Au cours du processus de fabrication, le pliage des tôles se heurte souvent à divers problèmes de qualité, qui affectent l'amélioration de l'efficacité de la production et la stabilité de la qualité du produit.
Cet article traite des problèmes de qualité de cintrage et de coupe rencontrés dans la pratique de la production, analyse les causes de ces problèmes et propose des solutions afin de fournir une expérience et une référence pour des problèmes similaires qui pourraient survenir dans des pratiques de production ultérieures.
Introduction
Le pliage de tôles consiste à utiliser un Machine à plier CNC équipés de matrices standard (ou spécialisées) pour plier les tôles en diverses formes géométriques de section transversale requises.
La rationalité du processus de pliage affecte directement les dimensions finales et l'apparence du produit. Le choix des bonnes matrices de pliage est crucial pour la forme finale du produit.
Dans la production réelle, en raison de l'incertitude des dimensions du produit et de la diversité des types de produits, nous rencontrons souvent des problèmes tels que des interférences dimensionnelles et des angles de matrices mal adaptés lors de l'usinage à froid des pièces, ce qui pose des défis importants.
La qualité du pliage est influencée par des facteurs tels que la taille et la forme du produit, le matériau, les matrices, l'équipement et les installations auxiliaires, ce qui entraîne divers problèmes de qualité qui ont une incidence sur l'efficacité de la production et la stabilité de la qualité du produit. Il est donc particulièrement important de résoudre et de prévenir ces problèmes de qualité.
Cet article résume et décrit les problèmes de qualité de pliage de tôle les plus courants dans la pratique de la production, analyse leurs causes sur la base de l'expérience de la production et propose des solutions.
Problèmes courants de qualité du cintrage
2.1 Fissuration par flexion
La fissuration par pliage désigne le phénomène par lequel des bavures ou de fines fissures apparaissent souvent sur les bords des matériaux après la découpe, cisaillementLes accessoires de locomotive HXD1C ont été fabriqués à partir de matériaux de base tels que l'acier, l'aluminium ou l'estampage. Un exemple est la fissuration aux coins de la rainure de renforcement en forme de U (2A90100185G00) de l'accessoire de locomotive HXD1C après pliage, comme le montre la figure 1.
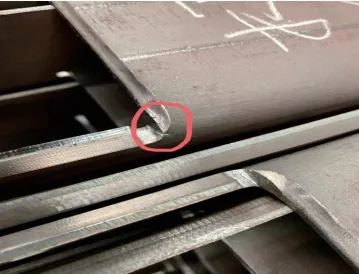
Les principales causes de fissuration par flexion sont les suivantes :
- Bavures non éliminées sur les bords de la pièce.
- Sens de pliage parallèle au sens de laminage de la feuille.
- Excessivement petit rayon de courbure de la feuille.
Dans le processus de fabrication, le phénomène de fissuration par flexion doit être traité en fonction de circonstances spécifiques. Pour le problème de fissuration par flexion illustré à la figure 1, des solutions telles que l'ajout de trous ou de rainures de traitement peuvent être employées, comme illustré à la figure 2.
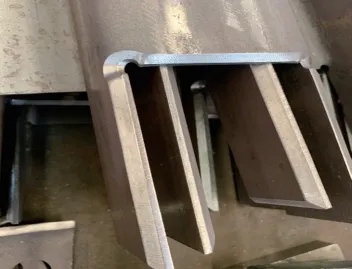
2.2 Interférence de la flexion
L'interférence de cintrage se produit principalement dans les produits soumis à un cintrage secondaire ou supérieur, lorsque le bord de cintrage entre en collision avec la matrice ou l'équipement, empêchant la formation normale. L'interférence de cintrage est principalement influencée par la forme, la taille et la matrice de la pièce, et est causée par la structure de conception de la pièce cintrée, la séquence de cintrage choisie et les matrices de cintrage sélectionnées.
Les solutions sont les suivantes :
- Fabrication ou remplacement de matrices (par exemple, matrices pour lames de cintrage).
- Modifier les matrices de pliage (par exemple, en usinant des zones spécifiques).
- Ajuster la séquence de pliage (par exemple, la méthode de déformation inversée).
- Modification des dimensions de la pièce à plier.
Par exemple, le support d'installation du chemin de câbles de la ligne 18 de Shanghai (ADC1027252G030) est un profilé d'acier en U d'une largeur moyenne de 100 mm, d'une hauteur latérale de 80 mm et d'un rayon de courbure de 15 mm. L'utilisation de matrices d'atelier existantes pour une simulation de pliage a entraîné des interférences de pliage.
Pour remédier à cette interférence, une partie de la matrice supérieure de pliage a été modifiée mécaniquement (comme le montre la figure 3). Une encoche de 140 mm × 48 mm a été pratiquée sur la ligne médiane de la matrice supérieure à lame droite R15 mm existante (L=800 mm) (comme le montre la figure 4).
La position de l'encoche a été déterminée en fonction de l'emplacement de l'interférence de pliage simulée, sans affecter sa fonction d'origine. Cette modification de la matrice de pliage a permis de résoudre le problème d'interférence de pliage.
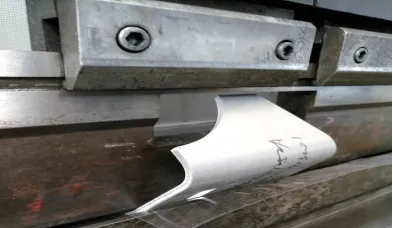

Figure 4 : Interférence de flexion, détermination de la zone d'usinage
2.3 Indentation par flexion
L'indentation de pliage se produit lorsque la tôle appuie progressivement sur la surface intérieure de la rainure en forme de V de la matrice pendant le pliage, créant une friction qui laisse des marques visibles sur la surface du matériau.
Pour les pièces présentant des exigences de surface élevées, le pliage traditionnel ne peut répondre aux exigences de qualité, et l'empreinte de pliage (comme le montre la figure 5) ne satisfait pas aux exigences du processus ultérieur.

L'empreinte de pliage est principalement influencée par la dureté du matériau de la feuille et la structure de la matrice inférieure. Plus le matériau est dur, plus il est résistant à la déformation plastique, plus il est difficile pour le matériau de se déformer et plus les empreintes se forment facilement.
La probabilité d'apparition d'une indentation de flexion dans les matériaux courants est dans l'ordre suivant : Aluminium > Acier au carbone > Acier inoxydable. Plus l'ouverture de la matrice inférieure est large, plus l'empreinte est large et peu profonde. Plus la taille R de l'épaulement de la matrice est grande, plus la profondeur de l'empreinte est faible.
Pour résoudre les problèmes d'indentation, outre l'amélioration de la dureté du matériau et la modification de la structure de l'outil inférieur, des méthodes telles que l'utilisation de tampons en caoutchouc anti-indentation et d'outils inférieurs à roulements à billes peuvent être employées.
Les tampons en caoutchouc anti-indentation réduisent la formation d'indentations grâce à l'isolation physique, comme le montre la figure 6. Les matrices inférieures à roulement à billes convertissent le frottement de compression requis pour le formage traditionnel des matrices en frottement de roulement, ce qui réduit le frottement et minimise les dommages au produit, comme le montre la figure 7.
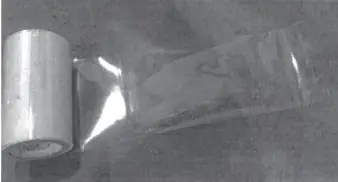

2.4 Retour élastique en flexion
Lors du cintrage, les matériaux subissent des déformations plastiques et élastiques. Une fois que la pièce est retirée de la matrice de cintrage, elle subit une reprise élastique, ce qui fait que sa forme et sa taille diffèrent de celles observées lors du chargement. Ce phénomène est connu sous le nom de flexion retour élastique et c'est l'une des principales raisons pour lesquelles les angles de flexion sont inadéquats.
Les facteurs qui influencent le retour élastique sont les propriétés mécaniques du matériau de la tôle et les conditions de déformation par flexion. L'ampleur du retour élastique est directement proportionnelle à la limite d'élasticité de la tôle et inversement proportionnelle à son module d'élasticité.
Plus le rayon de courbure relatif est faible (le rapport entre le rayon de courbure et l'épaisseur de la tôle, R/t), moins le retour élastique est important. La forme de la pièce pliée influe également sur l'ampleur du retour élastique ; en général, les pièces en forme de U ont un retour élastique moins important que les pièces en forme de V.
La principale méthode pour surmonter le retour élastique de cintrage est la compensation angulaire. On y parvient généralement en concevant la matrice de pliage avec une pente égale à l'angle de retour élastique, ce qui permet d'équilibrer efficacement les effets du retour élastique. Comme le montre la figure 8, l'utilisation d'une matrice de pliage avec une pente de 80° permet de plier avec succès une pièce à un angle de 90°.
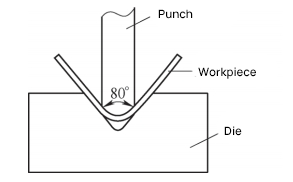
Étant donné la multitude de facteurs affectant le retour élastique de pliage, il est extrêmement difficile de calculer avec précision sa valeur. Grâce à des essais d'ajustement et à l'accumulation d'expérience, la maîtrise du modèle de retour élastique et l'application d'une compensation appropriée, ainsi que des mesures dans la structure de la matrice, sont des méthodes efficaces pour garantir la qualité du produit.
2.5 Glissement de la courbure
Le glissement de la pièce à plier est le phénomène par lequel la pièce à plier n'a pas de points d'appui complets et efficaces sur la rainure inférieure de la matrice, ce qui fait que la pièce glisse facilement et n'est pas positionnée correctement pour le pliage.
Les principales causes de glissement de la courbure sont les suivantes :
1) La largeur de la matrice de pliage inférieure est trop grande, ce qui entraîne un glissement lorsque la taille du pliage est inférieure à la moitié de la largeur de la matrice inférieure.
2) La forme et la taille de la pièce à usiner influencent le positionnement, ce qui entraîne un glissement du pliage lorsque la pièce à usiner a un côté trop court pour le positionnement de l'outil ou n'a pas d'arête de positionnement efficace.
Il existe principalement deux méthodes pour résoudre le problème du glissement de la courbure :
1) Méthode 1. Sélectionner une matrice de pliage inférieure appropriée, en choisissant généralement une largeur de matrice de 4 à 6 fois l'épaisseur de la tôle à plier.
2) Méthode 2. Résoudre les problèmes de glissement du pliage causés par un mauvais positionnement pendant le pliage en ajoutant des gabarits ou des arêtes de traitement.
En général, le cintrage est positionné le long d'un bord droit de la pièce, ce qui nécessite un contact avec deux faces de la matrice de cintrage pour le positionnement. Cependant, dans la production réelle, il arrive que le bord du produit pour le positionnement de la matrice soit trop court ou inexistant, ce qui rend le positionnement du cintrage impossible.
Les solutions comprennent
a) Pour les tôles d'épaisseur t ≤ 6mm, ajouter des bords de traitement pour le positionnement. L'arête de traitement doit s'étendre au ras de l'arête finale de la pièce et la jonction peut être découpé au laser fente pour faciliter le meulage et l'enlèvement après le pliage.
b) Pour une épaisseur de tôle t > 6mm, utiliser des gabarits coupés pour le positionnement. L'épaisseur du gabarit peut être égale ou légèrement inférieure à l'épaisseur de la pièce. Comme le montre la figure 9, les deux méthodes de positionnement permettent de résoudre le problème du glissement du pliage.
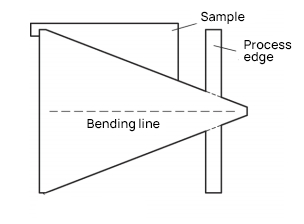
2.6 Cintrage à grand rayon
Au cours du processus de fabrication, il est fréquent de rencontrer des pièces nécessitant un grand rayon de courbure pour lesquelles l'atelier ne dispose pas de matrices à grand rayon adaptées. Dans ce cas, la fabrication d'une matrice de formage intégrale ou d'une matrice à grand rayon peut s'avérer longue et coûteuse. Au lieu de cela, l'utilisation d'un processus de formage multi-courbe à petit rayon est plus rentable et plus polyvalent.
Par exemple, le composant du projet Superbus 2.0, la plaque verticale 3 (ADC1043361G030), nécessite un rayon de courbure de 125 mm et un angle de courbure de 90°, comme le montre la figure 10. En l'absence d'une matrice de pliage correspondante dans l'atelier, un processus de pliage multiple peut être appliqué.
Tout d'abord, la position R125mm est modélisée dans un logiciel 3D pour le cintrage, puis le logiciel déplie automatiquement le dessin plat en deux dimensions. En entrant un rayon de cintrage de 45 mm dans le logiciel et en comparant plusieurs ensembles de données, il est confirmé que le formage par cintrage 8 fois peut garantir la section de l'arc.
Ensuite, les données de cintrage pour chaque coupe (angle de cintrage, longueur de la ligne de cintrage) sont générées, comme le montre la figure 11. Enfin, les données de cintrage sont utilisées pour les essais de cintrage sur site, comme le montre la figure 12.

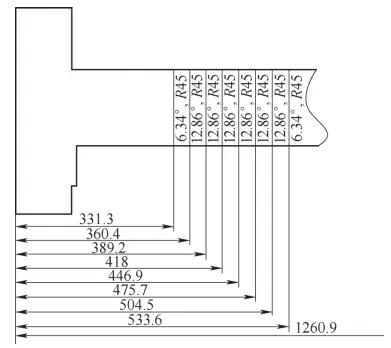

2.7 Renflement de flexion
Le renflement de pliage se produit lorsque la tôle, après pliage, présente une protubérance des deux côtés du pli en raison de la compression du matériau, ce qui entraîne une largeur supérieure à la taille d'origine. La taille du renflement de pliage dépend généralement de l'épaisseur de la pièce et du rayon de pliage ; plus le matériau est épais et plus le rayon est petit, plus le renflement est prononcé.
Pour éviter ce problème, des encoches peuvent être ajoutées de part et d'autre de la ligne de cintrage lors de la phase de dessin de l'expansion du cintrage, comme le montre la figure 13. Ces encoches ont généralement la forme d'un arc, avec un diamètre généralement supérieur à 1,5 fois l'épaisseur de la pièce, ce qui permet de contrer efficacement le renflement de flexion. Pour les pièces qui ont déjà développé un renflement de flexion, le meulage manuel est généralement utilisé pour la correction.

Conclusion
Il convient de noter que les problèmes courants de qualité du pliage et de la découpe énumérés ci-dessus ne tiennent pas compte de l'impact des facteurs humains ou de l'équipement (tels que les erreurs d'utilisation de l'équipement). se déployer (dimensions, sélection incorrecte des paramètres de cintrage et vieillissement de l'équipement).
Dans la pratique de la production, il est essentiel de sélectionner les paramètres appropriés du processus de pliage en fonction des performances de l'équipement, de la taille du produit et des caractéristiques du matériau, et de respecter scrupuleusement les normes d'exploitation.
Il est non seulement nécessaire de prendre en compte des facteurs tels que l'avancement du projet, le coût et la qualité de manière globale et d'adopter des méthodes appropriées pour résoudre les problèmes de qualité du pliage, mais aussi d'identifier et de prévenir à l'avance les problèmes de pliage potentiels grâce à l'accumulation d'expérience et à la prévoyance dans l'analyse des processus.
Cet article énumère plusieurs problèmes courants de qualité de cintrage et leurs solutions, dans l'espoir de fournir des références et des conseils aux collègues de l'industrie.