Das Scherschneiden ist ein primäres Stanzverfahren in der Kaltbearbeitung, das sich durch eine hohe Produktionseffizienz, relativ glatte Schnittflächen und die Fähigkeit, Bleche und verschiedene Profile zu schneiden, auszeichnet.
1. Grundkenntnisse der Scherverarbeitung
Es gibt viele Methoden der Scherbearbeitung, aber das Wesentliche ist, dass durch die oberen und unteren Messer eine Scherkraft auf das Material ausgeübt wird, wodurch das Material eine Scherverformung erfährt und schließlich bricht und sich trennt. Um die Technologie der Scherverarbeitung zu beherrschen, ist es daher notwendig, die Verformungs- und Spannungsbedingungen von Materialien bei der Scherverarbeitung, die geometrischen Anforderungen an die Klingen und die Berechnung der Scherkraft zu verstehen.
Bei der Kaltumformung wird in der Produktion häufig die in Abbildung 3-42 dargestellte Schrägschere verwendet. Hier wird nur die ScherprozessDie Scherkraft und die geometrischen Parameter der schrägen Schere werden analysiert, und es wird eine Methode zur Berechnung der Scherkraft vorgestellt.
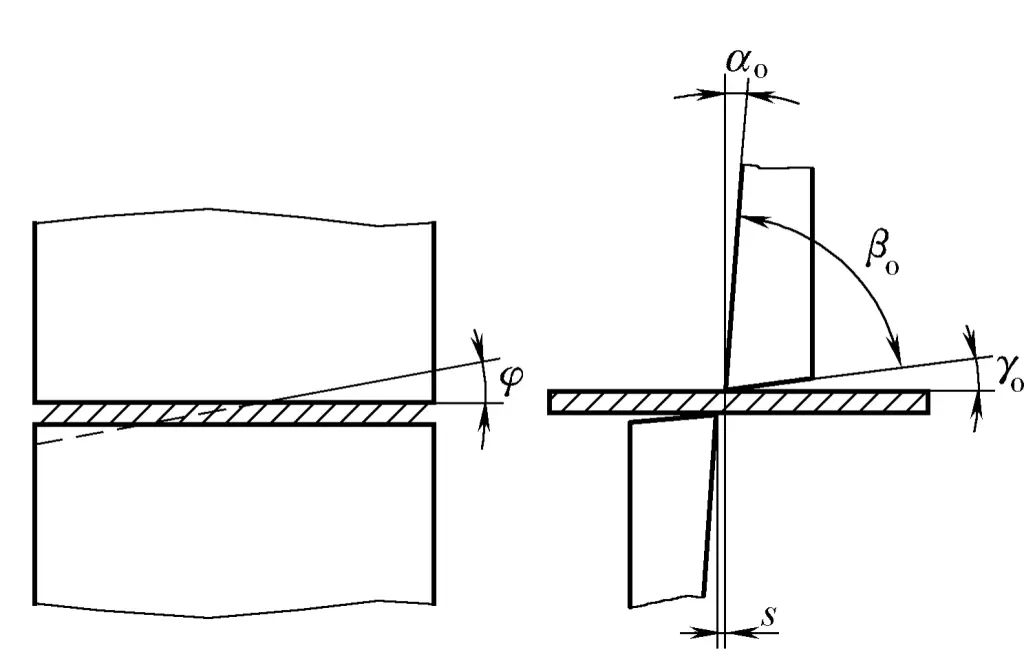
- γ o - Winkel der Harke
- α o - Freiwinkel
- β o - Keilwinkel
- s - Klingenabstand
- φ - Schrägungswinkel der Klinge
Während des Scherens wird das Material zwischen den oberen und unteren Messern platziert. Der Verformungs- und Scherprozess des Materials unter Einwirkung der Scherkraft ist in Abbildung 3-43 dargestellt.
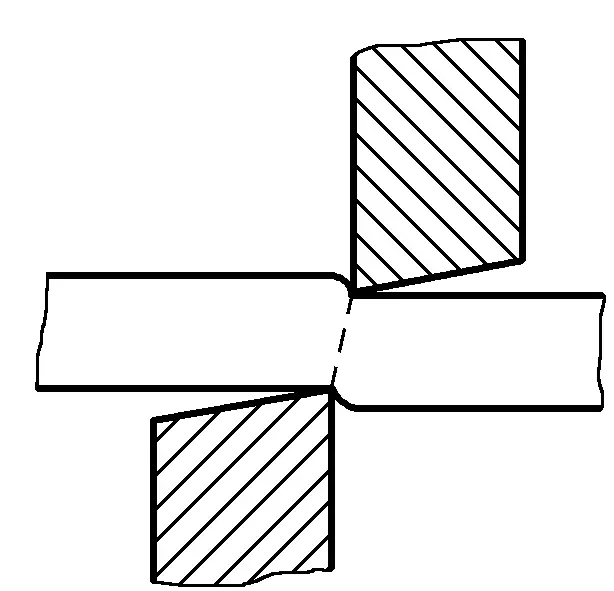
Wenn die Schaufelkante das Material zu berühren beginnt, befindet sich das Material in der Phase der elastischen Verformung. Wenn sich die obere Klinge weiter absenkt, nimmt der Druck der Klinge auf das Material zu, was zu einer lokalen plastischen Biegung und Zugverformung des Materials führt (vor allem, wenn der Klingenabstand groß ist).
Gleichzeitig beginnt die Kante der Schere, sich in das Material zu pressen, wodurch ein zusammengebrochener Winkelbereich und eine helle plastische Scherzone entstehen, in der der Spannungszustand und die Verformung des Metalls in der Nähe der Klinge extrem ungleichmäßig sind. Mit zunehmender Eindrücktiefe der Klinge bildet sich an der Kante eine große Konzentration von Spannungen und Verformungen.
Wenn diese Verformung die Grenze der Verformbarkeit des Materials erreicht, entstehen Mikrorisse im Material. Wenn sich das Scherungsphänomen ausweitet, fallen die von den oberen und unteren Schaufelkanten erzeugten Scherrisse zusammen, was schließlich zur Trennung des Materials führt.
Abbildung 3-44 zeigt die gescherte Oberfläche des Materials, die deutliche regionale Charakteristika aufweist, die klar in zusammengebrochenen Winkel, helles Band, Scherband und Grate unterteilt sind. Die Bildung des kollabierten Winkels 1 ist darauf zurückzuführen, dass das Material in der Nähe der Kante gedehnt und verformt wird, wenn die Klinge in das Material drückt; das helle Band 2 entsteht, wenn die Klinge in das Material drückt und schneidet, mit einer glatten und flachen Oberfläche; das Scherband 3 entsteht, wenn das Material schert und sich trennt, mit einer rauen Oberfläche, leicht geneigt, nicht senkrecht zur Plattenoberfläche; und die Grate 4 entstehen, wenn Mikrorisse auftreten.
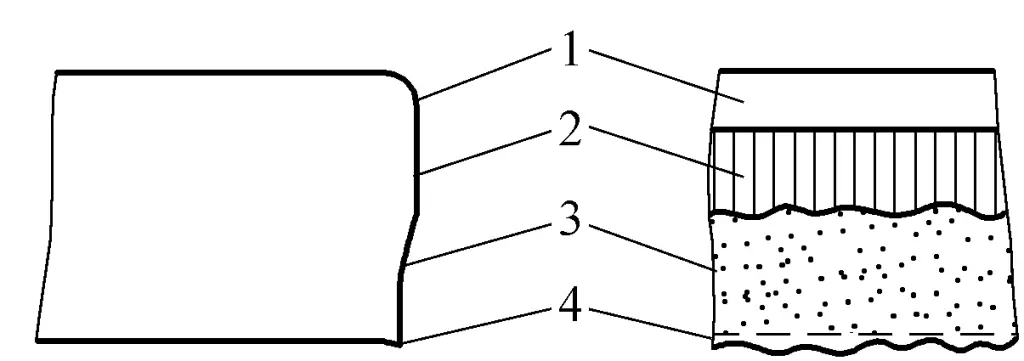
1 - Zusammengeklappter Winkel
2 - Helles Band
3 - Scherzone
4 - Grat
Das Verteilungsverhältnis von Einfallwinkel, hellem Band, Scherzone und Grat auf der gesamten Scherfläche variiert mit den Materialeigenschaften, der Dicke, der Messerform, dem Messerspalt und der Art des Pressens beim Scheren.
Die scharfe Klinge lässt sich leicht in das Material eindrücken und schneiden, was sich vorteilhaft auf die Vergrößerung des hellen Bandes auswirkt, während ein größerer Vorderwinkel r o der Klinge kann die Schärfe der Schneide erhöhen.
Wenn der Spalt zwischen den Messern groß ist, steigt die Zugspannung im Material, was die Bildung von Scherrissen erleichtert, und die Phase der plastischen Verformung endet früher, so dass das helle Band kleiner wird, während die Scherzone, der kollabierte Winkel und der Grat größer sind. Umgekehrt nimmt bei einem kleinen Schaufelspalt die Zugspannung im Material ab, die Bildung von Rissen wird unterdrückt, so dass das helle Band größer wird, während der Einfallwinkel, das Scherband usw. abnehmen.
Sowohl ein zu großer als auch ein zu kleiner Spalt führt jedoch dazu, dass die Risse auf der Ober- und Unterseite nicht auf einer Linie zusammenfallen. Wenn der Spalt zu klein ist, entstehen latente Risse und größere Grate auf der Scherfläche; wenn der Spalt zu groß ist, nehmen Scherzone, Einfallwinkel, Grat und Neigung zu, wodurch die Oberfläche extrem rau wird.
Wenn das Material fest auf die untere Klinge gepresst wird, kann dies die Zugspannung verringern und dadurch das helle Band vergrößern. Darüber hinaus können eine gute Plastizität und eine geringere Dicke des Materials das helle Band ebenfalls erhöhen.
Aus der obigen Analyse lässt sich schließen, dass die wichtigsten Maßnahmen zur Erhöhung des Glanzbandes, zur Verringerung des Einfallwinkels und des Grats und damit zur Verbesserung der Qualität der Scherfläche darin bestehen, die Schärfe der Messerkante zu erhöhen, den Mindestwert eines angemessenen Messerspaltes festzulegen und das Material fest auf das untere Messer zu drücken usw.
Der Schaufelspalt s ist ein geometrischer Parameter zur Vermeidung von Kollisionen zwischen den oberen und unteren Schaufeln, zur Verringerung der Scherkraft und zur Verbesserung der Qualität der Scherfläche. Der angemessene Spaltwert ist ein Größenbereich, wobei die obere Grenze als maximaler Spalt und die untere Grenze als minimaler Spalt bezeichnet wird. Die Bestimmung eines angemessenen Messerspaltes hängt hauptsächlich von den Eigenschaften und der Dicke des zu schneidenden Materials ab, wie in Tabelle 3-1 dargestellt. Verschiedene Schergeräte werden mit sehr spezifischen Datenschildern für die Spalteinstellung geliefert, die als Grundlage für die Einstellung des Messerspaltes verwendet werden können.
Tabelle 3-1 Bereich des angemessenen Schaufelspalts
Material | Spalt (in Prozent der Blechdicke) | Material | Spalt (in Prozent der Blechdicke) |
Reines Eisen | 6~9 | Rostfreier Stahl | 7~ 11 |
Baustahl (kohlenstoffarmer Stahl) | 6~9 | Kupfer (hart, weich) | 6~ 10 |
Harter Stahl (Stahl mit mittlerem Kohlenstoffgehalt) | 8 ~12 | Aluminium (hart) | 6 ~10 |
Siliziumstahl | 7 ~ 11 | Aluminium (weich) | 5~8 |
2. Schergeräte
Es gibt viele Arten von Schermaschinen, die üblicherweise bei der Kaltbearbeitung eingesetzt werden, darunter: Portalmaschinen mit schrägem Querschnitt SchermaschineQuereinlauf-Schrägschere, Scheibenschere, Vibrationsschere und kombinierte Stanz- und Schermaschine.
(1) Schrägschneidemaschine in Portalbauweise
Die in Abbildung 3-45 gezeigte Portalschere wird hauptsächlich zum Scheren gerader Schnitte verwendet. Sie ist einfach zu bedienen, bequem in der Beschickung, schnell in der Schergeschwindigkeit, minimale Verformung des geschnittenen Materials und hohe Präzision der Schnittfläche, daher wird sie am häufigsten in der Blechschere verwendet.
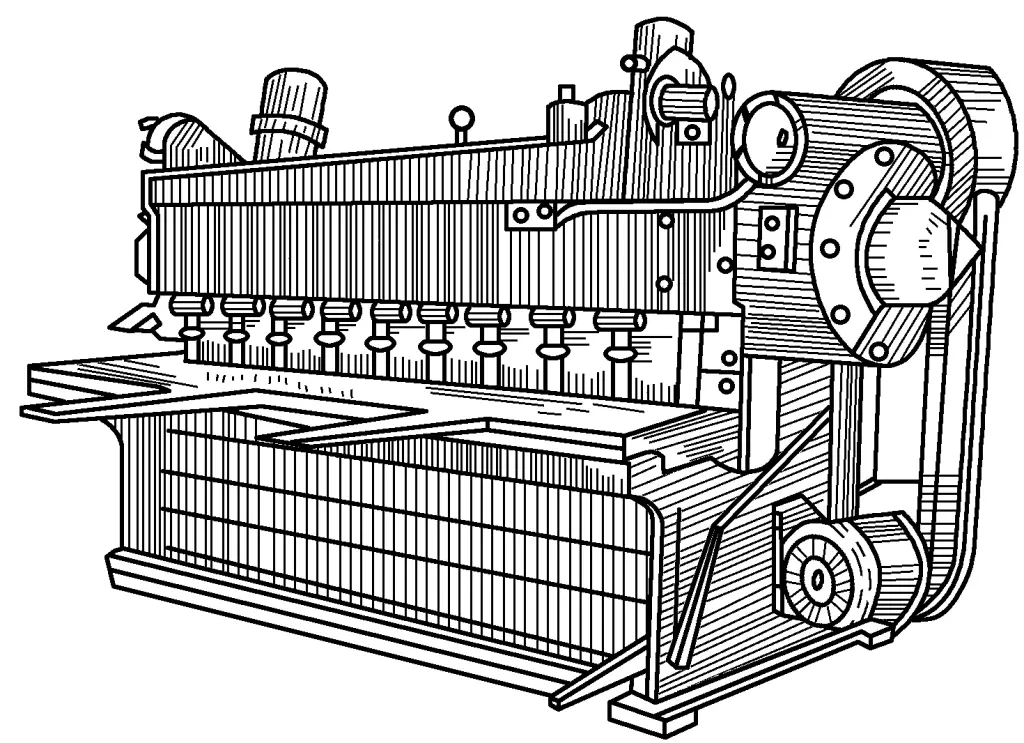
(2) Quereinlauf-Schrägschneidemaschine
Die in Abbildung 3-46 gezeigte Schrägschneidemaschine mit Quereinlauf wird hauptsächlich zum Scheren gerader Linien verwendet. Während des Scherens kann das zu scherende Material von der Seite der Schere her eintreten und sich entlang der Scherrichtung bewegen, so dass das Scheren in Segmenten ohne Begrenzung der Scherlänge erfolgen kann. Im Vergleich zur Portalschere hat sie einen größeren Scherenmesserwinkel φ und damit eine größere Verformung während des Scherens und ist schwerfälliger zu bedienen. Im Allgemeinen wird sie besser zum Scheren dünner und breiter Bleche verwendet.
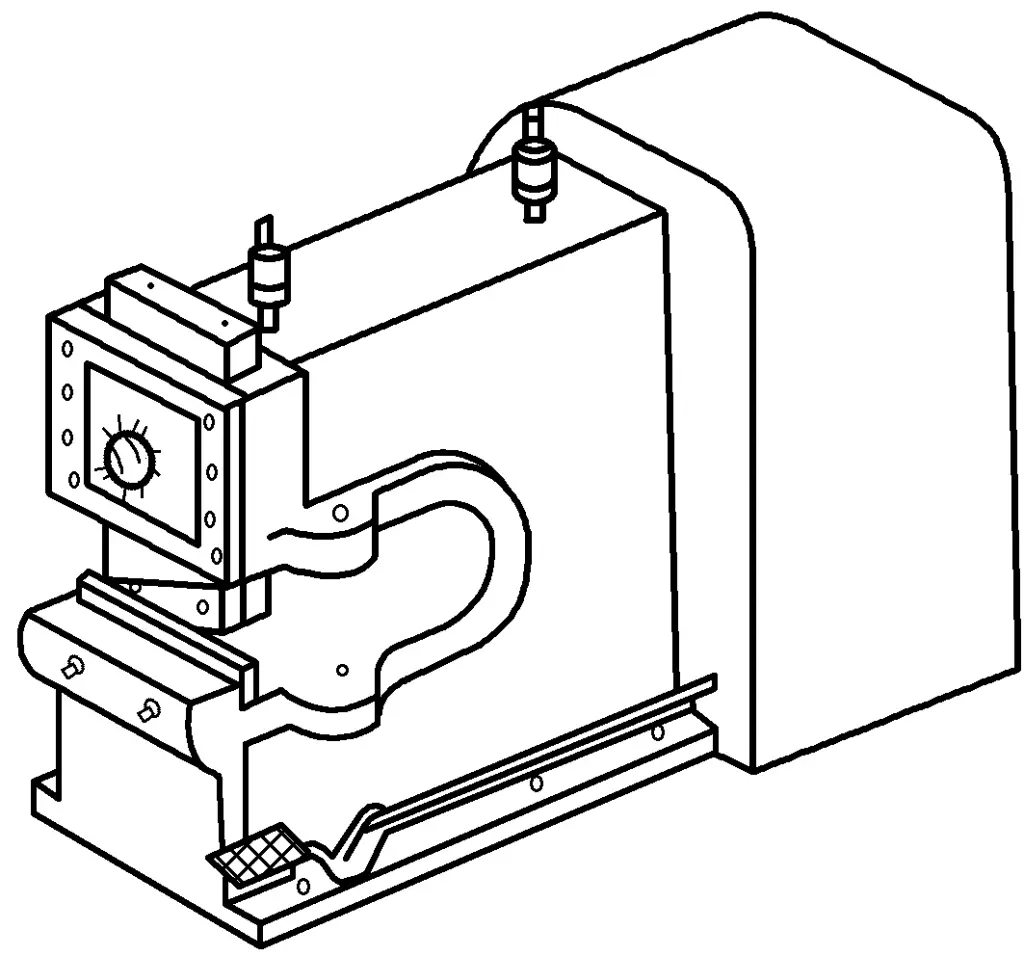
(3) Scheibenscherbett
Der Scherteil des Scheibenscherbettes besteht aus einem oberen und einem unteren rotierenden Schneidwerk. Während des Scherens drehen sich die obere und die untere Messerwelle in entgegengesetzte Richtungen mit der gleichen Geschwindigkeit, und das Material wird zwischen den beiden Messerwellen geschert und transportiert (siehe Abbildung 3-47a). Bei der Kaltbearbeitung wird in der Regel ein geneigtes Scherbett mit rotierenden Messern verwendet, wie in Abbildung 3-47b dargestellt.
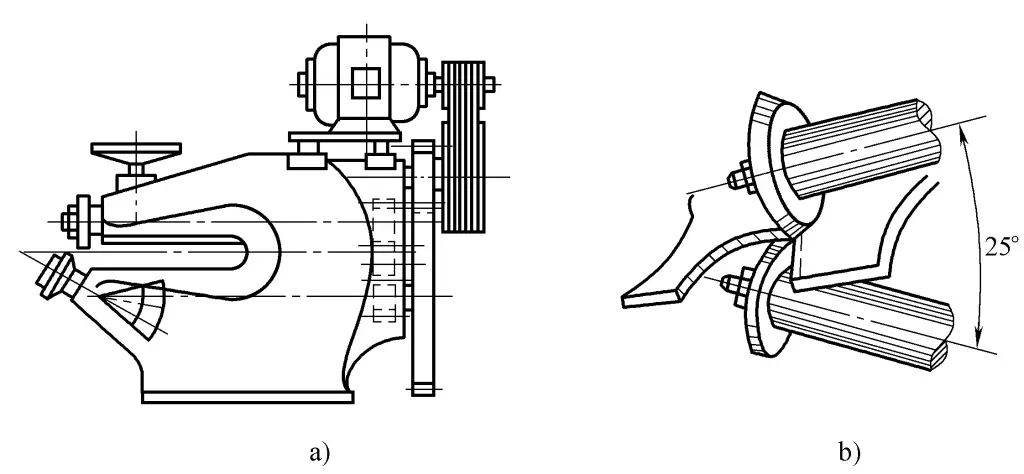
Das Scheibenscherbett ist aufgrund der geringen Überlappung der oberen und unteren Schneidkanten und der extrem kurzen momentanen Scherlänge sowie der im Grunde ungehinderten Rotation des Plattenmaterials für das Scheren von Kurven geeignet und kann kontinuierlich scheren. Da sich das zu scherende Material jedoch stark biegt und die Kanten Grate aufweisen, kann das Scheibenscherbett im Allgemeinen nur dünnere Bleche scheren.
(4) Vibrierendes Scherbett
Beim vibrierenden Scherbett, wie in Abbildung 3-48 dargestellt, sind sowohl die obere als auch die untere Messerplatte mit einem großen Schnittwinkel geneigt, und der Scherteil ist extrem kurz. Während des Betriebs vibriert die obere Messerplatte Tausende von Malen pro Minute.
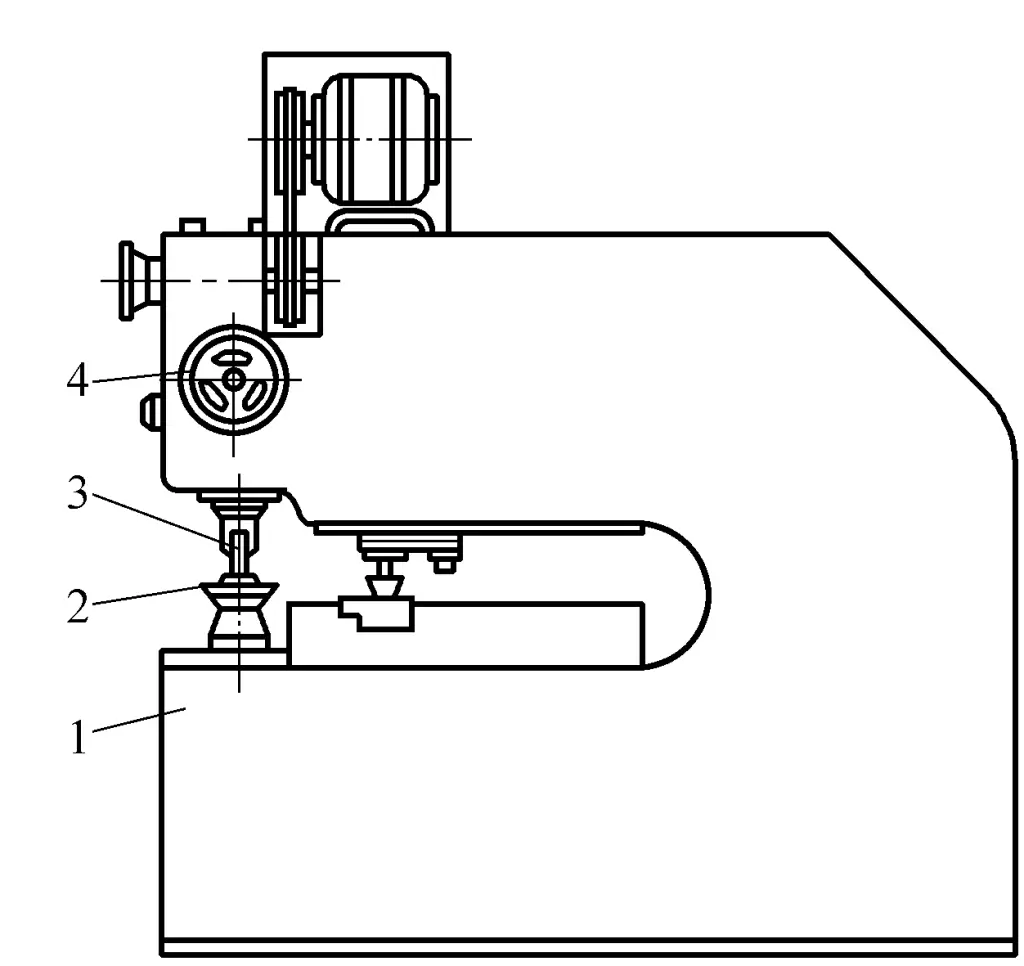
1-Bett-Körper
2-Untere Klinge
3-Obere Klinge
4-Stufen-Griff
Vibrierende Scherenbetten können verschiedene Kurven und Innenlöcher in Bleche schneiden, aber ihre Messer sind verschleißanfällig, die Schnittflächen haben Grate, die Produktivität ist gering und sie können nur dünne Bleche schneiden.
(5) Kombinierte Stanz- und Schermaschine
Kombinierte Stanz- und Schermaschinen bestehen in der Regel aus einer Schrägschere, einer Profilstahlschere und einer kleinen Stanze und sind in der Lage, Stahlplatten und verschiedene Profilstähle zu schneiden sowie kleine Teile zu stanzen und zu lochen.
3. Arten und technische Leistung von Schermaschinen
Die Bediener von Schermaschinen sollten in der Lage sein, eine einfache Analyse der verwendeten Schermaschinen durchzuführen, um die Schermethoden zu beherrschen und zu verbessern und die Schermaschinen richtig zu warten und zu benutzen. Anhand der strukturellen Form kann man den Typ einer Schermaschine vorläufig beurteilen und dann die Bedeutung des Modells im Detail verstehen.
Das Modell des Scherenbettes beschreibt den Typ, die Eigenschaften und die grundlegenden Betriebsparameter des Scherenbettes. Zum Beispiel die Portalschermaschine des Typs Q11-13×2500, deren Bedeutung durch das Modell dargestellt wird
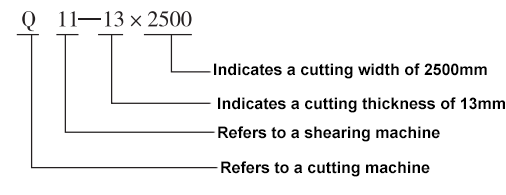
Die nationale Norm für Werkzeugmaschinennummern wurde mehrmals geändert, daher sollte man sich für die verschiedenen Scherbettmodelle, die durch die Bedeutungen dargestellt werden, auf die nationalen Normen beziehen, die sich auf die Herstellungszeit des Scherbettes beziehen.
Die technischen Leistungsparameter der verschiedenen Arten von Schermaschinen sind in der Regel auf den Typenschildern angegeben, die auf dem Maschinenkörper angebracht sind und als Grundlage für die Bearbeitung der Schere dienen. Die technische Leistung der Geräte wird auch im Handbuch der Geräte detailliert beschrieben. Daher kann man sich anhand des Typenschilds oder des Handbuchs ein Bild von der technischen Leistung des Scherbettes machen.
4. Technologische Ausstattung der Schermaschinen
Um den Anforderungen des Scherprozesses gerecht zu werden, sind Schermaschinen in der Regel mit einer einfachen Prozessausrüstung ausgestattet. Abbildung 3-49 zeigt die Prozessausrüstung einer typischen Portal-Schrägschermaschine.
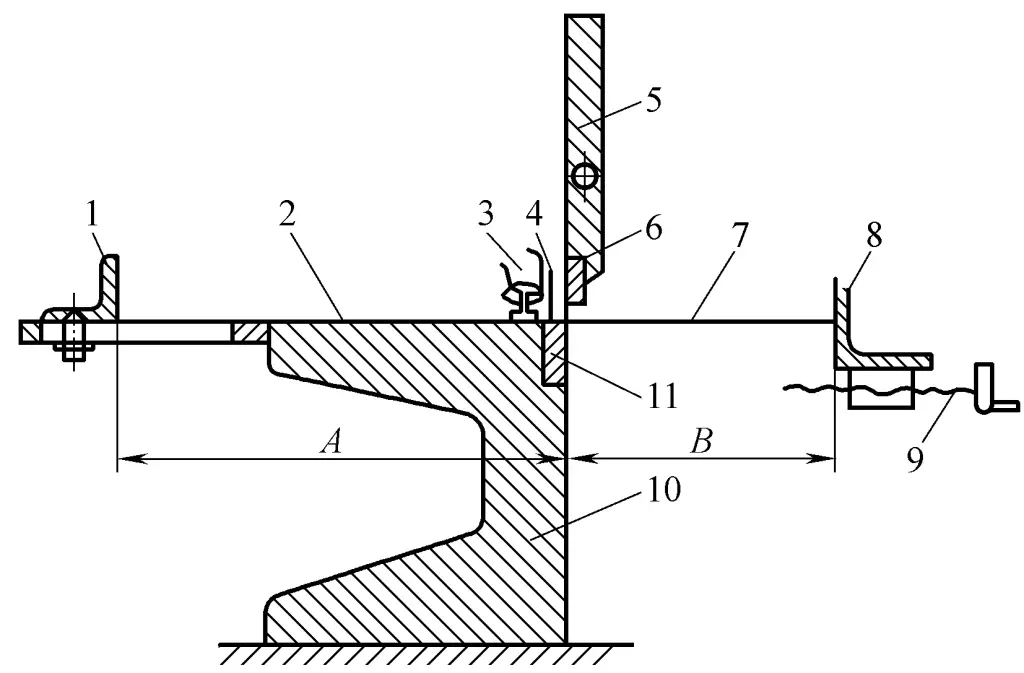
1 - Vorderer Anschlag
2 - Bett
3 - Pressplatte
4 - Gitterrost
5 - Scherbettschieber
6 - Obere Klinge
7 - Material der Platte
8 - Hinterer Anschlag
9 - Schraube
10 - Bett
11 - Untere Klinge
Die Niederhalterplatte verhindert das Drehen und Bewegen der Platte während des Scherens, um die Scherqualität zu gewährleisten. Die Niederhalterplatte wird von der Arbeitskurbelwelle angetrieben und klemmt die Platte ein, bevor das Obermesser die Platte berührt, wodurch die automatische Klemmung abgeschlossen wird. Sie kann auch mit manuellen Exzenterrädern geklemmt werden, so dass sie zu einem manuellen Klemmtyp wird. Der Schieber ist eine Sicherheitsvorrichtung, die verhindert, dass Hände oder andere Gegenstände in die Scherenöffnung gelangen und Unfälle verursachen.
Die vorderen und hinteren Anschlagplatten spielen eine wichtige Rolle bei der Positionierung während des Scherens. Beim Schneiden einer großen Anzahl von Teilen mit der gleichen Größe kann die Verwendung der Anschlagplatten zur Positionierung die Produktionseffizienz verbessern und die Produktqualität sicherstellen. Positionier-Lehrplatten können auch auf dem Bett installiert werden.
Einige Fabriken haben ihre Scherenmaschinen entsprechend ihren spezifischen Bedingungen modifiziert, um die Automatisierung zu verbessern, z. B. durch automatisches Be- und Entladen, automatische Zuführung, Positionierung (für die Scherenlinie) und Klemmung.
5. Der Einfluss des Scherprozesses auf die Stahlqualität
Das Scheren ist ein effizientes Verfahren zum Schneiden von Metall, das relativ saubere und glatte Schnitte erzeugt, aber es hat auch einige Nachteile. Das Scheren von Stahl kann zu Veränderungen der mechanischen Eigenschaften und der äußeren Form führen, was die Leistungsfähigkeit des Stahls beeinträchtigt. Dies äußert sich vor allem in den folgenden beiden Aspekten:
1) Schmales und langes Bandmaterial weist nach dem Scheren eine erhebliche Biege- und Torsionsverformung auf und muss anschließend gerade gerichtet werden. Wenn der Messerspalt ungeeignet ist, wird der gescherte Abschnitt außerdem rau und weist Grate auf.
2) Während des Scherprozesses kommt es aufgrund der Scherkraft, die auf das Metall in der Nähe des Schnitts einwirkt, zu einer Quetsch- und Biegeverformung, die eine Erhöhung der Metallhärte und der Streckgrenze sowie eine Verringerung der Plastizität bewirkt und das Material spröde macht. Dieses Phänomen wird als Kaltverfestigung bezeichnet. Die Breite des gehärteten Bereichs hängt von den folgenden Faktoren ab:
1) Mechanische Eigenschaften von Stahl. Je besser die Plastizität des Stahls ist, desto größer ist der Verformungsbereich und desto breiter ist der Verfestigungsbereich; umgekehrt ist der Verfestigungsbereich umso kleiner, je höher die Härte des Materials ist.
2) Dicke des Stahlblechs. Je dicker das Stahlblech ist, desto größer ist die Verformung und desto größer ist der Härtebereich; umgekehrt ist er umso kleiner.
3) Schermesserspalt s. Je größer der Spalt, desto stärker ist die Biegung des Materials und desto breiter ist der Verfestigungsbereich.
4) Schermesserwinkel φ. Je größer der Schermesserwinkel φ ist, wenn die Scherkraft beim Scheren der gleichen Dicke des Stahlblechs kleiner ist, desto kleiner ist auch die Verfestigungsfläche.
5) Schärfe des Schermessers. Je stumpfer das Schermesser ist, desto größer ist die Scherkraft und desto breiter wird die Härtefläche.
6) Position und Klemmkraft der Klemmvorrichtung. Wenn die Klemmvorrichtung näher am Schermesser angebracht ist und die Klemmkraft größer ist, kann sich das Material weniger verformen und die Breite des Härtebereichs wird verringert.
Zusammenfassend lässt sich sagen, dass die Breite der Kaltverfestigungszone, die durch das Scherschneiden von Stahl verursacht wird, von verschiedenen Faktoren abhängt und das Ergebnis eines umfassenden Effekts ist. Wenn die Dicke des gescherten Stahlblechs weniger als 25 mm beträgt, liegt die Breite des Verfestigungsbereichs im Allgemeinen im Bereich von 1,5 bis 2,5 mm.
Bei der Herstellung wichtiger Strukturen oder wenn nach dem Scheren noch eine Kaltverformung erforderlich ist, muss die Kaltverfestigung an den Blechkanten durch Fräsen, Hobeln oder Wärmebehandlung beseitigt werden, um die Verfestigung zu beseitigen.
II. Grundsätze und Ausrüstung des Stanzens
1. Grundsätze des Stanzens
Das Verfahren, bei dem ein Stempel auf einer Presse verwendet wird, um einen Teil des Blechs von einem anderen zu trennen, wird als Stanzen bezeichnet. Das Stanzen ist auch eine Methode zum Schneiden von Stahl. Bei der Serienfertigung von Teilen oder geformten Produkten kann das Stanzen die Produktionseffizienz und die Produktqualität verbessern.
Beim Stanzen wird das Material zwischen Stempel und Matrize eingelegt, und unter der Einwirkung äußerer Kräfte erzeugen Stempel und Matrize ein Paar Scherkräfte (die Scherlinie ist normalerweise geschlossen), und das Material wird unter der Einwirkung von Scherkräften getrennt, wie in Abbildung 3-50 dargestellt.
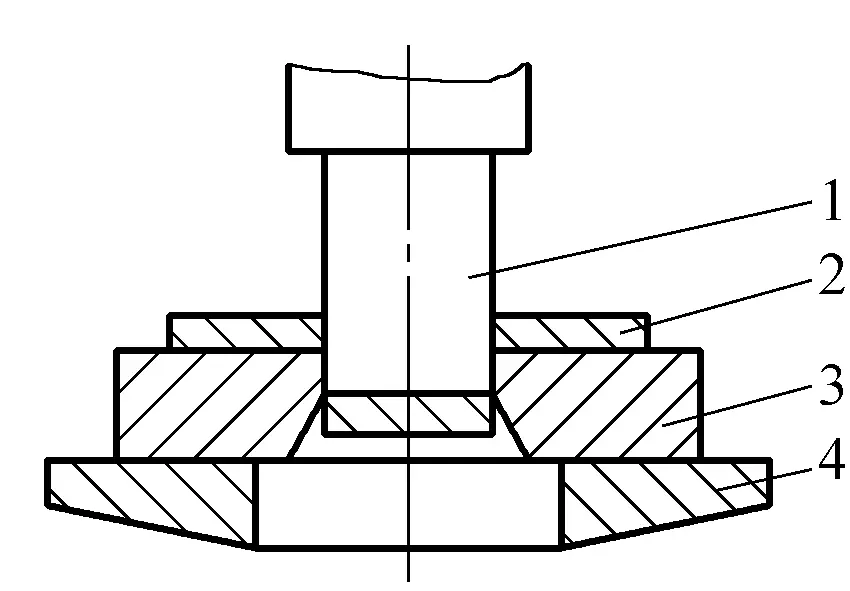
1-Stempel
2-Blatt-Material
3-Würfel
Arbeitstisch für 4 Stanzmaschinen
Das Grundprinzip des Schneidens ist das gleiche wie das des Scherens, mit dem Unterschied, dass die beim Scheren verwendete gerade Schneide durch eine geschlossene kreisförmige oder andere Form der Schneide ersetzt wird.
Die Verformung des Materials und der Zustand des Querschnitts während des Stanzvorgangs sind in etwa die gleichen wie beim Scheren.
Der Vorgang vom Kontakt des Stempels mit dem Bogenmaterial bis zur Trennung des Bogenmaterials ist augenblicklich abgeschlossen. Wenn der Spalt zwischen Stempel und Matrize normal ist, kann der Verformungsprozess beim Stanzen im Allgemeinen in die folgenden drei Phasen unterteilt werden:
Die erste Phase ist die Phase der elastischen Verformung. Wie in Abbildung 3-51a dargestellt, beginnt das Blech unter dem Druck des Stempels und der Matrize komplexe Verformungen wie elastische Stauchung, Biegung und Dehnung (AB'>AB) zu erfahren, wenn der Stempel das Blech berührt und nach unten drückt. Zu diesem Zeitpunkt drückt der Stempel leicht in das Blech, und der untere Teil des Blechs drückt ebenfalls leicht in das Matrizenloch, so dass an der Kontaktstelle mit den Stempel- und Matrizenrändern eine sehr kleine Kehle entsteht.
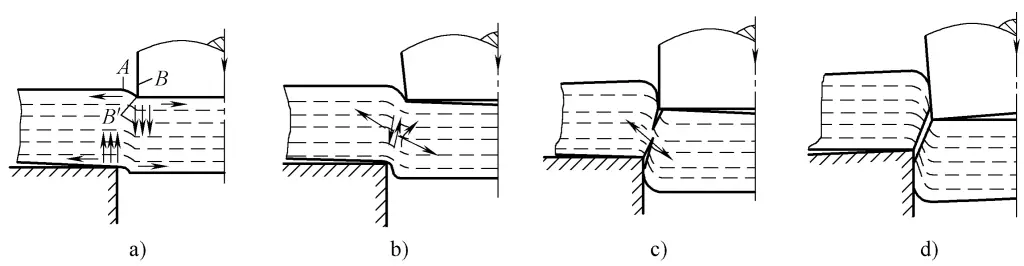
a) Stadium der elastischen Verformung
b) Stadium der plastischen Verformung
c), d) Stufe der Bruchtrennung
In der Zwischenzeit wölbt sich das Blech leicht, je härter das Material ist, je größer der Spalt zwischen Stempel und Matrize ist und je stärker die Wölbung ist. Wenn der Stempel nach unten drückt, nimmt die Spannung auf dem Blech in der Nähe der Schneidkante allmählich zu, bis sie die Elastizitätsgrenze erreicht und die Phase der elastischen Verformung beendet.
Die zweite Phase ist die Phase der plastischen Verformung. Wenn der Stempel weiter nach unten drückt und die Spannung im verformten Bereich des Blechs die Streckgrenze überschreitet und plastische Bedingungen erreicht, tritt es in das Stadium der plastischen Verformung ein, wie in Abbildung 3-51b dargestellt.
Zu diesem Zeitpunkt nimmt die Tiefe des Stempels, der in das Blech drückt, und des Blechs, das in die Matrize gedrückt wird, allmählich zu, wodurch eine plastische Scherverformung entsteht, die eine glänzende, gescherte Oberfläche bildet. Wenn sich der Stempel absenkt, nimmt der Grad der plastischen Verformung zu, das Material im verformten Bereich verhärtet sich, der Verformungswiderstand nimmt kontinuierlich zu, und die Stanzkraft nimmt ebenfalls entsprechend zu, bis die Spannung in der Nähe der Schneidkante die Zugfestigkeit erreicht und das Stadium der plastischen Verformung beendet.
Aufgrund des Spalts zwischen Stempel und Matrize kommt es auch in dieser Phase zu Biege- und Streckverformungen, und je größer der Spalt ist, desto größer sind die Biege- und Streckverformungen.
Die dritte Stufe ist die Stufe der Bruchtrennung. Wenn die Spannung im Inneren des Blechs die Zugfestigkeit erreicht und der Stempel weiter nach unten drückt, entstehen anschließend Mikrorisse an den Teilen des Blechs, die mit den Stempel- und Matrizenkanten in Kontakt sind, wie in Abbildung 3-51c dargestellt. Der Ausgangspunkt der Risse befindet sich im Allgemeinen auf der Seite nahe der Schneidkante und tritt normalerweise zuerst auf der Seite nahe der Stempelkante und dann auf der Seite nahe der Stempelkante auf.
Wenn der Stempel weiter nach unten drückt, dehnen sich die bereits gebildeten oberen und unteren Mikrorisse entlang der Richtung der maximalen Scherspannung weiter in das Innere des Blechs aus. Wenn die oberen und unteren Risse zusammenfallen, wird das Blech abgeschert und getrennt, wie in Abbildung 3-51d dargestellt. Anschließend drückt der Stempel das abgetrennte Material in das Matrizenloch, und der Stanzverformungsprozess endet.
In den drei Phasen des Stanzverformungsprozesses sind die äußere Kraft und die für jede Phase erforderliche Zeit nicht gleich. Im Allgemeinen hängt die Stanzzeit oft von den Materialeigenschaften ab, und die Dauer ist kürzer, wenn das Material spröder ist.
2. Ausrüstung zum Stanzen
(1) Aufbau der Presse
Das Stanzen wird im Allgemeinen auf einer Presse durchgeführt. Zu den gebräuchlichen Pressen gehören Kurbelpressen und Exzenterpressen, die beide nach dem gleichen Prinzip arbeiten, wobei der Hauptunterschied in der verwendeten Hauptspindel besteht.
Der grundsätzliche Aufbau einer Kurbelpresse ist in Abbildung 3-52a dargestellt, und das Funktionsprinzip ist in Abbildung 3-52b gezeigt. Der Pressenkörper und der Arbeitstisch sind integriert, wobei vertikale Führungsschienen am Körper über der Arbeitstischoberfläche die Auf- und Abwärtsbewegung des Schlittens ermöglichen. Das obere und das untere Stanzwerkzeug sind auf dem Schlitten bzw. auf der Arbeitstischfläche montiert.
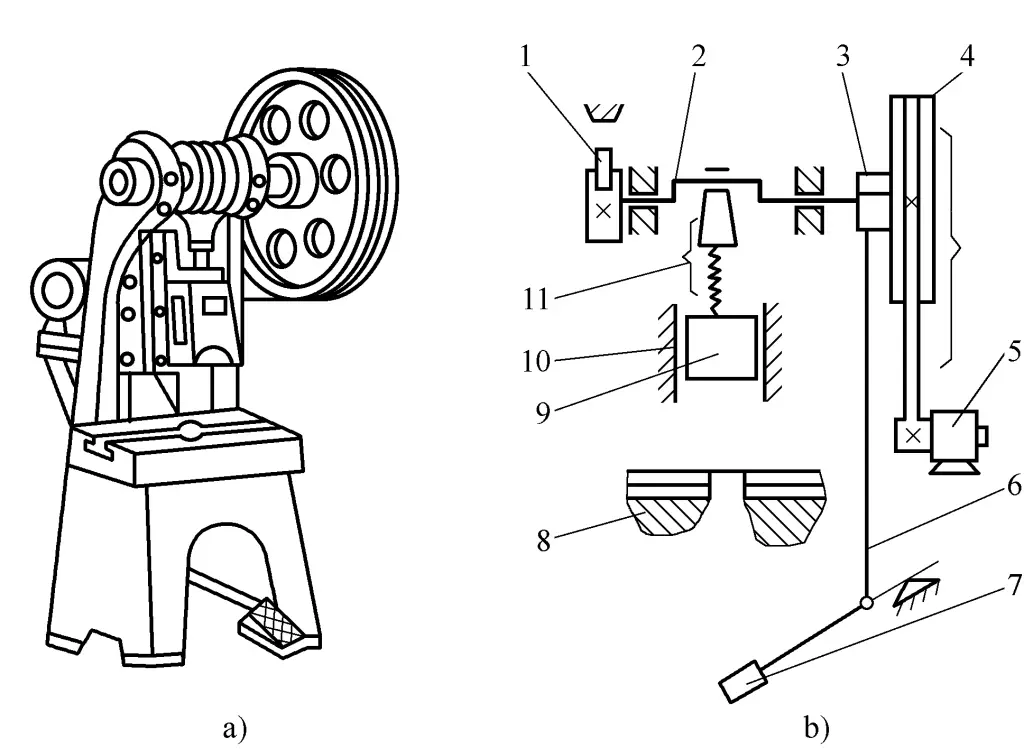
a) Erscheinungsbild
b) Schema des Arbeitsprinzips
1 - Bremse
2-Kurbelwelle
3-Kupplung
4-Große Riemenscheibe
5-Elektromotor
6-Stoßstange
7-Pedal
8-Workbench
9-Schieberegler
10-Führungsschiene
11-Verbindungsstange
Wenn die Stanzpresse in Betrieb ist, treibt der Motor zunächst die große Riemenscheibe über den Transmissionsriemen in den Leerlauf. Nach dem Treten des Pedals schließt sich die Kupplung und treibt die Kurbelwelle an, die dann den Schieber über die Pleuelstange entlang der Führungsschiene auf und ab bewegt und den Stanzvorgang ausführt.
Wird das Pedal nach dem Treten sofort losgelassen, bleibt der Schieber nach einem Schlag durch die Bremse in der höchsten Position stehen; wird das Pedal ständig gedrückt, bewegt sich der Schieber weiter auf und ab und führt einen kontinuierlichen Schlag aus.
(2) Technische Leistungsparameter der Stanzpresse
Die technischen Leistungsparameter der Stanzpresse haben einen erheblichen Einfluss auf die Stanzarbeit. Bei der Durchführung von Stanzarbeiten ist es notwendig, die Stanzpresse nach den technischen Leistungsparametern auszuwählen.
1) Tonnage und Nennleistung der Stanzpresse.
Die Tonnage und die Nennleistung der Stanzpresse sind zwei Angaben, die die Arbeitskapazität der Stanzpresse kennzeichnen. Die benötigte Stanzkraft und Leistung für die tatsächlich gestanzten Teile muss unter diesen beiden Kennziffern der Stanzpresse liegen. Beim Stanzen von dünnen Blechen ist die erforderliche Stanzleistung relativ gering und kann im Allgemeinen vernachlässigt werden.
2) Geschlossene Höhe der Stanzpresse.
Der Abstand zwischen der Unterseite des Schiebers in seiner untersten Position und der Oberfläche des Arbeitstisches. Wenn die Einstellvorrichtung den Schieber in die obere Endstellung bringt, erreicht die geschlossene Höhe ihren Höchstwert, der als maximale geschlossene Höhe bezeichnet wird. Die geschlossene Höhe der Stanzpresse sollte mit der geschlossenen Höhe der Form kompatibel sein.
3) Hub des Schiebereglers.
Der Weg, den der Schieber von der höchsten bis zur niedrigsten Position zurücklegt, wird auch als Hub bezeichnet. Die Größe des Schieberhubs bestimmt die geschlossene Höhe und die offene Höhe der verwendeten Stanzpresse und sollte einen reibungslosen Vorschub und Rückzug während des Stanzvorgangs gewährleisten.
4) Größe des Stanztisches.
Beim Stanzen sollte die Größe der Matrize an die Größe des Arbeitstisches der Stanzpresse angepasst werden, um sicherzustellen, dass die Matrize fest auf dem Tisch installiert werden kann.
Andere technische Leistungsparameter haben nur einen geringen Einfluss auf den Stanzprozess und können je nach den spezifischen Gegebenheiten entsprechend ausgewählt werden.
(3) Vorsichtsmaßnahmen bei der Verwendung der Stanzpresse
1) Überprüfen Sie vor dem Gebrauch alle Teile der Stanzpresse und füllen Sie alle Schmierstellen mit Schmieröl.
2) Prüfen Sie, ob das Spiel zwischen den Lagerschalen und die Dichtheit der Bremse angemessen sind.
3) Prüfen Sie, ob sich Fremdkörper in den beweglichen Teilen verfangen haben.
4) Überprüfen Sie regelmäßig die Abnutzung und das Spiel zwischen dem Schlitten und der Führungsschiene der Stanzpresse. Ein zu großes Spiel beeinträchtigt die Führungsgenauigkeit, daher muss das Spiel zwischen den Führungsschienen regelmäßig eingestellt werden. Wenn der Verschleiß zu stark ist, muss eine Wartung durchgeführt werden.
5) Richten Sie beim Einbau der Matrize den Druckmittelpunkt der Matrize auf den Druckmittelpunkt der Stanzpresse aus und achten Sie darauf, dass der Abstand zwischen Patrize und Matrize gleichmäßig ist.
6) Nach dem Einschalten des Schalters lassen Sie die Maschine 3 bis 5 Mal leer laufen, um zu prüfen, ob das Steuergerät und der Betriebszustand normal sind.
7) Konzentrieren Sie sich beim Stanzen, treten Sie nicht willkürlich auf das Pedal, und es ist strengstens verboten, die Hände zwischen den Formen auszustrecken oder mit dem Kopf den Schieber zu berühren, um Unfälle zu vermeiden.
8) Stanzen Sie keine Materialien, die zu hart sind oder abgeschreckt wurden. Die Stanzpresse darf nicht überlastet werden.
9) Achten Sie beim Stanzen über längere Zeit darauf, ob die Form locker ist und ob der Spalt gleichmäßig ist.
10) Nach Beendigung des Stanzvorgangs ist die Stromzufuhr zu unterbrechen oder der Sicherheitsschalter zu verriegeln. Die gestanzten Teile und das Abfallmaterial sollten rechtzeitig entfernt werden, um den Bereich um die Stanzpresse frei von Hindernissen zu halten.
III. Grundsätze und Methoden der Schleifscheibenbearbeitung
Beim Schleifscheibenschneiden wird durch die Hochgeschwindigkeitsrotation der Schleifscheibe Wärme durch Reibung mit dem Werkstück erzeugt, das dadurch schmilzt und einen Schnitt bildet. Schleifscheibe Schneiden ist unkompliziert, effizient, einfach zu bedienen, und weit verbreitet in Schneiden von Winkelstahl, Kanalstahl, Flachstahl, Stahlrohre und andere Profile, besonders geeignet für Schneiden von rostfreiem StahlLagerstahl und verschiedene legierte Stähle.
Abbildung 3-53 zeigt eine weit verbreitete tragbare Schleifscheiben-Trennmaschine, die aus einem Schneidkopf 4, einer drehbaren Klemme 1, einem zentralen Einstellmechanismus 3 und einer Basis 2 besteht.
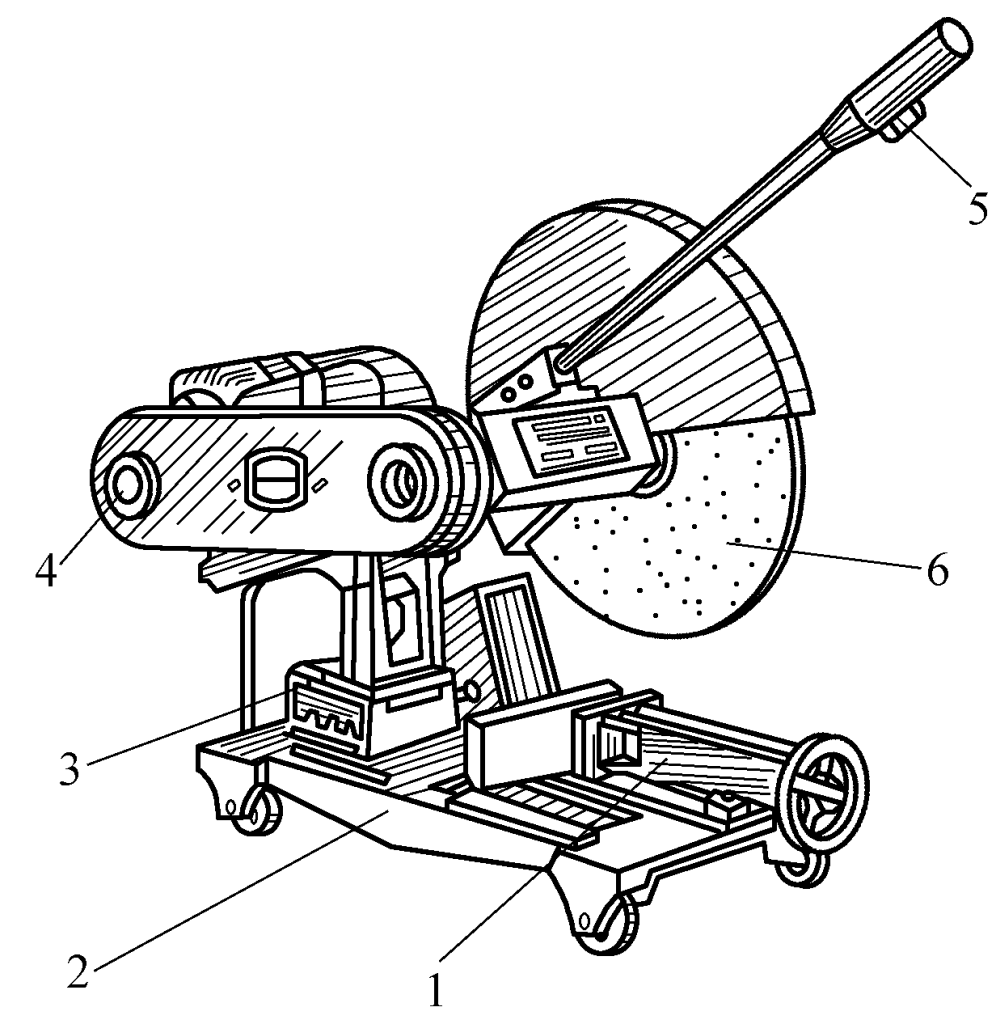
1-Drehbare Klemme
2-Basis
3-Zentraler Anpassungsmechanismus
4-Schneider-Kopf
5-Schalter
6-Schleifscheibe
Die üblicherweise verwendete Schleifscheibe hat einen Durchmesser von 300 bis 400 mm, eine Dicke von 3 mm und eine Geschwindigkeit von 2900 U/min bei einer Schnittgeschwindigkeit von 60 m/s. Um ein Bersten der Schleifscheibe zu verhindern, wird eine faserverstärkte Schleifscheibe verwendet. Der gesamte Antriebskopf und das Zentrum der Schleifscheibe können je nach Schneidbedarf eingestellt und gedreht werden, was durch einen Griff erreicht werden kann, der auch einen Schalter zur Steuerung des Motorbetriebs hat.
Der drehbare Schraubstock kann seinen Winkel mit der Schleifscheibenspindel (0°~45°) nach Bedarf einstellen. Zum Einstellen lösen Sie einfach die Sechskantschraube, ziehen den Positionierungsstift heraus, und die Backen können sich um die Drehschraube in den gewünschten Winkel drehen. Unter dem Sockel sind vier Rollen angebracht, so dass der gesamte Schleifscheibenfräser beweglich ist.
Während des Schneidens wird das Profil auf den drehbaren Schraubstock montiert und eingespannt, der Schalter am Handgriff wird betätigt, um den Motor anzutreiben, der über eine Riemenübertragung die Schleifscheibe mit hoher Geschwindigkeit dreht. Sobald sich die Geschwindigkeit der Scheibe stabilisiert, betätigen Sie den Griff zum Schneiden.