Os principais factores que afectam a qualidade da corte a laser podem ser divididas em duas categorias: a influência do desempenho do sistema de corte a laser e a influência dos parâmetros de corte a laser. A primeira deve ser considerada aquando da aquisição de lasers e da criação de um sistema de corte a laser, enquanto a segunda diz respeito à forma de escolher e otimizar os parâmetros durante o processo de corte a laser. processo de corte a laser.
Impacto do desempenho do sistema de corte a laser na qualidade do corte
Modo de feixe
Quanto menor for o modo do feixe, menor será o tamanho do ponto após a focagem, maior será a iluminação radiante, mais estreita será a fenda de corte e maior será a eficiência do corte e a qualidade da superfície. A Figura 8-8 mostra a curva de impacto de dois modos de feixe na rugosidade da superfície de corte. Utilizando um TEM00 para cortar uma placa de 2 mm de espessura, a rugosidade da superfície de corte Rz é de apenas 0,8μm, obtendo-se um nível muito suave.
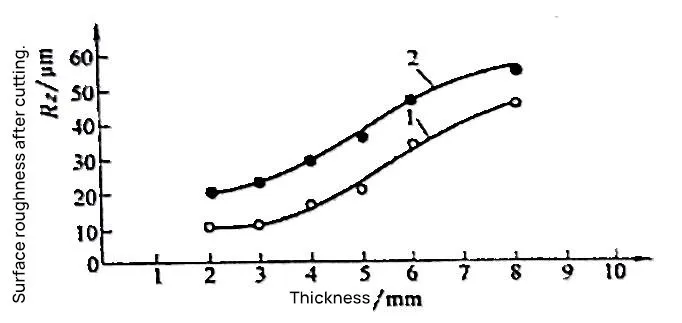
- 1-TEM00
- 2-TEM01
A qualidade de corte com TEM01 é ligeiramente pior, mas ainda mantém um bom nível. A figura 8-9 mostra a curva de impacto dos dois modos de feixe na velocidade de corte. Como se pode ver na Figura 8-9, quando corte uma placa de aço inoxidável de 2 mm de espessura com um laser de modo TEM00 de 500 W, a velocidade de corte pode atingir 2,0 m/min, enquanto que com um laser de modo TEM01, a velocidade de corte é de apenas 1,0 m/min.
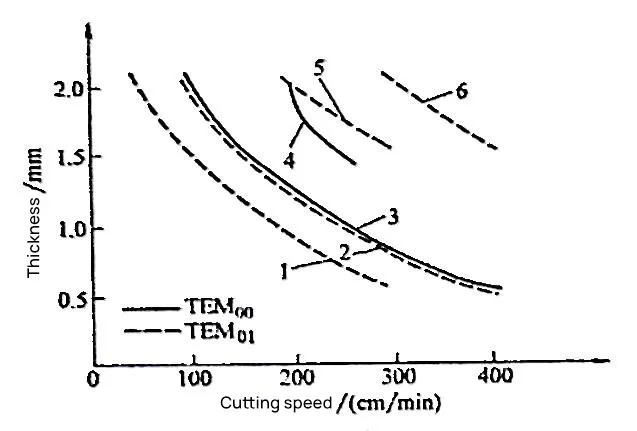
- 1, 3-300W
- 2, 4-500W
- 5-800W
- 6-1000W
- Nota: Material: Aço inoxidável SUS304.
Por conseguinte, para obter uma melhor qualidade de corte e uma maior eficiência de corte, é preferível escolher uma máquina TEM00 ou, pelo menos, não superior ao laser de modo TEM01 modo. Lasers com modos superiores a TEM01 não pode garantir a qualidade do corte e não deve ser utilizado.
Polarização do feixe
A polarização do feixe laser afecta grandemente a qualidade e a eficiência do corte a laser. Se for utilizada luz polarizada linearmente para o corte, a direção de corte muda em relação à direção de polarização do feixe, a taxa de absorção da aresta de corte para o laser muda, afectando assim o efeito do corte a laser.
1) Quando a direção de corte é paralela à direção de polarização, o rácio de absorção da aresta de corte pelo laser é o mais elevado, pelo que o corte é estreito, a perpendicularidade e a rugosidade do corte são baixas e a velocidade de corte é rápida, como se mostra na Figura 8-10a.
2) Quando a direção de corte é perpendicular à direção de polarização, a razão de reflexão da aresta de corte para o laser é a mais elevada, a razão de absorção é a mais pequena e a razão de absorção lateral aumenta, pelo que a velocidade de corte diminui, o corte alarga-se e o valor da rugosidade da superfície de corte também aumenta, como se mostra na Figura 8-10b.
3) Quando a direção de corte está em ângulo com a direção de polarização, a direção com a maior taxa de absorção do laser está também em ângulo com a direção de corte, resultando numa inclinação na parte inferior do corte, como se mostra nas Figuras 8-10c e 8-10d.
4) Para evitar alterações na forma do corte e na qualidade da superfície de corte devido a alterações na direção de corte, deve ser utilizada luz polarizada circularmente para o corte. A amplitude do vetor elétrico da luz polarizada circularmente é igual em todas as direcções, pelo que a relação de absorção da aresta de corte para o laser não se altera com a mudança da direção de corte, e o corte é uniforme e limpo, como se mostra na Figura 8-10e.
Para converter a luz linearmente polarizada de saída do laser em luz circularmente polarizada, deve ser adicionado um polarizador circular à saída do feixe.
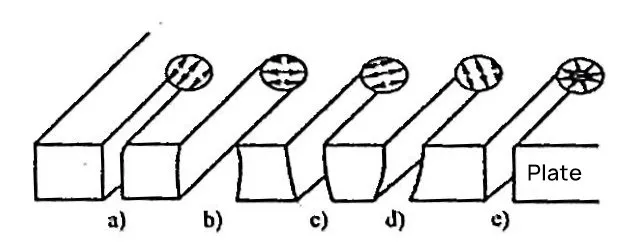
Bocal e caudal de gás
A pressão e o caudal do gás auxiliar estão relacionados com a estrutura e a dimensão do bocal, que influenciam grandemente a qualidade e o desempenho do gás auxiliar. velocidade de corte a laser.
(1) Estrutura do bocal
A Figura 8-11 enumera várias formas estruturais de bocais de corte a laser, entre as quais o bocal cónico apresentado na Figura 8-11a é o mais utilizado.
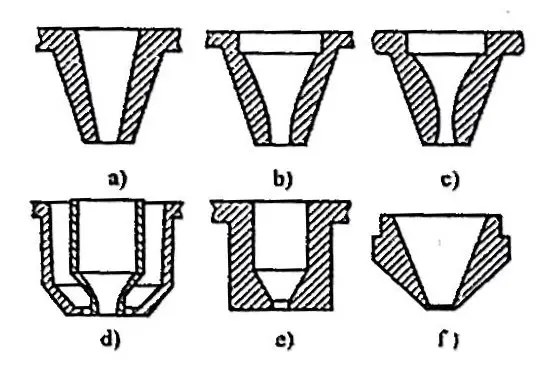
(2) Abertura do bocal
A dimensão da abertura do bocal deve, em primeiro lugar, garantir que o feixe possa passar suavemente, evitando que o feixe no interior do orifício toque na parede interna do bocal. Quanto mais pequena for a abertura, mais difícil será a colimação do feixe, pelo que a abertura não pode ser demasiado pequena.
Além disso, sob uma determinada pressão de gás auxiliar, existe uma gama óptima para a abertura do bocal. Uma abertura demasiado pequena ou demasiado grande afectará a passagem do produto fundido no corte pelo gás auxiliar, afectando assim a velocidade de corte. As figuras 8-12 e 8-13 mostram o impacto da abertura do bocal na velocidade de corte. velocidade de corte de uma placa de aço de baixo carbono com 2 mm de espessura sob determinada potência laser e pressão de gás auxiliar.
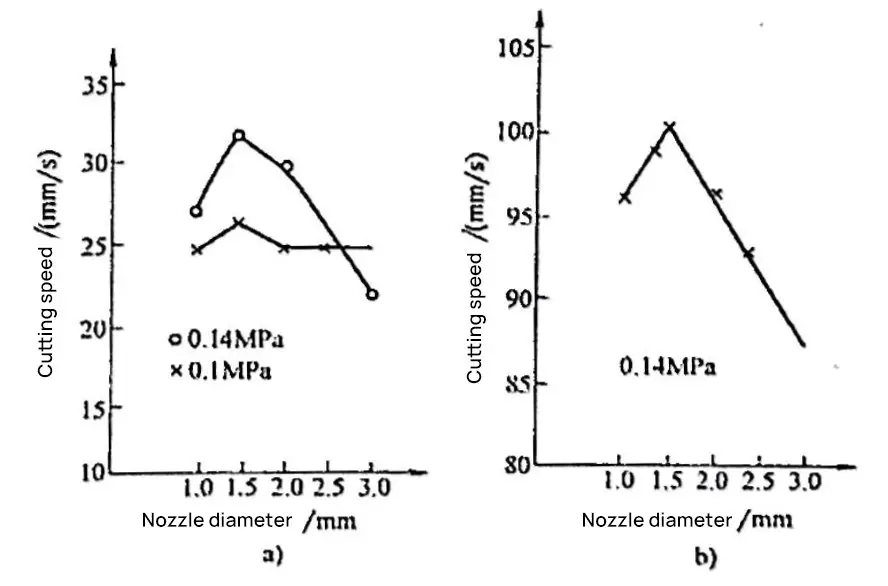
a) Árgon
b) Oxigénio
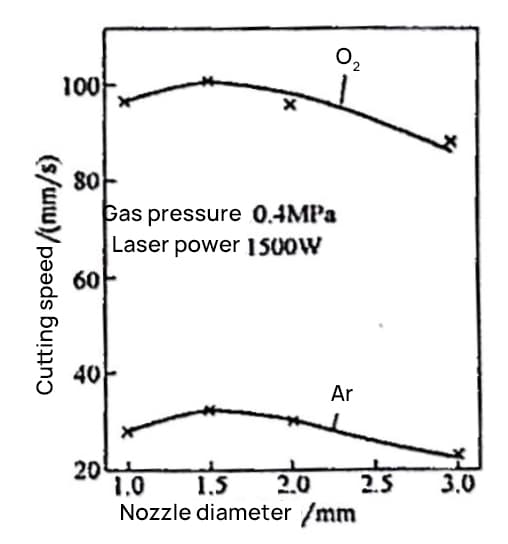
Como se pode ver nas Figuras 8-12 e 8-13, existe um valor ótimo de abertura do bocal para atingir a velocidade máxima de corte. Quer seja utilizado oxigénio ou árgon como gás auxiliar, este valor ótimo é de cerca de 1,5 mm. Os testes de corte a laser em ligas duras, que são difíceis de cortar, mostram que o valor ótimo da abertura do bocal também está muito próximo dos resultados acima, como mostra a Figura 8-14.
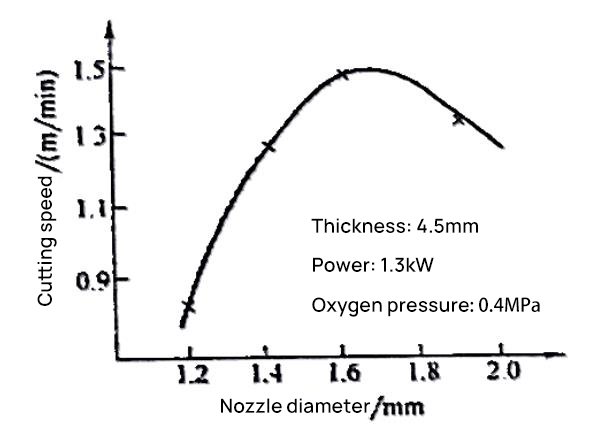
A abertura do bico também afecta a largura da fenda de corte e o tamanho da zona afetada pelo calor, como mostra a Figura 8-15. Como se pode ver na Figura 8-15, à medida que a abertura aumenta, o corte alarga-se e a zona afetada pelo calor estreita-se. A principal razão para o estreitamento da zona afetada pelo calor é que o efeito de arrefecimento do fluxo de gás auxiliar no material de base na área de corte é aumentado.
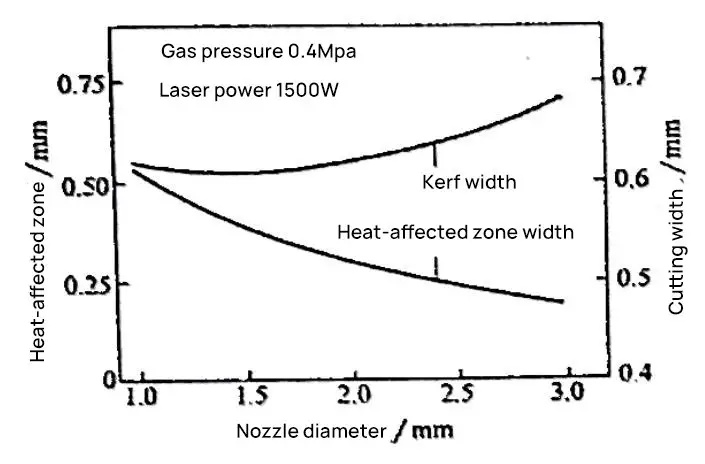
(3) Pressão do gás do bocal
Aumentar a pressão do gás pode melhorar a velocidade de corte, mas depois de atingir um valor máximo, novos aumentos de pressão causarão uma diminuição da velocidade de corte.
Como pode ser visto nas Figuras 8-16 e 8-17, a velocidade máxima de corte é uma função da potência do laser e da espessura da placa da peça de trabalho. Com pressões elevadas de gás auxiliar, a velocidade de corte diminui. As razões para esta diminuição podem ser atribuídas não só ao efeito de arrefecimento reforçado das altas velocidades do fluxo de ar na área de ação do laser, mas também à interferência de ondas de choque intermitentes no fluxo de ar com a área de ação do laser.
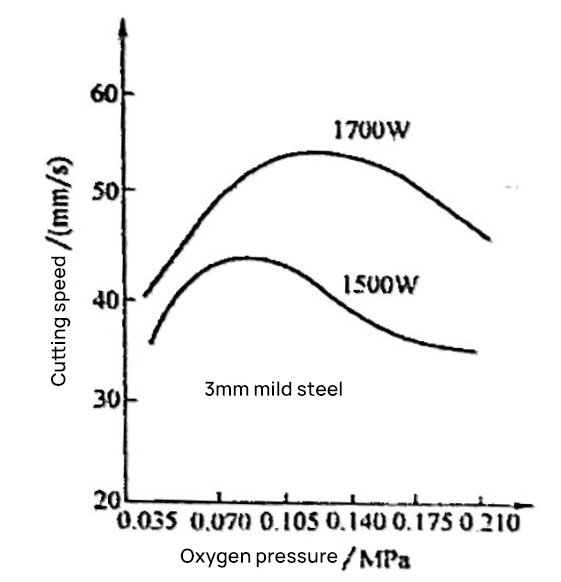
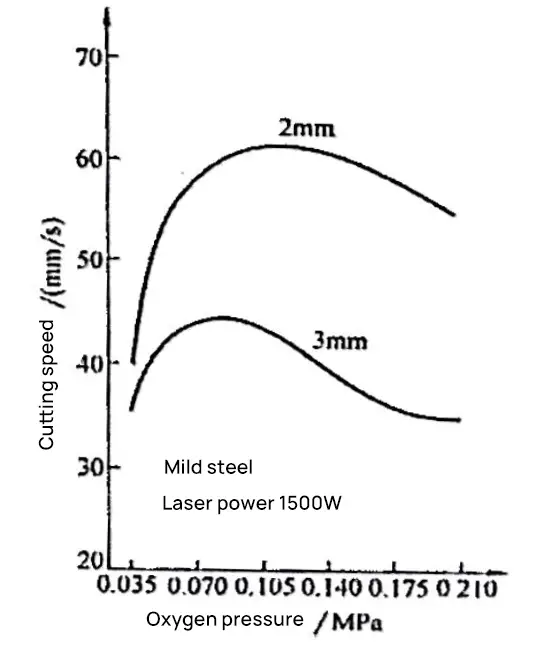
A presença de pressão e temperatura desiguais no fluxo de ar causará alterações na densidade do campo de fluxo de ar. SteenWM e outros mediram que, sob altas pressões de gás, existe um campo de gradiente de densidade na superfície da peça de trabalho diretamente em frente ao bocal, cuja forma e tamanho dependem da pressão do gás, da distância entre a extremidade do bocal e a peça de trabalho, e da abertura do bocal.
Este campo de gradiente de densidade provoca alterações no índice de refração no interior do campo, interferindo assim com a focagem do feixe laser, causando a refocagem ou a divergência do feixe, como se mostra na Figura 8-18. Esta interferência pode afetar a eficiência da fusão e, por vezes, pode alterar a estrutura do modo, causando uma diminuição da qualidade do corte. Se o feixe divergir demasiado, tornando o ponto demasiado grande, o corte normal pode mesmo tornar-se impossível.
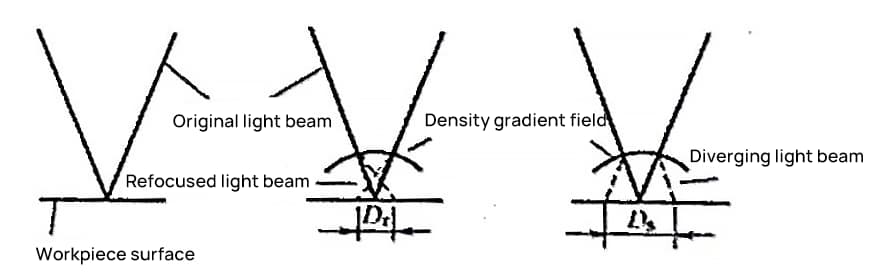
Impacto dos parâmetros de corte a laser na qualidade do corte
Influência da posição do foco na rugosidade da superfície
O impacto da posição de focagem na rugosidade da superfície do corte é mostrado na Figura 8-19, em que a coordenada horizontal na Figura 8-19 é o rácio ab da distância da peça de trabalho à lente de focagem para a distância focal.
A partir da Figura 8-19, pode ver-se que a gama mais suave da superfície do corte é: 0,988 <ab< 1,003, portanto, para o corte geral, o foco é geralmente colocado dentro de 1mm abaixo da superfície da peça de trabalho.
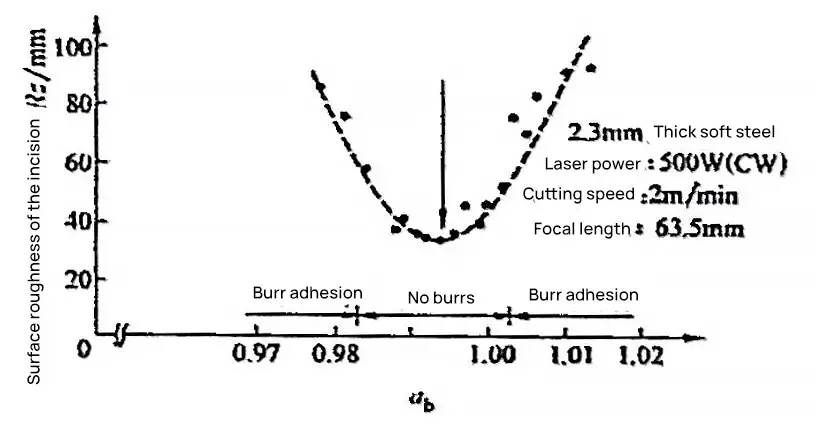
Impacto da potência do laser e da velocidade de corte na largura do caracol
A largura do corte aumenta com o aumento da potência do laser e diminui com o aumento da velocidade de corte, como mostram as Figuras 8-20 e 8-21.
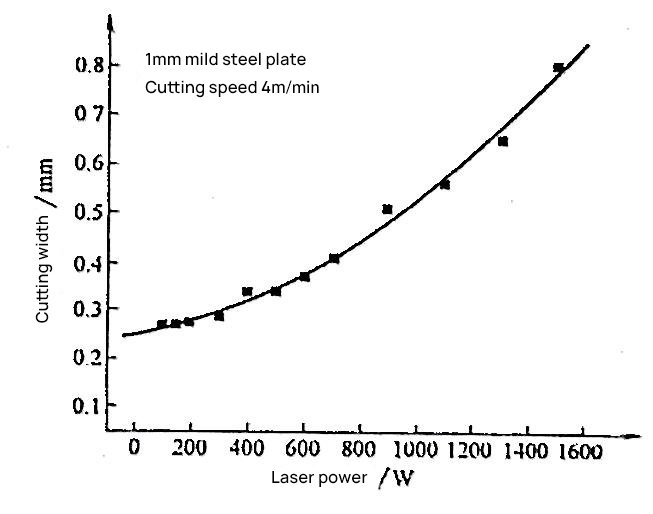
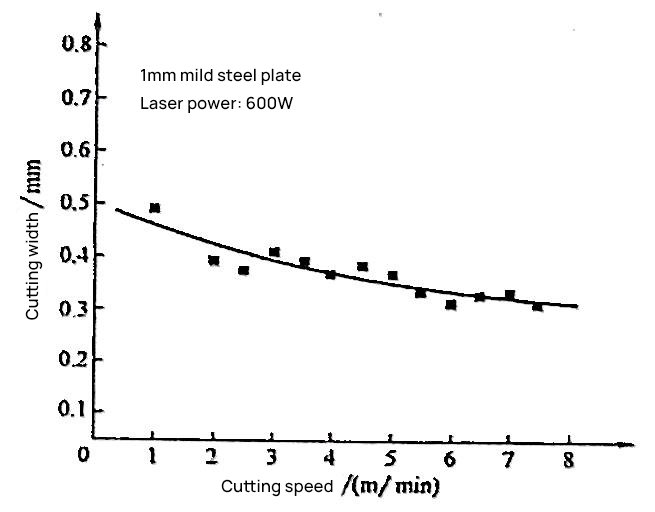
Impacto da potência laser na rugosidade da superfície
Numa determinada placa espessura e velocidade de corteExiste uma gama óptima de potência laser, dentro da qual a rugosidade da superfície de corte é a mais baixa. Se nos desviarmos da gama de potência óptima, a rugosidade aumenta; se aumentarmos ou diminuirmos ainda mais a potência, haverá queimaduras excessivas ou defeitos de escória.
A Figura 8-22 mostra a relação entre a potência do laser e a qualidade da superfície de corte ao cortar uma chapa de aço de baixo carbono com 2 mm de espessura a uma velocidade de corte de 50 mm/s (ou seja, 3 m/min), utilizando o método de medição da rugosidade junto à aresta inferior. A partir da Figura 8-22, pode ser visto que a potência do laser pode ser dividida em três áreas: área de escória, área livre de defeitos e área de queimadura excessiva.
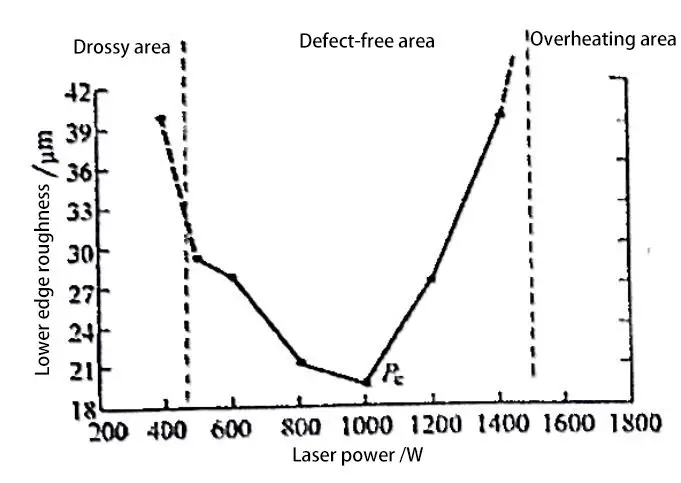
Nota: A espessura da placa de aço de baixo carbono é de 2 mm, v=50 mm/s.
1) Se a potência do laser for demasiado elevada, causando demasiada entrada de calor, a gama de fusão da peça de trabalho é maior do que a gama que a corrente de gás de alta pressão pode afastar, e o metal fundido não pode ser completamente soprado pela corrente de gás, resultando em sobreaquecimento.
2) Se a potência do laser for demasiado baixa, o calor não é suficiente. Quanto mais próximo do bordo inferior, mais baixa é a temperatura do produto fundido e mais alta é a viscosidade [11], pelo que não pode ser completamente soprado pela corrente de gás de alta pressão e permanece no bordo inferior da superfície de corte, resultando em escória. Em casos graves, nem sequer se consegue formar um corte.
3) Dentro da área livre de defeitos, existe uma gama óptima de potência laser (cerca de 800~1000W na Figura 8-22), onde a rugosidade da superfície de corte é a menor.
Impacto da velocidade de corte na rugosidade da superfície
Para uma determinada espessura de chapa e potência laser, existe uma velocidade de corte óptima, na qual a rugosidade da superfície de corte é a menor.
Um desvio da velocidade de corte ideal aumentará a rugosidade; um aumento ou uma diminuição da velocidade de corte resultará em queimaduras excessivas ou defeitos de escória [5].
A Figura 8-23 mostra a relação entre a velocidade de corte e a qualidade da superfície de corte para uma placa de aço de baixo carbono com 2 mm de espessura a uma potência laser de 1000 W, sendo a coordenada vertical a rugosidade perto do bordo inferior. A partir da Figura 8-23, pode ver-se que a velocidade de corte também pode ser dividida em área de queima excessiva, área sem defeitos e área de escória.
Se a velocidade de corte for demasiado baixa, as queimaduras são causadas por uma entrada excessiva de calor; se a velocidade de corte for demasiado elevada, são produzidas escórias, ou mesmo o corte não está completo.
A razão para a ocorrência de escórias devido à elevada velocidade de corte, para além da insuficiente entrada de calor e da baixa temperatura que provoca uma elevada viscosidade do produto fundido, é que a elevada velocidade de corte faz com que a frente de corte se incline significativamente para trás (aumentando a quantidade de arrastamento), o que é ainda mais desfavorável para o fluxo de gás soprar o produto fundido.
Dentro da área livre de defeitos, existe uma velocidade de corte óptima v (50mm/s na Figura 8-23), onde a rugosidade da superfície de corte é a menor.
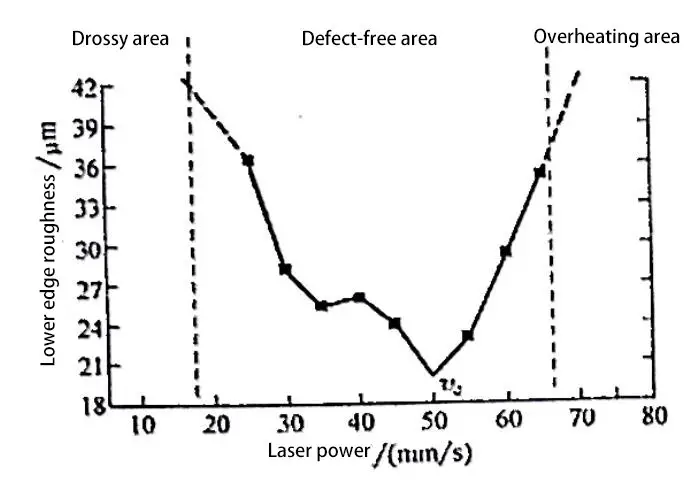
Nota: A espessura da placa de aço de baixo carbono é de 2mm, P=1000W.