O corte é um método de corte primário utilizado no trabalho a frio, caracterizado por uma elevada eficiência de produção, superfícies de corte relativamente lisas e a capacidade de cortar chapas metálicas e vários perfis.
1. Conhecimentos básicos de processamento de cisalhamento
Existem muitos métodos de processamento de cisalhamento, mas a essência é aplicar força de cisalhamento ao material através das lâminas superior e inferior, fazendo com que o material sofra deformação por cisalhamento e, finalmente, fracture e se separe. Por conseguinte, para dominar a tecnologia de processamento de corte, é necessário compreender as condições de deformação e tensão dos materiais no processamento de corte, os requisitos de forma geométrica das lâminas e o cálculo da força de corte.
O trabalho a frio utiliza frequentemente o cisalhamento oblíquo mostrado na Figura 3-42 na produção. Aqui, apenas o processo de cisalhamentoA força de corte, a força de corte e os parâmetros geométricos da lâmina do corte oblíquo são analisados e o método de cálculo da força de corte é introduzido.
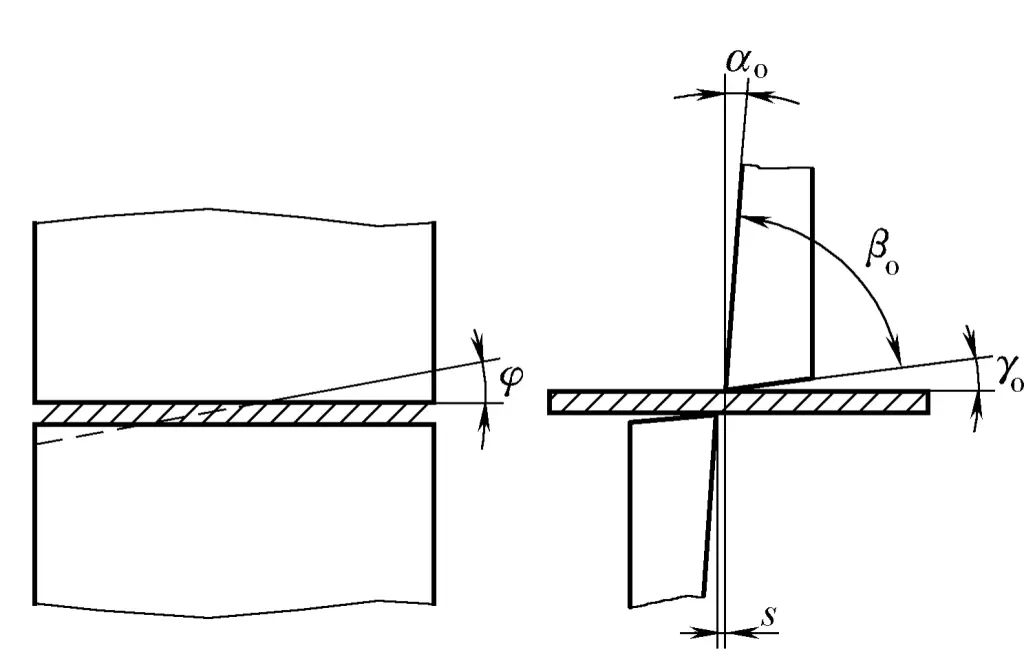
- γ o - Ângulo de inclinação
- α o - Ângulo de folga
- β o - Ângulo da cunha
- s - Folga da lâmina
- φ - Ângulo do bisel da lâmina
Durante o cisalhamento, o material é colocado entre as lâminas superior e inferior, e o processo de deformação e cisalhamento do material sob a ação da força de cisalhamento é mostrado na Figura 3-43.
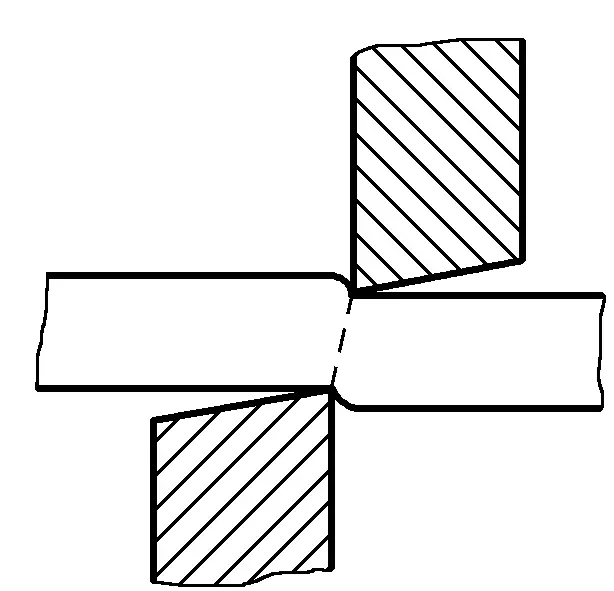
Quando a extremidade da lâmina começa a entrar em contacto com o material, este encontra-se na fase de deformação elástica. À medida que a lâmina superior continua a descer, a pressão da lâmina sobre o material aumenta, causando a flexão plástica local e a deformação por tração do material (especialmente quando a abertura da lâmina é grande).
Ao mesmo tempo, a borda da tesoura também começa a pressionar o material, formando uma área de ângulo colapsado e uma zona de corte de plástico brilhante, onde o estado de tensão e a deformação do metal perto da lâmina são extremamente desiguais. À medida que a profundidade da pressão da lâmina aumenta, forma-se uma grande concentração de tensão e deformação no bordo.
Quando esta deformação atinge o limite de deformação do material, aparecem microfissuras no material. À medida que o fenómeno de cisalhamento se expande, as fissuras de cisalhamento produzidas pelos bordos superior e inferior da lâmina coincidem, provocando a separação final do material.
A Figura 3-44 mostra a superfície cisalhada do material, que tem características regionais distintas, claramente divididas em ângulo colapsado, banda brilhante, banda de cisalhamento e rebarbas. A formação do ângulo de colapso 1 deve-se ao facto de o material ser esticado e deformado perto da borda quando a lâmina pressiona o material; a banda brilhante 2 forma-se quando a lâmina aperta e corta o material, com uma superfície lisa e plana; a banda de corte 3 forma-se quando o material é cortado e separado, com uma superfície rugosa, ligeiramente inclinada, não perpendicular à superfície da placa; e as rebarbas 4 são produzidas quando aparecem microfissuras.
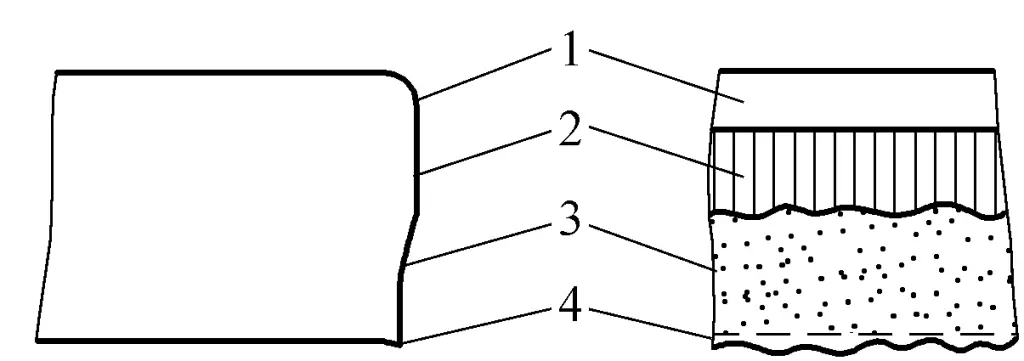
1 - Ângulo recolhido
2 - Banda brilhante
3 - Zona de cisalhamento
4 - Burr
A relação de distribuição do ângulo de colapso, da banda brilhante, da zona de cisalhamento e da rebarba em toda a superfície de cisalhamento varia com as propriedades do material, a espessura, a forma da lâmina, a abertura da lâmina e o método de prensagem durante o cisalhamento.
O gume da lâmina é afiado, facilitando a compressão e o corte no material, o que é benéfico para aumentar a banda brilhante, enquanto um ângulo frontal maior r o da lâmina pode aumentar a nitidez do gume.
Quando a folga da lâmina é grande, a tensão de tração no material aumenta, facilitando a produção de fissuras de cisalhamento, e a fase de deformação plástica termina mais cedo, pelo que a banda brilhante será menor, enquanto a zona de cisalhamento, o ângulo colapsado e a rebarba são todos maiores. Inversamente, quando a folga da lâmina é pequena, a tensão de tração no material diminui, a produção de fissuras é suprimida, pelo que a banda brilhante se torna maior, enquanto o ângulo de colapso, a banda de cisalhamento, etc., diminuem.
No entanto, uma folga demasiado grande ou demasiado pequena fará com que as fissuras nas superfícies superior e inferior não coincidam numa linha. Quando a folga é demasiado pequena, aparecem fissuras latentes e rebarbas maiores na superfície de corte; quando a folga é demasiado grande, a zona de corte, o ângulo de colapso, a rebarba e a inclinação aumentam, tornando a superfície extremamente rugosa.
Se o material for pressionado firmemente na lâmina inferior, pode reduzir a tensão de tração, aumentando assim a banda brilhante. Além disso, uma boa plasticidade e uma menor espessura do material também podem aumentar a banda brilhante.
A partir da análise acima, pode concluir-se que as principais medidas para aumentar a banda brilhante, reduzir o ângulo de colapso e a rebarba e, assim, melhorar a qualidade da superfície de corte são: aumentar a nitidez do gume da lâmina, adotar o valor mínimo de um intervalo razoável entre as lâminas e pressionar o material firmemente na lâmina inferior, etc.
A folga da lâmina s é um parâmetro geométrico para evitar a colisão entre as lâminas superior e inferior, reduzir a força de corte e melhorar a qualidade da superfície de corte. O valor da folga razoável é uma gama de tamanhos, sendo o limite superior designado por folga máxima e o limite inferior por folga mínima. A determinação de uma folga razoável da lâmina depende principalmente das propriedades e da espessura do material que está a ser cortado, como se mostra na Tabela 3-1. Vários equipamentos de corte são fornecidos com placas de dados de ajuste de folga muito específicas, que podem ser utilizadas como base para ajustar a folga da lâmina.
Tabela 3-1 Intervalo de folga razoável da lâmina
Material | Folga (em percentagem da espessura da placa) | Material | Folga (em percentagem da espessura da placa) |
Ferro puro | 6~9 | Aço inoxidável | 7~ 11 |
Aço macio (aço com baixo teor de carbono) | 6~9 | Cobre (duro, macio) | 6~ 10 |
Aço duro (aço de carbono médio) | 8 ~12 | Alumínio (duro) | 6 ~10 |
Aço silício | 7 ~ 11 | Alumínio (macio) | 5~8 |
2. Equipamento de cisalhamento
Existem muitos tipos de máquinas de corte normalmente utilizadas no trabalho a frio, incluindo: tipo pórtico oblíquo máquina de corteMáquina de corte de entrada transversal oblíqua, máquina de corte de disco, máquina de corte vibratória e máquina combinada de puncionamento e corte.
(1) Máquina de cisalhamento oblíquo tipo pórtico
A máquina de corte oblíquo do tipo pórtico, conforme ilustrado na Figura 3-45, é utilizada principalmente para cortar cortes rectos. É simples de operar, conveniente para a alimentação, rápida na velocidade de corte, deformação mínima do material cortado e alta precisão da superfície de corte, pelo que é mais amplamente utilizada no corte de chapas metálicas.
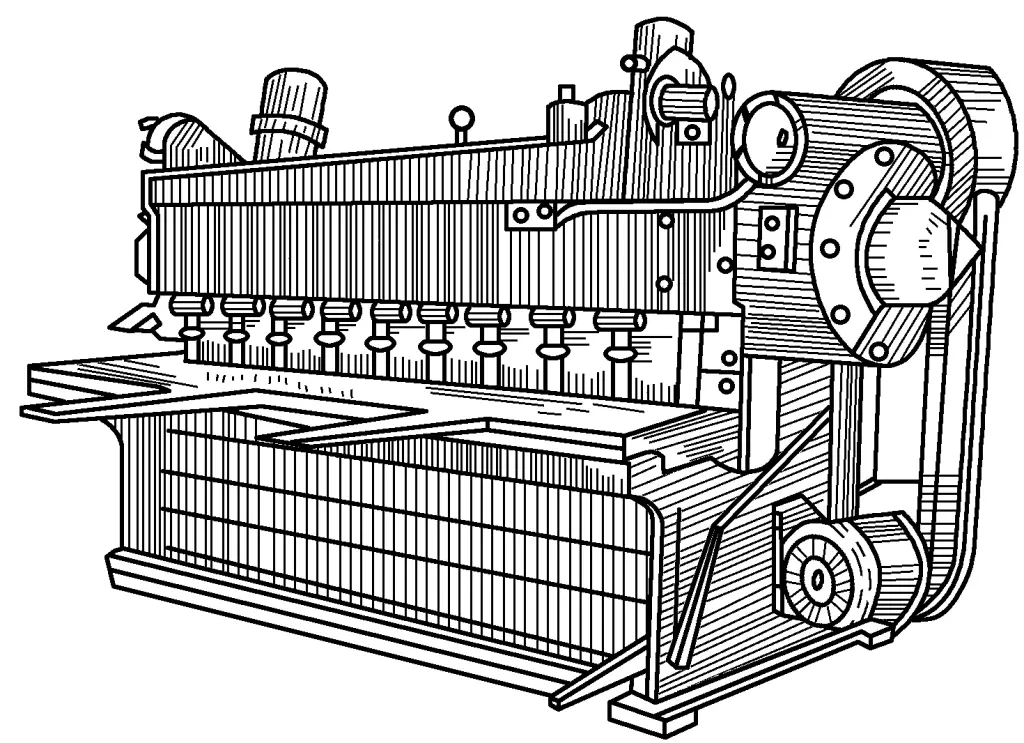
(2) Máquina de cisalhamento oblíqua de entrada transversal
A máquina de cisalhamento oblíquo de entrada transversal, como mostrado na Figura 3-46, é usada principalmente para cisalhar linhas rectas. Durante o cisalhamento, o material a ser cisalhado pode entrar pelo lado do cisalhamento e pode mover-se ao longo da direção de cisalhamento, permitindo que o cisalhamento seja realizado em segmentos, sem limite no comprimento de cisalhamento. Em comparação com a máquina de cisalhamento oblíquo do tipo pórtico, tem um ângulo de lâmina de cisalhamento maior φ, portanto, maior deformação durante o cisalhamento, e é mais complicado de operar. Geralmente, é melhor usado para cortar placas finas e largas.
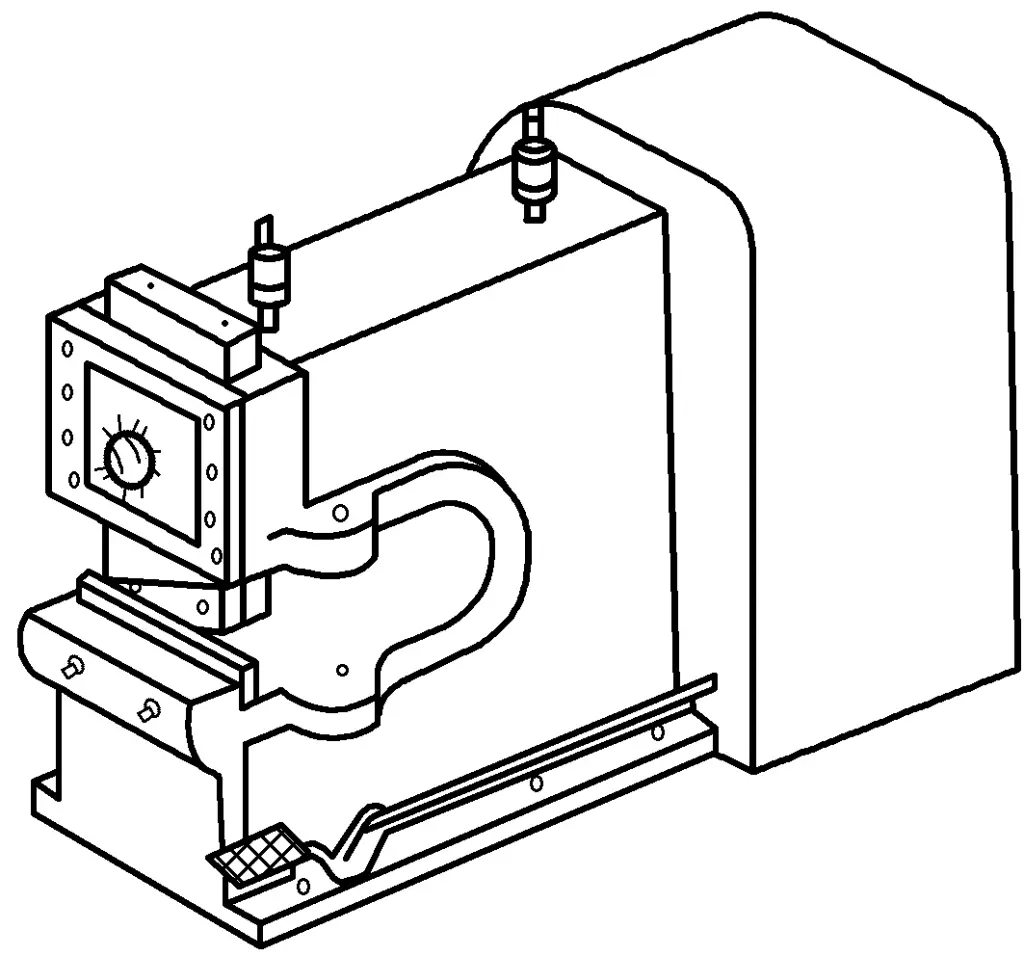
(3) Cama de corte de disco
A parte de corte do leito de corte de disco é constituída por cortadores rotativos superiores e inferiores. Durante o cisalhamento, os cortadores rotativos superior e inferior rodam em direcções opostas à mesma velocidade e o material é cisalhado e transportado entre os dois cortadores rotativos, como se mostra na Figura 3-47a. O trabalho a frio utiliza normalmente o leito de cisalhamento do disco do cortador rotativo inclinado, como se mostra na Figura 3-47b.
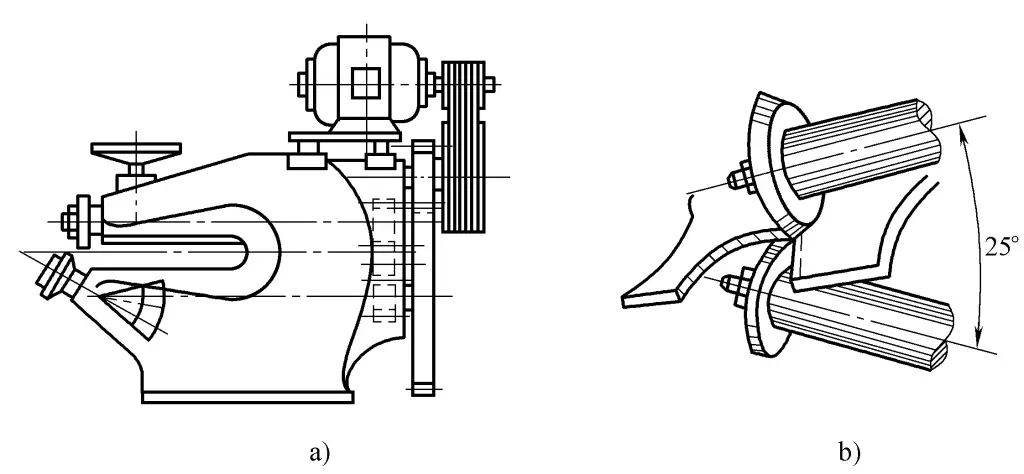
O leito de cisalhamento de disco, devido à muito pouca sobreposição das arestas de corte superior e inferior e ao comprimento de cisalhamento instantâneo extremamente curto, e a rotação do material da placa é basicamente sem restrições, é adequado para curvas de cisalhamento e pode cisalhar continuamente. No entanto, o material a ser cisalhado dobra-se significativamente e as arestas têm rebarbas, geralmente, o leito de cisalhamento do disco só pode cisalhar placas mais finas.
(4) Cama de cisalhamento vibratória
O leito de cisalhamento vibratório, como mostrado na Figura 3-48, tem as suas lâminas superior e inferior inclinadas com um grande ângulo de intersecção, e a parte de cisalhamento é extremamente curta. Durante o funcionamento, a placa da lâmina superior vibra milhares de vezes por minuto.
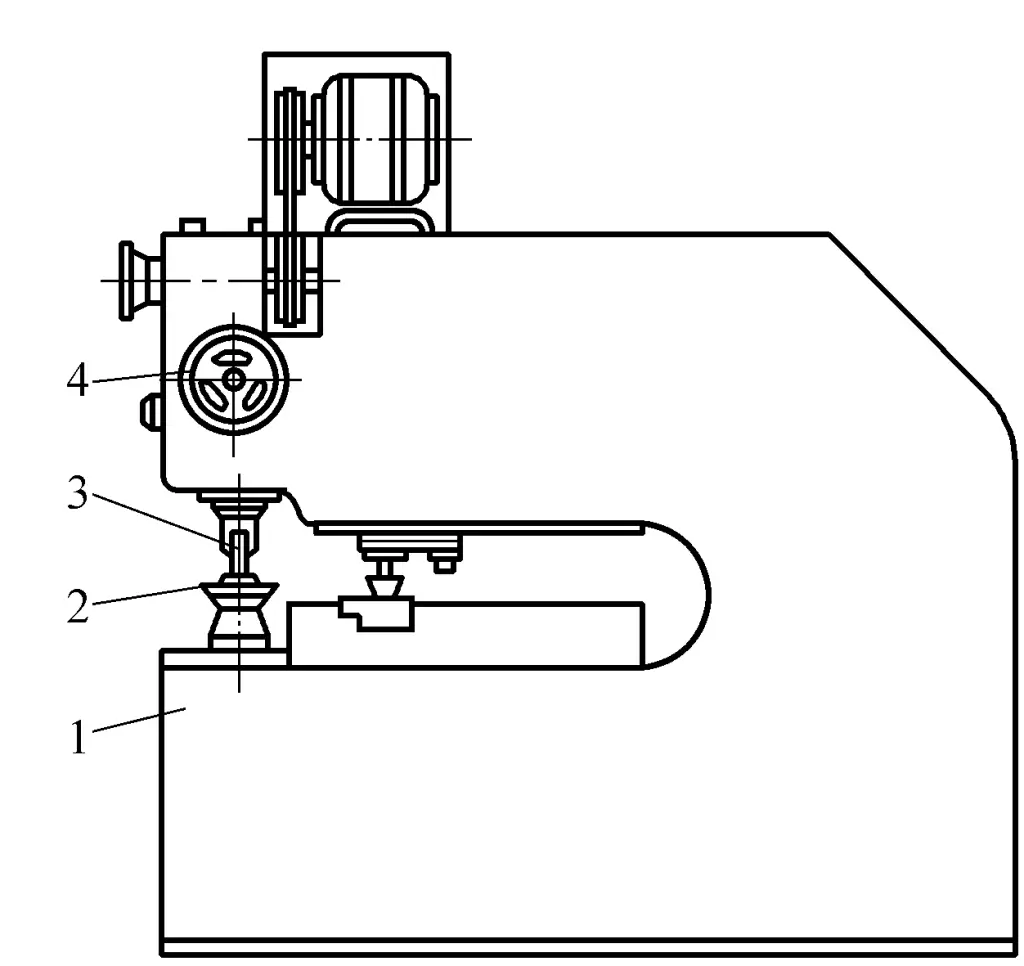
Carroçaria com 1 cama
2-Lâmina inferior
3-Lâmina superior
Pega de 4 fases
Os leitos de cisalhamento vibratórios podem cortar várias curvas e orifícios internos em chapas metálicas, mas as suas lâminas são propensas ao desgaste, as superfícies de corte têm rebarbas, a produtividade é baixa e só podem cortar chapas metálicas mais finas.
(5) Máquina combinada de puncionamento e cisalhamento
As máquinas combinadas de puncionamento e cisalhamento são normalmente compostas por uma tesoura inclinada, uma tesoura para perfis de aço e um pequeno punção, capazes de cortar chapas de aço e vários perfis de aço, e podem efetuar estampagem e puncionamento de pequenas peças.
3. Tipos e desempenho técnico das máquinas de corte
Os operadores de máquinas de tosquia devem ter a capacidade de efetuar uma análise simples das máquinas de tosquia utilizadas, o que ajuda a dominar e a melhorar os métodos de tosquia, bem como a manter e utilizar corretamente as máquinas de tosquia. Com base na sua forma estrutural, é possível avaliar preliminarmente o tipo de máquina de tosquia e, em seguida, compreender em pormenor o significado representado pelo seu modelo.
O modelo da plataforma de corte descreve o tipo, as características e os parâmetros básicos de funcionamento da plataforma de corte. Por exemplo, a máquina de cisalhamento de pórtico do tipo Q11-13×2500, o significado representado pelo seu modelo
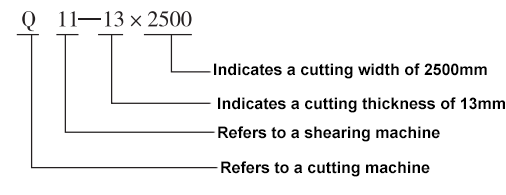
A norma nacional para os números das máquinas-ferramenta foi alterada várias vezes, pelo que, para os diferentes modelos de plataforma de corte representados pelos significados, é necessário consultar as normas nacionais relacionadas com a época de fabrico da plataforma de corte.
Os parâmetros de desempenho técnico dos vários tipos de equipamento de cisalhamento são geralmente registados em placas de identificação incorporadas no corpo da máquina, servindo de base para o processamento do cisalhamento. O desempenho técnico do equipamento também é detalhado no manual do equipamento. Por conseguinte, ao consultar a placa de identificação ou o manual do leito de corte, é possível compreender o seu desempenho técnico.
4. Equipamento tecnológico das máquinas de corte
Para satisfazer as necessidades do processo de corte, as máquinas de corte têm normalmente um equipamento de processamento simples. A Figura 3-49 mostra o equipamento de processo de uma máquina de corte oblíqua típica do tipo pórtico.
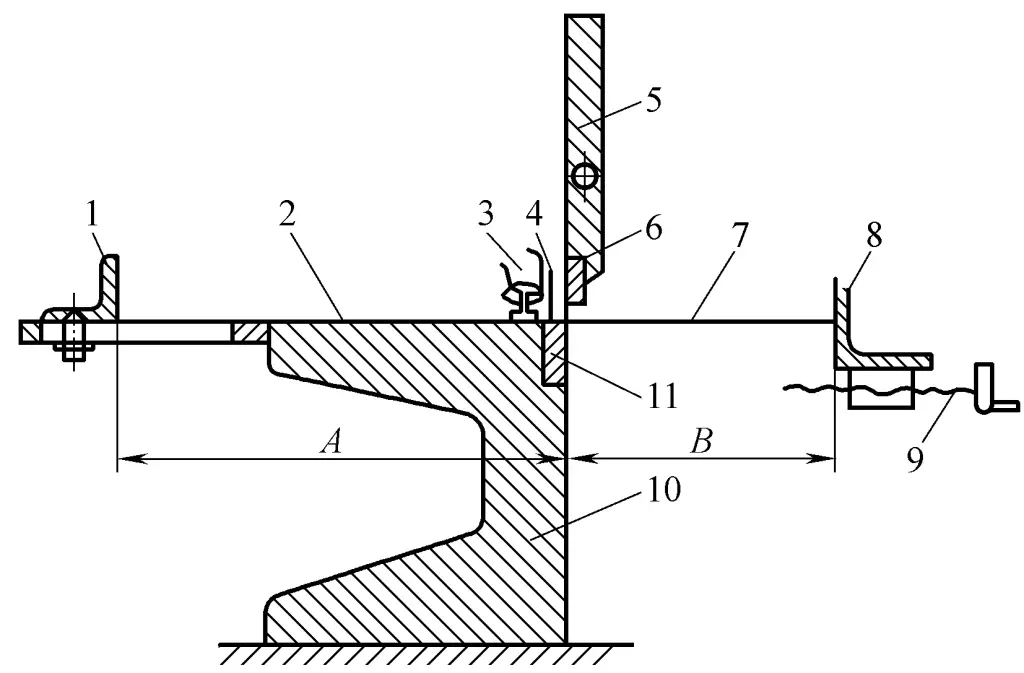
1 - Paragem frontal
2 - Cama
3 - Placa de prensagem
4 - Grelha
5 - Barra de corte do leito de cisalhamento
6 - Lâmina superior
7 - Material da placa
8 - Paragem traseira
9 - Parafuso
10 - Cama
11 - Lâmina inferior
A placa de retenção impede a rotação e o movimento da placa durante o corte para garantir a qualidade do corte. A placa de retenção é accionada pela cambota de trabalho, fixando a placa antes de a lâmina superior entrar em contacto com a placa, completando a fixação automática. Também pode atingir objectivos de fixação utilizando rodas excêntricas manuais, tornando-se um tipo de fixação manual. O portão é um dispositivo de segurança utilizado para evitar que as mãos ou outros objectos entrem na boca da tesoura e causem acidentes.
As placas de medição dianteira e traseira desempenham um papel de posicionamento durante o corte. Ao tosquiar um grande número de peças com o mesmo tamanho, a utilização das placas de medição para posicionamento pode melhorar a eficiência da produção e garantir a qualidade do produto. As placas de posicionamento também podem ser instaladas na mesa.
Algumas fábricas modificaram as suas máquinas de corte de acordo com as suas condições específicas para melhorar a automatização, como a carga e a descarga automáticas, a alimentação automática, o posicionamento (para a linha de corte) e a fixação.
5. O impacto do processo de cisalhamento na qualidade do aço
O corte por cisalhamento é um método eficiente de cortar metal, produzindo cortes relativamente limpos e suaves, mas também tem algumas desvantagens. O corte do aço pode provocar alterações nas propriedades mecânicas e na forma externa, afectando o desempenho do aço. Este facto manifesta-se principalmente nos dois aspectos seguintes:
1) Os materiais de tiras estreitas e longas apresentam uma deformação significativa por flexão e torção após o corte, e devem ser endireitados posteriormente. Além disso, se a abertura da lâmina for inadequada, a secção cortada será áspera e terá rebarbas.
2) Durante o processo de cisalhamento, devido à força de cisalhamento que actua no metal perto do corte, ocorre uma deformação por compressão e flexão, causando um aumento da dureza do metal e do ponto de escoamento, uma diminuição da plasticidade e tornando o material frágil. Este fenómeno é designado por endurecimento por trabalho a frio. A largura da área endurecida está relacionada com os seguintes factores
1) Propriedades mecânicas do aço. Quanto melhor for a plasticidade do aço, maior será a área de deformação e maior será a área de endurecimento; inversamente, quanto maior for a dureza do material, mais estreita será a área de endurecimento.
2) Espessura da chapa de aço. Quanto mais espessa for a chapa de aço, maior será a deformação e maior será a área de endurecimento; inversamente, quanto mais pequena for.
3) Folga da lâmina de cisalhamento s. Quanto maior a folga, mais severa será a flexão do material, portanto, maior será a área de endurecimento.
4) Ângulo da lâmina de cisalhamento φ. Quanto maior o ângulo da lâmina de cisalhamento φ, ao cisalhar a mesma espessura de chapa de aço, se a força de cisalhamento for menor, então a área de endurecimento também é menor.
5) Nitidez da lâmina de cisalhamento. Quanto mais afiada for a lâmina de cisalhamento, maior será a força de cisalhamento e maior será a área de endurecimento.
6) Posição e força de aperto do dispositivo de aperto. Quando o dispositivo de aperto está mais próximo da lâmina de corte e a força de aperto é maior, é menos provável que o material se deforme e a largura da área de endurecimento é reduzida.
Em resumo, a largura da área de endurecimento por trabalho a frio causada pelo processamento de corte do aço está relacionada com vários factores e é o resultado de um efeito abrangente. Quando a espessura da chapa de aço cisalhada é inferior a 25 mm, a largura da área de endurecimento situa-se geralmente entre 1,5 e 2,5 mm.
Para o fenómeno de endurecimento por trabalho a frio no bordo da chapa, quando se fabricam estruturas importantes ou quando o processamento de estampagem a frio ainda é necessário após o corte, é necessário submeter-se a fresagem, aplainamento ou tratamento térmico para eliminar o fenómeno de endurecimento.
II. Princípios e equipamento de puncionamento
1. Princípios de perfuração
O método de processamento que consiste em utilizar uma matriz numa prensa para separar uma parte da folha da outra é designado por corte em branco. O corte em vazio é também um método de corte de aço e, para a produção em série de peças ou produtos moldados, a utilização do corte em vazio pode melhorar a eficiência da produção e a qualidade do produto.
Durante o corte, o material é colocado entre o punção e a matriz e, sob a ação de forças externas, o punção e a matriz geram um par de forças de corte (a linha de corte é normalmente fechada) e o material é separado sob a ação de forças de corte, como se mostra na Figura 3-50.
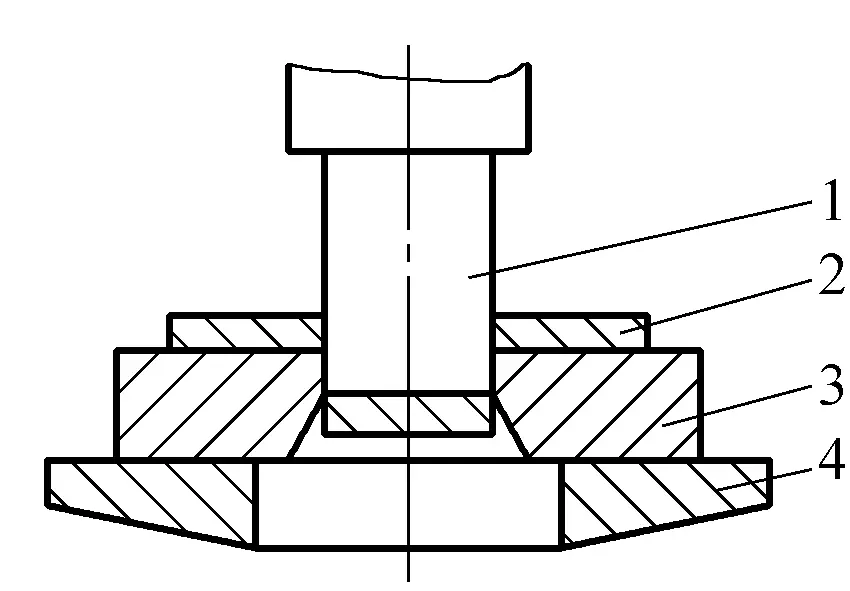
1-Soco
Material de 2 folhas
3-Die
Mesa de trabalho da prensa de 4 punções
O princípio básico do corte é o mesmo que o do cisalhamento, exceto que a aresta de corte reta utilizada no cisalhamento é substituída por uma aresta de corte circular fechada ou de outra forma.
A deformação do material e o estado da secção transversal durante o processo de corte são aproximadamente os mesmos que durante o cisalhamento.
O processo, desde o contacto do punção com o material em folha até à separação do material em folha, é concluído instantaneamente. Quando o espaço entre o punção e a matriz é normal, o processo de deformação do corte pode geralmente ser dividido nas três fases seguintes:
A primeira fase é a fase de deformação elástica. Como se mostra na Figura 3-51a, quando o punção começa a entrar em contacto com a chapa e a pressiona para baixo, sob a pressão do punção e da matriz, a chapa começa a sofrer deformações complexas, tais como compressão elástica, flexão e alongamento (AB'>AB). Neste momento, o punção pressiona ligeiramente a chapa, e a parte inferior da chapa também pressiona ligeiramente o orifício da matriz, formando um filete muito pequeno no ponto de contacto com os bordos do punção e da matriz.
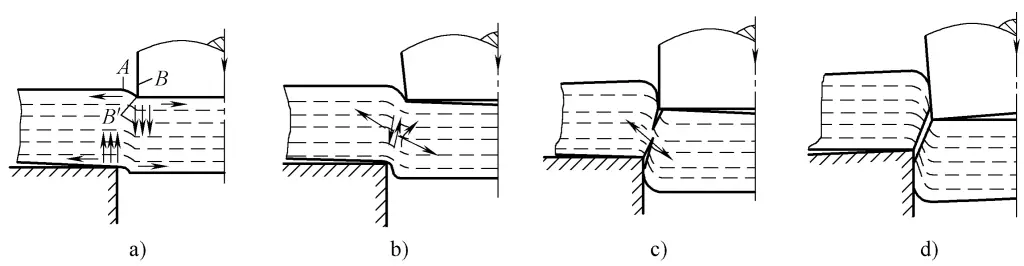
a) Fase de deformação elástica
b) Fase de deformação plástica
c), d) Fase de separação das fracturas
Entretanto, a chapa arqueia ligeiramente, quanto mais duro for o material, maior será o espaço entre o punção e a matriz e mais grave será o arqueamento. À medida que o punção pressiona para baixo, a tensão na chapa perto da aresta de corte aumenta gradualmente até atingir o limite elástico, terminando a fase de deformação elástica.
A segunda fase é a fase de deformação plástica. À medida que o punção continua a pressionar para baixo, fazendo com que a tensão na área deformada da chapa exceda o seu ponto de cedência e atinja condições plásticas, entra na fase de deformação plástica, como se mostra na Figura 3-51b.
Nesta altura, a profundidade do punção que pressiona a folha e a folha que pressiona a matriz aumenta gradualmente, produzindo deformação plástica de corte, formando uma superfície brilhante de corte. À medida que o punção desce, o grau de deformação plástica aumenta, o material na área deformada endurece, a resistência à deformação aumenta continuamente e a força de perfuração também aumenta em conformidade, até que a tensão perto da aresta de corte atinge a resistência à tração, terminando a fase de deformação plástica.
Devido ao espaço entre o punção e a matriz, esta fase também envolve deformações de flexão e alongamento, e quanto maior for o espaço, maiores serão as deformações de flexão e alongamento.
A terceira fase é a fase de separação da fratura. Quando a tensão no interior da chapa atinge a resistência à tração e o punção continua a pressionar, surgem subsequentemente microfissuras nas partes da chapa em contacto com os bordos do punção e da matriz, como se mostra na Figura 3-51c. O ponto de partida das fissuras situa-se geralmente no lado próximo da aresta de corte e, normalmente, ocorre primeiro no lado próximo da aresta da matriz e, depois, no lado próximo da aresta do punção.
À medida que o punção continua a pressionar para baixo, as microfissuras superiores e inferiores já formadas continuarão a expandir-se para o interior da placa ao longo da direção da tensão de corte máxima. Quando as fissuras superior e inferior coincidem, a placa é cisalhada e separada, como se mostra na Figura 3-51d. Subsequentemente, o punção empurra o material separado para o orifício da matriz e o processo de deformação por punção termina.
Nas três fases do processo de deformação por perfuração, a força externa e o tempo necessário para cada fase não são os mesmos. De um modo geral, o tempo de perfuração depende muitas vezes das propriedades do material, e a duração é mais curta quando o material é mais frágil.
2. Equipamento de perfuração
(1) Estrutura da imprensa
A perfuração é geralmente efectuada numa prensa. As prensas normalmente utilizadas incluem as prensas de manivela e as prensas excêntricas, ambas funcionando segundo o mesmo princípio, sendo a principal diferença o fuso principal utilizado.
A estrutura básica de uma prensa de manivela é mostrada na Figura 3-52a, e o princípio de funcionamento é mostrado na Figura 3-52b. O corpo da prensa e a mesa de trabalho estão integrados, com calhas de guia verticais no corpo acima da superfície da mesa de trabalho, permitindo que o cursor se mova para cima e para baixo. As matrizes de perfuração superior e inferior são montadas no cursor e na superfície da mesa de trabalho, respetivamente.
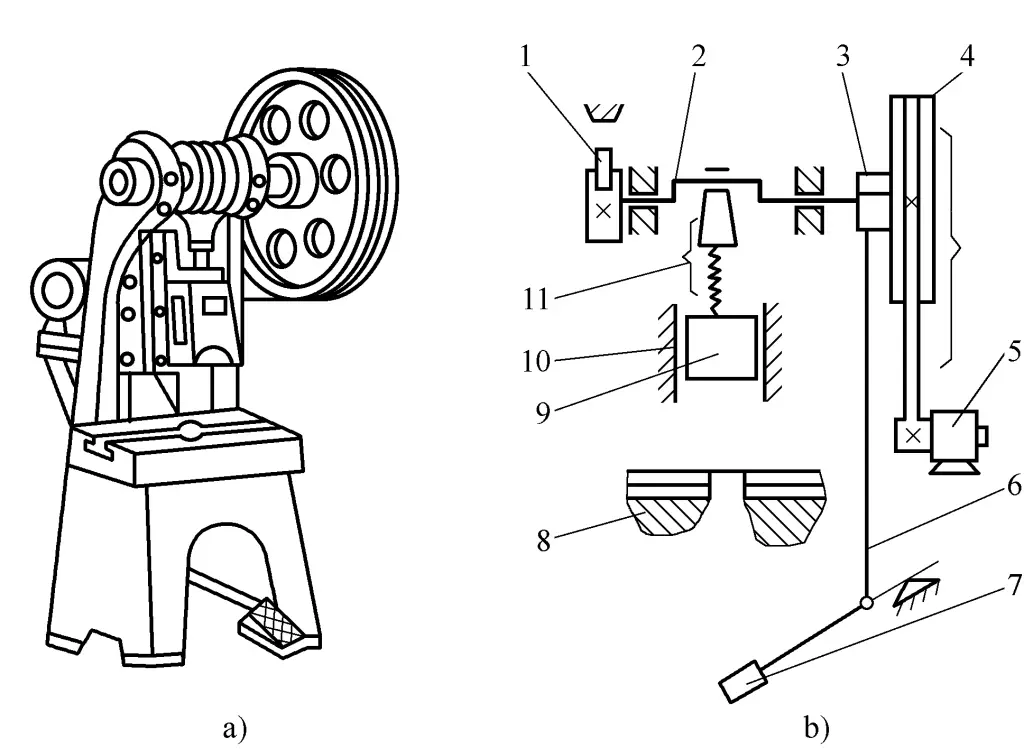
a) Aspeto
b) Diagrama do princípio de funcionamento
1 - Travão
2-Virabrequim
3 embraiagens
4-Polia grande
5-Motor elétrico
6-Bastão de pressão
7-Pedal
8-Bancada de trabalho
9-Deslizador
Carril de 10 guias
11-Barra de ligação
Quando a prensa de punção está a funcionar, o motor aciona primeiro a polia grande para ficar ao ralenti através da correia de transmissão. Depois de pisar o pedal, a embraiagem fecha-se e faz rodar a cambota, o que faz com que a corrediça se mova para cima e para baixo ao longo da calha-guia através da biela, realizando a perfuração.
Se o pedal for imediatamente libertado depois de ter sido pisado, o cursor pára na posição mais alta após um curso de perfuração sob a ação do travão; se o pedal for continuamente pressionado, o cursor continua a mover-se para cima e para baixo para executar a perfuração contínua.
(2) Parâmetros de desempenho técnico da prensa de punção
Os parâmetros de desempenho técnico da prensa de perfuração têm um impacto significativo no trabalho de perfuração. Ao processar a perfuração, é necessário selecionar a prensa de perfuração de acordo com os parâmetros de desempenho técnico.
1) Tonelagem e potência nominal da prensa de punção.
A tonelagem e a potência nominal da prensa de punção são dois indicadores que marcam a capacidade de trabalho da prensa de punção. A força de perfuração e a potência necessárias para as peças efetivamente perfuradas devem ser inferiores a estes dois indicadores da prensa de perfuração. Ao perfurar placas finas, a potência de perfuração necessária é relativamente pequena e geralmente pode ser ignorada.
2) Altura de fecho da prensa de punção.
A distância entre a superfície inferior da corrediça na sua posição mais baixa e a superfície da mesa de trabalho. Quando o dispositivo de regulação ajusta o cursor para a posição limite superior, a altura fechada atinge o seu valor máximo, que é designado por altura máxima fechada. A altura fechada da prensa de punção deve ser compatível com a altura fechada do molde.
3) Traço do cursor.
A distância que o cursor percorre desde a posição mais alta até à posição mais baixa, também conhecida como o curso. O tamanho do curso do cursor determina a altura fechada e a altura aberta da prensa de punção utilizada, e deve assegurar uma alimentação e retração suaves durante o processo de punção.
4) Tamanho da mesa da prensa de punção.
Ao perfurar, o tamanho da matriz deve ser adaptado ao tamanho da mesa de trabalho da prensa de perfuração para garantir que a matriz pode ser firmemente instalada na mesa.
Outros parâmetros de desempenho técnico têm pouco impacto no processo de perfuração e podem ser adequadamente seleccionados de acordo com circunstâncias específicas.
(3) Precauções para utilizar a prensa de punção
1) Antes da utilização, inspecionar todas as peças da prensa de punção e encher todos os pontos de lubrificação com óleo lubrificante.
2) Verificar se a folga entre os casquilhos das chumaceiras e o aperto do travão são adequados.
3) Verificar se existem objectos estranhos presos nas partes móveis.
4) Verificar frequentemente o desgaste e a folga da corrediça e da calha de guia da prensa de punção. Uma folga excessiva afectará a precisão da guia, portanto, a folga entre as calhas de guia deve ser ajustada regularmente. Se o desgaste for demasiado acentuado, deve ser efectuada uma manutenção.
5) Ao instalar a matriz, alinhe o centro de pressão da matriz com o centro de pressão da prensa de punção e certifique-se de que a folga entre as matrizes macho e fêmea é uniforme.
6) Depois de ligar o interrutor, colocar a máquina em vazio 3 a 5 vezes para verificar se o dispositivo de controlo e o estado de funcionamento estão normais.
7) Ao perfurar, concentre-se, não pise o pedal arbitrariamente, e é estritamente proibido esticar as mãos entre os moldes ou fazer com que a cabeça entre em contacto com o cursor, para evitar acidentes.
8) Não perfurar materiais demasiado duros ou que tenham sido temperados. A prensa de punção não deve ser sobrecarregada.
9) Para perfurações de longa duração, prestar atenção para verificar se o molde está solto e se a folga é uniforme.
10) Depois de parar de puncionar, corte a alimentação eléctrica ou bloqueie o interrutor de segurança. As peças perfuradas e os materiais de sucata devem ser removidos atempadamente para manter a área em redor da prensa de perfuração livre de obstáculos.
III. Princípios e métodos de corte com mós
O corte com mó utiliza a rotação a alta velocidade da mó para gerar calor através da fricção com a peça de trabalho, fundindo-a para formar um corte. O corte com rebolo é simples, eficiente, fácil de operar e amplamente utilizado no corte de aço angular, aço de canal, aço plano, tubos de aço e outros perfis, especialmente adequado para corte de aço inoxidávelaço para rolamentos e várias ligas de aço.
A figura 3-53 mostra uma máquina de corte de mós portátil muito utilizada, que consiste numa cabeça de corte 4, um grampo rotativo 1, um mecanismo de regulação central 3 e uma base 2.
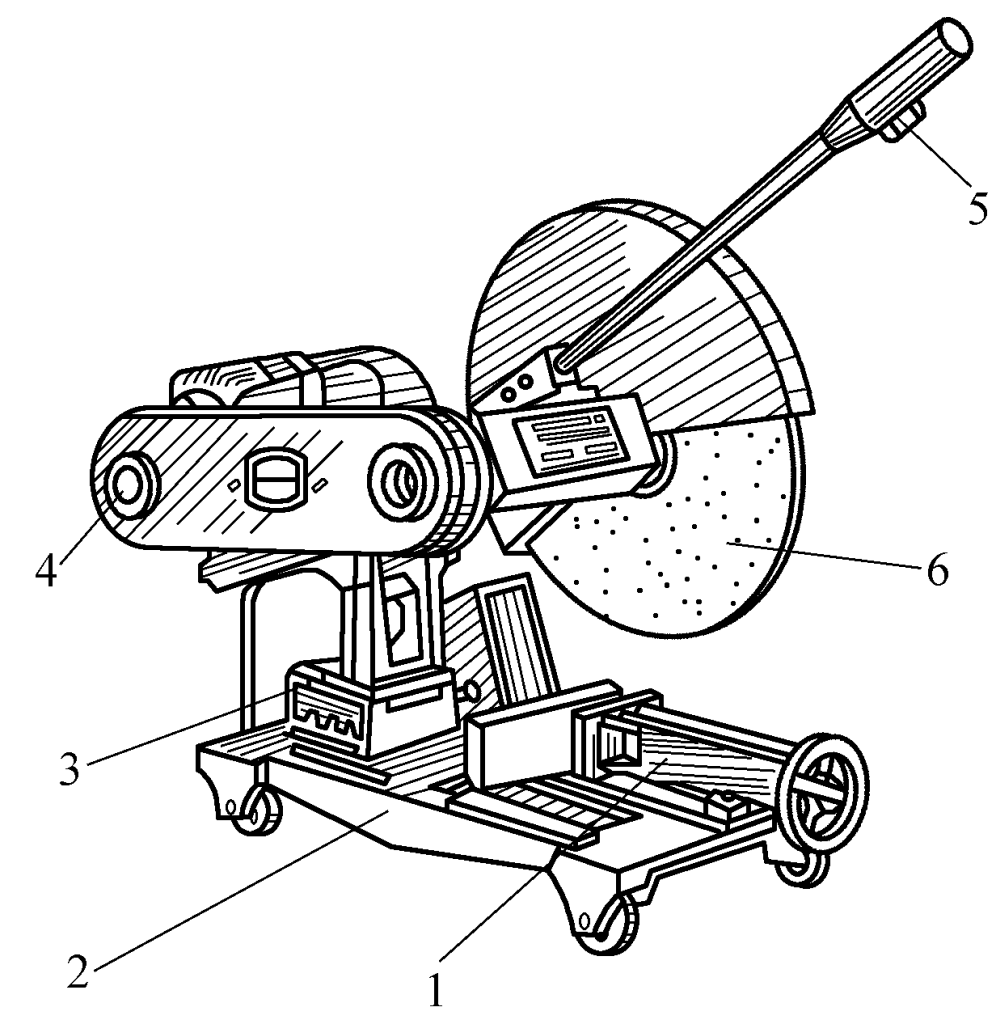
1-Abraçadeira giratória
2-Base
3-Mecanismo de ajustamento central
Cabeça motorizada de 4 cortes
5-Switch
6-Rodas de moagem
A mó normalmente utilizada tem um diâmetro de 300~400mm, espessura de 3mm, e uma velocidade de 2900r/min, com uma velocidade de linha de corte de 60m/s. Para evitar que o rebolo rebente, é utilizado um rebolo reforçado com fibra. Toda a cabeça de potência e o centro do rebolo podem ser ajustados e rodados de acordo com as necessidades de corte, o que pode ser conseguido através de uma pega que também tem um interrutor para controlar o funcionamento do motor.
A morsa rotativa pode ajustar o seu ângulo com o eixo da mó (0°~45°) conforme necessário. Para ajustar, basta desapertar o parafuso sextavado, puxar a cavilha de posicionamento e as maxilas podem rodar para o ângulo necessário em torno do parafuso de articulação. Existem quatro rolos instalados sob a base, permitindo que todo o cortador de mós seja móvel.
Durante o corte, o perfil é montado na morsa rotativa e fixado, ligando o interrutor na pega para acionar o motor que, através da transmissão por correia, faz girar o rebolo a alta velocidade. Quando a velocidade da mó estabilizar, acionar o punho para cortar.