Los sistemas robóticos industriales suelen constar de cuatro partes: el manipulador (cuerpo), el entorno, las tareas y el controlador, como se muestra en la figura 1.
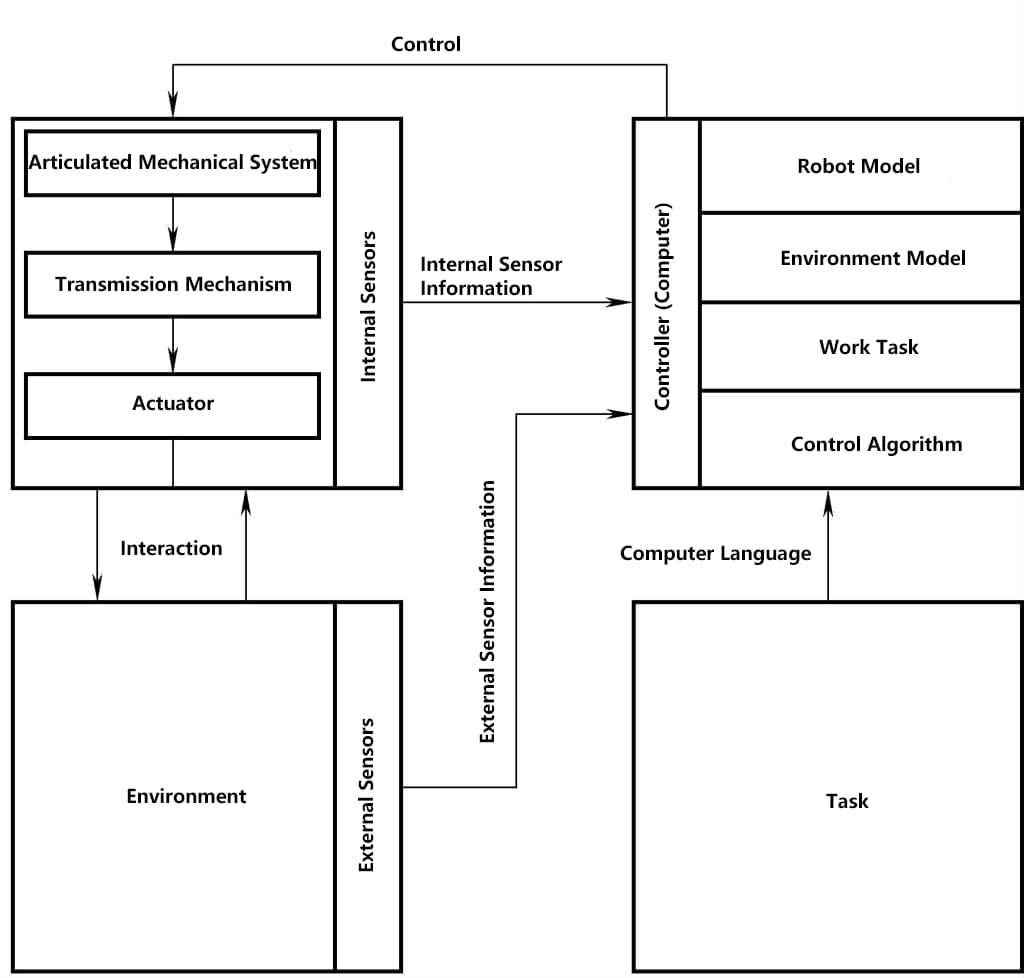
El entorno se refiere al ambiente de trabajo del robot, incluyendo el objeto de trabajo y algunos obstáculos. El robot debe evitar interferencias con estos objetos durante su movimiento.
La tarea se refiere al trabajo que debe realizar el robot, como soldar, pintar o manipular, etc. Suele definirse como la diferencia entre dos estados del entorno, y debe describirse y almacenarse en el controlador del robot con el lenguaje o los programas adecuados.
El controlador se utiliza para recibir la información detectada por los sensores internos y externos del robot, procesarla y generar señales de control de acuerdo con un determinado programa de control, accionando las distintas articulaciones del cuerpo del robot y completando así la tarea encomendada. El cuerpo del robot es el mecanismo mecánico que realiza la tarea, formado por un conjunto de mecanismos de movimiento interconectados que incluyen brazos, articulaciones y efectores finales.
En ingeniería práctica, el cuerpo del robot también se conoce como manipulador, brazo robótico, mano mecánica, etc. La mayoría de los cuerpos robóticos son estructuras mecánicas articuladas con varios grados de libertad. Robots de soldadura suelen tener 6 grados de libertad, 3 de los cuales guían la herramienta final hasta la posición requerida, y los otros 3 se utilizan para controlar la postura de la herramienta.
I. Formas de la estructura del cuerpo del robot
En sentido amplio, los mecanismos robóticos pueden considerarse en general un tipo de varilla que incluye piezas como brazos, muñecas, garras y mecanismos de marcha. En el caso de los robots soldadores, su estructura corporal incluye principalmente las partes del brazo y la muñeca.
Para un cuerpo rígido libre, tiene 6 grados de libertad en el espacio tridimensional, como se muestra en la figura 2. Para completar cualquier operación espacial, el robot también necesita 6 grados de libertad.
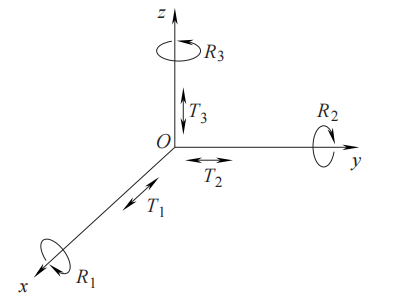
El movimiento del robot es una combinación de los movimientos del brazo y la muñeca. Normalmente, la parte del brazo tiene 3 articulaciones, que se utilizan para cambiar la posición del punto de referencia de la muñeca, llamado mecanismo de posicionamiento; la parte de la muñeca también tiene 3 articulaciones, normalmente estos 3 ejes de articulación se cruzan, utilizados para cambiar la postura de la herramienta final, llamado mecanismo de orientación. Por lo tanto, todo el robot puede considerarse como el mecanismo de posicionamiento conectado al mecanismo de orientación.
1. Estructura del brazo
El brazo del robot es la parte que realiza directamente la operación, y su estructura afectará en gran medida a la capacidad del robot. En términos generales, el brazo se compone de barras y de las articulaciones (pares cinemáticos) que las conectan. Una articulación tiene uno o varios grados de libertad.
Los llamados grados de libertad son un indicador de la flexibilidad del movimiento del robot, es decir, del número de movimientos individuales independientes. Los grados de libertad que pueden producir movimiento activo por el actuador se denominan grados de libertad activos, y los que no pueden producir fuerza motriz se denominan grados de libertad pasivos. La Tabla 1 muestra los símbolos y direcciones de movimiento de articulaciones representativas de un solo grado de libertad.
Tabla 1 Articulaciones de un grado de libertad
Nombre | Símbolo | Ejemplo |
Traducción | ![]() | ![]() |
Rotación | ![]() | ![]() |
Rotación ① | ![]() | ![]() |
Rotación ② | ![]() |
Los métodos de construcción de miembros y articulaciones pueden dividirse a grandes rasgos en dos tipos. Desde el punto de vista general del brazo, los miembros y articulaciones que lo componen están conectados en serie, lo que se conoce como robots de miembros en serie o robots de cadena abierta, mientras que los conectados en paralelo se denominan robots de miembros en paralelo o robots de cadena cerrada. En la figura 3 se muestran ejemplos de los grados de libertad de las manos robóticas de miembros en serie y en paralelo. De hecho, la mayoría de las manos robóticas son del tipo de miembros en serie.
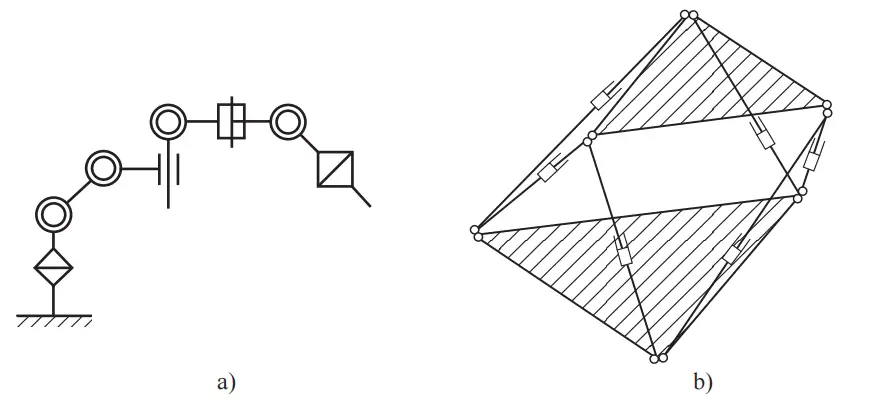
a) Tipo de miembro en serie
b) Tipo de miembro paralelo
El método de construcción de los grados de libertad afecta en gran medida a la amplitud de movimiento y la operatividad del robot, entre otras prestaciones. Por ejemplo, una articulación esférica es una articulación de tres grados de libertad que puede moverse en cualquier dirección, lo que puede determinar fácilmente una postura adecuada para la tarea. Sin embargo, debido a las limitaciones del actuador, es difícil realizar plenamente esta función. Por ello, los robots suelen conectar en serie tres mecanismos de un solo grado de libertad para conseguir estos tres grados de libertad.
Utilizando un método de conexiónincluso con los mismos tres grados de libertad, existen muchas combinaciones diferentes de grados de libertad, cada una con funciones distintas.
Por ejemplo, existen muchos métodos de construcción específicos para un mecanismo de muñeca de 3 grados de libertad. Considerando las condiciones de tener grados de libertad de traslación y rotación en los ejes x, y, y z, si no hay desplazamiento entre eslabones adyacentes, y los ejes de las articulaciones adyacentes son perpendiculares o paralelos entre sí, hay un total de 63 tipos. Además, con la inclusión de tres grados de rotación, un brazo de 6 grados de libertad tiene nada menos que 909 formas de construir grados de libertad.
Por lo tanto, es necesario determinar la forma eficaz de construir grados de libertad basándose en criterios como los requisitos de la operación objetivo.
El objetivo principal del brazo es posicionarse en el espacio tridimensional, para lo cual, como ya se ha mencionado, son necesarios tres grados de libertad. Si se considera la combinación de grados de libertad traslacional, rotacional y de rotación, hay un total de 27 formas de construir grados de libertad. Sin embargo, basándose en su forma de movimiento, las formas representativas de construir grados de libertad pueden dividirse en los cuatro tipos siguientes:
- Robot de coordenadas cilíndricas.
- Robot de coordenadas esféricas.
- Robot de coordenadas cartesianas.
- Robot articulado.
El robot de tipo coordenadas cilíndricas, visto en la Figura 4, está formado por una combinación de una rotación y dos traslaciones; el robot de tipo coordenadas esféricas, visto en la Figura 5, está formado por una combinación de rotación, giro y traslación.
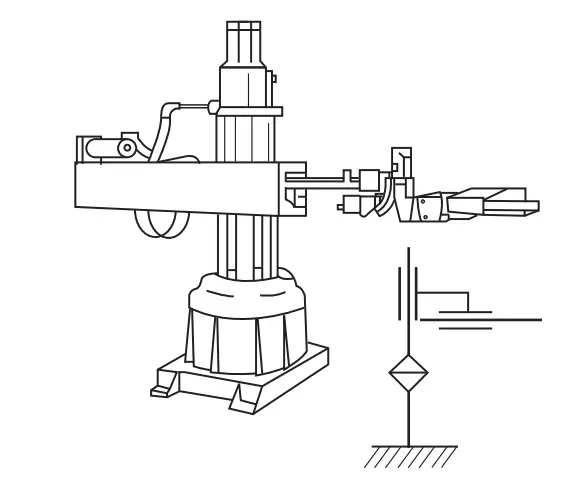
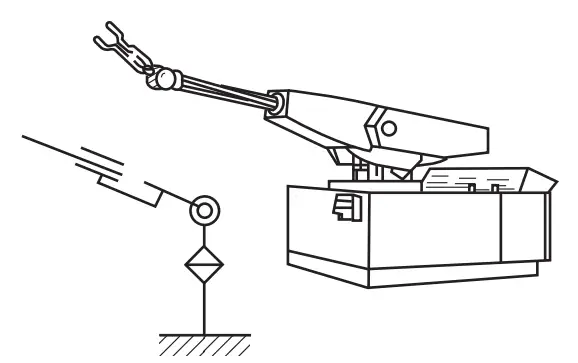
Estos dos tipos de robots, con un grado de libertad rotacional central, tienen una gran amplitud de movimiento y sus cálculos de coordenadas son relativamente sencillos. El primer robot práctico robots industrialesVersatran" y "Unimate", adoptaron mecanismos de coordenadas cilíndricas y esféricas, respectivamente.
El robot de coordenadas cartesianas (Figura 6) tiene grados de libertad independientes en los ejes x, y y z, una estructura sencilla, una gran precisión y un cálculo y control de coordenadas extremadamente simples. Sin embargo, su rango de movimiento no es amplio, lo que dificulta la realización de acciones a alta velocidad.
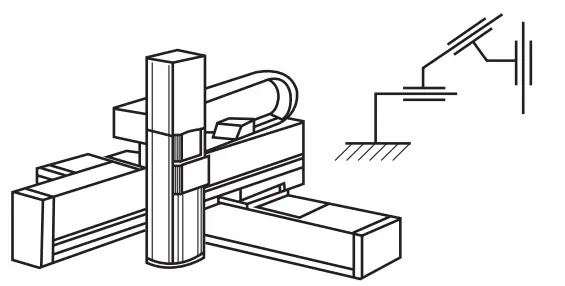
El robot articulado se compone principalmente de grados de libertad de rotación y giro, que pueden verse como una estructura que imita un brazo humano, con una estructura de articulación de enlace que tiene una articulación de codo. En este caso, la parte que va del codo al hombro se denomina brazo, y la que va del codo a la muñeca, antebrazo. Esta estructura es la más eficaz para determinar cualquier posición y postura en el espacio tridimensional. Tiene una buena adaptabilidad a diversas tareas, pero su desventaja es que el cálculo y el control de coordenadas son relativamente complejos, y es difícil lograr una gran precisión.
El robot articulado, en función de su método de construcción de grados de libertad, puede dividirse a su vez en varias categorías.
La figura 7 es un brazo general, que adopta una estructura de grados de libertad de rotación, giro y rotación. El brazo de la figura 8 utiliza un enlace de paralelogramo y monta el actuador utilizado para el accionamiento de la articulación en la base del brazo.
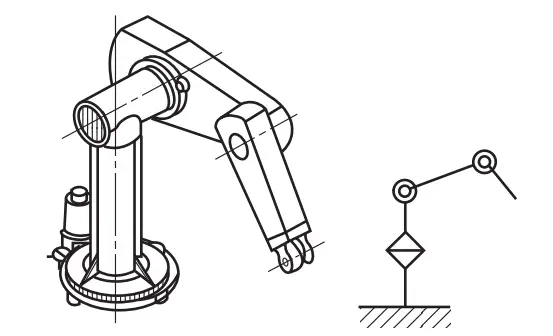
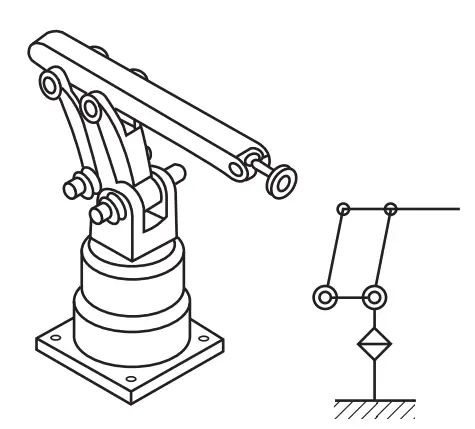
La figura 9 se denomina robot SCARA (Selective Compliance Assembly Robot Arm), y la estructura frontal del brazo adopta grados de libertad que pueden moverse arbitrariamente dentro de un plano bidimensional, por lo que tiene las características de alta rigidez en la dirección vertical y baja rigidez (compliance) en la dirección horizontal.
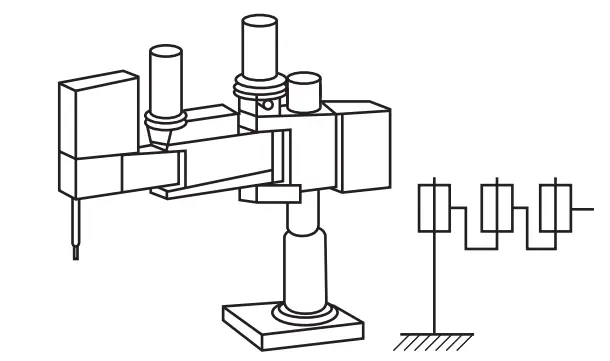
Sin embargo, en el funcionamiento real, no se debe principalmente a esta propiedad especial de conformidad que posee, sino a que puede realizar de forma más sencilla acciones en un plano bidimensional, por lo que se utiliza ampliamente en operaciones de montaje.
2. Estructura de la muñeca
La muñeca del robot es la pieza de conexión entre el brazo y la herramienta final, utilizada para cambiar la posición y orientación de la herramienta en el espacio. La estructura de la muñeca suele ser compleja, lo que afecta directamente a la destreza del robot. La muñeca más común consta de dos o tres ejes articulares perpendiculares entre sí, siendo la primera articulación de la muñeca la cuarta articulación del robot.
(1) Muñeca esférica de dos grados de libertad
La figura 10 es una simple muñeca esférica Pitch-Roll. Tres engranajes cónicos A, B y C forman un mecanismo diferencial, con engranajes A y B conectados a dos motores de accionamiento mediante transmisión por cadena o correa, utilizando la diferencia de velocidad y el sentido de giro de los engranajes A y B para sintetizar el sentido de giro y la velocidad de la herramienta.
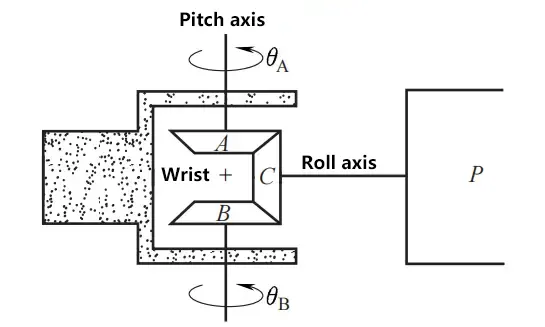
(2) Muñeca ortogonal de tres ejes
La figura 11 muestra un diagrama esquemático y de transmisión de una muñeca de 3 grados de libertad, con tres ejes perpendiculares entre sí y que se cruzan en un punto. Teóricamente, esta muñeca puede alcanzar cualquier postura, pero debido a las limitaciones estructurales de los ángulos articulares, no puede alcanzar ninguna postura. Este tipo de muñeca es el más común en los robots.
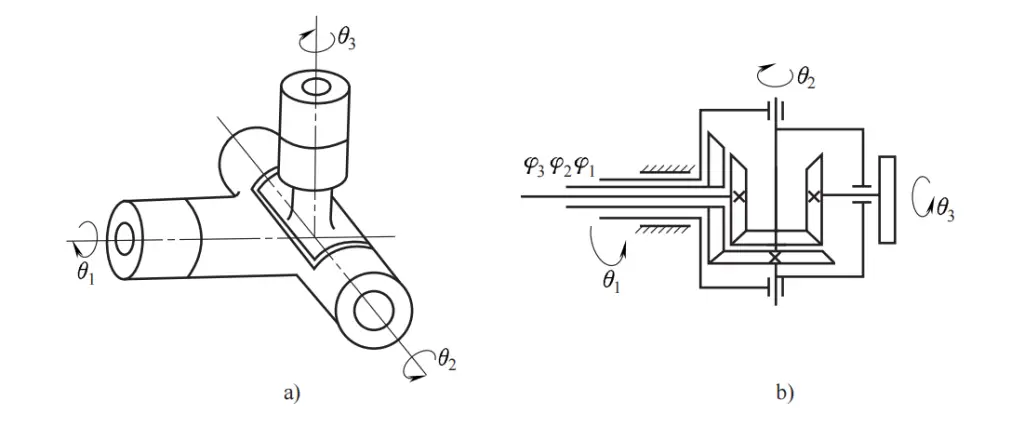
a) Diagrama esquemático
b) Diagrama de transmisión
II. Mecanismo de accionamiento de la articulación del robot
Los principales accionamientos de los robots se dividen en accionamiento hidráulico, accionamiento neumático y accionamiento eléctrico, etc.
La principal ventaja del accionamiento hidráulico es su gran potencia, su estructura sencilla, la eliminación de los engranajes reductores, la conexión directa con la barra accionada y su rápida respuesta. El servoaccionamiento hidráulico tiene una gran precisión, pero requiere una fuente hidráulica adicional y es propenso a las fugas de líquido, de ahí que el accionamiento hidráulico se utilice sobre todo en sistemas robóticos de muy alta potencia.
Los actuadores neumáticos tienen fuentes de energía y estructuras sencillas, pero en comparación con los actuadores hidráulicos, tienen menor potencia en las mismas condiciones de volumen (debido a la menor presión), y su velocidad no es fácil de controlar, por lo que se utilizan sobre todo en sistemas de control de puntos de baja precisión.
Los actuadores eléctricos son los más utilizados en la actualidad. Disponen de fuentes de energía sencillas, una amplia gama de cambios de velocidad, alta eficiencia y gran precisión de velocidad y posición, pero a menudo están conectados con engranajes reductores, lo que dificulta el accionamiento directo. Los actuadores eléctricos pueden dividirse en DC, AC servo motor drive, y stepper motor drive.
Estos últimos son principalmente de control en bucle abierto, de control sencillo pero no de alta potencia, y se utilizan sobre todo en sistemas robóticos de baja precisión y potencia. Los servomotores de CC tienen muchas ventajas, pero sus escobillas son propensas al desgaste y pueden formar chispas con facilidad. Con el progreso tecnológico, los servomotores de CA han ido sustituyendo gradualmente a los servomotores de CC como principales actuadores en robots en los últimos años.
1. Servomotor de CC
Los servomotores de CC tienen una inercia rotacional pequeña, una respuesta rápida de arranque y parada, una amplia gama de cambios de velocidad, una alta eficiencia y una gran precisión de control de velocidad y posición.
Los servomotores de CC tienen muchas ventajas y una elevada relación coste-rendimiento, por lo que siempre han sido el motor estándar de las plataformas robóticas. Sin embargo, sus escobillas son propensas al desgaste y pueden formar chispas con facilidad. Por eso se han desarrollado los motores sin escobillas, que utilizan circuitos Hall para la conmutación.
La figura 12 muestra un servomotor de CC y un amplificador de accionamiento.
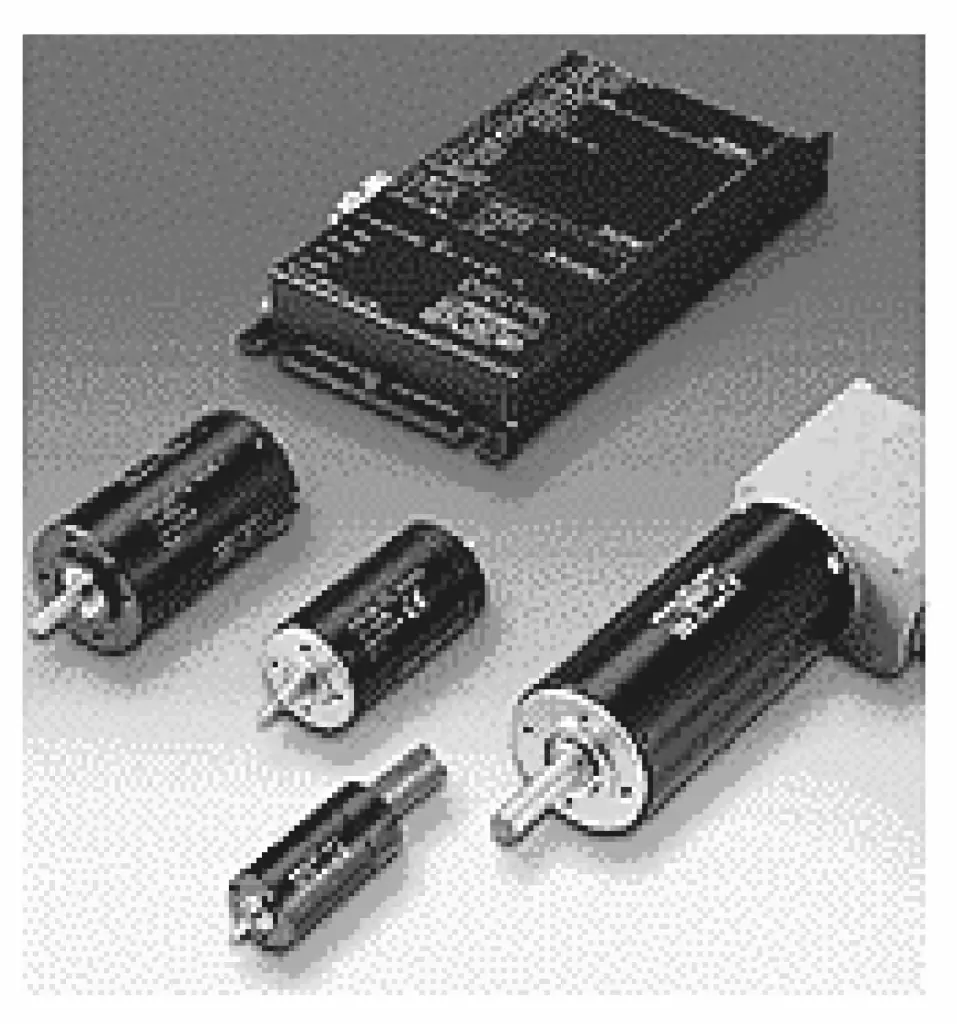
2. Servomotor de CA
Los servomotores de CA tienen mayor potencia que los de CC, no necesitan escobillas, tienen un alto rendimiento y son fáciles de mantener, por lo que son los más utilizados en robots industriales. La figura 13 muestra un servomotor de CA y un amplificador de accionamiento.
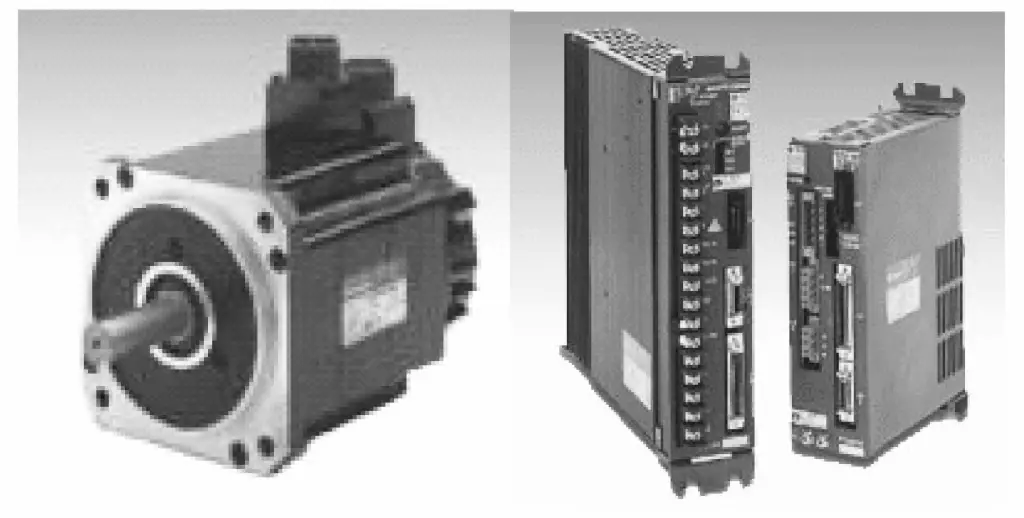
Los principales parámetros técnicos de los servomotores de CA son similares a los de los servomotores de CC.
3. Motor paso a paso
Los motores paso a paso son un tipo de motor sin escobillas, con imanes montados en el rotor y bobinados montados en la carcasa. Los motores paso a paso son esencialmente motores de baja velocidad, fáciles de controlar, capaces de realizar movimientos precisos, con una velocidad de funcionamiento óptima de 50~100r/min. La figura 14 muestra un motor paso a paso y un excitador.
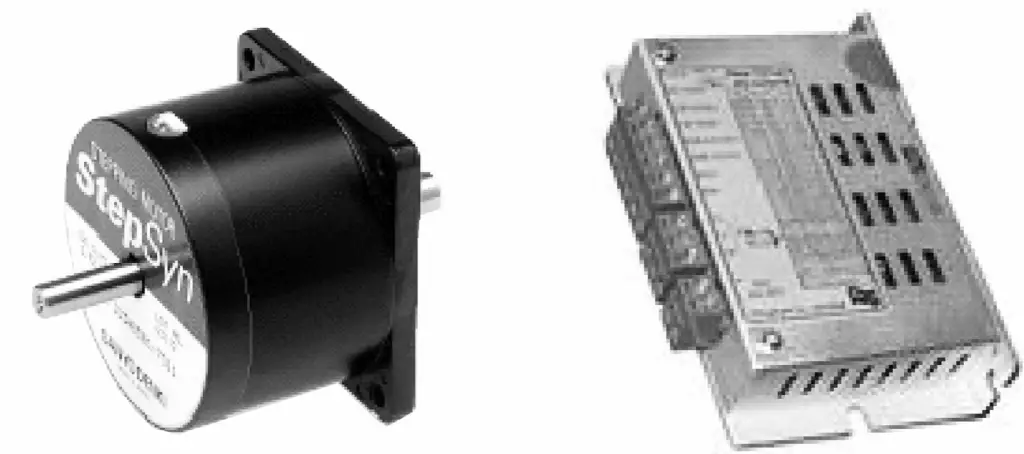
Los accionamientos de motor paso a paso son principalmente de control en bucle abierto, sencillos de controlar pero no potentes, con buenos efectos de frenado, pero pueden experimentar pérdidas de paso a velocidades muy bajas o bajo cargas pesadas, a menudo utilizados en sistemas robóticos de baja precisión y potencia.
III. Mecanismo de transmisión de articulaciones robóticas
Existen dos tipos de métodos de accionamiento de articulaciones: accionamiento directo y accionamiento indirecto. El método de accionamiento directo conecta directamente el eje de salida del excitador al eje de la articulación del brazo robótico. El método de accionamiento indirecto transmite la fuerza del excitador a la articulación a través de un reductor o de un eje de acero. cable metálicocorrea, enganche paralelo, etc.
La ventaja del accionamiento directo es que hay menos sistemas mecánicos entre el excitador y la articulación, con lo que se reduce el impacto de factores no lineales como la fricción, lo que redunda en un mejor rendimiento del control. Sin embargo, por otro lado, para accionar directamente la articulación del brazo, el par de salida del excitador debe ser muy grande, además, hay que tener en cuenta la dinámica del brazo.
El motor de par desarrollado en la década de 1980, cuyo sistema mecánico consiste principalmente en rodamientos, puede lograr una excelente capacidad de accionamiento inverso (accionamiento del eje de salida del conductor desde el lado de la articulación). En la figura 15 se muestra un ejemplo de estructura de articulación que utiliza un motor de par para accionamiento directo. Los robots que utilizan estos métodos de accionamiento directo suelen denominarse Robots de Accionamiento Directo (Robots DD).
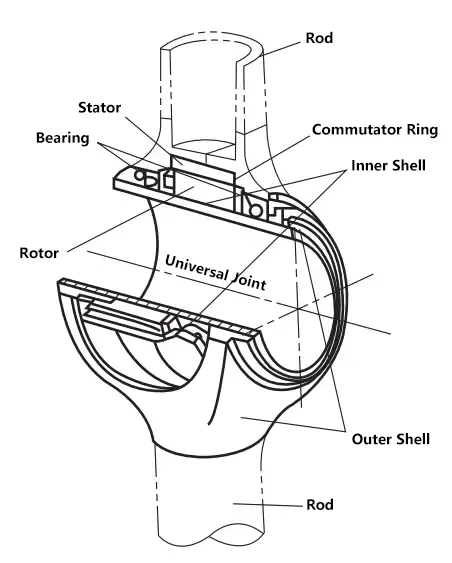
La mayoría de las articulaciones robóticas son de accionamiento indirecto. Para este tipo de accionamiento indirecto, el par de salida del controlador suele ser significativamente inferior al par necesario para accionar la articulación, por lo que debe utilizarse un reductor.
Además, dado que el brazo adopta generalmente una estructura de viga en voladizo, la posición de instalación del controlador que acciona la articulación del robot de múltiples grados de libertad aumentará la carga sobre el controlador de la articulación raíz del brazo. Por lo general, la solución a este problema puede lograrse con los siguientes mecanismos de accionamiento simples.
1. Cadenas, correas de acero
Este método también sitúa al conductor lejos de la articulación, como uno de los medios de conducción a distancia. Las cadenas y las correas de acero tienen una buena rigidez y pueden transmitir un gran par, por lo que se utilizan a menudo en robots de tipo SCARA. El método de accionamiento por correa dentada se muestra en la figura 16.
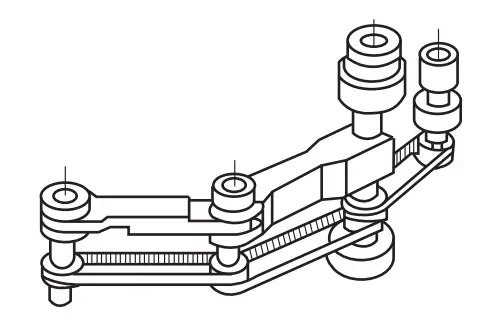
2. Enlace en paralelogramo
La característica de este método es que puede instalar el controlador en la base del brazo, y esta estructura hace que el cálculo de transformación de coordenadas sea extremadamente simple, un ejemplo se muestra en la Figura 17.
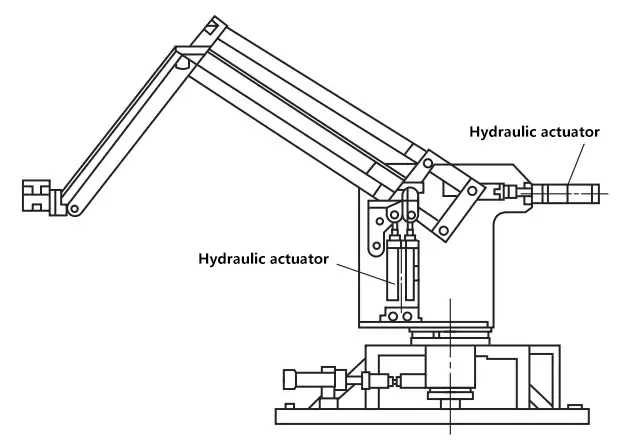
IV. Mecanismos comunes de reducción para articulaciones robóticas
Como se ha mencionado anteriormente, en el proceso de accionamiento de articulaciones robóticas con motores eléctricos, teniendo en cuenta el par de accionamiento y la precisión de control, generalmente se requiere un mecanismo de reducción. Los mecanismos de reducción comunes utilizados en robots incluyen reductores armónicos y reductores de molinete cicloidal RV, y la transmisión helicoidal también se utiliza en la transmisión lineal de algunos robots.
1. Reductor de armónicos
El reductor de transmisión armónica incluye tres componentes básicos: generador de ondas, flexspline y spline circular, como se muestra en la Figura 18. Cualquiera de los tres componentes puede ser fijo, siendo los otros dos activos y pasivos, que pueden conseguir reducción o aceleración, o utilizarse como dos entradas y una salida, formando una transmisión diferencial. La figura 19 muestra una estructura esquemática del reductor de transmisión armónica.
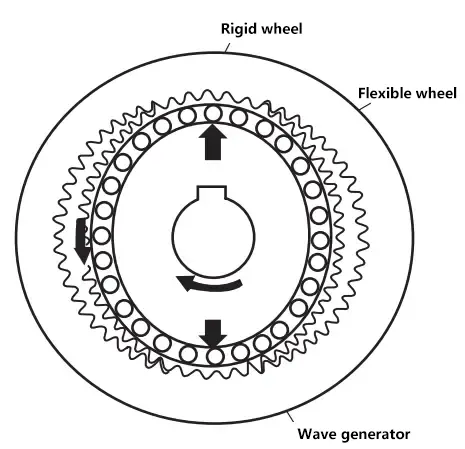
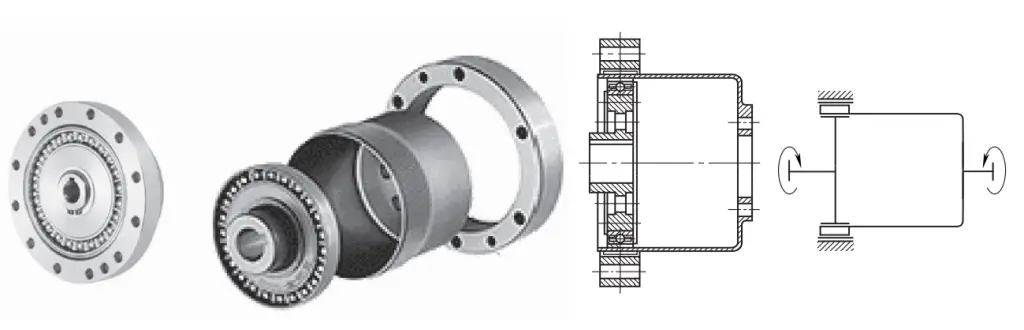
El principio de funcionamiento del reductor de accionamiento armónico se muestra en la figura 20. Cuando el spline circular está fijo, el generador de ondas está activo y el flexspline está pasivo, el flexspline se deforma bajo la acción del generador de ondas elípticas, con los dientes del flexspline en ambos extremos del eje mayor del generador de ondas engranando completamente con los dientes del spline circular.
En ambos extremos del eje menor del generador de ondas, los dientes de la flexspline se desenganchan completamente de los dientes de la spline circular; en los lados del eje mayor elíptico, los dientes de la flexspline y los dientes de la spline circular se encuentran en un estado parcialmente engranado. En el lado de rotación del eje mayor en sentido positivo, se denomina zona de engrane; en el lado de rotación del eje mayor en sentido contrario, se denomina zona de desengrane.
Debido a la rotación continua del generador de ondas, los cuatro estados de engrane, engrane completo, desenganche y desenganche completo cambian en secuencia, ciclando continuamente. Dado que la flexspline tiene unos pocos dientes menos (normalmente 2 ó 4) que la spline circular, cuando el generador de ondas gira una vuelta, la flexspline gira unos pocos dientes en ángulo en la dirección opuesta, consiguiendo así una gran relación de reducción.
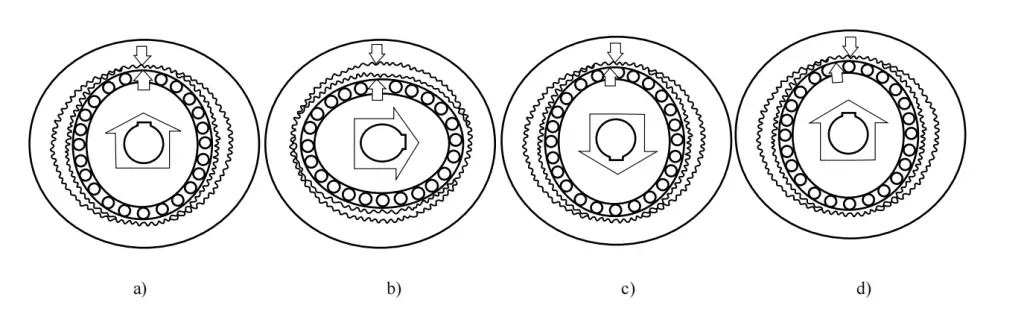
a)0°
b)90°
c)180°
d)360°
En comparación con la transmisión por engranajes general, la transmisión armónica presenta las siguientes características principales:
(1) Gran relación de transmisión, la relación de transmisión de una sola etapa puede ser 50~300.
(2) Transmisión suave, gran capacidad de carga.
Como muchos dientes están engranados en la transmisión al mismo tiempo, la transmisión es suave y la capacidad de carga es alta. En las mismas condiciones de trabajo, el volumen puede reducirse en 20%~50%.
(3) Desgaste pequeño y uniforme de la superficie del diente, alta eficiencia de transmisión.
Si los parámetros de engrane se seleccionan correctamente, la velocidad relativa de deslizamiento de las superficies de los dientes es muy baja, lo que se traduce en un desgaste mínimo y un alto rendimiento. Cuando la estructura es razonable y la lubricación es buena, para una transmisión con i=100, la eficiencia η puede alcanzar 0,85; para una transmisión con i=75, la eficiencia η puede alcanzar 0,92.
(4) Alta precisión de transmisión.
Con la misma precisión de fabricación, la precisión de la transmisión armónica puede ser un nivel superior a la de la transmisión por engranajes ordinaria. Si las superficies de los dientes están bien rectificadas, la precisión de transmisión de la transmisión armónica transmisión por engranaje puede ser cuatro veces superior a la de la transmisión por engranajes ordinaria.
(5) Contragolpe pequeño.
El juego de la transmisión armónica de precisión puede ser generalmente inferior a 3′~1′, e incluso se puede lograr una transmisión sin juego.
(6) El movimiento puede transmitirse a través de una pared sellada.
Cuando se utiliza una transmisión fija flexspline de copa larga, el movimiento puede transmitirse a una caja sellada, algo difícil de conseguir con otros mecanismos de transmisión.
(7) El accionamiento armónico no puede obtener una salida intermedia, y la rigidez de la flexspline tipo copa es relativamente baja.
Basándose en las características anteriores de los reductores de armónicos, se utilizan ampliamente en la transmisión de articulaciones robóticas, sirviendo a menudo como dispositivo de desaceleración y transmisión para las articulaciones de las muñecas robóticas.
2.RV Reductor de molinete cicloidal
El dispositivo de transmisión de molinete cicloidal RV se compone de un conjunto de engranajes planetarios de una etapa seguido de un reductor de molinete cicloidal de una etapa, como se muestra en la figura 21.
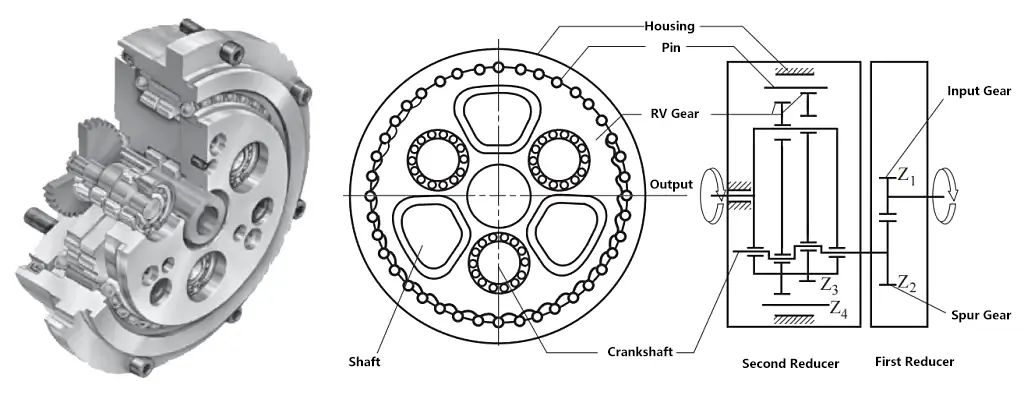
Tiene un eje de entrada, que acciona 2~3 engranajes planetarios distribuidos por la circunferencia a través del engranaje del eje. Cada engranaje planetario está conectado a un eje excéntrico bidireccional, que a su vez acciona dos ruedas cicloidales RV radialmente opuestas para que rueden sobre la carcasa fija con dientes internos. A continuación, las ruedas cicloidales accionan el eje de salida del disco para que gire a través de 2~3 ejes de pasadores no cilíndricos distribuidos por la circunferencia.
Comparado con el accionamiento armónico, el accionamiento de molinete cicloidal RV, además de tener las mismas características de alta relación de velocidad, transmisión coaxial, estructura compacta y alta eficiencia, su característica más significativa es la buena rigidez y la pequeña inercia rotacional.
En comparación con los dispositivos de transmisión armónica producidos en Japón y utilizados en robots, en las mismas condiciones de par de salida, velocidad y relación de reducción, el volumen de ambos es casi igual, pero la rigidez de transmisión de este último es 2~6 veces mayor. Convertido al eje de entrada, la inercia rotacional es más de un orden de magnitud menor, pero el peso ha aumentado en 1~3 veces.
La razón del gran peso total y de la inercia rotacional del par del volante de inercia particularmente pequeño del eje de entrada es que el dispositivo de transmisión RV añade una etapa de transmisión planetaria, permitiendo que el eje de entrada y los engranajes se conviertan en un cilindro no muy grande, mientras que las piezas giratorias de detrás, aunque muy pesadas, tienen su inercia rotacional convertida al eje de entrada se vuelven muy pequeñas después de una etapa de reducción.
Debido a la alta rigidez, la pequeña inercia rotacional y el peso relativamente grande, este reductor es particularmente adecuado para la primera etapa de la articulación de rotación (articulación de la cintura) de los robots, donde el gran peso propio se encuentra en la base, y la alta rigidez y la pequeña inercia rotacional desempeñan plenamente sus funciones.
La alta rigidez puede aumentar significativamente la frecuencia natural de toda la máquina, reduciendo las vibraciones; la pequeña inercia rotacional puede mejorar la velocidad de respuesta y reducir el consumo de energía durante las aceleraciones y desaceleraciones frecuentes. La figura 22 muestra una imagen real del reductor RV.
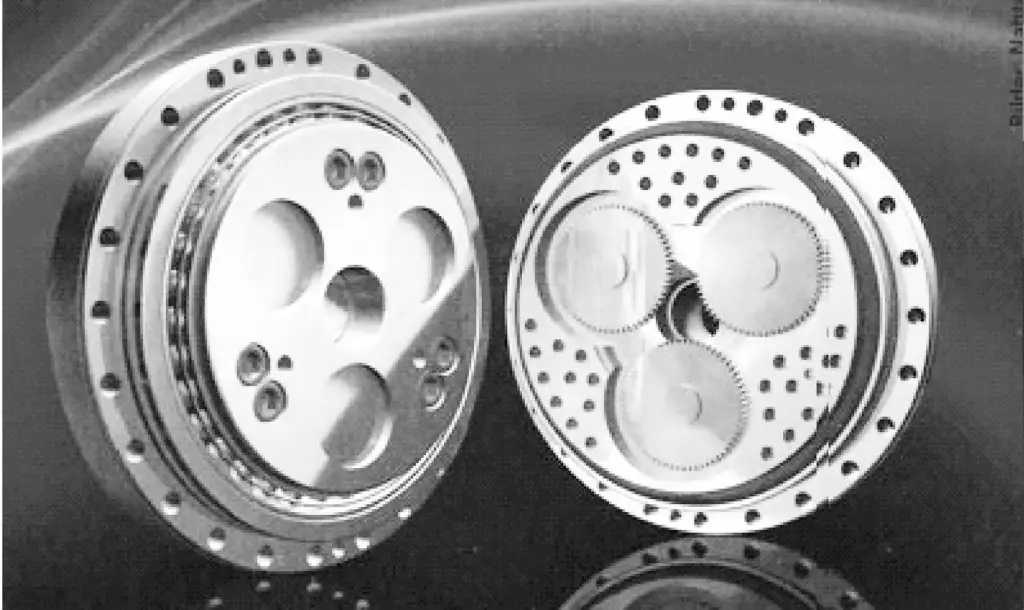
3.Transmisión helicoidal rodante
La transmisión helicoidal rodante puede lograr la conversión entre movimiento rotativo y movimiento lineal. Su estructura implica la colocación de bolas adecuadas entre el tornillo con ranuras helicoidales y la tuerca, cambiando la fricción de deslizamiento entre el tornillo y la tuerca en fricción de rodadura, un tipo de transmisión helicoidal, como se muestra en la figura 23. El tornillo 1 y la tuerca 3 tienen ranuras helicoidales con superficies en forma de arco, y ensamblándolos forman una pista de rodadura helicoidal, con la bola 4 girando y rodando en ella.
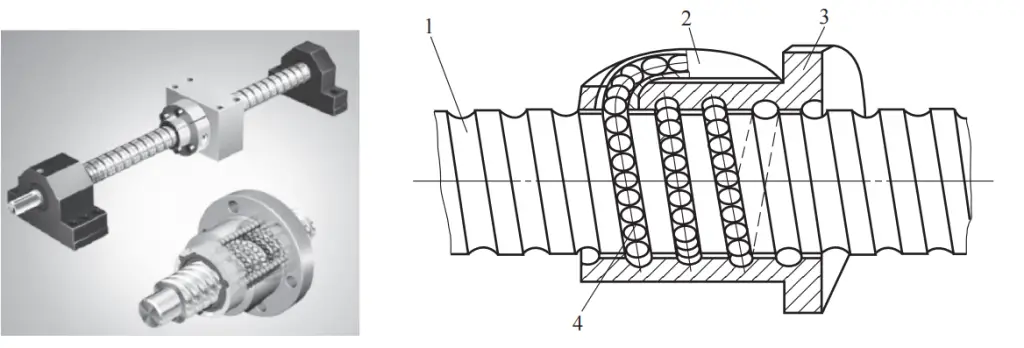
1-Tornillo
2-Carretera
3-Tuercas
Bola 4
El canal de retorno de bolas tiene circulación interna y externa. La estructura de circulación interna se muestra en la figura 24, donde las bolas en el modo de circulación interna permanecen siempre en contacto con la superficie del tornillo. En los dos canales de circulación adyacentes se instalan deflectores. Cuando el tornillo gira, las bolas empiezan a moverse desde la salida del deflector, se mueven durante un ciclo y luego entran en el deflector, formando un bucle de circulación.
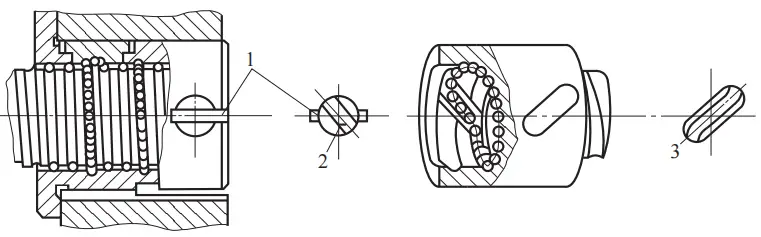
1-llave
2,3-Llave deflectora
Generalmente, se instalan de 2 a 4 inversores en la misma tuerca y se distribuyen uniformemente a lo largo de la circunferencia de la tuerca. En la estructura de circulación interna, el bucle de circulación de bolas es corto, suave, eficiente, y el tamaño radial de la tuerca también es menor, pero los requisitos de precisión de fabricación son elevados.
La estructura de la circulación externa de la bola se muestra en la figura 25. Para el tipo de ranura helicoidal, cuando el tornillo gira, la bola se mueve desde el punto inicial, y cuando alcanza el punto final, el bloqueador de bola bloquea la bola en la ranura helicoidal dentro del soporte de la tuerca, y la ranura helicoidal conduce al punto inicial, formando un bucle de circulación.
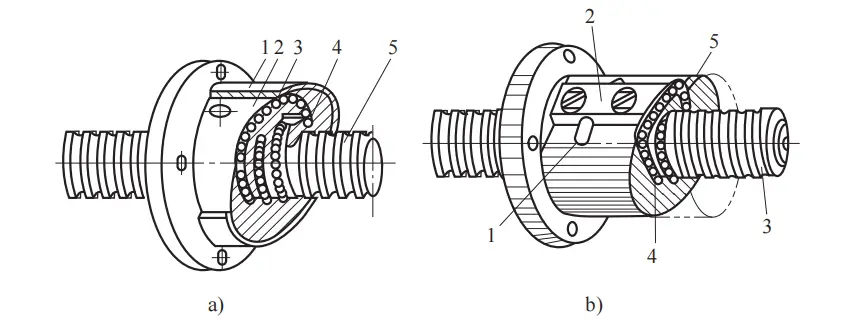
a) Tipo ranura helicoidal
1-Manga
2 Tuercas
Bola 3
Bloqueador de 4 bolas
5 tornillos
b) Tipo de inserción del tubo
1-Tubo doblado
2-Placa de presión
3 tornillos
Bola 4
5-Carretera
Para el tipo de inserción de tubo, cuando el tornillo gira, la bola empieza a moverse y puede circular por cualquier canal entre dos tubos doblados, con el tubo doblado dentro del soporte de la tuerca, no instalando tubos doblados en el canal de circulación ya existente.
Para eliminar la holgura, la tuerca se divide en dos secciones, y la posición axial relativa de las dos secciones de la tuerca se ajusta con calzos, tuercas dobles o diferencia de dientes para eliminar la holgura y aplicar precarga, de modo que la holgura pueda ser nula bajo la carga nominal de extracción.
La figura 26 muestra el ajuste de la separación y la precarga, entre los cuales el tipo de doble tuerca es el más utilizado, y el tipo de diferencia de dientes es el más fiable. La transmisión helicoidal rodante es la que más teme caer en polvo, limaduras de hierro, granos de arena. Normalmente, ambos extremos de la tuerca deben sellarse, y la parte expuesta del tornillo debe sellarse con una cubierta de "fuelle" o una envoltura de banda de acero.
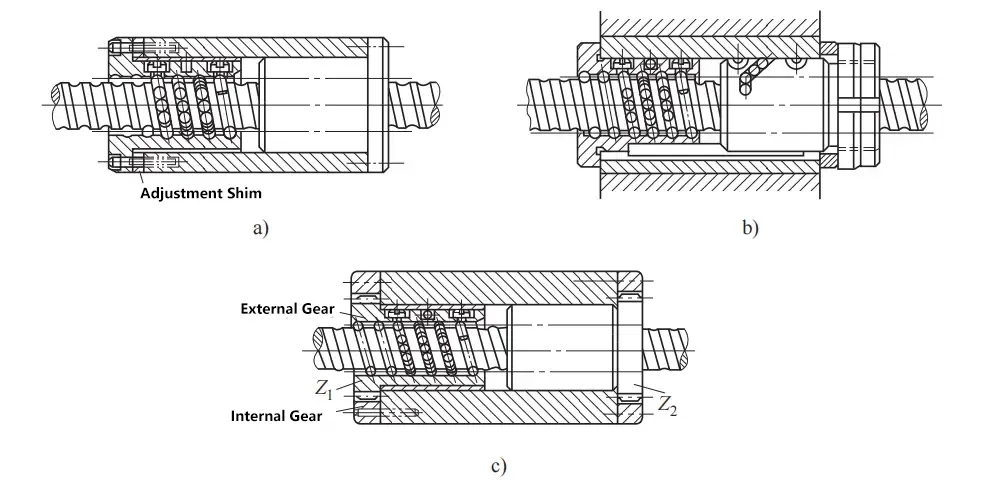
a) Tipo de calza
b) Tipo de doble tuerca
c) Tipo de diferencia entre dientes
Las condiciones de trabajo del par helicoidal rodante son similares a las de los rodamientos, por lo que su capacidad de carga también se expresa en términos de carga dinámica nominal y carga estática nominal, siendo la definición, el cálculo y el método de selección básicamente los mismos que los de los rodamientos.
Las especificaciones de tamaño del par helicoidal de rodadura se determinan generalmente por la carga dinámica nominal o la carga estática nominal. Para tornillos de rodadura esbeltos que soportan cargas de compresión, se requiere una comprobación de la estabilidad de la barra de compresión; para tornillos de rodadura con alta velocidad y gran distancia de apoyo, se requiere un cálculo de la velocidad crítica.