma tensão de modulação de largura de impulso sinusoidal trifásica (PWM), permitindo que o motor obtenha a corrente de binário e a corrente de excitação necessárias.
A gama de amplitude da tensão PWM trifásica de saída é de 0-430V, com uma gama de ajuste de frequência de 0-300Hz. Durante a travagem regenerativa, a energia do motor carrega o condensador através dos seis díodos de roda livre do conversor. Quando a tensão no condensador excede os 600V, a energia no condensador é devolvida à rede eléctrica através do controlo do regulador e do inversor do lado da rede.
(2) Sistema servo de alimentação
1) Sistema servo de alimentação por modulação de largura de impulsos.
O método de controlo de velocidade por modulação de largura de impulsos controla o tempo de comutação de transístores de alta potência utilizando um modulador de largura de impulsos. Este converte o sinal de controlo de velocidade numa tensão de onda quadrada de uma determinada frequência, que é aplicada aos terminais da armadura do servomotor CC. Ao controlar a largura da onda quadrada, a tensão média nos terminais da armadura é alterada, atingindo assim o objetivo de controlar a velocidade do servomotor.
A CPU do sistema CNC emite uma série de sinais de impulsos através do interpolador. Estes impulsos, depois de passarem pelo multiplicador de comando CMR, são comparados com os impulsos de feedback de posição. A diferença resultante é enviada para o registo de erros, depois calculada com compensação de ganho e desvio de posição, e enviada para o PWM para modulação de largura de impulsos. Subsequentemente, é convertida em D/A ou tensão analógica e enviada para a unidade de controlo de velocidade como o sinal de controlo de velocidade VCMD.
Os impulsos do codificador de impulsos, depois de confirmada a ausência de desconexão do sinal pelo detetor de desconexão, são enviados para o detetor de fases para determinar o sentido de rotação do motor através da análise dos dois grupos de impulsos PA e PB.
Um sinal do detetor de fase sofre conversão F/V para se tornar o sinal de feedback de velocidade TSA; a outra saída passa pelo multiplicador de deteção DMR para se tornar o sinal de feedback de posição. O contador do ponto de referência e o sinal de uma volta PC são utilizados para a operação de retorno do ponto de referência do método de grelha.
2) Sistema servo de acionamento de alimentação AC.
Embora os sistemas servo de alimentação CC tenham excelentes funções de regulação de velocidade, os motores utilizados têm escovas e comutadores que são propensos ao desgaste. Além disso, as faíscas produzidas durante a comutação limitam a velocidade máxima do motor.
Além disso, os motores de corrente contínua têm estruturas complexas, são difíceis de fabricar, consomem grandes quantidades de materiais de cobre e ferro e têm custos de fabrico elevados. Os motores de corrente alternada, no entanto, não apresentam estes inconvenientes.
Nos últimos 20 anos, com o aparecimento de novos dispositivos electrónicos de alta potência, os avanços na nova tecnologia de conversão de frequências, a moderna teoria de controlo e a tecnologia de controlo digital por microcomputador em aplicações práticas promoveram o rápido desenvolvimento da tecnologia servo de alimentação CA. Os sistemas servo de alimentação CA substituíram completamente os sistemas servo de alimentação CC.
Uma vez que os servomotores CA utilizam motores síncronos de ímanes permanentes CA, o dispositivo de acionamento de alimentação CA é essencialmente um dispositivo de acionamento de motor CC comutado eletronicamente.
4. Armazém de ferramentas e dispositivo de troca automática de ferramentas
Os centros de maquinação utilizam armazéns de ferramentas para realizar a troca de ferramentas, que é atualmente o método de troca de ferramentas mais utilizado nos centros de maquinação. Com o magazine de ferramentas, a máquina só precisa de um fuso fixo para segurar as ferramentas, o que é benéfico para melhorar a rigidez do fuso.
Um armazém de ferramentas independente aumenta consideravelmente a capacidade de armazenamento de ferramentas, o que é benéfico para expandir a funcionalidade da máquina e pode isolar melhor vários factores que afectam a precisão da maquinação.
A troca de ferramentas com um magazine de ferramentas pode ser dividida em duas categorias com base no facto de um braço mecânico estar envolvido no processo: troca de ferramentas com um braço mecânico e troca de ferramentas sem um braço mecânico. No processo de troca de ferramentas com um braço mecânico, um braço mecânico retira a ferramenta acabada do fuso, enquanto simultaneamente outro braço mecânico retira a ferramenta em espera do armazém de ferramentas. Em seguida, os dois trocam de posição para completar o processo de troca de ferramenta.
Para a troca de ferramentas sem um braço mecânico, as ferramentas no armazém são armazenadas paralelamente ao fuso, e as ferramentas são colocadas numa posição acessível pelo fuso. Durante a troca de ferramentas, a cabeça do fuso desloca-se para a posição de troca de ferramentas acima do armazém. Utilizando o movimento do eixo Z do fuso, a ferramenta acabada é inserida na posição vazia necessária no magazine. De seguida, a ferramenta em espera no armazém roda para a posição de espera. O mandril desloca-se na direção Z para retirar a ferramenta em espera do armazém e introduzi-la no mandril.
Os sistemas com braços mecânicos são mais flexíveis em termos de configuração do depósito de ferramentas, posição relativa ao fuso e número de ferramentas, com tempos de mudança de ferramentas mais curtos. O método sem braços mecânicos tem uma estrutura mais simples mas tempos de mudança de ferramenta mais longos.
(1) Tipos de magazines de ferramentas de centros de maquinagem
Existem vários tipos de magazines de ferramentas, sendo os do tipo disco e do tipo corrente os mais utilizados nos centros de maquinagem.
Na estrutura do disco (ver Figura 5), as ferramentas podem ser armazenadas ao longo do eixo do fuso, radialmente ou em ângulo. A instalação axial de ferramentas é a mais compacta, mas para que a troca de ferramentas se alinhe com o fuso, algumas ferramentas no magazine precisam de ser rodadas 90° na posição de troca de ferramentas.
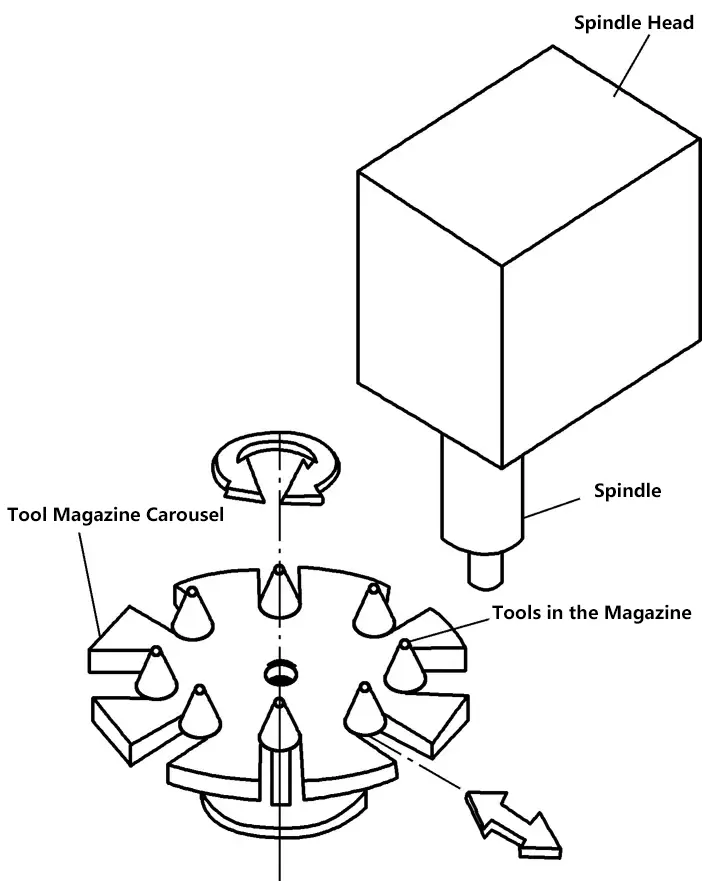
Para grandes capacidades de armazém de ferramentas, pode ser adoptada uma estrutura do tipo tambor para facilitar o armazenamento e a recuperação, mantendo uma estrutura compacta. Atualmente, muitos armazéns de ferramentas são instalados na parte superior ou lateral da coluna da máquina, e alguns são instalados em fundações separadas para isolar as vibrações causadas pela rotação do armazém de ferramentas.
A estrutura básica de um carregador de ferramentas do tipo corrente é mostrada na Figura 6. Normalmente, tem uma maior capacidade de ferramentas do que um carregador do tipo disco e uma estrutura mais flexível. A capacidade do armazém de ferramentas pode ser aumentada através da extensão da corrente, ou a utilização do espaço pode ser melhorada através da dobragem e rebobinagem da corrente. Para requisitos de capacidade de ferramentas muito grandes, podem também ser adoptadas estruturas de correntes múltiplas.
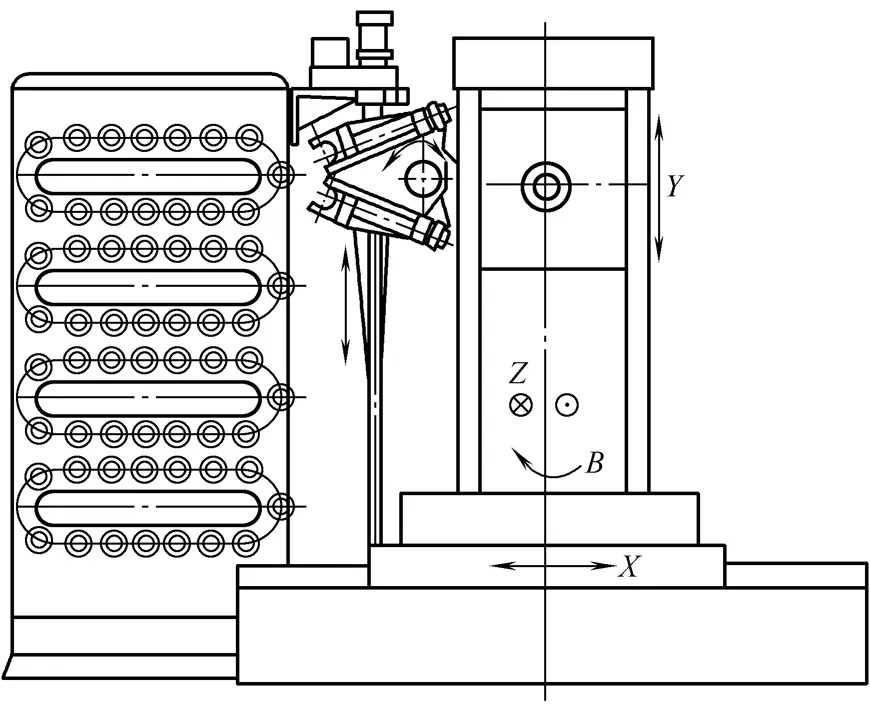
(2) Trocador automático de ferramentas para centros de maquinagem
Os trocadores automáticos de ferramentas podem ser divididos em cinco formas básicas: tipo torre, tipo de rotação de 180°, tipo de inserção rotativa, tipo de rotação de dois eixos e tipo de fuso direto. As ferramentas para troca automática de ferramentas podem ser fixadas em porta-ferramentas especiais, e cada vez que uma ferramenta é trocada, o porta-ferramentas é diretamente inserido no fuso.
1) Trocador de ferramentas tipo torre.
A utilização de uma torreta para mudar as ferramentas é a forma mais antiga de mudança automática de ferramentas. Como se mostra na Figura 7, a torre consiste em vários fusos ligados à cabeça de potência da máquina de fresar (caixa de fusos). Antes de executar o programa, as ferramentas são instaladas nos fusos, e quando uma ferramenta específica é necessária, a torre gira para a posição correspondente.
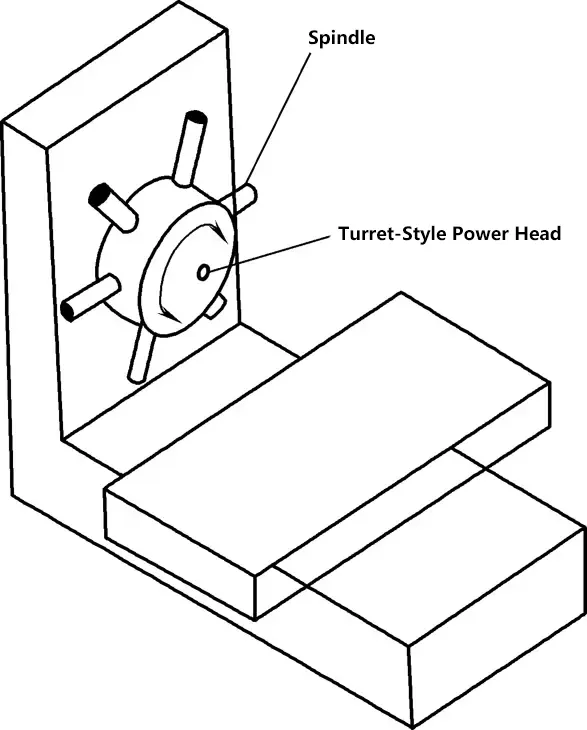
A desvantagem deste dispositivo é que o número de fusos é limitado. Ao usar mais ferramentas do que o número de fusos, o operador deve remover as ferramentas usadas e instalar as ferramentas necessárias para os programas subsequentes. A troca de ferramentas do tipo torreta não envolve a desmontagem da ferramenta, mas sim a troca da ferramenta e do porta-ferramentas em conjunto, pelo que este método de troca de ferramentas é muito rápido. Atualmente, as máquinas de perfuração NC e outras ainda utilizam magazines de ferramentas do tipo torreta.
2) Trocador de ferramentas com rotação de 180°.
O trocador de ferramentas mais simples é o trocador de ferramentas do tipo rotação de 180°, como mostrado na Figura 8.
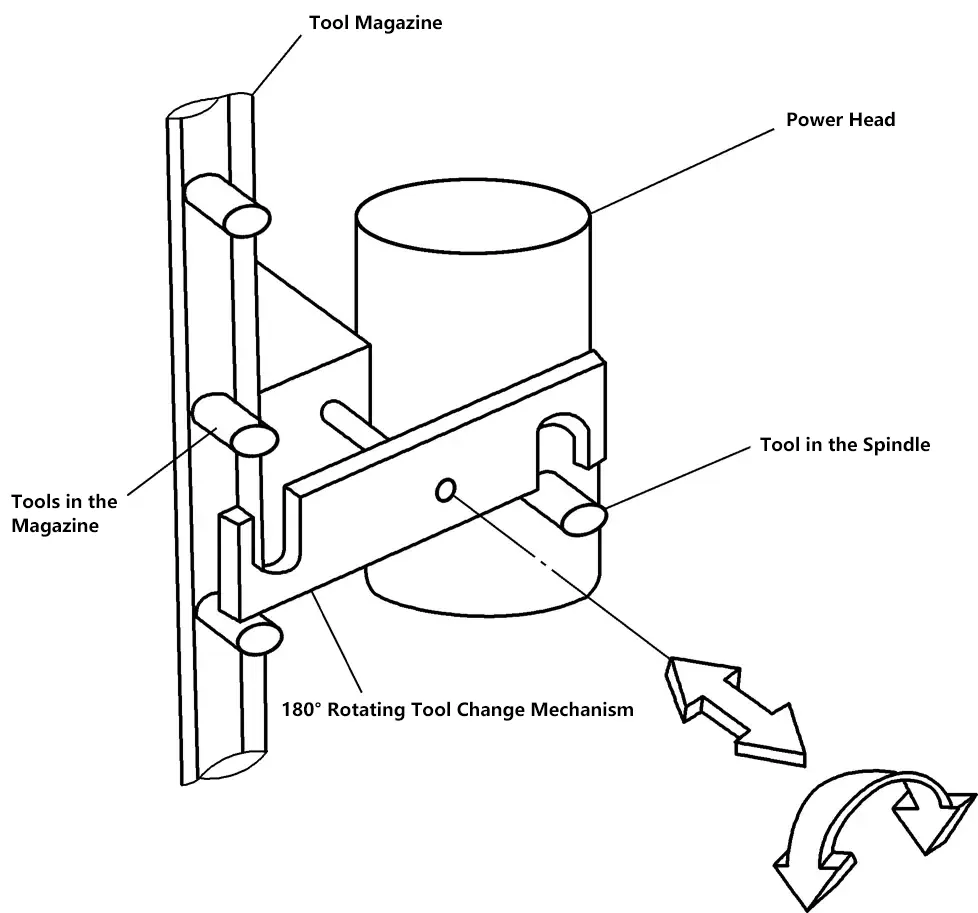
Ao receber um comando de troca de ferramenta, o sistema de controlo da máquina move o fuso para a posição de troca de ferramenta especificada; simultaneamente, o armazém de ferramentas move-se para a posição apropriada, e o trocador de ferramentas roda e engata no fuso e na ferramenta no armazém de ferramentas.
A barra de tração liberta a ferramenta do fuso e o trocador de ferramentas retira as ferramentas das respectivas posições; o trocador de ferramentas roda 180° e retira a ferramenta do fuso e a ferramenta do armazém.
À medida que o trocador de ferramentas gira, o magazine de ferramentas reajusta sua posição para receber a ferramenta removida do fuso; em seguida, o trocador de ferramentas instala a nova ferramenta no fuso e a ferramenta removida no magazine de ferramentas; finalmente, o trocador de ferramentas retorna à sua posição original de "standby".
Neste ponto, a troca de ferramentas está completa e o programa continua a ser executado. A principal vantagem deste trocador de ferramentas é a sua estrutura simples, o menor número de movimentos envolvidos e a rápida troca de ferramentas; a principal desvantagem é que as ferramentas devem ser armazenadas num plano paralelo ao fuso e, em comparação com os armazéns de ferramentas montados lateralmente e montados na parte traseira, as limalhas e o fluido de corte podem entrar facilmente no porta-ferramentas, pelo que é necessária uma proteção adicional para as ferramentas.
As aparas na superfície cónica do porta-ferramentas podem causar erros na troca de ferramentas e até danificar potencialmente o porta-ferramentas e o fuso. Alguns centros de maquinação utilizam uma barra de transferência e colocam o armazém de ferramentas na lateral.
Quando é acionado um comando de troca de ferramenta, a barra de transferência retira a ferramenta do armazém de ferramentas, roda para a frente da máquina e posiciona-se para encaixar no trocador de ferramentas. O trocador de ferramentas do tipo rotação de 180° pode ser utilizado tanto em máquinas horizontais como verticais.
3) Trocador de ferramentas rotativo do tipo inserção.
Esta é uma das formas mais utilizadas e é uma versão melhorada do alternador de ferramentas do tipo rotativo. O mecanismo de inserção rotativa é uma combinação de um trocador de ferramentas e uma barra de transferência. A Figura 9 mostra o princípio de funcionamento de um trocador de ferramentas do tipo inserção rotativa aplicado a um centro de maquinação horizontal. O design estrutural deste trocador de ferramentas é basicamente o mesmo que o do trocador de ferramentas do tipo rotativo de 180°.
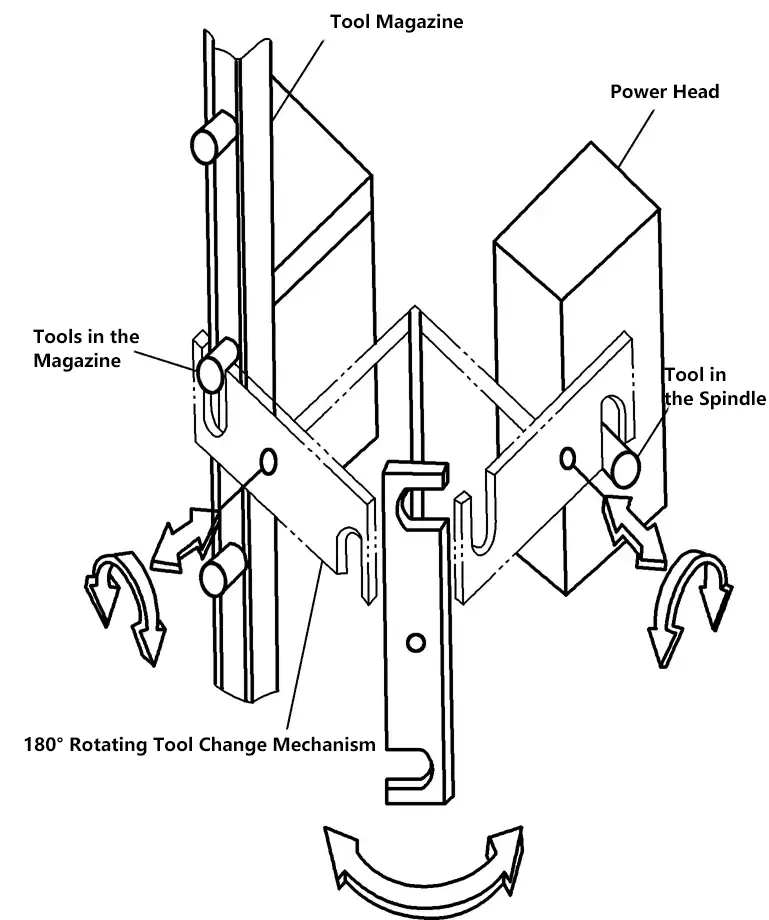
Quando é recebido um comando de troca de ferramenta, o fuso desloca-se para o ponto de troca de ferramenta, o armazém de ferramentas roda para a posição apropriada, permitindo ao trocador de ferramentas retirar a ferramenta desejada da sua ranhura; o trocador de ferramentas roda e retira a ferramenta do armazém de ferramentas localizado na lateral da máquina, o trocador de ferramentas roda para a frente da máquina, onde retira a ferramenta do fuso, roda 180° e instala a nova ferramenta no fuso.
Entretanto, o armazém de ferramentas desloca-se para a posição adequada para receber a ferramenta retirada do fuso; o trocador de ferramentas roda para o lado da máquina e coloca a ferramenta retirada do fuso na ranhura do armazém de ferramentas.
A principal vantagem deste dispositivo é o facto de as ferramentas serem armazenadas na parte lateral da máquina, evitando a possibilidade de as limalhas danificarem o fuso ou o porta-ferramentas. Em comparação com o trocador de ferramentas do tipo rotação de 180°, sua desvantagem é que há mais ações durante o processo de troca de ferramentas, resultando em um tempo maior de troca de ferramentas.
4) Trocador de ferramentas do tipo rotação de dois eixos.
A figura 10 mostra o princípio de funcionamento de um trocador de ferramentas do tipo rotação de dois eixos. Este trocador de ferramentas pode ser usado com magazines de ferramentas montados na lateral ou na traseira, e suas características estruturais são mais adequadas para centros de usinagem verticais.
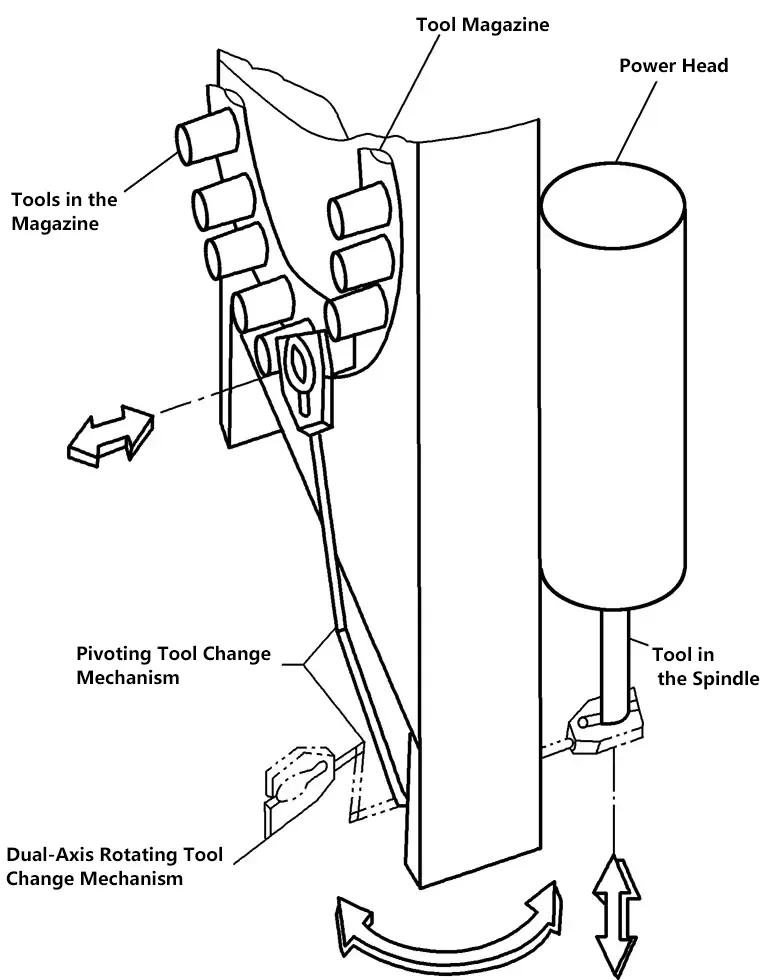
Ao receber um comando de mudança de ferramenta, o mecanismo de mudança de ferramenta começa a mover-se a partir da posição de "espera", agarra a ferramenta no fuso e retira-a, roda para o armazém de ferramentas e devolve a ferramenta ao armazém de ferramentas; em seguida, recupera a ferramenta desejada do armazém de ferramentas, roda em direção ao fuso e instala a ferramenta no fuso; finalmente, regressa à posição de "espera", completando a mudança de ferramenta.
A principal vantagem deste dispositivo é que o armazém de ferramentas está localizado na parte lateral ou traseira da máquina, proporcionando a máxima proteção para as ferramentas. A sua desvantagem é o facto de haver mais transferências e movimentos de ferramentas. Este dispositivo nos centros de maquinação verticais tem vindo a ser gradualmente substituído por trocadores de ferramentas do tipo rotação de 180º e do tipo fuso direto.
5) Trocador de ferramentas de tipo fuso direto.
O trocador de ferramentas do tipo fuso direto é diferente de outras formas de trocadores de ferramentas. Neste dispositivo, ou o magazine de ferramentas se desloca diretamente para a posição do fuso, ou o fuso se desloca diretamente para o magazine de ferramentas. A Figura 11 mostra a aplicação de um trocador de ferramentas do tipo fuso direto em um centro de usinagem horizontal.
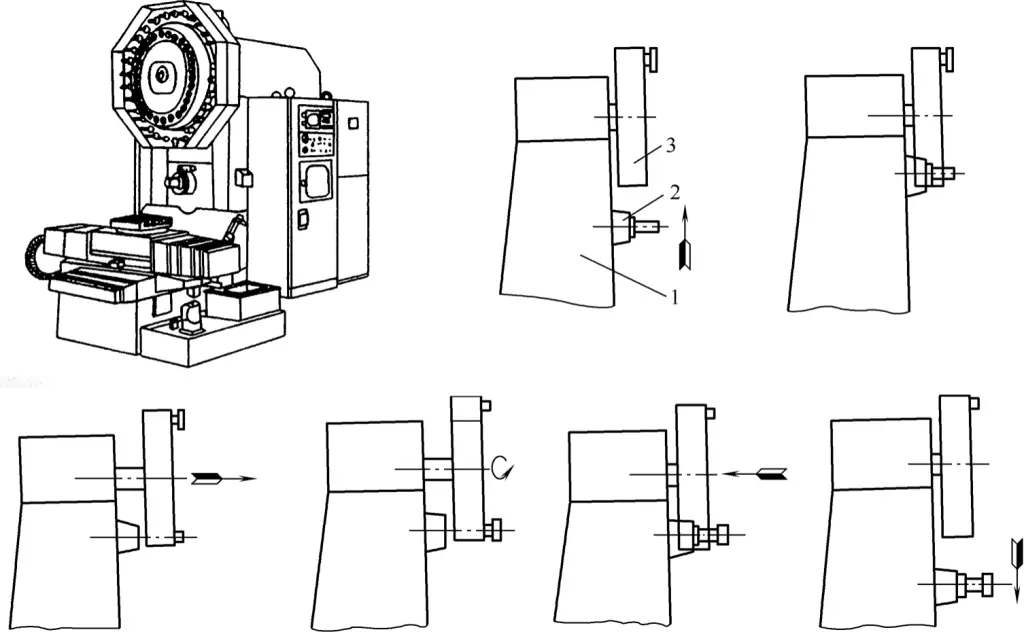
1-Coluna principal
Caixa de 2 fusos
Carregador de 3 ferramentas
Durante a troca de ferramenta, o fuso move-se para a posição de troca de ferramenta, o magazine de ferramentas tipo disco roda para a posição da ranhura da ferramenta necessária e move a ferramenta da posição de "espera" para a posição de troca de ferramenta, encaixando no suporte de ferramenta instalado no fuso.
A barra de tração retira-se do porta-ferramentas, o armazém de ferramentas avança e retira a ferramenta; em seguida, o armazém de ferramentas roda para alinhar a ferramenta pretendida com o fuso, desloca-se para trás, introduz a ferramenta no fuso e fixa-a; finalmente, o armazém de ferramentas afasta-se do fuso, desloca-se para cima e regressa à posição de "espera", concluindo a troca de ferramentas.
No caso dos centros de maquinação vertical, os mais pequenos geralmente efectuam as mudanças de ferramentas movendo o armazém de ferramentas; em algumas máquinas de grande dimensão, o processo de mudança de ferramentas é diferente do acima descrito, uma vez que o armazém de ferramentas é demasiado grande para ser movido convenientemente, pelo que o fuso se move para remover e instalar ferramentas ou é utilizado um braço robótico para as mudanças de ferramentas.
A figura 12 mostra a estrutura de um braço robótico e de uma pinça e a figura 13 mostra o processo de trabalho de uma mudança de ferramenta robótica.
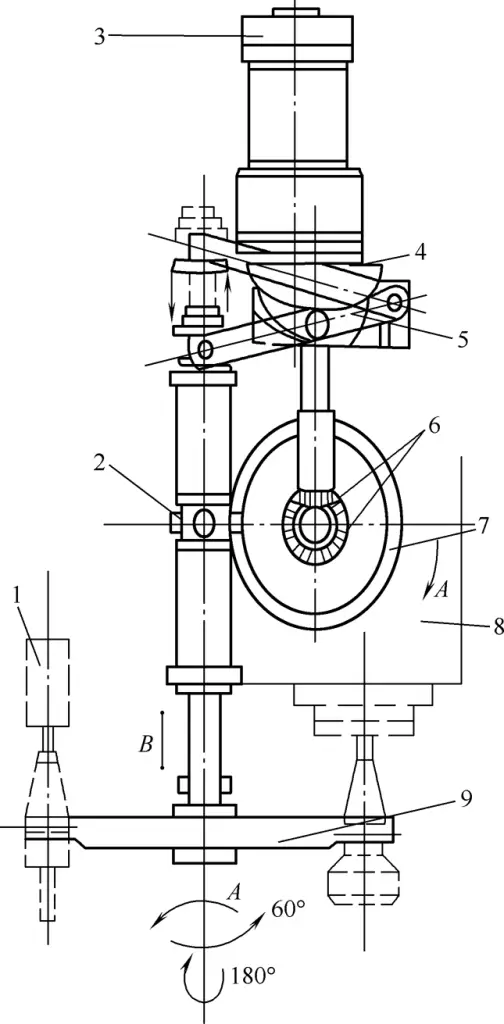
1-Porta-ferramentas
2-Eixo transversal
3-Motor
4-Câmara de ranhura cilíndrica (braço para cima e para baixo)
5 alavancas
Engrenagem de 6 níveis
7-Cam roller (rotação do braço)
Caixa de 8 fusos
9-Braço de troca de ferramentas
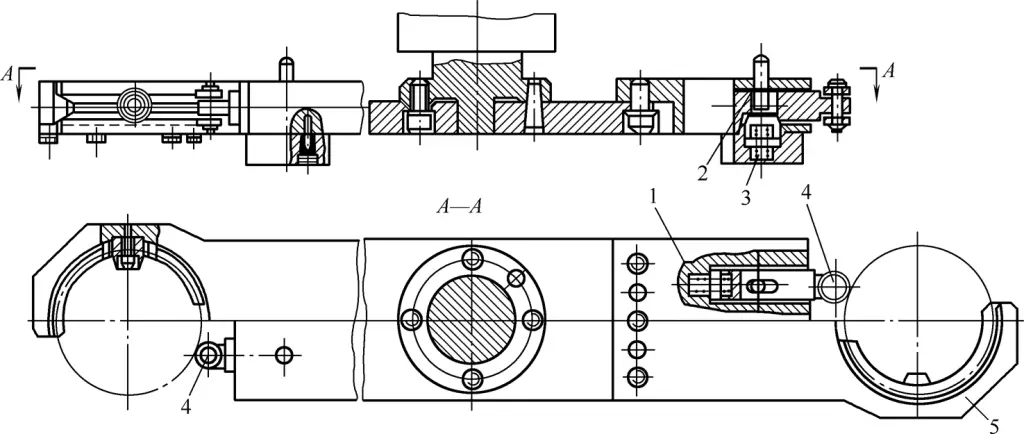
1,3-Molas
2-Pino de bloqueio
Pino 4-Ativo
5-Gripper
V. Principais funções do sistema CNC
As funções do sistema CNC para centros de maquinação têm muitas semelhanças com as das fresadoras CNC, mas os sistemas CNC configurados para centros de maquinação têm funções e comandos mais ricos e abrangentes em comparação com as fresadoras CNC.
Os sistemas CNC configurados para centros de maquinação produzidos por diferentes fabricantes variam, mas as suas funções básicas são praticamente as mesmas. Os centros de maquinação equipados com sistemas FANUC e sistemas SIEMENS são amplamente utilizados. Com exceção da troca de ferramentas, a programação e o funcionamento destes centros de maquinação são basicamente os mesmos das fresadoras CNC.
As funções dos sistemas CNC incluem geralmente funções básicas e funções opcionais. As funções básicas são funções essenciais do sistema CNC, enquanto as funções opcionais são escolhidas pelos utilizadores em função das características e da finalidade da máquina. Diferentes sistemas CNC têm diferentes funções. Segue-se uma breve descrição de algumas funções utilizando o sistema FANUC como exemplo.
1. Função de controlo multi-coordenado
O sistema de controlo pode controlar um número de eixos de coordenadas, referindo-se ao número máximo de eixos de coordenadas que o sistema CNC pode controlar, incluindo eixos lineares e eixos rotativos. Os eixos coordenados lineares básicos são os eixos X, Y e Z; os eixos coordenados rotativos básicos são os eixos A, B e C. O número de eixos simultâneos refere-se ao número de eixos coordenados que o sistema CNC pode controlar para se moverem simultaneamente de acordo com os requisitos de maquinação.
A função de controlo refere-se ao número de eixos que o dispositivo CNC pode controlar e pode controlar simultaneamente. A função de controlo é um dos principais indicadores de desempenho de um dispositivo CNC.
Os eixos de controlo incluem eixos móveis e eixos rotativos, eixos básicos e eixos adicionais. Quanto mais eixos puderem ser controlados, especialmente quanto mais eixos puderem ser controlados simultaneamente, mais forte será a funcionalidade do dispositivo CNC, mais complexo será o dispositivo CNC e mais difícil será a programação.
2. Função de compensação da ferramenta
A função de correção da ferramenta inclui a correção do comprimento da ferramenta e a correção do raio da ferramenta. A correção do comprimento da ferramenta inclui ainda a correção da geometria da ferramenta e a correção do desgaste da ferramenta.
(1) Função de correção do comprimento da ferramenta
A correção do comprimento da ferramenta refere-se à correção axial da ferramenta, que aumenta ou diminui a posição real da ferramenta na direção axial com um valor de desvio em relação ao valor programado. Esta função não só altera automaticamente a altura da superfície de corte, como também reduz os erros de ajuste axial da ferramenta.
(2) Função de compensação do desgaste da ferramenta
As ferramentas desgastam-se durante a utilização e, se a compensação do desgaste da ferramenta não for efectuada atempadamente, isso conduzirá a uma diminuição da precisão de maquinação das peças. Ao ajustar a compensação do desgaste da ferramenta, mantendo a compensação da geometria da ferramenta inalterada, a compensação do comprimento da ferramenta é indiretamente modificada para garantir a precisão da maquinação da peça.
(3) Função de correção do raio da ferramenta
Utilizando esta função, o centro da ferramenta pode deslocar-se automaticamente do contorno da peça de trabalho por um raio da ferramenta, tornando conveniente calcular e programar de acordo com as dimensões reais do contorno da peça de trabalho durante a programação, sem a necessidade de calcular e programar com base na trajetória do centro da fresa.
Esta função também pode ser utilizada para compensar a precisão de fabrico insuficiente das fresas, alterando o valor de compensação do raio da ferramenta, expandindo a gama de seleção do diâmetro da ferramenta e o erro admissível para a retificação da ferramenta.
O método de alteração do valor de compensação do raio da ferramenta também pode ser utilizado para obter uma fresagem em camadas e uma maquinação grosseira e fina com o mesmo programa de processamento, ou para melhorar a precisão de maquinação das peças. Além disso, a alteração dos sinais positivos e negativos do valor de compensação do raio da ferramenta também pode ser utilizada para processar determinadas peças que precisam de ser combinadas entre si utilizando o mesmo programa de maquinação.
3. Função de ciclo fixo
Os ciclos de maquinagem são séries pré-programadas de operações de maquinagem típicas armazenadas na memória, que podem ser chamadas através de códigos G quando necessário. A utilização de funções de ciclo fixo pode simplificar muito a preparação do programa. Os ciclos fixos incluem ciclos de furação, ciclos de perfuração, ciclos de roscagem e muito mais.
4. Função de maquinagem de espelhos
A maquinação em espelho é também conhecida como maquinação de simetria axial. Para uma peça de trabalho que é simétrica em relação ao eixo de coordenadas, utilizando a função de maquinação em espelho, apenas um ou dois quadrantes do programa precisam de ser escritos, e os contornos de outros quadrantes podem ser obtidos através da maquinação em espelho.
5. Função de rotação
Esta função pode rodar o programa de maquinação programado em qualquer ângulo dentro do plano de maquinação para execução.
6. Subprograma
Em algumas peças maquinadas, aparecem frequentemente percursos de maquinação geometricamente idênticos e, ao escrever programas de maquinação, há segmentos de programa com sequências fixas e padrões repetitivos que aparecem em vários programas.
Para simplificar a programação, estes segmentos típicos de programas de maquinação com sequências fixas e padrões repetitivos podem ser programados como subprogramas num determinado formato e depois introduzidos na memória.
Se o programa principal precisar de um determinado subprograma durante a execução, pode chamar esse subprograma através de uma instrução de chamada de subprograma num formato específico. Depois de o subprograma ser executado, regressa ao programa principal e continua a executar os segmentos de programa seguintes.
7. Função de programa de macro
Os programas de macros do utilizador referem-se a subprogramas que contêm variáveis. Os programas de macros do utilizador permitem a utilização de variáveis, operações aritméticas e lógicas, e transferências condicionais, tornando mais conveniente e mais fácil escrever programas para as mesmas operações de maquinação. No programa de maquinação, uma instrução simples, nomeadamente a instrução de macro do utilizador, pode ser utilizada para chamar o programa de macro do utilizador.
8. Função preparatória
A função de preparação, também designada por função G, permite determinar o modo de ação da fresadora CNC. As instruções da função G são constituídas pelo código de endereço G seguido de dois dígitos.
9. Função auxiliar
A função auxiliar é uma operação auxiliar essencial na maquinagem CNC, representada pelo código de endereço M seguido de dois dígitos quaisquer. Sistemas diferentes podem ter funções M diferentes. As funções auxiliares são utilizadas para especificar o arranque/paragem do fuso, ligar/desligar o fluido de corte, etc.
10. Função de alimentação
A função de avanço, também conhecida como função F, representa a velocidade de avanço e é indicada pelo código de endereço F seguido de vários dígitos. O avanço efetivo pode ser ajustado através do botão de anulação do avanço no painel de operações do CNC.
11. Função do fuso
A função do fuso do centro de maquinagem refere-se principalmente à especificação da velocidade do fuso (ferramenta velocidade de corte) durante o processo de maquinagem. A função do mandril é representada pelo código de endereço S seguido de vários dígitos, sendo a unidade r/min. Por exemplo, S1000 indica uma velocidade do mandril de 1000 r/min.
12. Função de ecrã gráfico
Os dispositivos CNC podem ser equipados com CRT monocromático ou a cores, implementando ecrãs de caracteres e gráficos através de software e interfaces. Pode apresentar programas de maquinação, parâmetros, vários valores de compensação, posições de coordenadas, informações de alarme, trajectórias dinâmicas de movimento da ferramenta, etc.
13. Função de controlo do funcionamento
Os centros de maquinagem têm normalmente funções como operação de bloco único, funcionamento a seco, salto, bloqueio da máquina, simulação gráfica de funcionamento e paragem de emergência.
14. Função de alarme de auto-diagnóstico
A função de alarme de auto-diagnóstico refere-se à capacidade do sistema CNC de auto-diagnosticar as suas falhas de software e hardware. Esta função pode ser utilizada para monitorizar se toda a máquina-ferramenta e todo o processo de maquinação estão normais, e emitir prontamente um alarme em caso de anomalias, identificando assim rapidamente o tipo e a localização das falhas, reduzindo o tempo de inatividade causado pelas falhas.
15. Função de comunicação
Os sistemas CNC modernos estão geralmente equipados com interfaces RS232C ou interfaces DNC, permitindo a transmissão de sinais a alta velocidade com computadores de nível superior. Os sistemas CNC topo de gama podem também ligar-se à INTERNET para satisfazer os requisitos do FMS (Flexible Manufacturing System) e do CIMS (Computer Integrated Manufacturing System).
VI. Desenvolvimento e orientação da tecnologia CNC
1. Processo de desenvolvimento de sistemas CNC
As máquinas-ferramentas CNC tiveram a sua origem nos Estados Unidos. Desde que a primeira máquina de furar e fresar de três coordenadas CNC do mundo foi introduzida em 1952, os sistemas CNC passaram por duas fases e seis gerações de desenvolvimento (ver Quadro 1).
A primeira geração de sistemas CNC utilizava componentes de tubos de vácuo, que eram grandes em tamanho, pouco fiáveis e de preço elevado. Eram utilizados principalmente na indústria militar e não eram amplamente aplicados, com baixos volumes de produção.
A segunda geração surgiu em 1961, consistindo em sistemas CNC baseados em transístores, que melhoraram a fiabilidade e reduziram consideravelmente o tamanho.
A terceira geração foi o sistema CNC de circuito integrado comercializado em 1965, que reduziu consideravelmente o tamanho dos dispositivos CNC e melhorou substancialmente a fiabilidade, tornando-o aceitável para os utilizadores em geral. Tanto o volume de produção como a variedade de máquinas-ferramentas CNC registaram um desenvolvimento significativo.
As três gerações anteriores de sistemas CNC eram essencialmente computadores especializados, que dependiam principalmente de hardware para implementar várias funções de controlo. Esta foi a primeira fase, designada por sistemas de Controlo Numérico (NC).
Em 1968, os minicomputadores foram aplicados em sistemas CNC, tornando-se a quarta geração de sistemas CNC. A aplicação de microprocessadores em 1974 tornou-se a quinta geração de sistemas CNC. Em 1990, os sistemas CNC abertos baseados em plataformas PC tornaram-se a sexta geração de sistemas CNC.
As três últimas gerações pertencem à segunda fase, designada por sistemas de controlo numérico computorizado (CNC).
Quadro 1 Seis gerações de desenvolvimento de sistemas CNC
História do desenvolvimento do sistema CNC | Ano de emergência mundial | Ano de aparecimento na China | |
Primeira fase (sistemas NC) | Sistema CNC de tubo de vácuo de primeira geração Sistema CNC de transístores de segunda geração Sistema CNC de circuitos integrados de terceira geração | 1952 1961 1965 | 1958 1964 1972 |
Segunda fase (sistemas CNC) | Sistema CNC de minicomputador de quarta geração Sistema CNC com microprocessador de quinta geração Sistema CNC aberto de sexta geração baseado numa plataforma PC (industrial) | 1968 1974 1990 | 1978 1981 1992 |
2. Tendências de desenvolvimento da tecnologia CNC
Atualmente, a China dispõe de sistemas CNC com direitos de propriedade intelectual independentes, mas a grande maioria das máquinas-ferramentas CNC plenamente funcionais continua a utilizar sistemas CNC estrangeiros. Do ponto de vista da máquina-ferramenta em geral, existe ainda uma diferença considerável em relação às suas congéneres estrangeiras em termos de fiabilidade, precisão, nível de automatização e eficiência da produção.
Com o desenvolvimento da ciência e da tecnologia e o aumento das tecnologias de fabrico avançadas em todo o mundo, os requisitos da tecnologia de maquinagem CNC estão a tornar-se cada vez mais elevados. Com o desenvolvimento de tecnologias conexas, como o corte a ultra-alta velocidade e a maquinagem de ultra-precisão, são necessários indicadores de desempenho mais elevados para as estruturas das máquinas-ferramentas, os accionamentos dos fusos, os sistemas CNC e os sistemas servo das máquinas-ferramentas CNC, o que conduziu às seguintes sete tendências de desenvolvimento da tecnologia das máquinas-ferramentas CNC.
(1) Alta precisão
A elevada precisão das máquinas-ferramentas CNC inclui uma elevada precisão geométrica da máquina-ferramenta e uma elevada precisão de maquinagem. A elevada precisão geométrica é a base para melhorar a precisão da maquinagem. O aspeto mais importante da precisão geométrica é a precisão de posicionamento. A melhoria da precisão de posicionamento, juntamente com a melhoria das características estruturais e da estabilidade térmica da máquina, melhorou consideravelmente a precisão de maquinação das máquinas-ferramentas CNC.
Por exemplo: A precisão de maquinação dos centros de maquinação melhorou dos anteriores ±0,01mm para ±0,005mm, ou até mais. Para atingir objectivos de maior precisão, são adoptadas principalmente as seguintes medidas:
1) Sistema de acionamento servo.
A adoção de sistemas servo AC digitais melhorou consideravelmente o desempenho dos servos em termos de precisão de posicionamento, velocidade de avanço e outros aspectos, em comparação com os anteriores sistemas servo DC analógicos. Existem até os chamados métodos de alimentação servo linear de "transmissão zero" que utilizam motores lineares para acionar diretamente a mesa da máquina-ferramenta, melhorando consideravelmente a precisão da maquinação.
2) Tecnologia de controlo por avanço.
Os sistemas servo anteriores multiplicavam o desvio entre a posição de comando e a posição real pelo ganho do circuito de posição, e o produto era utilizado como comando de velocidade para controlar a velocidade do motor. Este método apresentava sempre um erro de atraso no seguimento da posição, o que resultava na deterioração das condições de maquinagem ao processar cantos ou arcos.
O chamado controlo de avanço adiciona um método de controlo de comando de velocidade ao sistema de controlo original, o que reduz significativamente o erro de atraso de seguimento, melhorando assim a precisão de maquinação do corte de cantos.
3) Tecnologia de controlo de compensação não linear para o atrito dinâmico e estático de máquinas-ferramentas.
A não linearidade do atrito dinâmico e estático nas máquinas-ferramentas pode levar ao arrastamento do selim. Para além de tomarem medidas para reduzir o atrito estático na estrutura da máquina, os novos sistemas servo digitais têm a função de controlo para compensar automaticamente a não linearidade do atrito dinâmico e estático nos sistemas mecânicos.
4) Desenvolvimento e aplicação generalizada da tecnologia de compensação.
As máquinas-ferramentas CNC modernas utilizam a função de compensação de software dos sistemas de controlo numérico computorizado para efetuar várias compensações no sistema servo, tais como a compensação do erro de ponto fixo do movimento axial, a compensação do erro de passo do parafuso de avanço, a compensação da folga, a compensação da deformação térmica, etc.
5) Equivalente de impulsos de alta precisão.
O equivalente de impulsos de alta precisão pode melhorar a exatidão e a repetibilidade do posicionamento.
6) Adoção de dispositivos de deteção de posição de alta resolução.
Por exemplo: Codificadores de impulsos de alta resolução, circuitos de subdivisão compostos por microprocessadores incorporados, que melhoram consideravelmente a resolução.
(2) Alta velocidade
A melhoria da eficiência da produção foi sempre um dos objectivos do desenvolvimento da tecnologia das máquinas-ferramentas. O aparecimento e o rápido desenvolvimento das máquinas-ferramentas CNC devem-se, em parte, à sua eficiência de produção muito superior à das máquinas-ferramentas convencionais.
Nos últimos anos, a eficiência de produção das máquinas-ferramentas CNC melhorou significativamente, principalmente através da redução do tempo de corte e do tempo auxiliar não cortante. A redução do tempo de corte é conseguida através do aumento da velocidade de corte, ou seja, do aumento da velocidade do fuso.
A velocidade do fuso dos centros de maquinagem aumentou de 4000-6000 r/min há 10 anos para as actuais 8000-12000 r/min, com a mais elevada a atingir mais de 100000 r/min. A velocidade do fuso dos tornos CNC também aumentou para 5000-20000 r/min, e a velocidade linear das mós aumentou para 100-200 m/s.
De acordo com as estatísticas mais recentes, o tempo de corte dos centros de maquinagem não excede 55% do tempo total de trabalho. Por conseguinte, a redução do tempo de não corte é um meio importante para melhorar a eficiência da produção. O tempo de não corte é composto por duas partes: uma é o tempo de deslocamento rápido, que é o tempo necessário para o movimento rápido; a outra é o tempo auxiliar, principalmente o tempo de troca de ferramenta e o tempo de troca de peça.
Para encurtar o tempo de deslocação rápida, é necessário aumentar a velocidade do movimento rápido. Atualmente, a velocidade geral de movimento rápido atingiu 20~24m/min, algumas rondam os 30m/min e a mais rápida pode atingir os 60m/min.
Especialmente o aparecimento de servomotores de alimentação de movimento linear trouxe a possibilidade de aumentar ainda mais a velocidade de movimento. Além disso, para reduzir o tempo das acções auxiliares, é necessário encurtar o tempo de mudança automática da ferramenta e de mudança automática da peça.
Atualmente, o tempo de rotação da torre dos tornos CNC atingiu 0,4~0,6s, o tempo de mudança automática de ferramentas dos centros de maquinagem atingiu cerca de 3s, e o mais rápido pode atingir 1s. O tempo de mudança de palete dos centros de maquinação foi reduzido de 12~20s no passado para 6~10s, com o mais rápido a atingir 2,5s.
Atualmente, as medidas para melhorar os indicadores de velocidade são tomadas principalmente com base nos seguintes aspectos
1) Sistema CNC.
O microprocessador é o componente central dos sistemas CNC modernos. São utilizados microprocessadores de maior bit e frequência para melhorar a velocidade de computação básica do sistema. Atualmente, passou de CPUs de 16 bits para CPUs de 32 bits e está a evoluir para CPUs de 64 bits. Os microprocessadores de 32 bits e as estruturas multi-microprocessadores são adoptados para melhorar a capacidade de processamento de dados do sistema, ou seja, para aumentar a velocidade e a precisão dos cálculos de interpolação.
2) Configurar o PLC incorporado de alta velocidade e potente.
Ao melhorar a velocidade de funcionamento do PLC, este satisfaz os requisitos de maquinagem a alta velocidade das máquinas-ferramentas CNC. Os novos PLCs têm CPUs dedicadas, com velocidade de execução de instruções básicas que atinge μs/passo, e os passos programáveis podem ser expandidos para mais de 16.000 passos. A função de processamento a alta velocidade do PLC é utilizada para permitir a combinação orgânica entre o CNC e o PLC, satisfazendo vários requisitos de controlo em tempo real durante o funcionamento da máquina-ferramenta CNC.
3) Melhorar o nível de controlo multieixos.
Todos os novos sistemas CNC possuem funções de controlo multieixos, que podem utilizar a ligação multieixos para realizar a maquinação de superfícies complexas e especiais, e podem também adotar a maquinação simultânea multi-ferramentas com controlo multi-torres.
4) Aplicação de ferramentas de corte de velocidade ultra-elevada.
Atualmente, as ferramentas com revestimento de diamante e as ferramentas de cerâmica têm sido aplicadas na maquinagem a velocidade ultra-elevada.
(3) Elevada automatização
Após a evolução do sistema CNC para um sistema CNC baseado em microprocessador, as funções do sistema foram continuamente expandidas, pelo que o nível de automatização das máquinas-ferramentas CNC também foi continuamente melhorado.
Para além da troca automática de ferramentas e da troca automática de peças, têm surgido sucessivamente funções como a gestão da vida útil das ferramentas, a substituição automática de ferramentas sobresselentes, a medição e compensação automática do tamanho das ferramentas, a medição e compensação automática do tamanho das peças e o ajuste automático dos parâmetros de corte, fazendo com que a automatização de máquinas individuais atinja um nível muito elevado. As funções de monitorização do desgaste e da quebra da ferramenta estão também a ser continuamente melhoradas.
(4) Elevada fiabilidade
A fiabilidade do funcionamento da máquina-ferramenta CNC depende principalmente da fiabilidade do sistema CNC e de vários sistemas servo. Atualmente, são adoptadas principalmente as seguintes medidas para melhorar a fiabilidade:
1) Melhorar a qualidade do hardware do sistema CNC.
Selecionar chips de circuitos de maior integração, estabelecer e implementar uma seleção rigorosa de componentes, um fabrico estável de produtos e testes de desempenho abrangentes.
2) Modularização, normalização e universalização.
Atualmente, as funções dos sistemas CNC modernos estão a tornar-se cada vez mais poderosas, permitindo que as estruturas de hardware e software do sistema atinjam a modularização, a normalização e a universalização, o que facilita a organização da produção, o controlo da qualidade e a manutenção do utilizador.
(5) Multifuncionalidade
1) As máquinas-ferramentas CNC adoptam a multifuncionalidade para melhorar a utilização do equipamento.
A multifuncionalidade significa combinar as funções de diferentes máquinas-ferramentas numa única máquina-ferramenta. Os seus representantes típicos são os vários centros de maquinação equipados com mecanismos de troca automática de ferramentas (a capacidade do armazém de ferramentas pode atingir mais de 100 ferramentas), que podem executar simultaneamente vários processos como fresagem, furação, brocagem, torneamento, alargamento, rosqueamento e até mesmo retificação na mesma máquina-ferramenta.
Para melhorar ainda mais a eficiência do trabalho, as modernas máquinas-ferramentas CNC (como vários centros de maquinagem de cinco faces) adoptaram o corte multi-fuso e multi-face, ou seja, a realização simultânea de diferentes operações de corte em diferentes partes de uma peça de trabalho.
Além disso, o número de eixos de controlo nos sistemas CNC modernos está a aumentar constantemente, chegando alguns a atingir 31 eixos, e o número de eixos ligados simultaneamente atingiu 7. Estas máquinas-ferramentas têm uma maior precisão de maquinagem e podem melhorar significativamente a eficiência do trabalho, poupar espaço, reduzir a quantidade de equipamento e poupar investimento.
2) Boa função de diálogo homem-máquina.
Numa única máquina-ferramenta, o processamento de peças e a edição de programas podem ser efectuados em simultâneo, ou seja, tem a função de operação em primeiro plano e edição em segundo plano. Os sistemas CNC modernos utilizam CRT a cores para a visualização bidimensional da trajetória, e os melhores podem obter uma simulação gráfica dinâmica tridimensional a cores, apresentando a trajetória de maquinagem do código programado, facilitando a depuração e a modificação dos programas de peças e garantindo a segurança do processo de maquinagem real.
3) Reforço da função de comunicação.
O desenvolvimento de máquinas-ferramentas CNC, de máquinas autónomas para FMC (Flexible Manufacturing Cell), FMS (Flexible Manufacturing System) e posterior ligação em rede para formar CIMS (Computer Integrated Manufacturing System), exige que os sistemas CNC tenham funções de comunicação mais fortes.
A maioria dos sistemas CNC possui interfaces de série de alta velocidade e longa distância RS232C e RS422, que podem trocar vários dados com computadores de nível superior, de acordo com os requisitos de formato ao nível do utilizador. Os sistemas CNC de topo de gama devem ter interfaces DNC (Controlo Numérico Distribuído), que permitem a comunicação de dados entre várias máquinas-ferramentas CNC e podem também controlar diretamente várias máquinas-ferramentas CNC.
Para se adaptarem ao desenvolvimento da tecnologia de automação e satisfazerem os requisitos de uma automação de fábrica em grande escala e a necessidade de ligação em rede de diferentes fabricantes e tipos de máquinas-ferramentas CNC, as máquinas-ferramentas CNC modernas adoptaram as redes de controlo industrial MAP (Manufacturing Automation Protocol). A versão 3.0 do MAP foi agora implementada, criando condições para que as máquinas-ferramentas CNC modernas entrem no FMS e no CIMS.
(6) Automatização da programação CNC
A programação automática CAM é atualmente o método de programação de maquinação CNC mais avançado.
Atualmente, o software de programação automática interactiva gráfica CAD/CAM é amplamente utilizado. Utiliza o CAD para completar o desenho informático das geometrias das peças e, em seguida, através do cálculo e pós-processamento dos dados do percurso da ferramenta interno do computador, gera automaticamente programas de processamento de peças NC, que são depois transmitidos às máquinas-ferramentas CNC através de interfaces de comunicação para processamento de controlo automático, conseguindo assim a integração CAD/CAM e realizando o design e o fabrico sem desenhos.
Além disso, com o desenvolvimento da tecnologia CIMS, surgiu um método de programação totalmente automático que integra CAD/CAPP (Computer-Aided Process Planning)/CAM. A maior diferença em relação à programação do sistema CAD/CAM é que os parâmetros do processo de maquinagem necessários para a programação não necessitam de participação humana, sendo diretamente obtidos a partir da base de dados CAPP do sistema.
(7) Inteligência Os sistemas CNC modernos introduziram a tecnologia de controlo adaptativo.
A tecnologia de Controlo Adaptativo (CA) requer o ajuste automático do estado de trabalho e das características medidas durante o processo de maquinação em processos de maquinação que mudam aleatoriamente, corrigindo automaticamente os seus próprios parâmetros de trabalho de acordo com determinados indicadores de avaliação para atingir ou aproximar-se do estado de trabalho ideal.
A tecnologia de controlo adaptativo permite obter uma precisão de maquinação muito elevada e uma rugosidade da superfíciee, simultaneamente, melhorar a vida útil das ferramentas e a eficiência de produção do equipamento.
A inteligência dos sistemas CNC reflecte-se principalmente nos seguintes aspectos:
- Deteção e substituição automática da vida útil da ferramenta, alarme atempado para peças fora de tolerância, desgaste ou quebra da ferramenta, compensação automática ou substituição de ferramentas sobresselentes.
- Diagnóstico e reparação automáticos em caso de avaria.
- Compensação em tempo real da expansão e contração dos fusos de esferas e outros componentes devido à deformação térmica durante a maquinação.
- Introdução da tecnologia de reconhecimento de padrões, aplicação de reconhecimento de imagem e tecnologia de controlo por voz, permitindo que o sistema reconheça desenhos por si só e execute maquinação CNC automática de acordo com comandos de linguagem natural.